Intelligent styrenhetsteknik har sedan länge gjort det möjligt för anläggningschefer att hålla reda på hur deras kompressor presterar via MODBUS eller PROFIBUS internetanslutningar till ett centralt anläggningshanteringssystem.
– Dessa typer av styrsystem är i själva verket en slags ”hjärna” hos en kompressor, som samlar in data via inbyggda sensorer, bearbetar dem och levererar översikter över hur tryckluftssystemen fungerar, till anläggningschefer och andra berörda, konstaterar Stef Lievens, som är ”Business Line Manager” på Atlas Copco Compressors, på bolagets sajt.
REDUKTION AV MANUELL HANTERING PÅ SIKT
Men inget står stilla och utvecklingsdynamiken har fört med sig framsteg, som har gjort det möjligt för kompressorstyrenheter att anslutas till mobila enheter, surfplattor och smartphones via system som SMARTLINK, vilket underlättar fjärrövervakning över ett säkert nätverk. Lievens igen:
– Därmed kan operatörer hålla reda på viktiga parametrar som tryck, flöde, motor- och torkhastigheter och sedan göra justeringar vid behov via kompressorns manuella gränssnitt. På så vis kan man tillgodose olika produktionskrav och kan hjälpa anläggningschefer att förbättra effektiviteten och spara energi, konstaterar Lievens, som också menar att man på sikt kan reducera manuell hantering som utförs av kompressoroperatörerna till ett minimum genom att låta luftkompressorer själva spåra och göra processförbättringar autonomt som oberoende cyberfysiska system.
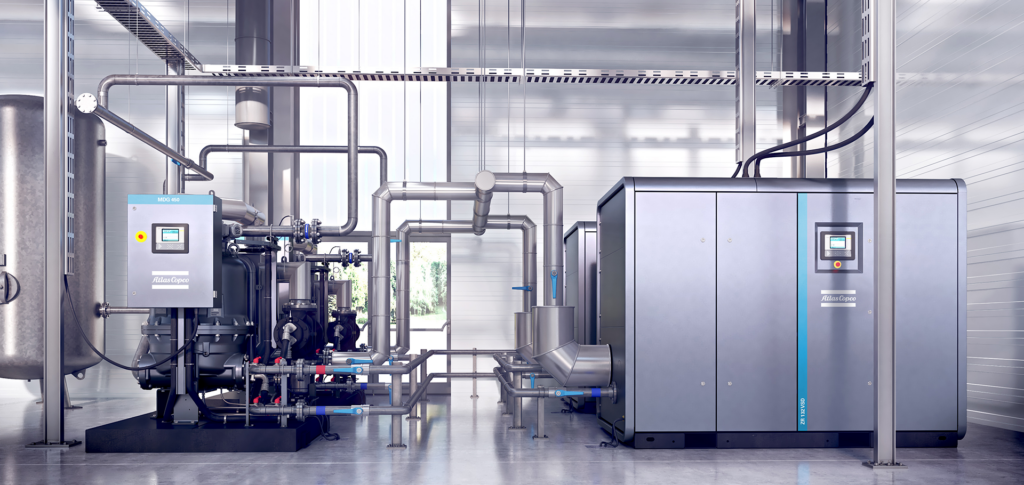
PREVENTIVT UNDERHÅLL KAN GE GODA VINSTER
Men i dagsläget är fjärrövervakning och prediktivt, förebyggande underhåll det mest påtagliga exemplet på hur IoT-tekniken används på tryckluftsidan inom industrin.
Fördelarna med preventivt är flera, men kokar allmänt ner till att förebyggande underhåll förlänger driftstid och minskar risken för haverier. Under en sådan process samlas, jämförs och analyseras data och kan vid behov resultera i alerts och insatser som hindrar haverier.
Lievens noterar att, ”analys av tillgängliga data har visat att drifttiden förbättras avsevärt på kompressorer med regelbunden service och kan göra en skillnad på 3,5 procent i förhållande till en kompressors tillgänglighet. Det kanske inte låter högt först, men eftersom det motsvarar ytterligare 210 produktionstimmar under ett år, baserat på en kompressor som går i 6000 timmar per år, blir de potentiella affärsfördelarna snabbt tydliga.”
Han hävdar vidare att man genom att känna till tryckluftsutrustningens status hela tiden, via t ex anläggningschefer och underhållspersonal, kan upptäcka eventuella problem, avslöja potentiella energibesparingar och uppnå maximal drifttid för både kompressorer och de produktionslinjer de stöder.
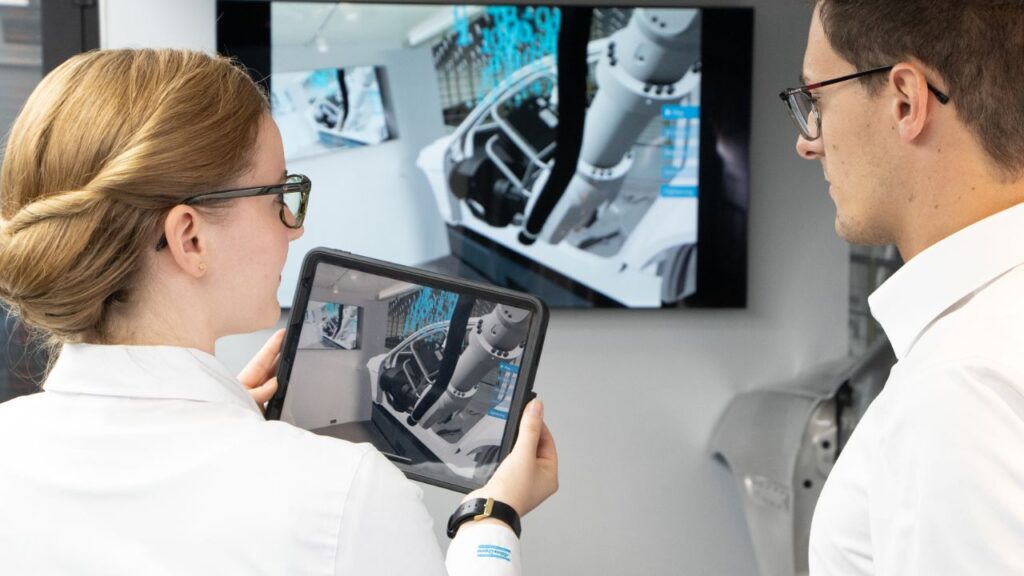
”VITSEN MED 5G ÄR INTE BARA HASTIGHETEN,” hävdar PTC
Det finns alltså en hel del att hämta genom satsningar på IIoT (Industrial IoT) och det är inte bara Atlas Copco, utan egentligen hela tillverkningsindustrin som är i stöpsleven. Svensk industri är inne i en stor omvandling, där processer, produkter och tjänster blir allt mer digitala och uppkopplade. Men uppkopplingen sker ännu främst via kabel, vilket innebär högre underhållskostnader och drar ner effektiviteten och flexibiliteten i verksamheten.
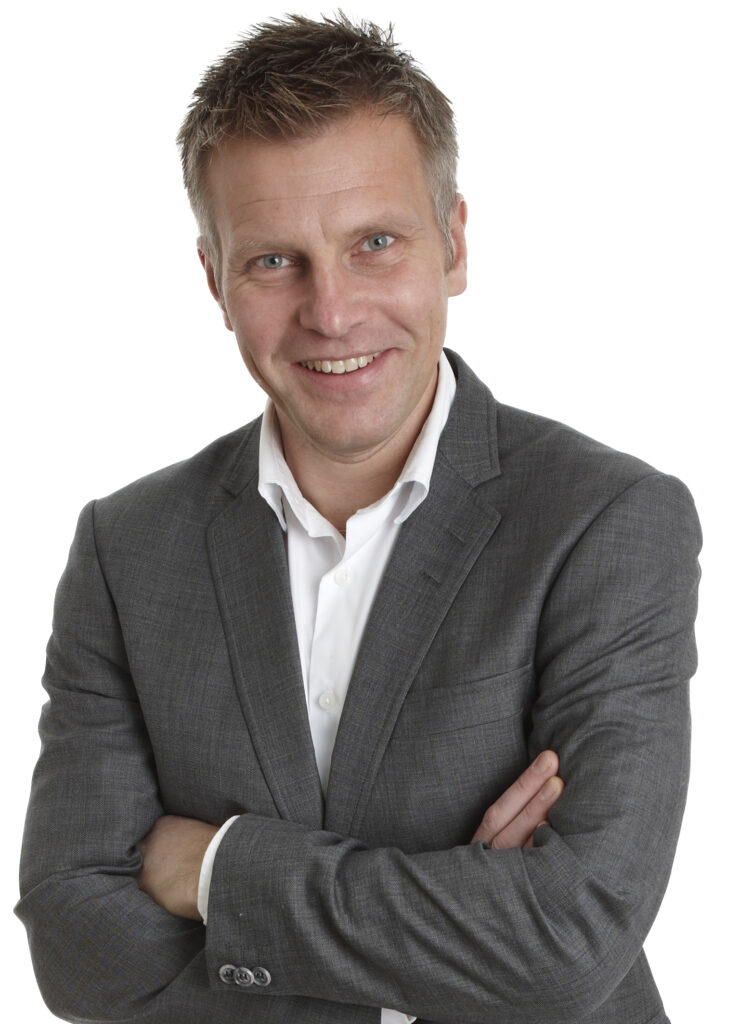
– Absolut är det så, säger PLM- och IoT-utvecklaren PTCs nordenchef, Filip Stål. Vitsen med 5G är långt ifrån bara hastigheten, den är inget självändamål. Det hela måste kombineras med industriella PLM-lösningar och kompetenta mjukvaror som ger bl a den flexibiltet som många inom industrin efterfrågar; kort sagt lösningar som bl a möjliggör att s a s kunna flytta runt industriella utrustningar utan en massa komplexa omkopplingar av kabelsystem.
Industri 4.0-konceptet innehåller mycket av mobilitetstanken, hävdar Stål. Detta med att snabbt kunna slå om för att effektivt kunna tillverka varianter av en produkt, eller andra produkter, på samma lina, kräver lite andra insatser. Det kan röra sig om förflyttning av robotar och maskinell utrustning, e t c. Då är kabelburet inget bra svar. När de industriella tillverkarna nu tittar framåt är det sålunda inte bara speeden man tittar på.
– Visst vill man ha maximal hastighet i dataflödena, säger PTCs nordenchef, men minst lika viktigt är att man får till de rätta dataapplikationerna. När vi idag samarbetar med Ericsson kring IoT och IIoT, är det de industriella kapabiliteterna vi menar är en viktig poäng. Sånt som digitala tvillingar, AR/VR och annat kommer att kräva inte bara 5G utan också mjukvaror och flexibla konfigurationer.
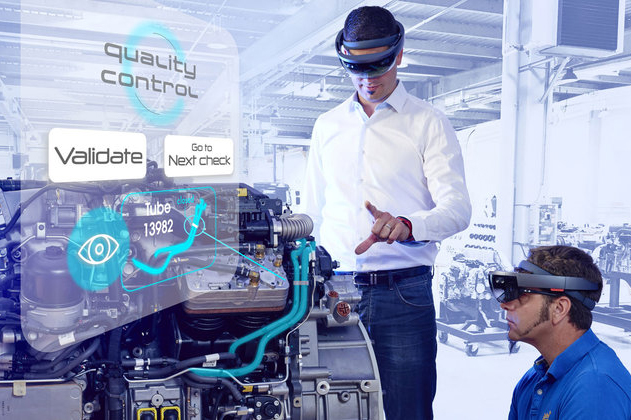
VOLVO ETT BRA EXEMPEL PÅ
NYTTAN SOM FLEXIBILITETEN SOM 5G GER
När exempelvis Volvo Group tittar framåt på produktionslinornas utveckling är mobilitet och flexibilitet en väsentlig del av det man strävar mot.
I detta siktar Volvo Group, som PLM&ERP News rapporterat om i tidigare artiklar, på att utveckla ett självbalanserande system med högt automatiserade, smarta arbetsstationer, som blir ”flytande” i perspektivet av att de fysiskt ska kunna flyttas runt kring produktionslinjerna där de för tillfället behövs. Andra bilder vi får vänja oss vid är att se cobotar, ”samarbetsrobotar”, jobba ihop med människorna på golvet.
En slags ”basmontering” av fordonen hanteras på huvudlinjen, medan speciella anpassningar hanteras vid eller av sub-assembly-enheter. Finessen med ett självbalanserande system är att det ”självt” hjälper till att anpassa produktionstakten i förhållande till de enheter som parallellt finns på linjen för tillverkning/sammansättning.
Vidare ska visualisering spela en växande och stor roll också på verkstadsgolvet, där sånt som VR (Virtual Reality) och AR (Augmented Reality) används för att visuellt stödja hur delar ska monteras och ge upplevelser som konkretiserar och ökar insikten kring produktionen på de individuella stationerna.
EN KNUFF UR STARTGROPARNA FÖR MOBILTEKNIKEN
Det är med detta som bakgrund intressant att se hur Atlas Copco, med Telenors och Ericssons hjälp, satsar på det privata 5G-nätverket i Sickla, vilket alltså ger tillgång till den senaste trådlösa tekniken som man strävat efter. En signal god som någon om att nästa generations mobilteknik nu ”officiellt” inte bara står i startgroparna för att bana vägen för den fortsätta digitaliseringen och effektiviseringen av svensk industri; man har också kommit igång med arbetet.
Det är förmodligen också inom tillverkningssektorn som detta med Industrial Internet of Things (IIoT), Industry 4.0, 5G och annat står som positiva och drivande förändringskrafter. Man har allmänt redan börjat introducera avancerad robotik på arbetsplatser och smarta komponenter som potentiellt kan kommunicera sina egna monteringsanvisningar till produktionslinjen.
Utmaningen för utrustningsleverantörer är att företag nu fortsätter att gå utöver att bara prata Industri 4.0-teorier och satsar på att tillämpa i praktiken. Gör man det kommer industrin att fortsatt ligga i global framkant och aktivt kunna slåss mot de som kommer senare upp på tåget.
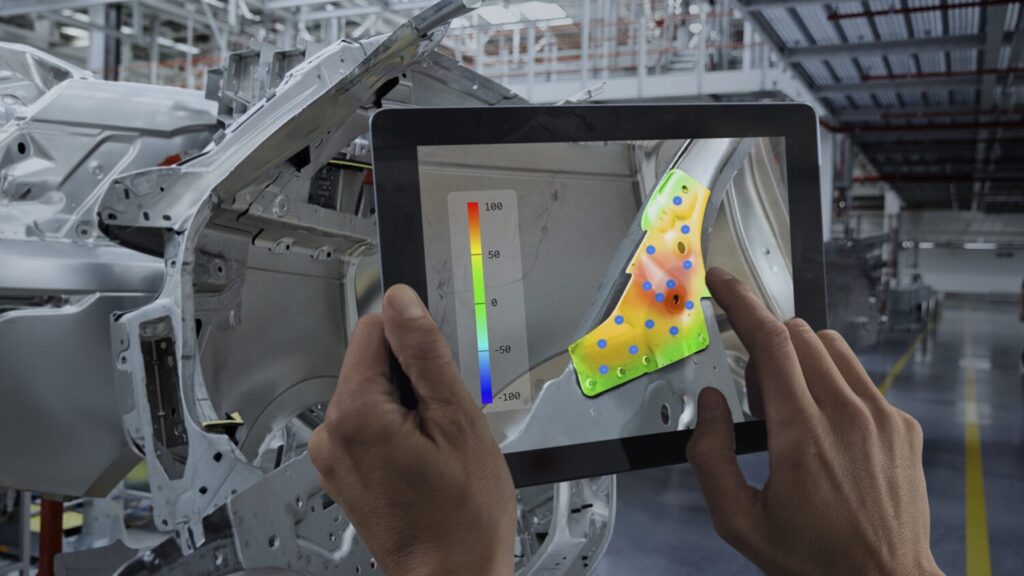
GODA NYHETER FÖR ATLAS COPCO
Hur ser utvecklingstrenderna ut? Analytikern IDC International Data Corporation publicerade för inte så länge sedan forskning som uppskattar att de globala IoT-utgifterna kommer att uppgå till nästan 1,4 biljoner dollar fram till 2021, och tillverkningen förutspås vara den ledande industrin för investeringar.
Detta är goda nyheter för Atlas Copco och ett viktigt industrisegment de befinner sig i, tryckluft och kompressorer. Det handlar nämligen om en av världens största industriella energikällor, som beräknas stå för 10 procent av all energi som används i industrin globalt.
– Tveklöst kommer tryckluft att spela en viktig roll i utformningen av framtidens smarta fabriker,” menar Stef Lievens. Tillämpningen av internetanslutning och datavetenskap i tryckluftsindustrin kommer inte bara att påverka driften av utrustningarna, utan också hur den den ursprungliga designen av utrustningen påverkas av driftsdata.
Återmatningen av fältdata till PLM-systemen alltså, där de påverkar utformningen av nya kompressorer och innovativa kringlösningar.
I Atlas Copcos fall består f ö den digitala verktygsarsenalen bl a av CAD från PTC, CREO, och komponenter från PTCs PLM-svit, Windchill.
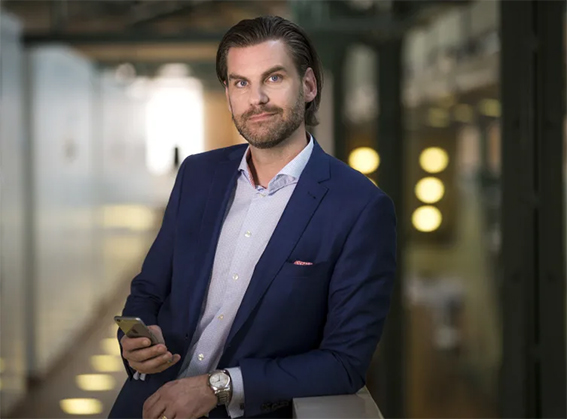
TELENOR TIDIGT UTE MED PAKETLÖSNING FÖR SMARTA FABRIKER
Som en av de första operatörerna i världen erbjuder Telenor en paketlösning för privata mobila nätverk skräddarsydd för företag och smarta fabriker i tillverkningsindustrin. Atlas Copco blir Telenors första kommersiella kund och tillsammans med Fujitsu har man nu installerat och aktiverat det privata nätverket i Atlas Copcos lokaler i Sickla i Stockholm.
– Det är väldigt glädjande att vi befäster vår ledande position på området när Telenor nu som första operatör i världen ingår ett kommersiellt 5G-avtal med Atlas Copco som bygger på Ericsson Industry Connect. Vi vet att privata nätverk kommer vara en viktig pusselbit för, säger Andreas Kristensson.