Kort sagt är det sådana faktorer som ovan nämnda som bidragit till att The Absolut Company för närvarande inte bara är den svenska livsmedelsindustrins flaggskepp, utan också, enligt statistiken, världens sjätte största spritvarumärke, med närvaro på cirka 150 marknader globalt.
TILLVERKNING I VÄRLDSKLASS
Detta är en position som ställer höga krav på alla etapper från början till slut.
– Vi har en produktionsfilosofi som återspeglar dessa höga ambitioner, kommenterade Svärdh och fortsatte: ”Den lyder ’En källa, en community – en majoritet av våra leverantörer är inom en 3 timmars bilresa), en superb vodka’. Denna slogan säger mycket om vår strävan att alltid leverera tillverkning i världsklass och i detta kommer konceptet Industry 4.0 att vara en avgörande faktor för att inte bara leva upp till nuvarande utan även framtida produktion, konsument- och miljökrav.
Han tillägger att ambitionen i detta i stor utsträckning också bygger på samarbete med partners som delar företagets tillvägagångssätt, vilket han menar gäller Siemens, vars programvara och hårdvara spelar avgörande roller för att uppnå målen.
Så hur kommer man dit? Absolut Company valde att göra detta via ett första projekt i en av sina fabriker i Åhus, baserat på Opcenter Execution Process-programvara från Siemens. Detta som ett första steg i utbyggnaden till de tre fabriker som producerar premiumdrycker för global distribution. Under 2020 digitaliserades en första produktionslinje. Men för The Absolut Company handlar detta på sista raden om en satsning på installation av fem helt digitaliserade produktionslinjer, varav de fyra sista produktionslinjerna blivit tekniskt implementerade och klara för runtime nu under 2021.
Vilka är företagets utmaningar?
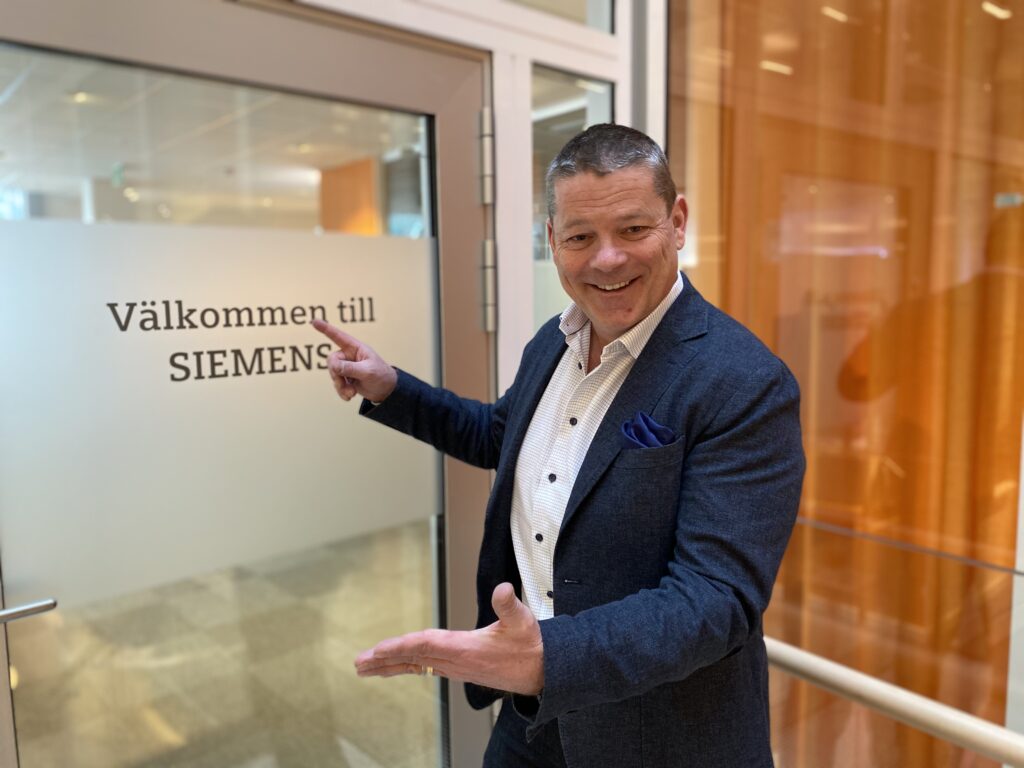
”EN EXPLOSION AV KOMPLEXITET”
Bakgrunden är att den tekniska, klimatiska och socioekonomiska utvecklingen har skapat en situation som förändrar ett antal villkor.
– Men förändringarna kommer på flera sätt, säger Mats Friberg, VP och chef för Siemens Digital Industries Softwares nordiska verksamhet. Dagens företag står inför en explosion av komplexitet. Naturligtvis kan detta vara tufft, men nya digitala verktyg och teknik ger organisationer möjlighet att dra nytta av denna komplexitet; vi kan helt enkelt vända komplexiteten till en konkurrensfördel. I industriorganisationer, som liksom The Absolut Company har höga ambitioner, har tekniken en betydande inverkan med aktivering av saker som rör sig i Industry 4.0 och IIoT-spåret (Industrial Internet of Things), användning av digitala tvillingar och en omfattande automatiserad maskin- till maskin-kommunikation och kontroll.
Friberg tillägger att B2C-företag över hela världen också står inför ökade och förändrade regler.
– Vidare kan behovet av tillverkning för att möta lokala krav, lokal konkurrens och marknader som snabbt förändras i efterfrågan sätta press på vinstmarginalerna. Detsamma gäller om konsumenternas efterfrågan går mot mer variation och specifika smaker, det betyder att det måste vara möjligt att ändra produktionen snabbare samtidigt som lönsamheten bibehålls, även om man producerar kortare batcher.
ETT PERFEKT INDUSTRI 4.0-KONCEPT
Hur hanterar du detta? Först och främst inser man på The Absolut Company att digitalisering är nyckeln till att fortsätta vara i framkant i en bransch i förändring. Att utvecklas till ett helt digitaliserat, spetskompetent företag är en av pelarna i verksamheten, säger Emil Svärdh.
– Vi har byggt en plattform för att kunna möta och säkra produktionen för framtida krav på flexibilitet och smidighet i produktionen. Med helautomatiska produktionslinjer och ökade lagkrav kommer det att bli behov av ökad spårbarhet av produktdata och integration med affärssystem , förklarade han.
Det låter som ett närmast perfekt Industry 4.0-koncept. Vad betyder konceptet för The Absolut Company?
– Det är en del av vår produktionsstrategi. För oss är Industri 4.0, liksom andra digitala investeringar, viktigt för att hålla jämna steg med utvecklingen i vår omvärld och den digitala störning som pågår där. Vi är övertygade om att vi kommer att hitta nya typer av värdeskapande inom ramen för både Industri 4.0 och digitalisering i allmänhet. Men inte bara för näringslivet utan också för våra kunder och konsumenter. Som i all annan utveckling ser vi att det kommer att kräva kompetensutveckling, både befintliga och nya partnerskap, samarbeten, testbäddar och investeringar. Jag tror dock att det kommer gå fort. Och vi måste vara förberedda, säger Emil Svärd.
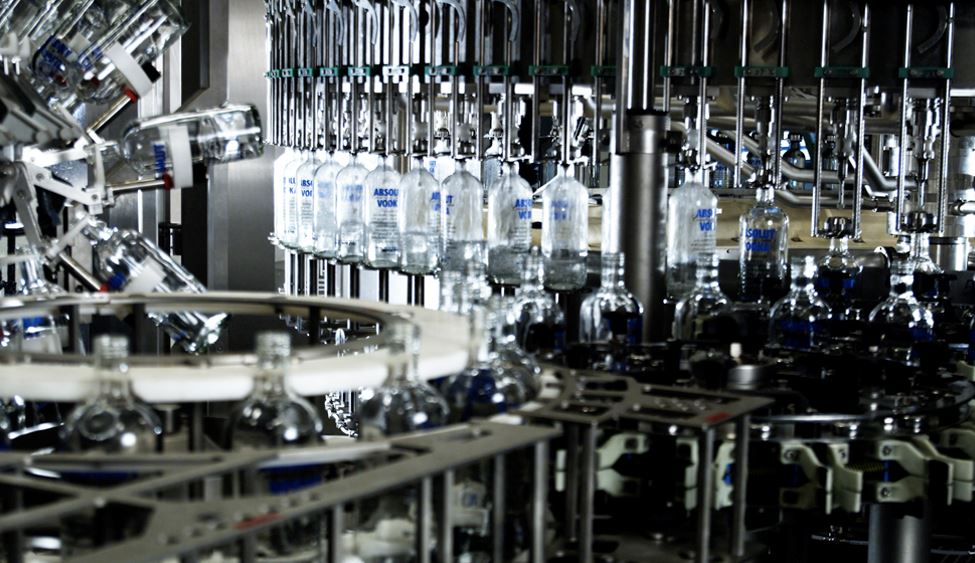
125 MILJONER FLASKOR VODKA OM ÅRET
Innan vi går vidare ska vi titta lite på mer exakt vad det är som produceras i företagets Åhus-anläggningar? Det handlar naturligtvis om vodka i alla dess former, inklusive leveranser av vodka för blandning i färdiga drycker och ”limited edition”; alla fortfarande i dotterbolag inom koncernen. Totalt produceras svindlande 125 miljoner flaskor per år. Vattnet som används kommer från våra egna djupa brunnar, med ett särskilt lämpligt kalkhaltigt vatten, beläget under Kristianstad-slätterna.
Destillationsprocessen – byggd på L O Smiths kontinuerliga process – är fortfarande en pelare i produktionen för att avlägsna föroreningar, skadliga ämnen och producera helt ren sprit. Vad det egentligen betyder är att destillationsprocessen är en kontinuerlig process som styrs av temperatur och tryck för att avlägsna oönskade föreningar. L O Smiths recept var att göra det 8 gånger.
– Men idag har detta utvecklats och inom samma sats kan vi faktiskt köra den kontinuerliga processen över hundra gånger innan total renhet har uppnåtts, säger Svärdh. Det som är intressant med det här är att vi är extremt energieffektiva, 98 procent bättre än branschgenomsnittet, vilket motsvarar 98 procent mindre klimatpåverkan per liter destillerat 96 procent alkohol.
Det är ingen slump att Svärdh under vår intervju ofta återkommer till klimataspekter som en gemensam nämnare i alla processer.
– Det är oerhört viktigt, och vi tar det på största allvar, sade han. 125 miljoner flaskor är mycket, men vi köper dem från ett företag som använder återvunnet glas till en återvinningsgrad på 49 procent. Dessutom använder vi i vår produktion idag mer än 85 procent förnybar energi. Målet är att vi ska vara 100 procent CO2-neutrala i hela värdekedjan år 2030. Utmanande? Ja, men absolut möjligt att genomföra.
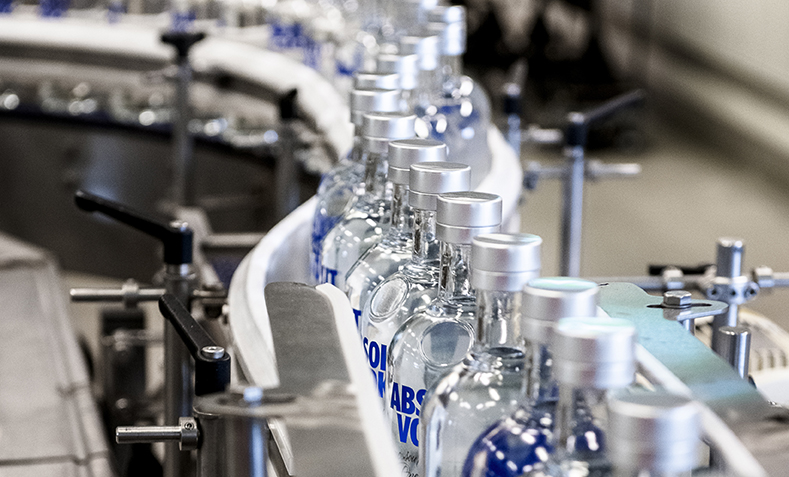
PRODUKTUTVECKLING OCH PRODUKTION
Cirka 300 personer arbetar i Åhusfabriken, detta täcker områdena produktutveckling och produktion.
På tillverkningssidan talar vi om en helautomatisk produktion.
– Vi brukar beskriva det lite bildmässigt när vi säger att ’första gången en persons hand rör vid en flaska är när den läggs på hyllan för exponering, andra gången när kunden tar den’, säger Emil Svärdh och fortsätter: ”Å andra sidan är detta en logisk följd av en helautomatisk produktion från att urrena inkommande glas till de fyllda och märkta flaskorna som går ut på en pall, transporteras direkt till ett lager i hamnen för senare frakt ut i världen.”
När det gäller fabriksproduktionen i Åhus har anläggningen planerat för fem helautomatiska produktionslinjer och en flexilinje för mindre specialserier.
– Majoriteten av styrsystemen kommer från Siemens och vi använder också Siemens SCADA-system (Supervisory Control and Data Acquisition) Simatic WinCC, som vår visualiseringsprogramvara, förklarar Absoluts seniora automationsingenjör och fortsätter; ”Vi bygger vanligtvis produktionslinjerna genom att ansluta komponenter och maskiner från flera olika leverantörer.”
UTMANINGAR I PRODUKTIONEN
Vilka är utmaningarna i produktionen i Åhus och hur är det med ansträngningarna för klimatneutralitet med avseende på produktionslinjerna? Generellt handlar det om att köra de stora satserna, men det Emil Svärdh och de anställda ser komma är framför allt mindre och mer varierade partier.
– Vi behöver högre effektivitet, vi har en hög utnyttjandegrad och en OEE mellan 70-75 procent. Vi strävar efter att bibehålla denna nivå, trots att satserna blir mindre i spåren av ett allt rikare antal smaker och flaskor. Vi fokuserar mycket på detta område tillsammans med Siemens just nu, vi bygger plattformen för att möta våra framtida krav.
Den digitala produktionsplattformen är integrerad med företagets ERP-system. Båda systemen skapar en integrerad arbetsorder som innehåller olika information, som kommer från flera affärssystem och slås samman med andra linjespecifika data. Denna arbetsorder är grunden för att sätta upp produktionslinjen och vilka operationer som ska utföras för att produkterna ska tillverkas.
– Vi bygger helt enkelt en dynamisk digital väg för varje arbetsorder, sammanfattade Svärdh. Om vi vill ändra, lägga till eller ta bort någon operation kan vi nu göra det digitalt. Det skapar en smidighet som gör att vi kan möta de förändringar som kommer.
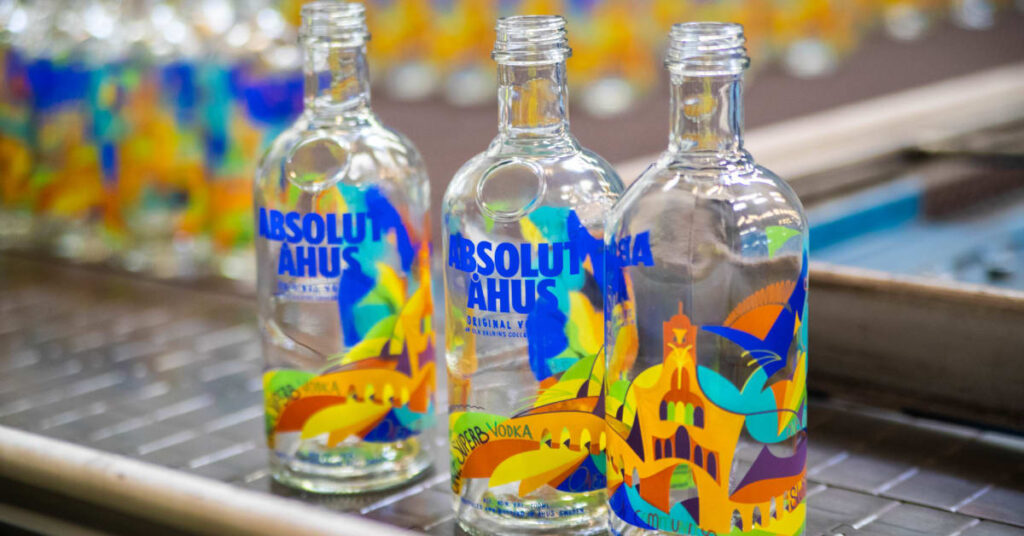
DIGITALA TVILLINGAR PÅ VÄG
Emil Svärd konstaterar slutligen att det är inte längre bara den fysiska värdekedjan som behöver hanteras och utvecklas, utan också den digitala reflektionen av dessa flöden.
– För oss handlar det om att integrera data och informationspunkter som finns i olika system helt, det är här Siemens-plattformen kommer in. Om du gör detta kommer du att upptäcka nya spännande möjligheter, som att ha data för att hjälpa oss i vår ständiga förbättring, eller information att följa produktens spårbarhet genom block chain -teknik, jag är övertygad om att detta kommer att ge nytt värde både för tillverkning och för våra konsumenter. För att göra det tittade vi oss omkring och valet föll – efter en noggrann utvärdering – på Siemens Opcenter Execution Process.
För varje fysisk värdekedja måste det finnas en ekvivalent digital värdekedja, hävdar den seniora automationsingenjören. För honom är detta synonymt med att etablera en digital kopia av produktionslinjerna och värdekedjan. För att göra detta är skapandet av digitala tvillingar ett måste.
– Det stämmer, konstaterade Svärdh. Vi strävar också efter detta, inte minst för att få ett bättre underlag för simuleringar av till exempel digitalt konfigurerade batch-körningar. På så sätt kan vi digitalt testa och validera att en körning fungerar som avsett. Om något behöver ändras kan vi göra det digitalt innan vi startar den fysiska ekvivalenten. Det blir faktiskt snabbare, kvalitativt bättre och framför allt billigare.