By definition, the area of vibration acoustics can be described as an interdisciplinary domain that deals with the interaction between mechanical vibrations and acoustic waves. As computational methods gain importance in predicting and controlling noise and vibration, vibro-acoustics has become a cornerstone for engineers and researchers. Building acoustics are not only important in reducing noise that may damage human health, they also help to promote effective transmission of different noises to ensure sound is transmitted and spread at optimal levels.
Why do engineers need vibration analysis software?
Especially in automotive, internal noise is often a decisive factor for differences in product choice at the end-user level. At the same time, the current state of affairs is such that today’s industry practice often relies on late-stage test procedures to identify vibro-acoustic performance. Doing this in the late stages of product development has its disadvantages, of course, partly because bad vibroacoustic effects can affect performance, partly because it can be extremely expensive to correct.
“Engineering teams in the automotive, aerospace and defense industries often struggle with long design cycles, high costs, and complex certification requirements. However, with VA One and VPS NVH – ESI Group’s vibro-acoustic performance simulation solutions – they can quickly and accurately assess high and low frequency noise, optimize noise control treatments and effectively meet regulatory standards. This leads to faster certification, lower costs and superior design quality. Ultimately, it streamlines product development, reduces testing costs and improves the performance and comfort of the final products,” comments Massimiliano Calloni.
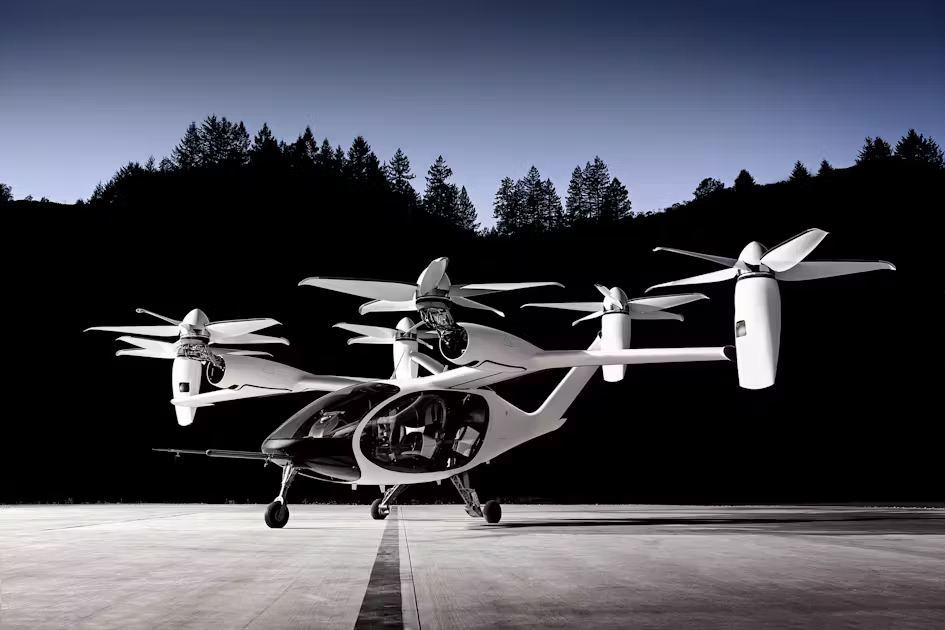
The strongest arguments for vibration acoustic software
In summary, the arguments for using vibro-acoustic software look like this, according to ESI Group’s Denise Börner, senior B2B Content Specialist:
- Early design validation: Engineers can assess variations in acoustic properties across the audible frequency range to optimize the acoustic and vibration performance of a design early in the development process. This digital method reduces the need for costly and time-consuming physical prototypes and tests.
- Compliance: Many industries, such as the automotive, aerospace and heavy machinery industries, are subject to strict noise regulations. Aero vibro-acoustic simulation allows engineers to design products and optimize them for compliance even before they are physically tested.
- Cost and time efficiency: By building acoustic models and simulating various design scenarios, engineers can identify and mitigate potential noise and vibration performance issues early, reducing the need for multiple design iterations and physical prototypes. This saves both time and money.
- Holistic optimization: Engineers can simultaneously study the acoustic response of different components affected by multiple factors such as weight, material properties, especially for complex poroelastic materials and structural dynamics. Aero-vibro acoustic simulation and modeling ensures that the final design meets all performance criteria without compromising noise control.
A single singular development environment
VA ONE is a unified platform designed for hi-fi vibro-acoustic analysis across industries. It allows users to predict noise and vibration behavior from the component level to whole vehicles or structures.
Designed for hi-fi vibro-acoustic analysis across industries the platform allows users to predict noise and vibration behavior from the component level to whole vehicles or structures. The software’s advanced features, such as Ray Tracing and Diffuse Field Acoustic Simulation, enable accurate simulation of complex acoustic environments, making it a great tool for getting the design right the first time.
Naturally, it has modules for importing and meshing CAD data from CATIA, NX, PTC Creo (Pro/E), SolidWorks and STEP.
The concept of moving vibro-acoustic development factors to early procedural stages is a pronounced strength for those who choose to work in ESI VA ONE. The advantage is most clearly manifested in the fact that the solution has a single environment for vibro-acoustic analysis and design. “It enables engineers to perform accurate predictive noise and vibration design assessments early in the design cycle to meet product performance goals,” the company claims.
Moreover, ESI states that users can face aggressive design time constraints, ensuring that engineering decisions can be made when they favor the requirements of a multidisciplinary development environment. In it, the VA One environment is accessed from a standard user interface, covering all frequency domains through a set of seamlessly coupled and proven modeling methods.
”With VA One, users achieve optimal design productivity without having to deploy separate solutions that require training for different user interfaces and data exchange between environments,” writes ESI in its press material.
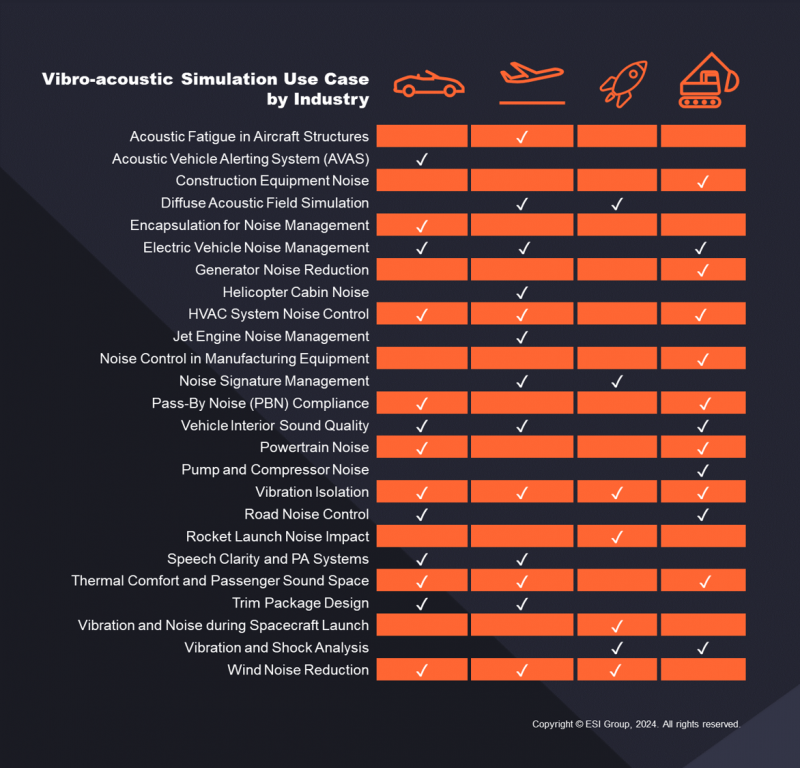
Quieter and more efficient vehicles
With the increasing demand for quieter, lighter and more efficient vehicles, engineers face significant challenges that cannot be addressed through traditional testing alone. VA ONE offers, according to Denise Börner, the following advantages for vibro-acoustic analysis of complex systems:
• Achieve operational goals (quality, cost) and achieve project milestones with accurate noise prediction models early in the design process
• Integrate noise prediction tools into existing design environments to quickly assess prototype designs with rapid model creation
• Access an optimal set of seamlessly coupled, fast methods to minimize simulation time
• Evaluate your design and quickly test countermeasures to meet attribute goals
• Achieve interior and exterior noise design goals within a single environment
• Eliminate expensive, late modifications.
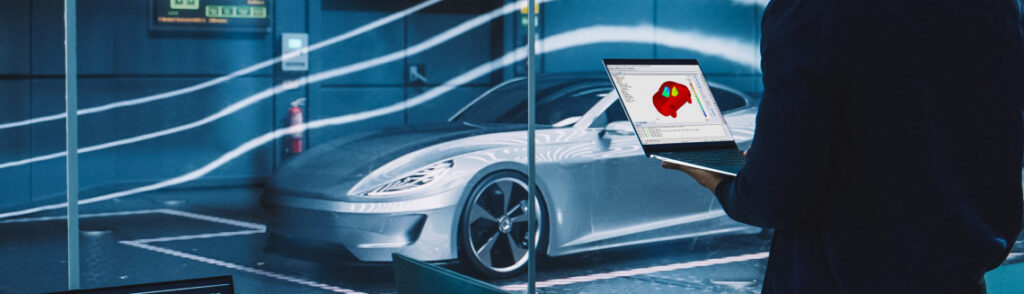
Finally a couple of words on aero vibro-acoustics
Wind noise is an essential aspect of vehicle performance. It impacts interior comfort and perceived product quality, which directly affects the passenger’s experience. The successful deployment of vibro-acoustic simulation and the resulting improvements to vehicle acoustics has led to reduced interior noise from sources such as powertrain, tires, and suspension. However, this results in a relatively more significant contribution from wind noise to the vehicle interior. Because wind noise directly influences the passenger’s ability to communicate with other occupants or make use of hands-free devices or phones, it is considered a vital product selection criterion. It is consistently ranked as a top concern for overall vehicle quality.
On ESI’s web site it is claimed that, “The growing speed and efficiency of Computational Fluid Dynamics(CFD) simulations result in greater accessibility to time-domain pressure distribution predictions. Turbulent flow can now be effectively simulated and processed to provide vibro-acoustic model excitations up to the higher frequencies that most strongly affect interior noise. The combination of CFD data and vibro-acoustic analysis as an ‘end-to-end’ solution for Aero-Vibro-Acoustic (AVA) simulation reduces dependence on expensive wind tunnels, whose availability is minimal. Allowing designers to virtually model interior acoustics excited by turbulent pressure fluctuations enables design decisions to be made earlier in the design cycle, reducing the need for costly revisions in later design stages.
ESI’s VA One Aero-Vibro-Acoustic module automatically converts CFD pressure-distribution time histories from a wide range of formats into the appropriate Fluctuating Surface Pressure load or input power in the frequency domain.”