Den globala förändring som pekas på i ingressen har motiverat de flesta fordonsföretag att investera kraftigt i de verktyg, teknologier, infrastruktur och affärsmodeller som behövs för att göra framtiden för nollutsläppsbilar möjlig. Några exempel:
- GM planerar att bara erbjuda helt elektriska alternativ, ur ett försäljningsperspektiv, till 2035.
- Reuters rapporterar att biltillverkare kommer att spendera cirka 1,2 biljoner dollar på elbilar och batteriteknik år 2030.
Det finns fler, men de flesta landar i att man senast runt 2040-2050 kommer att kunna erbjuda fordon med enbart helelektrisk batteri- eller vätgas-/bränslecell-genererad eldrift, alternativt hybrida fordon med nollutsläpp, både vad avser produktframtagning och drift.
Detta sagt ska vi titta lite närmare på de fyra verktyg som Hexagon pekar på som essentiella:
1. AUTOMATION garanterar kvalitet och hållbar industri
Kanske är att ytterligare automatisera processerna det mest intuitiva steget för att göra fordonstillverkning till en hållbar industri och öka utvecklingen av fordon utan utsläpp. Detta, menar Hexagon, ”bör vara instinktivt, precis som bilindustrin gång på gång har återuppfunnit hur man tillverkar och konstruerar produkter sedan sin tillkomst.” Från Fords rörliga löpande band till Toyotas ”magra” tillverkning (lean manufacturing), är denna typ av att återuppfinna fabriken mot maximal effektivitet. Den nuvarande rörelsen mot hållbarhet behöver bara ändra perspektiv på effektivitet till att inkludera avfall, kostnader, prestanda, kvalitet och miljö.
Oavsett om framtiden för bilar med nollutsläpp i slutänden blir batteri- eller bränslecells-baserade – eller en kombination av dessa båda – kommer automatisering att vara en viktig del av mixen på grund av sin potential att skapa effektivitet, anpassningsförmåga, skalbarhet, tillförlitlighet, motståndskraft och kvalitetsgaranti — eller sammanfattningsvis dess hållbarhet.
Som ett resultat kan denna process inte involvera traditionellt automationstänkande, där en linje gör en sak. Istället måste organisationer adoptera automation som snabbt kan anpassa sig till ibland betydande produkt ändringar.
– Med anpassningsförmåga sker ett skifte i tillvägagångssätt, säger Nicolas Lachaud Bandres, global chef för Automated Solutions på Hexagons Manufacturing Intelligence-division. Och han fortsätter: ”Förut handlade det att bygga skilda produktionslinjer för varje modell. Idag behöver en linje rymma tre till fem modeller. Denna mångsidighet kan bara göras med automatisering.”
Under tiden, ur ett kvalitetsperspektiv, måste automatisering fortfarande säkerställa att varje del eller produkt tillverkas korrekt. I detta överväger företag att använda mer automation och AI. De vill förlita sig mindre på mänskligt arbete och mer på teknik, och de föredrar att inte förlita sig alltför mycket på bara programvara.
– Detta koncept med automatisering av processer bör inte begränsas till bara produktionsanläggningar, hävdar Lachad Bandres vidare. När allt kommer omkring är automatisering förmågan att replikera resultat brett och med färre fel, slöseri och omarbetning. Det gör det möjligt för människor att fokusera på mervärdesarbete istället för att leta efter hur man gör något. Så, konceptet kan tillämpas överallt från försäljning till underhåll. Tänk till exempel på designen av en produkt och dess tillverkningslinje.
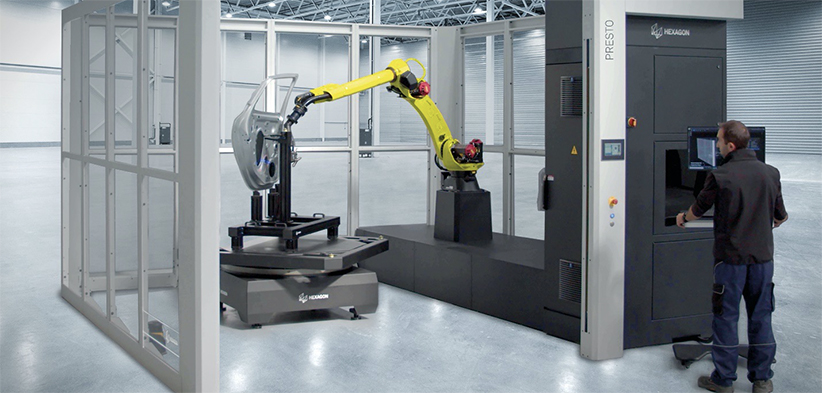
Ingen vill fortsätta att klicka på knappar för att utföra batch-jobb, säger Platten. När man vill göra många saker och ha många variabler behöver man många körningar av sina modeller för att optimera. Med simuleringar går det snabbt att hitta optimerade modeller för olika varianter av batchjobb.
– I det här scenariot kan ingenjörer designa produkter och deras tillverkningsprocesser bättre för att säkerställa att den bästa kvalitetsprodukten konsekvent kommer från linjen – även innan marken är bruten på tillverkningsanläggningen, summerar Michael Platten.
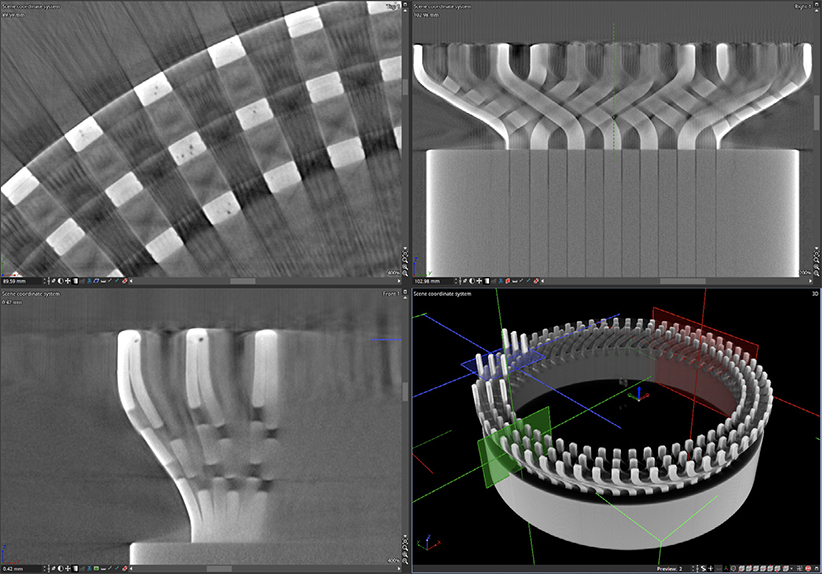
2. Kortare tid till marknaden kräver VIRTUELL PROTOTYPNING
Den roll simulering spelar inom en hållbar fordonsindustri går långt utöver dess förmåga att förbättra automatiseringar och kvalitetskontroll. Dess kanske största inverkan är förmågan att drastiskt minska behovet av dyra och tidskrävande fysiska prototyper.
– Den främsta anledningen är tid och pengar, säger Platten. När ditt fordon lanseras är det viktigt att nå lanseringsdatumet. Man måste vara på marknaden vid rätt ställe för att USPen (Unique Selling Proposition) ska sticka ut. Att göra dessa releasecykler snabbare kräver konvergering till en lösning där arbetsflödet är minimerat.
De nuvarande utvecklingscyklerna för bilindustrin tenderar att gå allt snabbare, så det finns ingen tid att bygga fysiska prototyper med innovativa förändringar.
– Du har inte råd att gå långt in i utvecklingen och ta reda på att det inte kommer att fungera. Hastigheten måste vara: en idé från hjärnan går in i datorn för att se om den fungerar.
Med simuleringar som fungerar som digitala prototyper kan ingenjörer utforska designutrymmet ytterligare och testa innovativa idéer genom att misslyckas snabbt. Detta fungerar perfekt för en industri som ännu inte har bestämt sig för en föredragen drivlina, för istället för att bara designa batteribaserade nollutsläppsfordon kan ingenjörer också köra igenom designutrymmet med bränsleceller. Kanske upptäcker de efter några simuleringar en modell som enkelt kan anpassas till båda kraftsystemen.
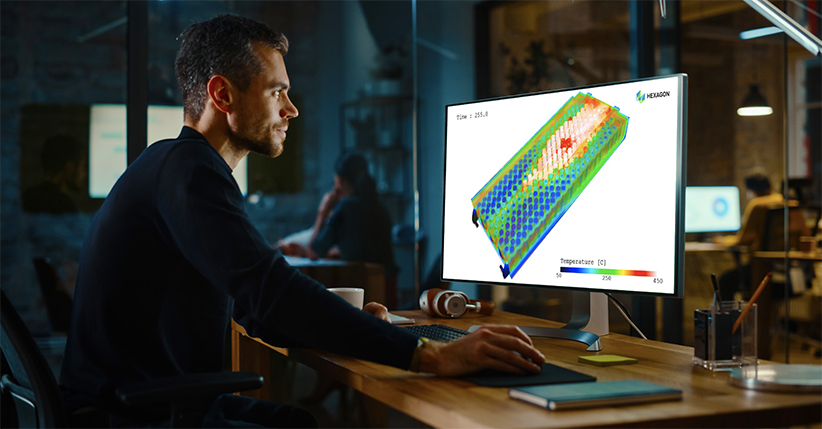
3. Den digitala tråden – vägen för snabba förbättringar av livscykel
Det är lätt att säga att verktyg som simuleringar och automatiserade system ska prata med varandra, men att sätta upp de digitala trådarna mellan dem – och allt annat – är en utmaning eftersom fordonsindustrin tenderar att bli nedtystad och ofta splittrad.
En av de mest utmanande sakerna inom fordonsutveckling är att göra nya komponenter eftersom man behöver sätta ihop team från olika företag och nivåer i leverantörskedjan. Att dela data har alltid varit komplext, eftersom varje del som designas ofta är gjord i en annan geografi och ett annat företag.
Detta har tidigare lösts genom att ett team gjorde en del och andra sedan gjorde andra delar och sedan upprepade alla utifrån vad de andra designade.
Syftet med den digitala tråden är att bryta ner dessa silos så att alla inblandade i produkten, från design till tillverkning och produktunderhåll, kan arbeta på samma data, i realtid, från en enda källa till sanning.
– På detta sätt har du något tillverkningsbart från slutet av designen utan någon iteration mellan organisationer. Den är redo att tillverkas, säger Stephen Graham, VP och chef för Nexus på Hexagons division Manufacturing Intelligence.
Hexagons Kah Khoon Goh, VP regionansvarig för försäljning och smart tillverkning på Manufacturing Intelligence-divisionen tillägger:
– Ingenjörer vill ha en lösning som kan göra det möjligt för dem att bryta silon mellan design-, produktions- och kvalitetsavdelningarna. De vill ha en plattform som tillåter dem att samarbeta effektivt med resultat från simuleringar, CAD-filer och kvalitetsdata, så att de kan ha ett aktivt samarbete.
Han tillägger att det finns ett växande fokus på att integrera tillverkningsprocesser med mätutrustning och digital kvalitetsstyrning för att samla verklighetens data. Denna data kan sedan jämföras med simuleringar, vilket möjliggör en återkopplingsslinga för kontinuerlig förbättring. Genom att utvidga denna logik bortom tillverkning och design är det inte svårt för att se hur en hel produktlivscykel simuleras, övervakas och optimeras ur ett hållbart industriperspektiv med digitala tvillingar.
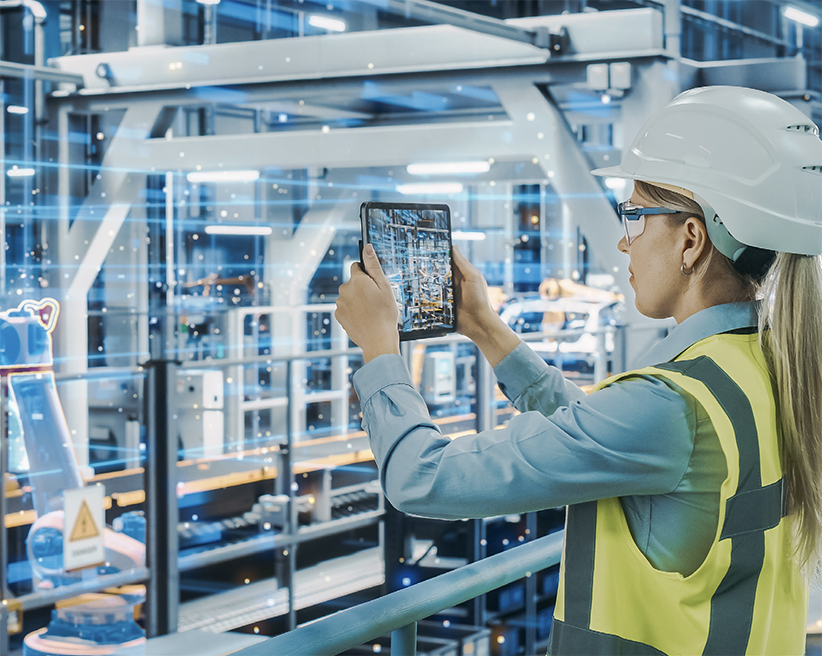
4. AI, ML och DJUPT LÄRANDE skapar hållbarhet och produktivitet
Med den digitala tråden etablerad kommer, enligt Hexagon, möjlighet till betydande optimeringar av nollutsläppsfordon på en systematisk nivå. Men data som finns i den digitala tråden blir värdelös om den är inaktiv efter den första användningen, vilket gör dessa optimeringar svåra. Detta gäller särskilt när datavolymen som är associerad med digitala trådar är för stor för att enkelt kunna bearbetas. Det är här artificiell intelligens (AI) och maskininlärning (ML) kommer in i bilden.
Michael Platten förklarar att med AI och ML kan ingenjörer simulera mycket på en mängd olika saker.
– Ett av nyckelområdena för modellbaserad systemteknik är till exempel att modellera hela fordonet. Även med sub-modellering på lägre nivå hjälper ML-verktyget att påskynda variabilitets-analysen och optimeringarna. Du kan optimera en växel för att göra den effektiv, optimal och tyst, och designen tar några minuter eller sekunder, säger han.
Genom att samarbeta med AI- och ML-verktygen med data från den digitala tvillingen kan den smarta optimerings-körningar utnyttja IoT-återmatade verkliga data från produkter på fältet, utrustning i fabriken eller andra simuleringar.
– Föreställ dig att du har en serie däckmönster och en databas med resultat i laboratoriet. Genom att koppla in det i ett ML-verktyg kan algoritmen tänkbart lära sig vilka prestanda man kan förvänta sig av helt nya mönster – även före fysiska tester eller simuleringar.
En liknande logik kan ställas in på fabriken. Istället för att köra simuleringar för att förutsäga stillestånds-tider på kort sikt kan AI tänkas förutsäga dem i god tid i förväg. Denna information kan användas för att eliminera oväntade driftstopp, nästan helt, genom förebyggande underhåll. Genom att koppla ihop tekniken med digitala tvillingar kan det till och med vara möjligt att förutsäga var problemen kommer ifrån.
Kort sagt, med AI och ML kan fordonsföretag förbättra kvaliteten på nollutsläpps-fordon samtidigt som de sparar tid och kostnader.
AI- och ML-modeller måste tränas, och det kan vara knepigt. Men när det väl är gjort är de innovativa och produktivitetsfördelar som AI producerar skalbara.