– Med den här tekniken kan kunderna leverera sina maskiner snabbare med bättre automatiserade lösningar, säger Thomas Strigl, affärsutvecklare på EDAG Production Solutions. Sånt som idrifttagningstid på en maskin kan minskas upp till en tredjedel jämfört med tidigare.
Branschspecifika paket en effektiviseringstrend. Att jobba med paketerade branschspecifika lösningar är en trend som kommer alltmer. AME är inget undantag. Denna lösning använder en modulariserad produktutvecklingsstrategi byggd på att kunna utnyttja gemensamma komponenter och processer i en produktgrupp, samtidigt som man definierar funktionella moduler som enkelt kan modifieras för att möta specifika kundkrav eller önskemål om förändringar.
Att använda avancerade multidisciplinära tekniker gör det också möjligt att avveckla seriella utvecklingsprocesser och gå mot integrerade, parallella samverkansprocesser. Också det ett sätt att spara ledtider.
Siemens menar vidare att den nya Advanced Machine Engineering-paketeringen gör det möjligt att samtidigt som man utvecklar produkterna ha ett verktyg som kan hantera den globala försörjningskedjan på ett sätt som kan förbättra exempelvis kvalitet vid montering. Detta tillvägagångssätt kan också resultera i kortare utvecklingstid, mindre komponentlager och möjligheten att integrera ett brett spektrum av maskinfunktioner.
Gemensamt ramverk för mekatronik och mjukvara. AME bygger på att lyfta den mekatroniska designen och ge den gemensam ram för mekanik-, elektronik- (inklusive elbitarna) och programvaruområdena. Genom att skapa ett gemensamt språk mellan discipliner – det talas idag ofta om digitala trådar i detta sammanhang – är det möjligt att utföra parallellt samarbete från de tidiga faserna i produktutvecklingen.
En annan mer processuell effekt är att arbetssättet möjliggör återanvändning av befintliga ”mönster”.
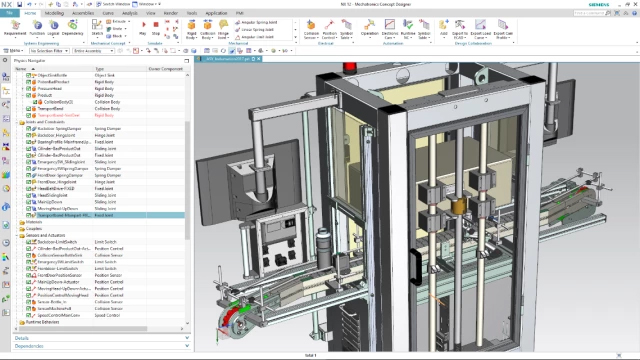
Ett sånt exempel kan vara att mekanikkonstruktörer kan använda konceptmodeller för detaljerad design; elkonstruktörer kan utnyttja modelldata för att välja de bästa sensorerna och manöverdonen för varje maskin; och automationsingenjörerna kan använda kameror och operativa sekvensdata från modellerna för att utveckla programvara. Genom denna mjukvara kan man minska antalet fysiska prototyper som behövs under produktutvecklingen.
Ett sätt att realisera digitala tvillingar. Att få ner antalet fysiska prototyper och kostnaderna för dess kan också förbättras ytterligare genom att jobba med digitala tvillingar av maskiner. Dessa tvillingar kan nu skapas inte bara för att konstruera och testa maskinen, utan kan också användas för att beställa nya produkter.
Siemens menar att man via bolagets end-to-end-lösningar kan ta fram konstruktionskoncept som bygger på förmågan att simulera effekten av variabler som gravitation, friktion och prestanda hos elektriska system, vätskor och pneumatik.
För de som varit med i branschen de senaste decennierna är det en vision som nu faktiskt kan realiseras. Genom digitala tvillingar för virtuell idrifttagning skapas en effektiv produktutvecklingscykel som möjliggör testning innan produkten ens byggs. Att identifiera problem tidigare i utvecklingscykeln kan förhindra dyra förseningar vid genomförandet eller senare i processen.
– Vår AME-paketering kan effektivt hantera komplexa processer och kontrollkostnader, samtidigt som det kortar tiden till marknaden och den tid det tar för kunderna att utvärdera, säger Rahul Garg, senior direktör för ”Industrial Machinery and Heavy Equipment”, på Siemens PLM. Genom att utnyttja våra mjukvaruverktyg kan företagen optimera iterativt framtagna systemkonstruktioner och fånga och återanvända institutionell kunskap och bästa praxis för att skapa ett innovativt, modulärt tillvägagångssätt för maskindesign.