It is a positive Ed Fontes who meets us at the head office in Stockholm. He is satisfied with the situation and development of the entire ”Multiphysics package”, including both technological and commercial outcome.
”What we are doing is right. Today, companies’ products are moving towards ever greater complexity. This increases the need for solutions that can handle the development of advanced products in entire teams, without the need for a PhD to be able to use and interpret simulation software. This is now more or less history. Our vision revolves around simplicity on the surface making it possible to handle complexity in depth. By building our solutions according to this, we can contribute to spreading the use of multi-physics solutions and increase the ability to create better products through the sharpened decision-making basis,” he asserts.
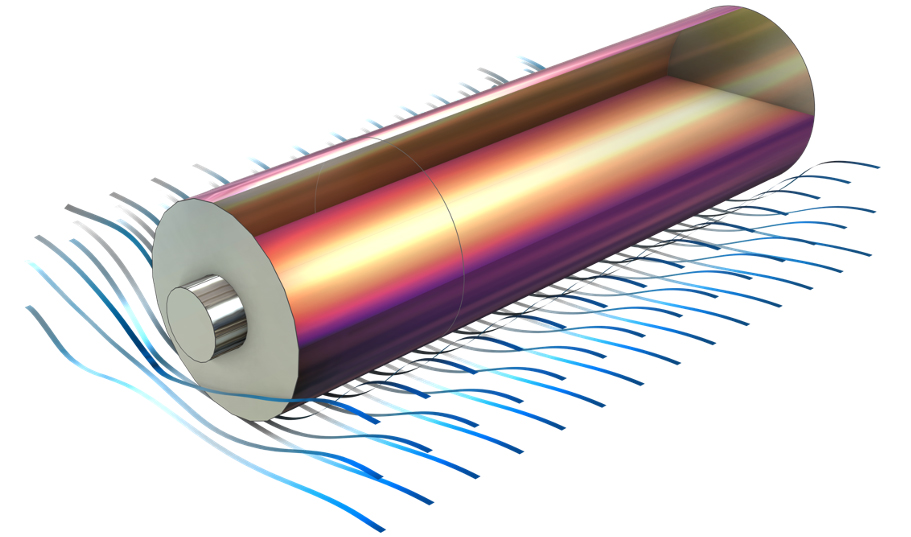
Great demand for battery solutions
On the commercial side, COMSOL’s development chief notes an interesting trend: the demand for multiphysics models for batteries is very high. It is encouraging and shows an underlying need, despite the fact that the battery industry has been tamed by an automotive market where the sale of pure electric cars and hybrids as a share of total sales have tended to point downward for some time. One interpretation of the increasing demand is that the technical development in the battery area, regarding, among other things, sustained performance, is very important to speed up business.
”There is a lot to it and one effect that is really a task for multiphysics simulation is the charging and discharging of batteries. In the lithium-ion battery, the electrodes are made up of small particles where lithium metal is reduced and oxidized. When the lithium enters the particles, they expand, when it leaves the particles, they shrink again. This gives rise to mechanical stresses in the electrodes which eventually fatigue, leading to the formation of cracks. These cracks eventually cause aging of the electrodes which lose performance. Low and high temperatures also give a ’supplement’ to aging. To model this, a coupled electrochemical, structural mechanical and heat balance model is required,” comments Fontes.
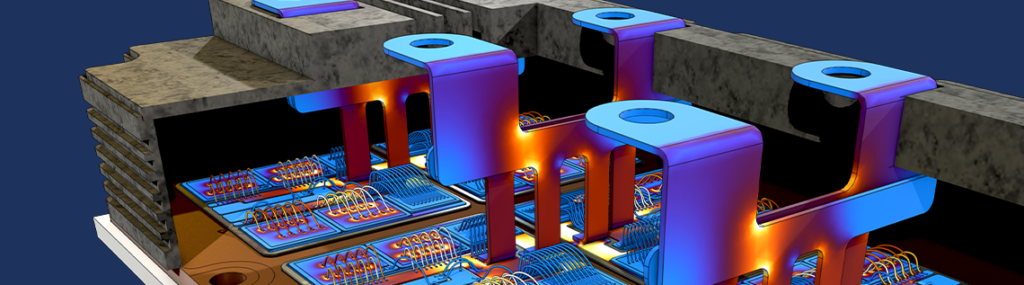
A multi-physical reality must be reflected in multi-physical digital models
A heavy point of multiphysics simulations typical of especially the environments COMSOL Multiphysics offers is that they enable modeling of complex, simultaneous interactions between multiple physics domains that cannot be easily studied experimentally due to cost, time, or safety constraints. Ultimately, it’s about saving time and money, while actually being able to increase quality.
”Exactly,” says Ed Fontes. ”Since processes and products are often controlled by several physical phenomena at the same time, they tend to behave more non-linearly than linearly. So how do you, for example, get a grasp on how complex, only digitally existing 3D models of products functionally behave when they are translated into physical counterparts? Of course, this requires sharp digital simulation and analysis tools. After all, they are governed by more than one type of physics, each of which is normally represented by a set of partial differential equations (PDEs). With our engine, you can basically build on these PDEs as far as you want and can thus describe the total effect,” says Fontes, pointing to an example where current is conducted in a cable. The current develops heat, the propagation of which can affect conductivity, material properties, fluid flows, or interfere with sensitive nearby signaling equipment, etc. Through multiphysics simulation, you can validate that all of this works together as intended. It is in this that the COMSOL Multiphysics math engine provides a unique flexibility; the real experts can even input their own systems of partial differential equations (PDEs) to get exactly the picture they’re looking for.
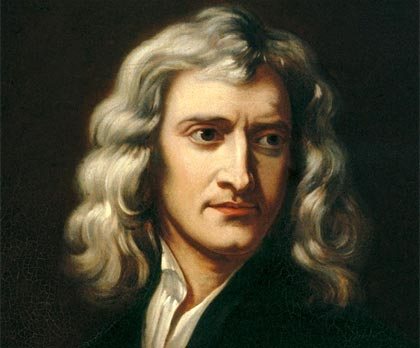
COMSOL’s big trump card
There is an interesting paradox in this in the age of AI and state-of-the-art computing technology. COMSOL’s successful multiphysics software rests heavily on these PDEs and thus also on the 1670-80s discovery of differential equations. It is considered to be the German Gottfried Vilhelm Leibniz, who in the late 1670s formulated the first PDE, which in turn was a consequence of Isaac Newton’s reasoning around physical dynamics and ”flow equations.” It’s hard to say who was first, but the foundation is in any case centuries-old mathematics, which, however, has been refined into today’s state-of-the-art multiphysics simulation solutions. But on the bottom line, it is still precisely this type of mathematics that, some 350 years after its discovery, gives COMSOL a significant competitive market advantage. The company’s development manager smiles at the picture:
”Sure, mathematics is old but, just as you say, so much refinement and expanded capabilities have been added throughout history with things like, for example, diff-equations for electromagnetism and other things from the likes of Euler, Schrödinger, Gauss, Maxwell and other giants. But of course, it is our competitive advantage; since physics is expressed as PDEs, this language already exists. What we do is interpret them and create a numerical model from a mathematic model. It makes things much easier, you write down the equations as you have always done, which minimizes errors and of course also the work of creating numerical models. This is also the main difference between us and Ansys. They have traditionally worked with ready-made numerical models, while ours are, so to speak, created on the fly.”
This PDE scheme is thus one of COMSOL’s competitive trump cards, providing capabilities that really no other player in the multiphysics field can match from a flexibility standpoint, Ansys included.
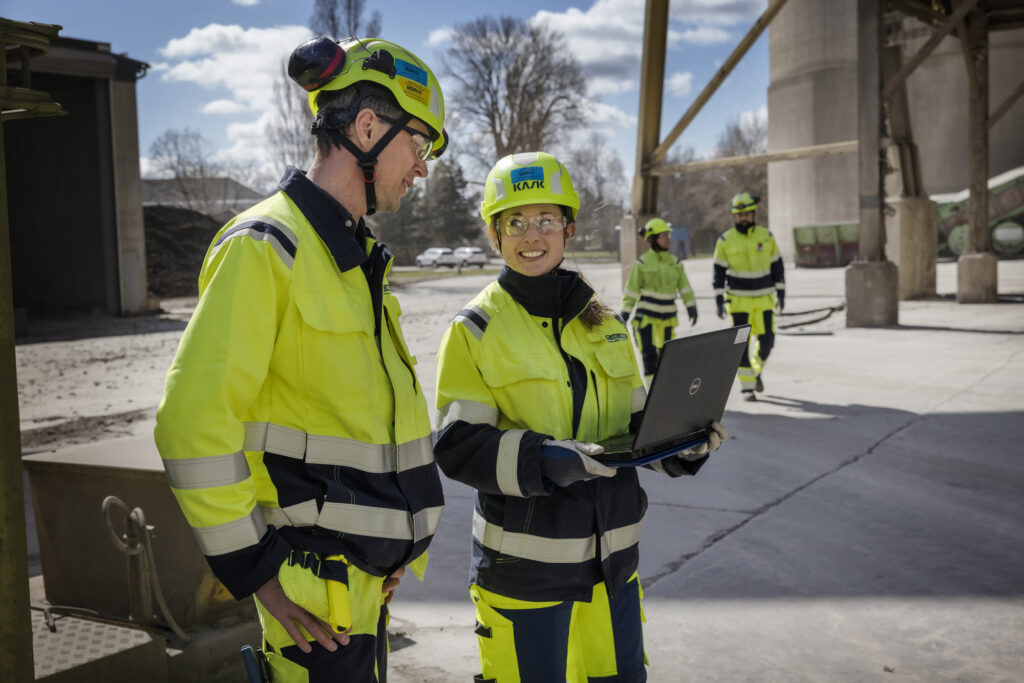
The world’s largest building materials supplier uses COMSOL’s multiphysics
”But of course there are more factors,” adds Ed Fontes. ”I’m talking here about our solutions that have contributed to spreading the simulation and analysis results to a wider circle, yes, actually even beyond the participants in the actual product and production development teams, through our Application Builder. The underlying idea is that the simulation-driven R&D workflow is most successful when colleagues across teams, departments, organizations and businesses can access and contribute to creating accurate models that can be used for innovation, design and optimization.”
To this end, the broader COMSOL Multiphysics platform contains three main workspaces:
• Model Builder: For model builders, there is all the functionality that modeling and simulation specialists need to build, solve, visualize and evaluate physics-based models.
• Application Builder: A connected solution that provides modeling professionals with user-friendly tools to build custom simulation apps for use by colleagues and customers.
• Model Manager: Provides a structured workspace for organizing models and apps, with version control, search and filter functionality, and efficient storage, as well as functionality to copy operational sequences from one model to reuse in another.
This is generally exciting, not least the Application Builder, and PLM&ERP News has, among other things, published a very illustrative case study under the heading: MULTIPHYSICS IN THE CONCRETE WORLD: Simulation app built in COMSOL’s Application Builder guides project decisions on construction sites.
This is about Heidelberg Materials, one of the world’s largest suppliers of building materials, which has given contractors access to multiphysics simulation with a COMSOL simulation app called HETT 22, built by Deflexional. The app enables the company’s customers to use simulation to make informed decisions about cost-effective casting strategies on construction sites. The article is in Swedish but an English version is on its way.
What are surrogate models?
When COMSOL introduced surrogate models in 2023, they were a big step forward. It should be noted that the concept has been further sharpened in the 6.3 version.
“Absolutely, when they arrived, it became possible to build lightning-fast apps by releasing functionality to train surrogate models using machine learning,” Ed Fontes says, explaining that when including the data-driven surrogate models in their simulation apps, users of the apps will get almost instant simulation results based on their input.
”That’s because surrogate models are trained to approximate the behavior of more computationally expensive, full-fledged finite element models, without sacrificing accuracy. Also, with the release of COMSOL Multiphysics version 6.3, the process of training surrogate models itself becomes much faster thanks to support for performing the training on the graphics card.”
There are more interesting capabilities: The ability to both use surrogate models and link simulation apps to external sensors, databases and web services makes it possible to build and run apps as effective digital twins.
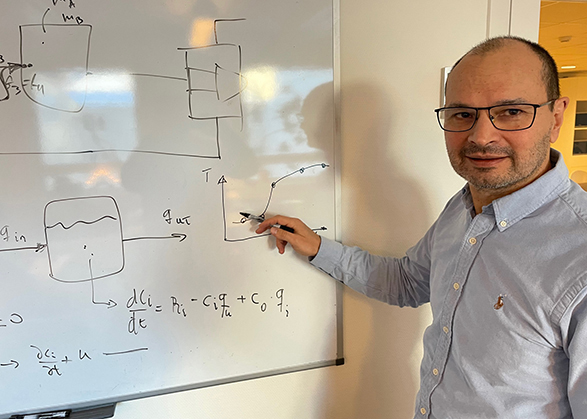
But what exactly is a surrogate model? ”It is simply an advanced functional adaptation that approximates a multiphysics model,” explains Ed Fontes and adds: ”The adaptation requires computing power, as the data is generated by solving the multiphysics model during the so-called ’training’. Given the input, the surrogate model calculates the outcome. If the fit to the multiphysics model is accurate, i.e. if you have ’trained’ the deep neural network or the Gaussian process well, the result calculated by the surrogate model is also accurate and covers many more data points.”
The advantage is that the surrogate model calculates the result lightning fast and for all points within the adaptation interval – ”infinitely” many more than have been used in the ”training” – and requires neither large computing power nor space. It is ”easy”.
Training the network
The surrogate model is thus lightning fast at calculating the outcome (given input data) and the model also takes up very little space, according to COMSOL’s development chief. It can be installed on field equipment and requires very little computing power. Simulation apps can thus run on many more platforms and in many more cases, because the user or process does not have to wait for the result; it comes instantly.
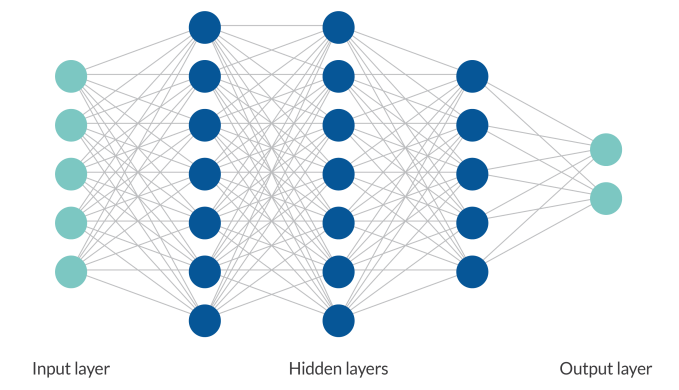
For this, COMSOL, as noted above, uses deep neural networks (DNN, Deep Neural Networks), or artificial neural networks, Gaussian processes and other advanced function approximations. The adaptation of these functions using multiphysics simulations is what is called ”training” the network or the Gaussian process. It all undeniably sounds like AI, or really ML (Machine Learning). Still, this is part of state-of-the-art AI. But Ed Fontes and COMSOL are a bit careful with the labeling here:
”Well, we don’t go out and say, ’we now have ’AI-based machine learning’. This is because such labeling does not explain what we mean, neither to our existing nor potential users. If we say instead, ’data-driven surrogate models with advanced function approximations, such as deep neural networks and Gaussian processes,’ many of our users immediately understand what we mean. Or they can easily look it up, because it’s very specific. Possibly ’AI-based machine learning’ would have worked well for the press and for investors. But for you in the press, we still have to explain what we mean in the end, and we have no investors. Also, it would have felt a bit cynical to try to ride the AI wave by using the term ’AI’ when there is a much more specific and useful description.”
More about the new 6.3 version of Multiphysics
That said, let’s briefly look at other bits that COMSOL points to and discusses in a launch press release:
We start with the new tools for automatic processing of geometries, which it claims, ”facilitate and streamline model development by removing unnecessary details and defects in CAD models, resulting in higher mesh quality and increased simulation reliability.” Users can thus import larger industrial CAD models that were not originally intended for simulation, and use the geometry preparation tools to make the necessary adjustments to achieve robust simulations.
But we also see here the results of the COMSOL developers’ effort to make the life of the engineering teams a little easier: The interactive Java environment enables immediate model changes using COMSOL’s API. A chatbot tool that can generate Java code and answer general questions is also on hand.
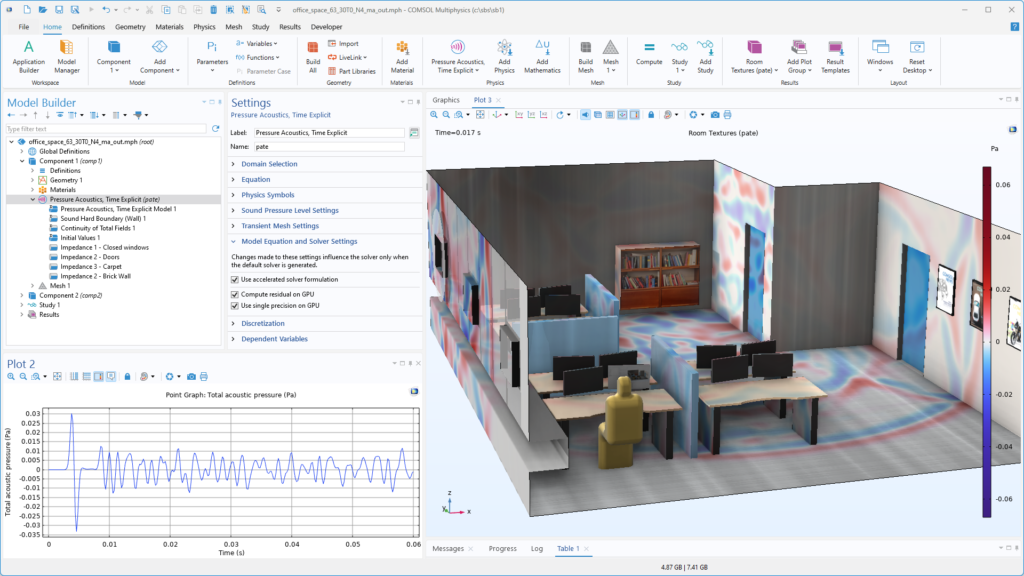
Up to 25 times faster simulations with time-dependent acoustics
We touched on this in the preamble above; the acoustics module now offers GPU support for up to 25x faster simulations of pressure acoustics in the time domain as well as new capabilities for poro-acoustics, including support for modeling anisotropic materials and frequency-dependent material properties in the time domain.
”The new GPU support for time-dependent acoustic simulations is invaluable for engineers working with automotive audio systems or optimizing acoustics in office and residential spaces,” said Mads J. Herring Jensen, head of acoustics development at COMSOL. ”Faster acoustic simulations will help our users to come up with new design solutions and product innovations in a shorter time and more efficiently.”
Detailed simulations for models with electrical discharges
Version 6.3 also introduces the Electric Discharge Module with powerful simulation capabilities that span a wide range of electrical discharge scenarios, including gas discharges at atmospheric pressure as well as breakdown phenomena in liquids such as transformer oil and solid materials such as insulating polymers.
”The Electric Discharge Module provides new modeling capabilities for the design of everything from consumer electronics to high-voltage systems,” said Lipeng Liu, Technical Product Manager at COMSOL. “Simulation of electrical discharges has been a high priority area for us, and it is gratifying to see COMSOL’s strengths in multiphysics come together in this product. Discharge phenomena involve several areas of physics and thus can take full advantage of the potential of COMSOL’s modeling tools.”
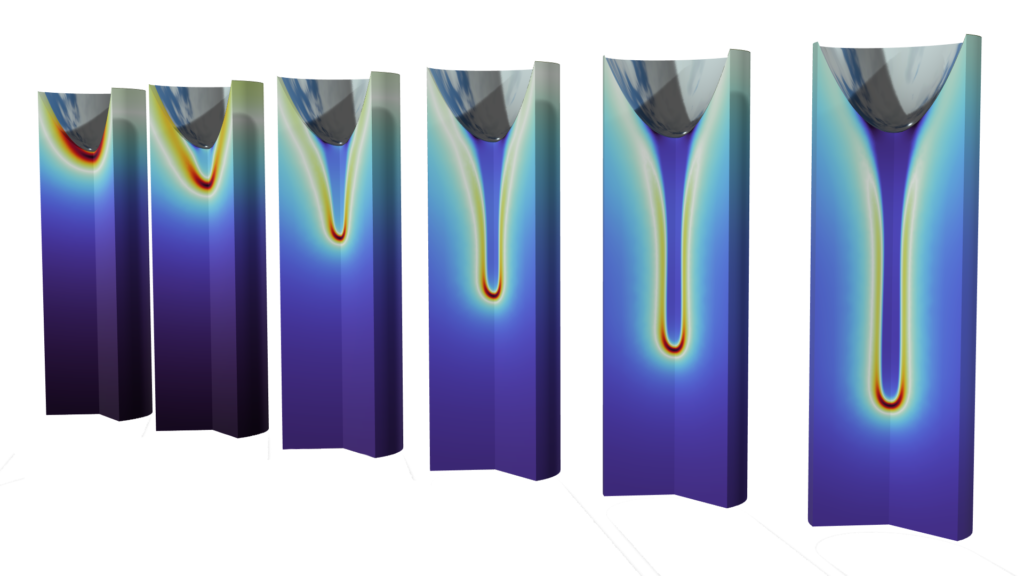
Other news in the product suite
More highlights of COMSOL Multiphysics version 6.3 are:
• Effective data sampling to create surrogate models
• Electromechanical modeling for thin structures, tools for moisture-induced swelling and simplified workflows for spot welds and fasteners
• More accurate electrostatic force calculations for MEMS devices, efficient modeling of laminated iron in motors and transformers, and simplified modeling of periodic structures in wave optics
• Turbulence models with Reynolds stress terms, non-Newtonian flow in porous media and rapid drying simulations with non-equilibrium moisture transport
• Simulation of precipitation and crystallization for particle nucleation and growth with particle size distribution
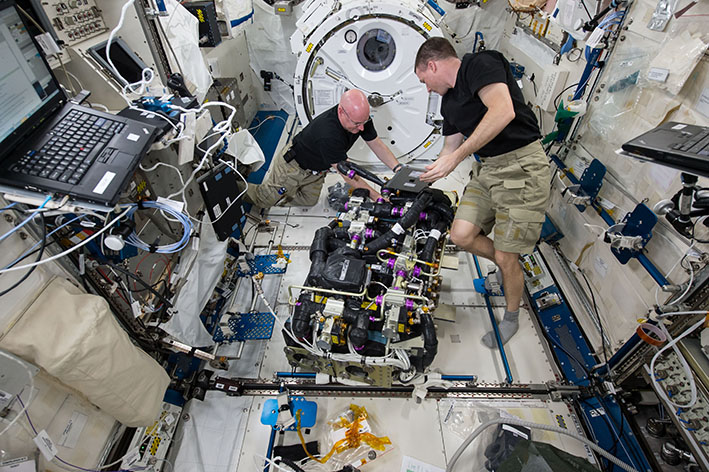
Read more on https://www.comsol.com/story/designing-next-generation-co2-removal-technology-for-better-life-in-space-131721
Acting in a tough market, but the future looks bright
On the global PLM scene, the simulation and analytics (S&A) domain is going through dramatic changes marked by consolidations, such as Synopsys’ acquisition of Ansys and most recently Siemens’ giant purchase (just over $10 billion) of Altair.
At the same time, the commercial pressure on the S&A area remains high. There is great revenue to be had in a world where digital product development has become the general norm. In their initial stages of development, today’s products hardly exist anymore as physical prototypes, but as visual 3D models and geometric descriptions in the form of binary structured algorithms in the form of sequences of ones and zeros. A reasonable interpretation of this is that the growth rate will continue to circulate around a roughly ten percent annual increase for the entire CAE area in terms of corporate investments in a market that in 2025 is estimated to exceed $12 billion in terms of total investments.
For COMSOL, the situation still looks good. It has heavy companies and organizations such as Northrop Grumman, Boeing, NASA, Apple, Ford, Lawrence Livermore National Laboratory and ABB on the customer list and the growth in the last three years has looked good. In 2022, according to analyst CIMdata, revenue landed at $156 million and has since continued to grow.
Generally, COMSOL operates in a market with good growth potential; CIM data expects that the CAE/Simulation & Analysis segment will increase by approx. 10 percent a year until 2027.
The future looks bright for the Swedish CAE player, both commercially and from a technical perspective.