Principiellt kan det se ut så här: I samband med fabrikstillverkning och på maskinnivå betyder ”closed-loop” att man arbetar med ett automatiskt styrsystem där driftstyrningen, processen eller mekanismen regleras av återkoppling av driftdata, en ”sluten cirkel” alltså. När det gäller driften av maskiner på verkstadsgolvet eller i en produktionslinje kan man tänka sig en IIoT (Industrial Internet of Things) uppkopplad plattform som fångar all driftdata från maskinerna, och som kontinuerligt matchar dessa mot förutbestämda mallar för hur produktionen bör se ut. Föreställ dig att systemet också kan skicka en varning när något går fel, kan berätta var problemet är och vad som orsakade avvikelsen – och kanske till och med kan föreslå åtgärder för att åtgärda problemet. Det är inte svårt att se fördelarna med ett sådant system, som på en idealisk nivå skulle kunna leda till betydande effektivitetsvinster i produktionen. I större anläggningar eller i grupper med flera fabriker kan ökad effektivitet med till och med några få procent vara värda miljoner.

Den digitala tvillingen i huvudrollen
I CLM – Siemens konceptet – spelar den digitala tvillingen en huvudroll; på flera sätt är det den minsta gemensamma nämnaren i en process som leder in på fabriksgolvet och sedan ut därifrån. Siemens delar upp tänket kring tvillingar i tre delar:
• Dels den digitala tvillingen av produkten
• Dels en tvilling av produktionsenheten, maskiner, ja, hela tillverkningslinan
• Dels en tvilling för produkten i användarens händer, med återkopplingsbarhet till PLM-systemets tvilling. Man ska t ex kunna simulera en turbinanläggning i drift för att optimera flöden, eller om något går sönder eller behöver förbättras, kunna gå tillbaka med fältdriftsdata till PLM-systemet för att där korrigera och förbättra baserat på dessa.

Simulering en nyckelkapacitet
Generellt är också simuleringsbiten en nyckelkapacitet. Med den digitala tvillingen i centrum är allt simuleringsbart i alla led, för att man ska kunna säkra att allt fungerar som tänkt innan man går över till de fysiska motsvarigheterna, då eventuella förändringar och upptäckta fel blir dyra att åtgärda.
I Siemens Xcelerator-portfölj finns grundbitarna som bygger upp den digitala tvillingen, med 3D CAD-mjukvaran NX som en av de centrala skapandesystemen, som sedan sömlöst kan kopplas vidare mot simuleringsportföljens, Simcenter, och andra lösningar i PLM-portföljen.
Allt kan sedan i sin tur kopplas ihop via IoT och IIoT (Industrial IoT), vilket i Siemens fall går över Insight Hub-mjukvaran (tidigare kallades den MindSphere). Denna i sin tur är kopplad till t ex simulerings- och analyssystemen via cPDm-plattformen (collaborative Product Definition management) Teamcenter, en databas-ryggrad till vilken man också kan koppla på den digitala tillverkningshanterings-lösningen Tecnomatix. Fungerar det inte som du tänkt dig? Förbättra och optimera genom att gå tillbaka och simulera igen. Det är en viktig poäng CLM-tanken.
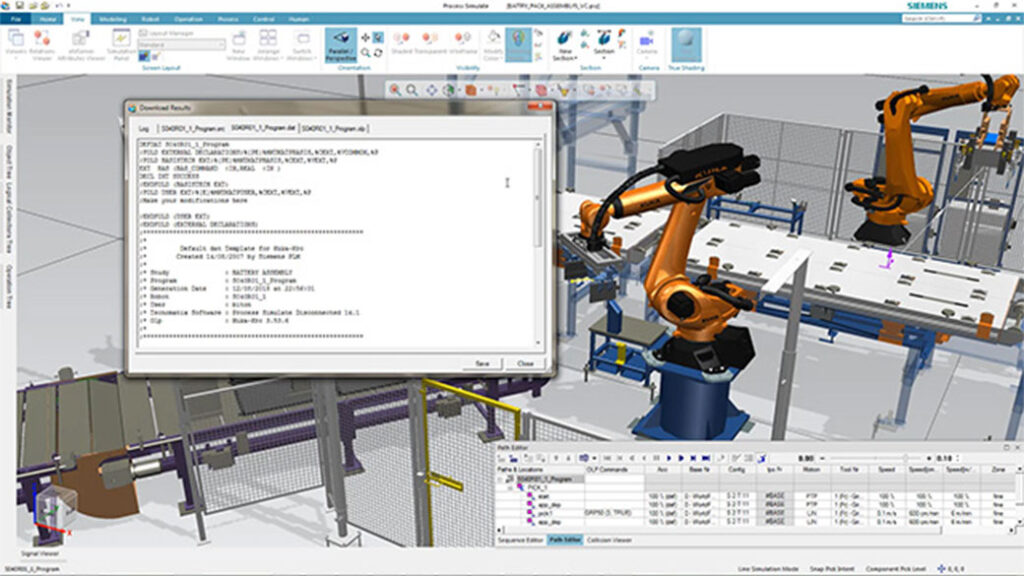
Värdet av kopplingar mellan PDM- och ERP-systemen
Men av vikt är också att kopplingar till ERP-systemen finns med i konceptlösningen. Om dessa inte finns kan man missa länkningen till orderhanterings-systemet och andra tangerande lösningar. Vilket öppnar möjligheten för att alternativa, divergerande ”sanningar” kommer att finnas; något som riskerar att dra ner process- och tillverkningskvalitén och öppnar för fel. ”One single source of truth,” som mantrat lyder, är den eftersträvansvärda finessen för att undvika felkällor.
Genom kopplingarna och en långt driven integration mellan PDM/cPDm- och ERP-system kan företag uppnå en rad fördelar som kan göra en betydande skillnad i såväl affärsprocesser som resultat. Goda exempel är att produkt- och konstruktionsdata, exempelvis ritningar, underlag och stycklistor eller BOMar (Bill of Materials), kan föras över mellan systemen bara med i princip ett knapptryck. Ett vanligt upplägg i sammanhanget är att man tar fram eBOMen (engineering BOM, ”konstruktions-BOMen”) i t ex Siemens cPDm-system Teamcenter, för att sedan föra över denna till SAPs ERP-system där mBOMen (manufacturing BOMen, ”tillverknings-BOMen”) tas fram. Genom att utveckla en långt driven integration mellan systemen minskas risken för att felaktig eller inaktuell data/information används. Men det finns betydligt mer, som vinsterna med ett vässat arbetsflöde, bättre lagerhantering, goda möjligheter att automatisera processer och annat.
Bland systemen man kan koppla ihop med PDM finns alla viktiga ERP-lösningar, som SAP, IFS och flera andra.