Siemens räknar med att serva och reparera ca 100 tåg per månad i det nya centret. För att snabbt kunna reparera har bolaget investerat i en Stratasys 450mc Production 3D-skrivare. Enligt Siemens Mobility har möjligheten att skriva ut reservdelar och verktyg i 3D minskat tillverkningstiden med upp till 95 procent.
Optimering av reservdelar för längre livscykler. Michael Kuczmik, chef för Additive Manufacturing på Siemens Mobility säger i ett pressmeddelande att användningen av 3D-utskrift, ”möjliggör för oss att optimera reservdelar för längre livscykler, till reducerad kostnad och inom kortare tidsramar än någonsin tidigare.
– Dessutom, tillägger han, kan eventuella sista minuten jobb åtgärdas snabbare än någonsin genom förmågan att producera delar additivt.
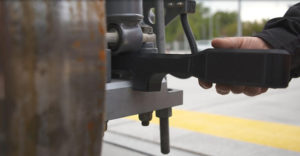
Tidigare var skräddarsydda, ”engångsdelar” inte ekonomiskt lönsamma. De var komplexa att tillverka med traditionell bearbetningsbaserad teknik och tog mycket längre tid. Förutom att man med additiva tekniker inte ”slösar” bort material, kan en 3DP-baserad framtagningsprocess ta 13 timmar istället för den tidigare tekniken sex veckor.
Tidsvinster av detta snitt är nu inte ovanliga, vilket ytterligare understryker vilka vinster man kan hämta hem genom att applicera 3DP industriellt.
Tyska Deutche Bahn producerar idag 15.000 reservdelar om året i 3DP. Förutom reservdelar tillverkar Siemens också som nämndes ovan 3D-printade verktyg. Exempelvis har produktionsteamet 3D-printat ett kopplingsverktyg som används för tågchassin (boggi). Denna typ av verktyg är svåra att producera med traditionella metoder på grund av sina komplexa geometrier och individuella anpassningsbehov. Eftersom boggis är tunga, de väger flera ton, använde Siemens Mobility-teamet Stratasys ULTEM 9085 termoplast, känd för sin hållfasthet och slitstyrka.
Slutligen ska notyeras att Siemensexemplet inte är unikt i järnvägsindustrin. Holländska tågbolaget Nederlandse Spoorwegen har 3D-printat 20 delar som används på tåg i i aktiv tjänst just nu. Företaget planerar vidare att producera 50 eller fler 3D-printade tågdelar i slutet av 2018.
Dessutom har tyska järnvägsföretaget Deutsche Bahn vägen till additiv framställning av reservdelar till tåg. De började med detta redan 2016 och har producerat minst 1.000 delar fram till början av 2017. Man fastställde då ett mål att producera 2.000 delar före årets slut och till slutet av 2018 hoppas Deutsche Bahn att 3D-printa 15.000 reservdelar.