Overall, Nexus builds on a legacy of innovation, combining Hexagon’s decades of industry expertise in industrial manufacturing and related IT with Microsoft’s latest cloud and AI technologies. The platform’s open and flexible data-centric architecture offers customers several distinct integration options to connect a variety of third-party applications, from simple file exchange to real-time data sharing, powered by Microsoft’s Fluid Framework.
“This versatility enables seamless connectivity across the digital wire, linking to CAE tools, simulation and process data management (SPDM) and PDM/PLM systems of record that have traditionally operated in isolation with production systems, shop floor IoT and quality data sources,” the company writes in the press release.
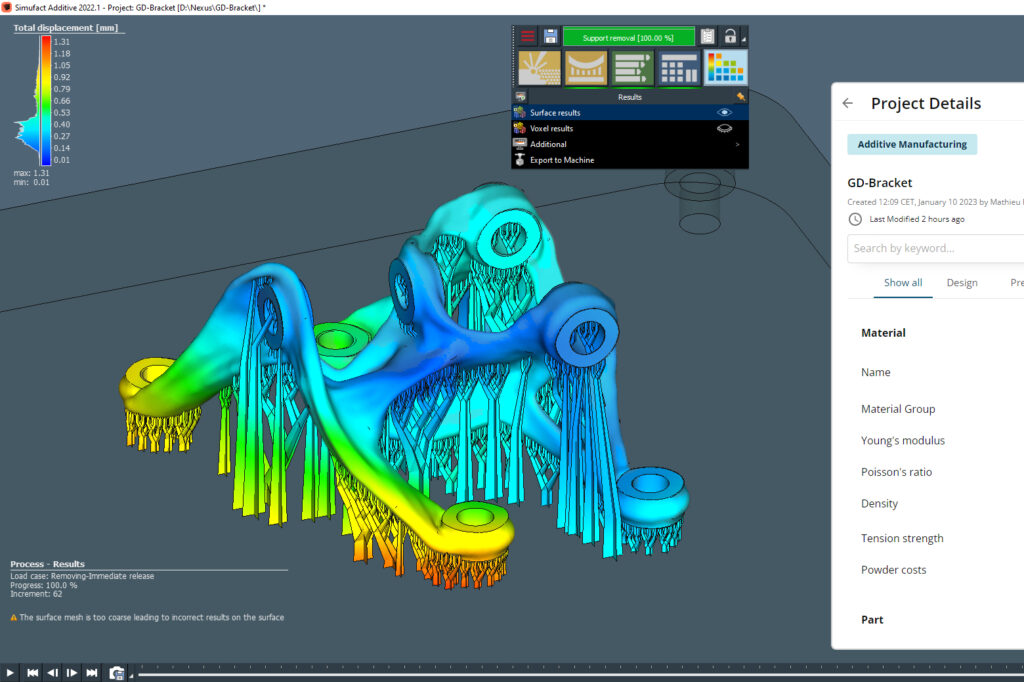
Enhancements that empower every step of the workflow
Hexagon further points out that it has expanded the Nexus product portfolio to empower users at every step of the workflow:
• Hyperscale computing for simulation: Nexus Compute offers on-demand access to Hexagon’s best-in-class CAE simulation solvers, regardless of company size.
• Cloud-based automotive applications: Solutions like Virtual Test Drive X (VTDx) – Hexagon’s IF award-winning SaaS for automotive software testing – simplify testing of ADAS and autonomous vehicle software through thousands of orchestrated cloud simulations.
• Accessibility-enhancing UX: From the start, user experiences, such as those in Metrology Reporting, are designed to save experts time on quality reporting deviations while allowing non-experts to quickly interpret data with accessible web-based reporting and cloud collaboration.
• Productivity-boosting AI: Automated program generation for machine tools (ProPlanAI), metrology (Metrology Mentor), and CoPilot customer support empower computer users to increase personal productivity and help employers achieve operational excellence and retain critical knowledge.
• Connect workflows and processes: Highly flexible and open cloud integration enables easy data sharing between software tools, IoT sensors, and machines, helping organizations overcome technical barriers and build efficient engineering and manufacturing workflows, connecting quality to the digital thread, and enabling data-driven operations with connected worker applications.
Increases productivity for users of CAM software
such as ESPRIT EDGE and EDGECAM
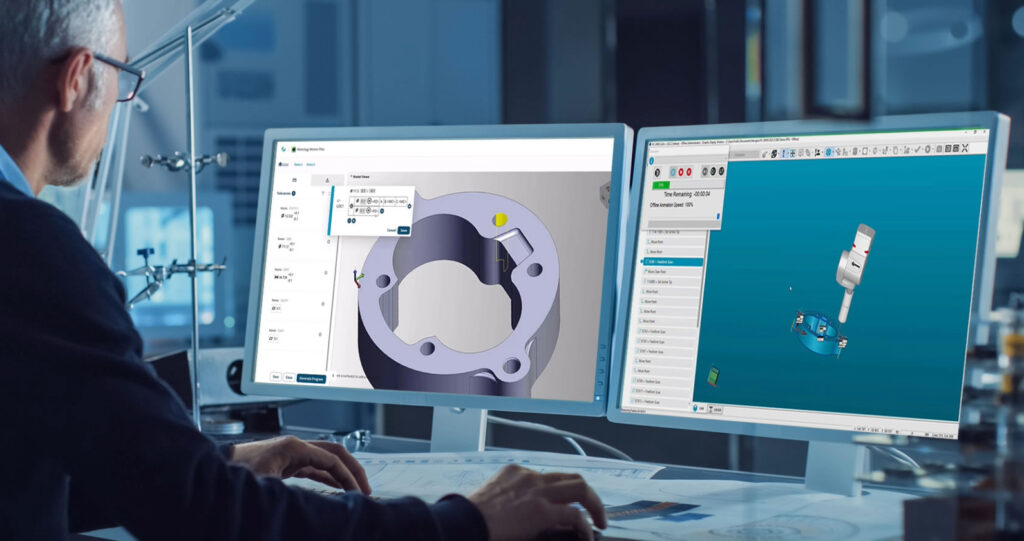
• Seamlessly connecting quality data to the digital thread: Nexus now also seamlessly connects Hexagon’s PC-DMIS – an inspection software solution for metrology specialists and shop floor operators, supporting systems from coordinate measuring machines (CMMs) to portable arms and laser trackers. The same goes for VGSTUDIO MAX, a modular software suite for GD&T (Geometric Dimensional and Tolerancing) analysis, materials analysis, simulation and CT reconstruction, and QUINDOS software, a leading modular metrology software for special geometries used in powertrains in aerospace, energy, automotive and engineering. With these pieces, additional critical quality data can be integrated into the digital thread and help users of CAD/CAM software such as ESPRIT EDGE, EDGECAM, DESIGNER and VISI CAD/CAM improve productivity on the shop floor. These initiatives, among others, create the conditions for increased use of quality control and measurement data to improve quality faster, optimize manufacturing processes and improve products and customer satisfaction
Additionally, Nexus as mentioned above also offers connectivity for third-party suppliers. This means that new technologies and solutions become available to Hexagon’s user base.
• The current software partner lineup includes Acerta LinePulse, CASTOR, Instrumental, JITbase, MachiningCloud, Moldex3D, OCTOPUZ and Zaptic. Integrations and data libraries include Solera VTD Catalog, Arcane Tech (for Cabinet Vision) and material databases through Materials Connect.
“Reliable CAE suite accelerates development work at Hyundai”
As Nexus continues to evolve, customers in automotive, aerospace and advanced manufacturing are already seeing tangible benefits, from streamlining simulation and testing to improved production efficiency and knowledge sharing, says Stephen Graham.
Companies like automaker Hyundai and Path Machining, “are already seeing the impact and using Nexus to accelerate development, optimize engineering performance and capture expert knowledge,” Hexagon writes in a press release, adding: “With new cloud-based applications, AI-driven automation and seamless data sharing, the platform is reshaping digital transformation across the entire manufacturing value chain.”
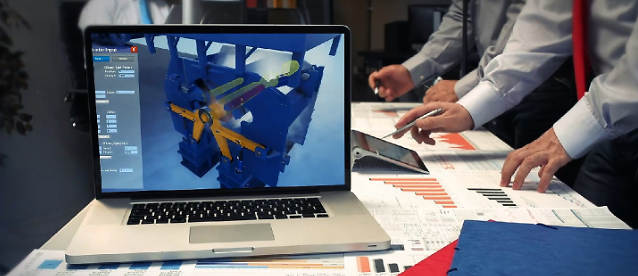
Jinhwa Lee, research engineer at Hyundai Motor Company, said in a statement:
“At Hyundai Motor Company, we leverage Nexus with Hexagon’s mature and reliable CAE suite to accelerate our development cycles, optimize engineering performance and drive a more agile, data-driven approach to vehicle development. Building a cloud-based vehicle development platform is our key strategy to achieve the open vehicle development goal and our innovative Nexus strategy.”
Gabe Schulze, industrial engineer at Path Machining, finally points to Hexagon’s ProPlanA as a game-changer:
“It excels by capturing best practices and the expertise we’ve built as a company and applying them to new parts. We don’t have to learn everything about AI – we simply use ESPRIT EDGE, and the cloud app refines our processes over time. Nexus is more than just a tool; it’s an evolving system that helps us capture know-how, maximize productivity, and improve operational excellence.”
A Brilliant Future for Holistic, Integrated and Open Platforms
How do you build a sustainable future in the manufacturing area? Part of the answer is about seamlessly connected, integrated, modularly built and holistic platforms for product realization. Competitive platforms must be modular, where new or updated and compatible pieces for specific domains can be easily replaced or added.
In today’s often highly diversified product development and manufacturing landscapes, few things stand on its own. Efficient product development and manufacturing processes require complete, well-connected solutions. This is also one of the important insights envisioned by Hexagon and a driving force behind the realization of the Nexus platform. Software and processes must be interconnected in order for the efficiency of the product realization chains to reach the level of maturity needed to remain competitive.
Today, the clear picture of where the manufacturing industry is going illustrates how these connections between programs have been developed into cohesive platforms that can also—to an increasing extent—link the previously “silofied” product development and manufacturing chains.
We are still not on an ideal level, but the direction of the journey is obvious, and Hexagon’s vision behind the Nexus platform is a significant step forward on that path.