Därmed berörde Maidl vad dagens robotar kan göra, mer än att s a s bara utföra uppgifter. De kan lära sig, anpassa sig och utvecklas med hjälp av funktioner som maskininlärning, ”datorsyn”, navigering och annat. Man behöver heller inte fundera särskilt länge för att inse att BMW – vars årliga bilförsäljning har fördubblats under de senaste tio åren till 2,5 miljoner fordon, uppdelade i flera bilmodeller – haft goda skäl att uppgradera alla delar i sin varianthantering på tillverkningssidan. I genomsnitt handlar det om 100 olika alternativa konfigurationer per fordonsmodell, vilket på sista raden resulterat i att 99 procent av kundbeställningarna unikt skiljer sig från varandra.
Lägg till detta de tiotals miljoner delar och komponenter som strömmar in från leverantörer runt om i världen varje dag, så blir det tydligt att fabrikslogistiken är en enorm utmaning. Dessutom är den helt avgörande för att BMW ska kunna skapa en relevant distributions- och kostnadseffektivitet i tillverkningen.
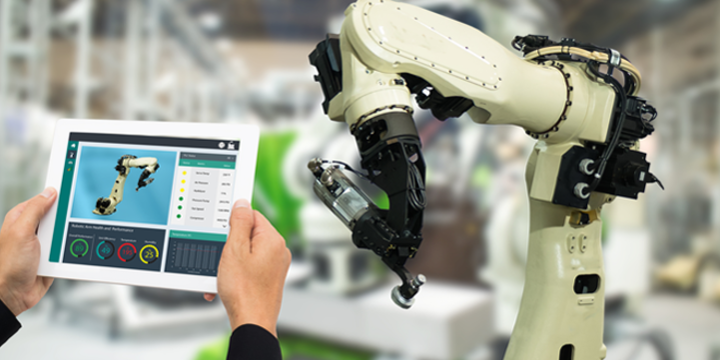
Produktframtagning i PLM-miljöer från PTC och Aras
Innan vi går vidare ska vi bara notera att BMW på PLM- och produktframtagningsidan bl a jobbar med lösningar från PTC (Windchill), Aras (Innovator-sviten som implementerats på R&D-området för cPDm, ”collaborative Product Definition management”) och SAP.
På tillverkningssidan, sett i perspektivet av kopplingar till PLM-systemet, är det framför allt PTCs Windchillsvit med Navigate och ThingWorx-lösningarna (det senare PTCs IoT-plattform) som spelar nyckelroller när det gäller produktdata, konfigurering och annat. På en mer detaljerad nivå handlar det om att med hjälp av Navigate ta en eBOM (”engineering BOM”) från PLM/cPDm-systemet och skapa en mBOM (”manufacturing BOM”), integrera denna med övriga produktionsplanerings-data och distribuera ut på golvet på ett standardiserat sätt för att skapa en flexibel produktion med kapacitet för snabba omställningar.
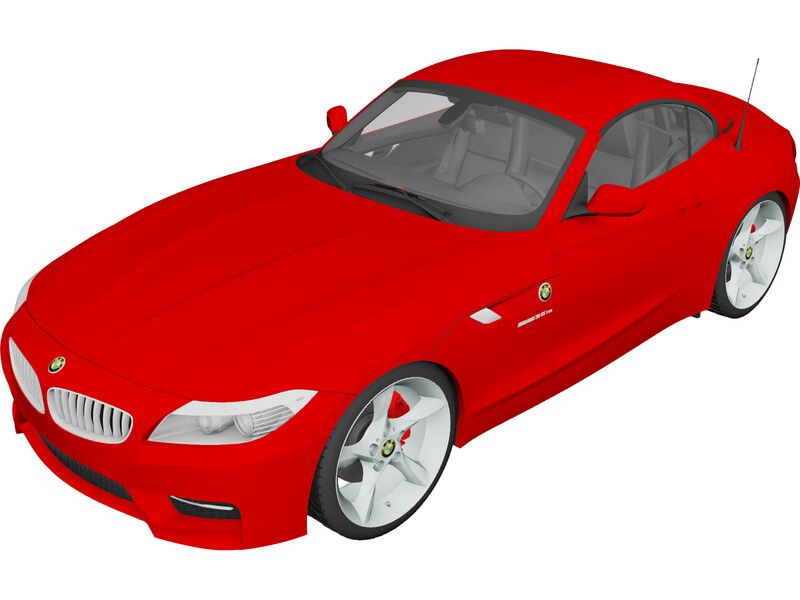
Men här finns förstås också inslag från en rad andra av de kända leverantörerna av PLM-relaterad mjukvara. CATIA från Dassault på CAD-området, från Siemens Digital Industries har ”digital manufacturing-verktyget” Tecnomatix funnits med och på simuleringsområdet har ANSYS viktiga installationer. Men PTC har alltså en mer bärande roll.
PTC-basen, Jim Heppemann, konstaterade i en tidigare PLM&ERP News-intervju att Windchill och Navigate möjliggör kortare ledtider och snabbare ”time-to-market” hos den tyska fordonstillverkaren.
– BMW Group utnyttjar Windchills kapabiliteter för att konfigurera stora mängder och komplexa data för fordonets struktur för att därmed uppnå målet att masstillverka kundanpassade fordon, samtidigt som man får ökad flexibilitet och når högre kvalitet.
Han pekade särskilt på att ThingWorx Navigate stöder samtidig (”concurrent”) produktionsplanering, vilket gör det möjligt för BMW Group att förkorta den totala tiden till marknaden. Med denna mjukvara blir det möjligt att uppnå ökad produktivitet, bland annat beroende på att samverkan i produktionsprocesserna underlättas av förenklad dataåtkomst. Det gör det möjligt för användare att få tillgång till exakt produktinformation.
Hur bra eller eventuellt mindre väl detta fungerat ska vi låta vara osagt. Klart är i alla fall att utvecklingen hela tiden rör på sig hos den tyska fordonsjätten och den digitala transformationen går kontinuerligt vidare, liksom hos i stort sett alla automotivespelare.
Mer än 30 miljoner parter och komponenter
I BMWs fall är alltså utmaningen att få till en effektiv tillverkningslogistik kring de mer än 30 miljoner delarna från 4 500 leverantörssajter, dessutom i realtid. Idealbilden är att arbetare meddelas om kommande uppgifter på smarta armbandsklockor, medan helt autonoma robotar som transporterar leveranser visslar förbi. Annat handlar om lastbilssläp som guidas av lasrar till hamnen, där de lastas och lossas av ett annat ”team” av robotar.
Detta sagt stod det klart för BMW Group att man behövde vässa sin förmåga att producera denna mängd av specifikt konfigurationsbeställda fordon i sina fabriker. Så, hur löste man problemet?
Ett svar kom alltså under NVIDIAs GTC 2020-event: Man satsar på NVIDIAs nya Isaac Robotics Platform.
– BMW Group leder därmed vägen till en tid av automatiska fabriker, utnyttjar genombrott inom AI och robotteknik för att skapa nästa nivå av mycket anpassningsbar, ”just-in-time, just-in-sequence-tillverkning”, sa NVIDIA-chefen, Jensen Huang.

maskinerna i systemet kommer att tränas på både verkliga och ”syntetiska data”, med BMW-personal över hela världen som kan jobba med simulering i NVIDIAs Omniverse-miljö.
BMW kommer sedan att släppa ett nytt sortiment av flera AI-aktiverade robotar byggda med Isaac Software-utvecklingspaket, som drivs av Nvidia Jetson och EGX-kantdatorer.
Djupa neurala nätverksalgoritmer
Samarbetet mellan de båda företagen är baserat på att skapa ett ”end-to-end-system” med hjälp av en enda robotikprogramvaruarkitektur med en omfattande verktygsarsenal inom ramen för Isaac-plattformen; bibliotek, referensapplikationer och förhandsskapade ”Deep Neural Network-algoritmer”.
Så här ser de viktigaste av de ingående plattformskomponenterna ut:
• AI-aktiverade robotar drivna av vad NVIDIA betecknar som sin, ”högpresterande Jetson-plattform och EGX-drivna ”edgedatorer”. När det gäller Jetson AGXTMsystemet kan tilläggas att det använder kraften i djuinlärning för att driva smart inbäddad robotik.
• NVIDIAs DGX-system för att träna nya AI-robotar.
• En simuleringslösning: NVIDIA Isaac-simuleringsteknik (Isaac Sim), byggd i bolagets Omniversemiljö, för att testa robotarna i virtuella fabriksmiljöer.
• NVIDIA Quadro GPUer för att göra rendera syntetiska maskindelar för snabbare utveckling.
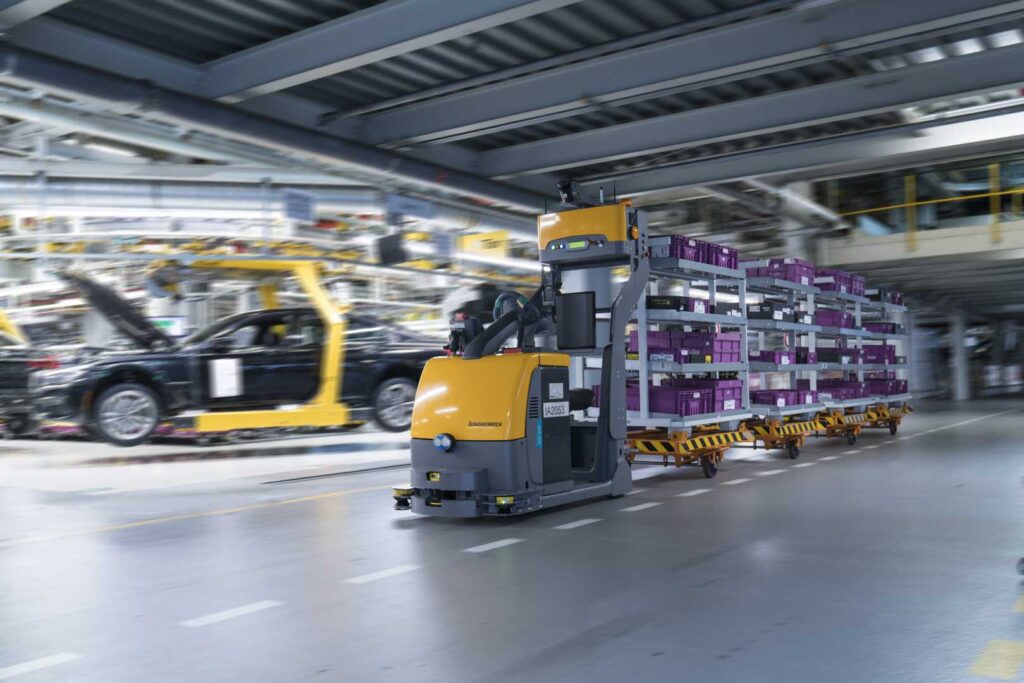
En färdigtillverkad bil var 56:e sekund
I detta menade NVIDIA-chefen vidare i sitt anförande att vad BMW gör är att man, ”omdefinierar biltillverkningen” med fabrikslogistik byggd ”end-to-end” på AI.
Systemet kommer från start inte att etbleras överallt, men i bolagets modernaste fordonsfabriker kommer man nu att inleda processen att bygga verksamhetslogistiken på avancerad AI-datoranpassning och -visualisering för logistikrobotar, dataanalys och simulering med hög upplösning för robotutbildning och fabriksplanering.
Detta, menar man, ligger också i linje med BMWs åtagande att tillhandahålla kunderna ”Power of Choice” (”kraftfulla valmöjligheter”). Det rör si´g här inte heller om småpotatis.
BMW Group producerar 10 000 bilar varje dag. De erbjuder 40 bilmodeller, med i genomsnitt 100 olika alternativ per bil – vilket resulterar i 2 100 olika möjliga konfigurationer.
För att göra detta möjligt tar man in 30 miljoner delar per dag från 1 800 leverantörer i sina 31 fabriker. 230 000 delnummer är organiserade i brickor för att producera 10 000 ”build-to-order-bilar” varje dag.
Detta kan nu skötas av smarta transportrobotar, STR, och något man kallar SortBot, via NVIDIAs Open Isac Robotics Software Platform, i ett logistikupplägg baserat på ”just-in-time-” och ”just-in-sequence-upplägg”.
Isaac-plattformen har en rad multimodala funktioner, inkluderat rörelseplanering, objektdetektering och positionuppskattning. Robotarna visas i Isaac Sim (Omniverse) och levererar exakt fysik och realism.
Plattforen hanterar dessa sina uppgifter via ”navigeringsrobotar”, som transporterar material autonomt, medan ”manipuleringsrobotar” väljer och organiserar delar.
NVIDIA-tekniken används för att designa, träna, utveckla, simulera och distribuera systemet.