In general, Siemens Digital Industries writes in a press release that it sees the GBA collaboration as a significant milestone in the company’s long-term commitment to promoting sustainable energy solutions, especially in the context of evolving global regulations for battery durability, carbon footprint and traceability.
By joining the GBA, Siemens is aligning major stakeholders across the battery supply chain, from material developers to cell suppliers, OEMs and government bodies to strive towards a greener and more ethical future.
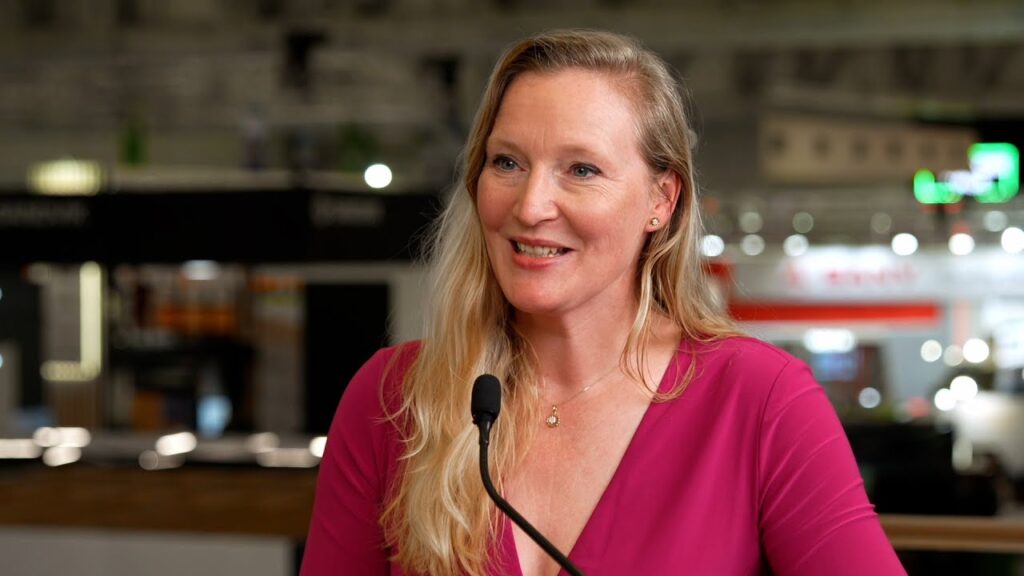
Vision around driving sustainability through digital transformation
Inga Petersen, CEO of the Global Battery Alliance, says in a comment that they naturally welcome Siemens to the platform.
”Exactly, within the framework of the Global Battery Alliance, Siemens will be able to help drive our shared vision to drive the adoption of digital transformation across all aspects of the production lifecycle, from ideation to design, production and disposal to increase efficiency and build a sustainable battery industry .”
Interesting is Pedersen’s emphasis on such things as the design, production and sustainability perspectives that govern the organization. As mentioned above, Siemens Digital Industries is already big in the battery area within the entire product production chain, with concepts such as closed-loop manufacturing, where the digitization pieces have absolutely decisive roles. Not least then within the Swedish Northvolt group, but also the world’s leading battery manufacturer, Chinese CATL, both working with Siemens Digital Industries solutions with NX CAD, the cPDm platform Teamcenter and the digital solution for manufacturing management, Tecnomatix.
Comprehensive digital twins
Clearly, the Siemens concept of digital twins – reliable virtual versions of products, processes, production lines and facilities, with iterative deployments of production processes – is significant for the industrial segment as such and the drive towards sustainability, claimed Puneet Sinha in a previous PLM&ERP News interview. These digital ventures, where simulation and analysis of the digital twins can be done without the costs and risks normally associated with doing the equivalent in the real world.
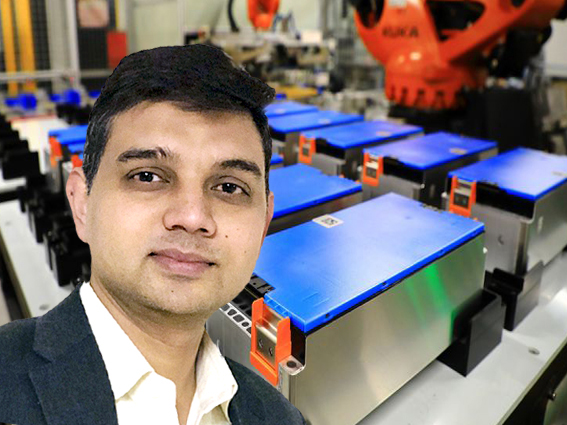
”Exactly, through simulation in Siemens environments, and within the framework of our Xcelerator portfolio, engineers can easily cover multiple domains spanning chemistry, mechanics, electrical/electronics and software to accurately evaluate the impact of different chemicals on cell performance, cell safety and aging. They can also optimize the cell design to maximize energy density and fast charging. Additionally, by leveraging Siemens digital twins, they can virtually validate cell designs and behaviors against package and end-system requirements. This frees companies from costly and time-consuming testing methods,” explained Siemens’ senior battery director.
The advantage of linked product development and production tools
Sinha said in the same interview that Siemens has a strong advantage in the connections between product development and automation tools.
”Correct, the company that wants to scale up production cost-effectively and take a leading market position needs a digital framework for product development and manufacturing, where the digital twin of production is connected to real physical factory operations through automation technology and where industrial IoT (IIoT) is enabled. This in turn enables digital design and optimization of the production line and validation of production processes prior to implementation on the factory floor; which reduces the investment risk and shortens the scaling time. Connecting the digital framework with automation hardware and software, as well as industrial IoT, facilitates an overall integration of production.
According to Sinha, this provides insights into actions and plans to improve production quality and maintain manufacturing best practices, all in an effort to reduce scrap rates and maximize production throughput, while balancing process sustainability and long-term profitability.