Inget står stilla i den produktframtagnings och -användningsdynamik som präglar dagens utvecklingsmiljö:
”Vilken nytta har ett företag som JBT av modern PLM-teknologi som digitala tvillingar, trådar, IoT, IIoT och AR (Augmented Reality)? Hur skapar man hållbara affärsmodeller kring de här bitarna? Och hur får man ihop det nya med det man redan har?”
Detta är hyperintressanta frågor som Leif Olsson ständigt funderar kring, tar fram nya lösningar för och sjösätter piloter kring, tillsammans med bolagets PLM-partner, PDSVISION, en av Europas största PTC-relaterade konsulter.
– Absolut, är det så, men vi ska minnas att teknik inte står för sig själv, säger Olsson och fortsätter:
– Teoretiskt är det inget större problem att sätta upp modeller som ser bra ut, kring det nya. Samtidigt ska detta integreras i ett existerande, historiskt sammanhang där teknik, metodik, affärsverksamhet, utrustning och annat ska samsas om utrymmet i landskap som sällan präglas obegränsade resurser ifråga om tid, personal och pengar.
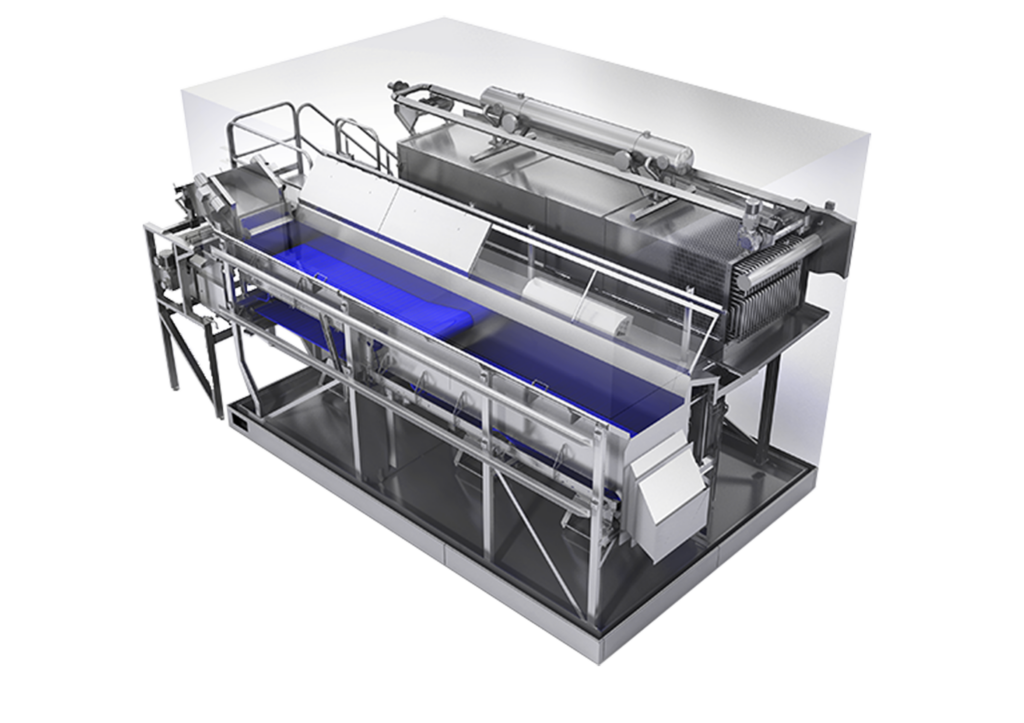
ATT BALANSERA DET GAMLA MOT DET NYA
Att utveckla framgångsrika modeller i detta handlar om att balansera och integrera nysatsningar med äldre teknik, hitta lönsamma ”business case”, övertyga kunderna om värdet av det nya och samtidigt hinna med att sköta den ordinarie produktutvecklingen och produktionen.
– Det ligger onekligen en hel del komplexitet i denna helhet, säger JBT’s PLM-ansvarige, men konstaterar samtidigt att ingen idag har råd att luta sig tillbaka och vara nöjd med det man har. Vill man vässa konkurrenskraften måste man ständigt vara på tårna för att inte bli omsprungen. Vår resa mot innovativa lösningar pågår ständigt och vi är på väg bort från bilden av en utpräglad mekanisk industri för att istället gå mot lösningar där mekanikinnehållet minskar och elektronik, sensorer, mjukvara och IoT-styrning och prediktivt underhåll ökar radikalt.
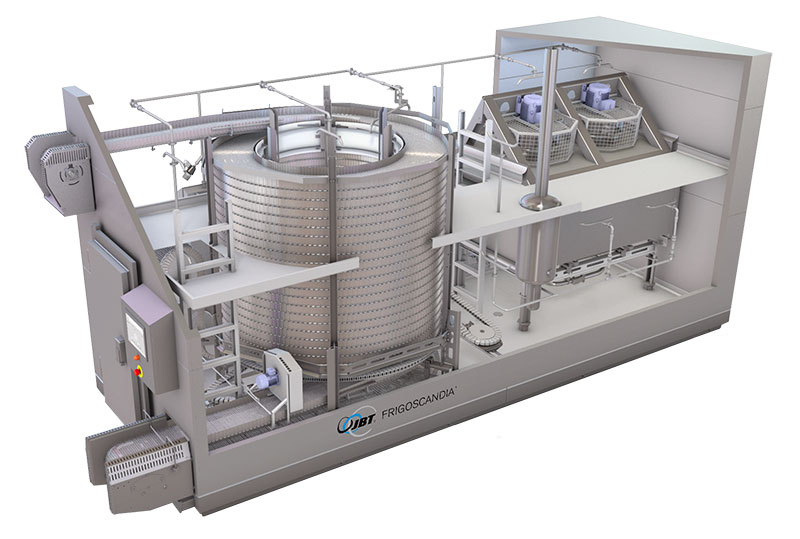
OM PTC-MILJÖERNA OCH BETYDELSEN AV EN VASS PLM-PARTNER
Till saken hör att bolaget har två divisioner, dels ”Food tech”, där tonvikten ligger på industriella frysutrustningar för allt ifrån grönsaker som ärtor till bröd och kyckling-nuggets, dels ”Aero tech-divisionen”, som tar fram flygplatsutrustningar, som transportfordonen som flyttar på flygplanen och annan serviceutrustning. Totalt har bolaget 6 000 anställda och på den svenska livsmedelsteknik-divisionen jobbar man med utveckling och produktion av industriella frysutrustningar och faktiskt också ugnar.
I samarbetet mellan bolagets anläggningar, i Ohio (USA), i Skottland och delvis den i Brasilien, har man i dagsläget samma PDM-system (Windchill/PDM Link) som gemensam plattform via vilken man huvudsakligen utbyter CAD-data.
När det gäller PLM-verktygen arbetar man som sagt i PTC-dominerade miljöer, med Windchill som cPDm-plattform (collaborative Product Definition management) och en proprietär konfigurator, som dock är på gång att integreras i Windchill.
På CAD- och simuleringssidan är det PTC’s CREO som gäller, med visst stöd av ANSYS ifråga om simulering. Ugnarna däremot designas digitalt i Autodesks 3D CAD-mjukvara Inventor.
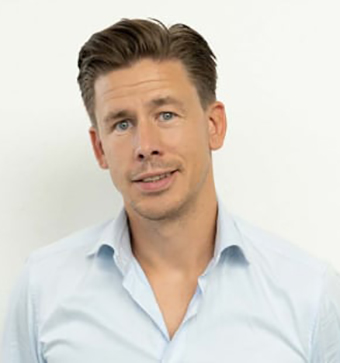
En nyckelroll spelas också av bolagets PLM-partner, PDSVISION; varför är en kompetent konsult av så avgörande betydelse?
Det hela hänger till stora delar ihop med produktframtagningsvärldens just nu så dramatiska teknikskifte. Tjänsteutbudet relaterat till sånt som PLM, IoT och vässade användarupplevelser påverkas starkt av detta. Behovet av kvalificerad rådgivning blir därför mer nödvändigt och viktigare än någonsin. Men hur påverkas de råd som konsulterna tillhandahåller mot bakgrund av sånt som digitaliseringen, nya ”out-of-the-box-lösningar”, explosionen av nya plattformar, IoT och den växande produktkomplexiteten?
Tempot är högt uppdrivet, konstaterar PDS-chefen, Otto Wetterlin. Vad man tror på vid en tidpunkt i tiden är en sak, men utvecklingsdynamiken kan i nästa steg leda mycket längre än man i sin vildaste fantasi kunde föreställa sig. Men någonstans måste man hoppa på tåget. Vart leder det hela?
– Med IoT, AR, additiv teknik och annat blir alternativen många, säger Wetterlin. Men lika mycket som all ny teknik påverkar produktionsprocesserna, måste ’PLM-legacy’ tas med i ekvationen för att det hela ska bli framgångsrikt. Integration mellan gammalt och nytt är en affärskritisk överlevnadsfaktor och framgångsrik transformation kräver effektiva broar. Vi har jobbat mycket med JBT kring datamigrering av legacy, integration och kring vad man kan åstadkomma med nya teknologier.
Det är absolut av stor vikt att ha en proaktiv partner på resan in i framtiden, säger Leif Olsson.
– Har man gjort samma sak i 25 år kan det i en organisation, där allt fungerar bra, vara svårt att byta tankebanor. Samtidigt är frågan om framgångsrika satsningar på ny teknologi och teknik ett måste. PDSVISION är lyhörda och bra på att guida rätt om tanken springer iväg. Vi diskuterar om det mesta kring processer, designmetodik, konfiguration och testbitarna med dem.
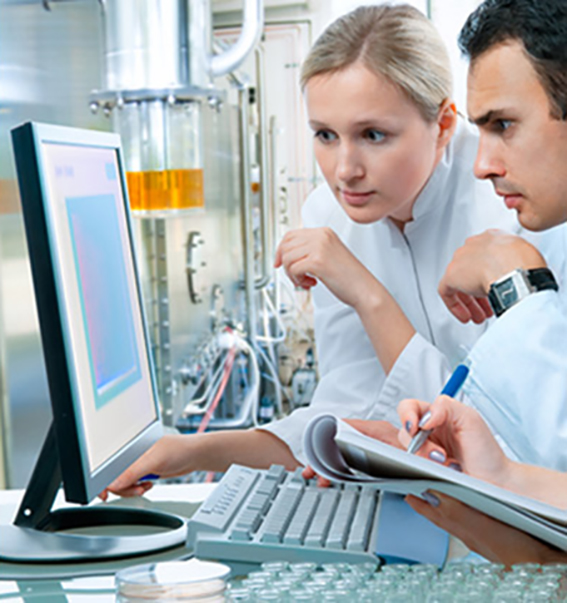
DÄRFÖR ÄR FRYSTEKNOLOGI EN TEKNISKT KOMPLEX UTMANING
Beväpnad med detta kraftfulla mjukvaruartilleri, lösningsplattformar och konsultstöd attackerar och utvecklar Leif Olssons team lösningar för tuffa teknik- och tillverkningsutmaningar som relaterar till bolagets produktion vid Helsingborgs-anläggningen. Men att frysa färska grönsaker, varför är det en utmaning?
– Flera skäl. Det handlar ju inte om några få ärtor i en förpackning, utan om tonvis av färska, nyskördade ärtor. I de upp till 20 meter långa och sex meter breda processlinor för frysning vi utvecklar måste det gå undan. Tid är pengar och ärtorna i sig är ömtåliga och måste hanteras inom snäva tidsramar när skörden kommer in till livsmedelsfabriken. Speed är därför framgångskritiskt.
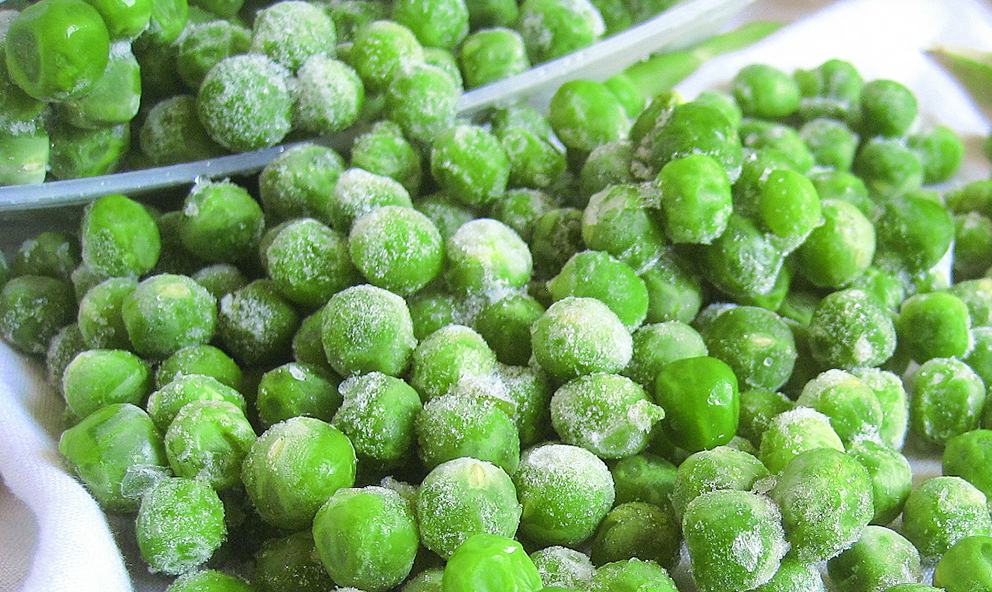
Men det finns andra utmaningar också. Att frysa in nybakat bröd är en sak, ärtor en helt annan. Bröd innehåller mycket luft och har därmed en helt annan densitet än de betydligt mer ”solida” ärtorna. Detta kräver olika tekniker.
– Luftinnehållet i bröd gör att det fryser långsamt, medan de tätare ärtorna fryses snabbare, förklarar Olsson. Det betyder att man måste hantera kylande luftströmmar på olika vis i utrustningarna. För ärtorna handlar detta bl a om att blåsa bort luftlagret närmast ärtornas yta. Temperaturen där skiljer sig från den inblåsta luftens och måste bort för att frysningsprocessen ska bli effektiv.
Detta i sin tur betyder att man i produktutvecklingen av maskiner dels har en hel del att göra med varianthantering, som alltså hänger ihop med att anpassa respektive maskins kapabiliteter till vad det är som skall frysas in, liksom att anpassa utrustningarna till fabrikslaytouten, och dels att man i utvecklingsarbetet använder sig av CFD-simulering av luftflöden för att optimera kyleffekterna relaterat till livsmedlen som ska frysas.
– Precis, säger Leif Olsson. Varianthantering är en av utmaningarna i produktutvecklingen och vi jobbar baserat på moduler, som matchar olika konfigurationskrav. Maskinutrustningarna ska i detta inte bara möta olika produkter för frysning, utan ska också, som sagt, matchas in i varierande fabrikslayouter. Kunderna levererar specar till JBT, som baserat på detta avgör vilken konfiguration som ska användas.
– Vi har tagit fram egenutvecklade beräkningslösningar för att matcha behoven, berättar Olsson. Dessa beräkningar matas sedan in i designprogrammet (Creo) där dimensionerna sedan anpassas till behoven.
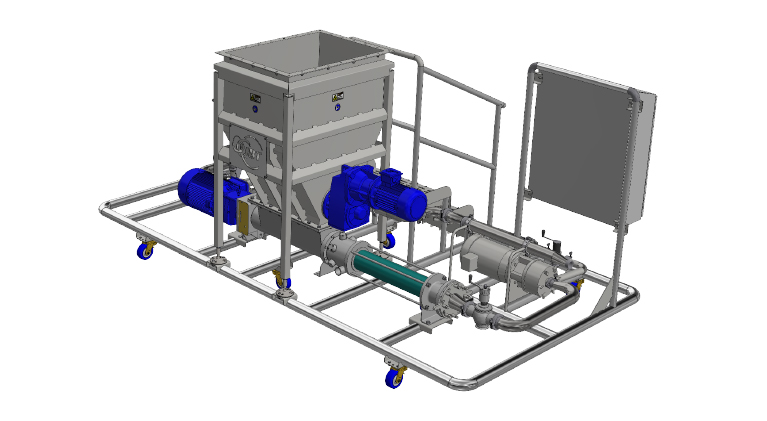
KONFIGURATORER PÅ VÄG ATT INTEGRERAS I WINDCHILL
Men som sagt – inget står stilla. Idag jobbar man med flera projekt, bl a handlar det om att att den egenutvecklade konfiguratorn är på väg att integreras i Windchill och man har också en säljkonfigurator på gång att kopplas upp direkt mot Windchill.
Säljarna ska, är tanken, kunna konfigurera krav som kunden har, t ex med avseende på spänningar, tillbehör och annat, och valen matas in i Windchill för att skräddarsys i en lösning.
– Vi tror att det finns en hel del att hämta här ifråga om kortare utvecklingstider och konfigurationslösningar har definitivt potentialen att kunna bidra till detta. När det gäller diskussionerna med kund och vägen till tillverkning har vi hittills lyckats väl. Men visst finns det mer att hämta, bl a baserat på att få igång konfigurationsbitarna tidigare i processen. Här är säljkonfiguratorn ett lovande steg i denna riktning.
PÅ VÄG MOT VASSARE eBOM- OCH mBOM-HANTERING
Andra områden där JBT och Leif Olsson-teamet arbetar proaktivt handlar om nya och skarpare lösningar kring BOM-produktionen.
”Precis, som många andra idag, har vi en blandning av eBOMar – som skapats i PLMsystemet, d v s en produktionsanpassad eBOM – och tillverkningsBOMar (mBOMar) utfärdad i ERP-systemet. Vi arbetar nu på att förfina detta så att vi har en tydligare eBOM, som bryts ner till en mBOM före produktion och detta drivs av det faktum att vi har fler anläggningar som har olika produktionsprocesser. Tillvägagångssättet är att göra detta i Windchill eftersom vi här ser ett kraftfullt och samtidigt lättanvänt verktyg för detta. ”
JBTs nuvarande ERP-system är INFORs Movex, som 2021 kommer att ersättas av INFOR LN, i princip samma – men förbättrade – system som Movex.
3D-PRINTING ETT JÄTTEKLIV I UTVECKLINGEN
När det gäller den typ av maskinell food tech-utrustning som JBT tar fram har plåtbockning och teknologier kring detta traditionellt varit en viktig del i utvecklings- och tillverkningsarbetet, det är dock kanske inte här de stora utvecklingskliven finns. På komponentsidan har det däremot hänt saker som kan väldigt stor betydelse, inte minst med entrén för additiv tillverkning, 3D-printing.
När det gäller komponenter i mindre serier – vilket är fallet för JBT, som alltså bygger större livsmedelstekniska produktionslinor – är denna teknik ”spot on” vad som kan bidra till ökad rationalitet.
– Absolut, konstaterar Leif Olsson med påtaglig entusiasm. Bara en sån sak att med additiv tillverkning kan skapa en enda komponent i en körning, där man tidigare kanske satte ihop tio mindre delar, ofta CNC-bearbetade, till denna komponent. Veckor kan bli till timmar, självklart kan detta ha en enorm betydelse ifråga om ledtidskapning. Så vi tittar förstås aktivt på detta, liksom att kunna skapa modeller för lokal reservdelstillverkning. Även där tror vi det finns det en hel del att hämta. På sista raden kan man åstadkomma sånt som man aldrig tänkt på ens som möjlighet.

EXPLOSIV UTVECKLING MED IoT, DIGITALA TVILLINGAR OCH AR
Det har som ovan nämnts hänt en hel del på teknologifronten, hur ser det t ex ut med sånt som digitala tvillingar, IoT, automation och AR, Augmented Reality? Alla dessa bitar har ju utvecklats explosivt och läget är att vi idag är på väg från teoretiska hajpar mot implementering av teknologierna i företagsapplikationer. Allt sånt har hamnat allt högre upp på agendan på många ställen, men samtidigt har ett problem varit att hitta bra affärsmodeller. Hur tänker Leif Olsson och JBT-teamet kring detta?
– Frågorna och möjligheterna kring detta är absolut mycket intressanta och vi tittar på teknologierna utifrån lite varierande perspektiv. När det handlar om IoT och automation är vi kort sagt bara i början; inte minst är utvecklingen när det gäller givare oerhört spännande där vi går mot att kunna stoppa in dem i vilket temperatur som helst. Eller sånt som att kunna byta reservdelar innan de går sönder. Prediktivt underhåll har fantastiska möjligheter till att bidra till längre livstid för maskinella utrustningar. På samma vis kan underhållsåtgärder komma att bli betydligt enklare att utföra när man med hjälp av bärbara datorglasögon och AR-teknik på distans kan guida även personer som inte är experter i att utföra t ex ett komponentbyte. Men även digitala tvillingar finns med i våra planer inför framtiden och vi har redan kommit igång med pilotprojekt här.
Leif Olsson pekar på fordonsindustrins resa mot framtiden som ett utmärkt exempel på vart utvecklingen är på väg. Detta industrisegment har tillsammans med aerospace-området alltid legat i utvecklingsspets.
JBT tänker inte vila på hanen i detta.
– Precis som bilar gått från att mest vara en fråga om plåt och mekanik har man gått mot att bli mjukvara och elektronik på fyra hjul. Vi är nu på väg i samma riktning.
Bortsett från hjulen förstås.