Formel 1 är känt för att bjuda på de tuffaste sportsliga utmaningarna. Det är kort sagt kungakronan inom motorsport. Men sporten är som sagt också en plats där ingenjörer kan tävla inom innovation på racingbanorna, vilket sker genom en process av kontinuerlig utvärdering, utveckling och optimering.
Till saken hör också att inom Formel 1 utvecklar varje stall sin egen bil, från idé till färdigt chassi, med ett minimum av standardiserade komponenter. Här spelar förstås NX den designmässiga förstafiolen, men vad som blivit allt viktigare i F1 är simuleringens betydelse.
Inte minst inför säsongen 2022 medförde de drastiskt förändrade tekniska föreskrifterna, särskilt när det gäller aerodynamik att simuleringssidan hamnat i strålkastarljuset. Tanken med de förändrade reglerna var att dramatiskt öka händelseintensiteten på racerbanorna med t ex fler omkörningar. För Oracle Red Bull Racing och andra lag skapade dessa regeländringar nya utmaningar.
– Med detta och med ett kostnadstak på plats kan vi fortfarande att justera bilen under hela säsongen, men vi har behövt vara mer selektiva när det gäller antalet och arten av förändringar, använda simulering ännu mer och noggrant hantera vår förbränningshastighet, säger Matt Cadieux, och tillägger: ”Lyckligtvis har vi infrastrukturen på plats så att vi kan fatta effektiva datadrivna beslut.”
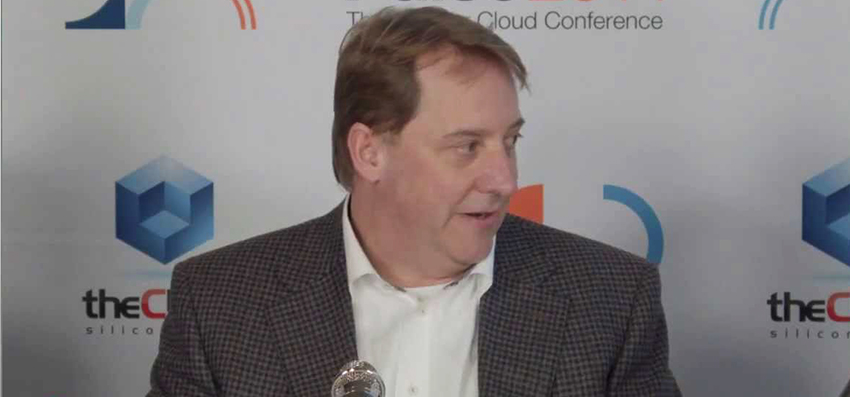
Högkvalitativ PLM-plattform
Denna infrastruktur, grundad på Teamcenter och NX – båda en del av PLM-portföljen Xcelerator – ger en omfattande och integrerad portfölj av programvara och tjänster från Siemens Digital Industries Software. Samarbetet etablerades reda 2004 när Red Bull Racing ingick ett partnerskap med Siemens, vilket också gjorde Siemens till en av de äldsta partnerna i det kända racingteamet.
– Eftersom vi har ett litet IT-team ville vi ursprungligen ha en högkvalitativ plattform med utmärkt teknisk support, fortsätter Cadieux. Med tillgång till Siemens ledarskap och expertis har vi utvecklat flexibla men strömlinjeformade arbetsflöden och åtgärdat flaskhalsar. Som ett resultat har vi tydlig insyn i utvecklingsprocessen, vi tillverkar direkt från digitala modeller och kan enkelt göra förändringar för att förbättra prestandan i fabriken och på racerbanan.
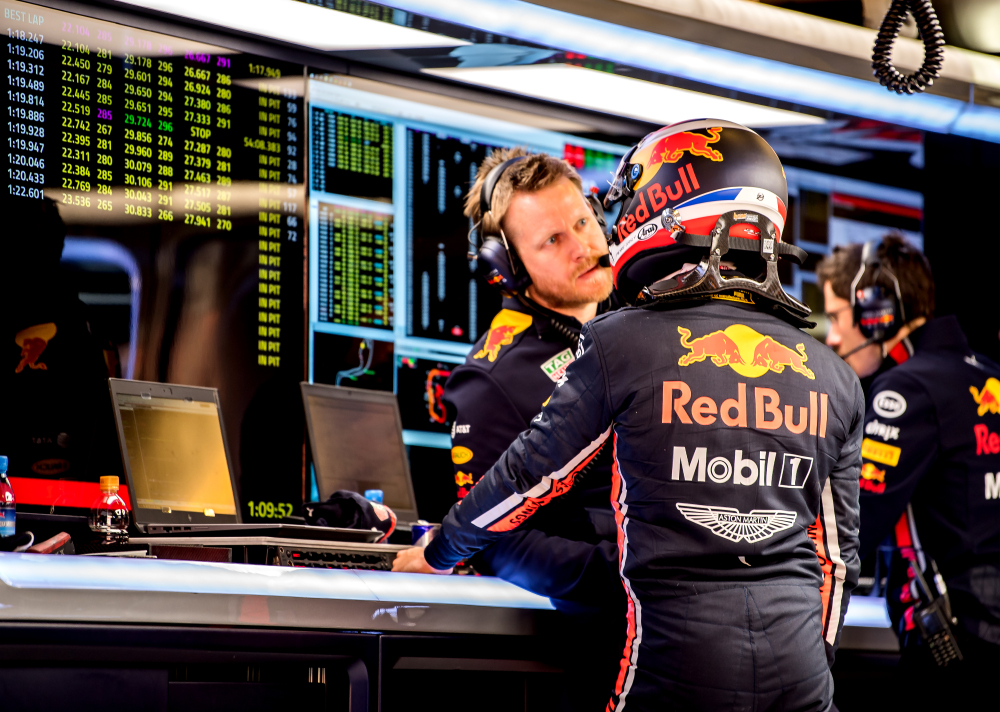
Händelsespecifika BOMar för varje lopp
En intressant vinkel på Formel 1 är att det egentligen inte finns en färdig produkt. En bil är mer att betrakta som en prototyp som kontinuerligt utvecklas och som genomgår så många som 1000 designförändringar varje vecka. Vässad teknikgenomströmning kan därmed också skapa en verklig fördel på banan om de tänkta innovationerna kan effektueras snabbt.
För att snabbt kunna omsätta dessa innovationer är Red Bull Racing också beroende av en digital PLM-ryggrad i världsklass, vilket man alltså får med lösningarna från Siemens Digital Industries på plats för att designa nya komponenter, testa dem virtuellt, ordna tillverkningen med så få musklick som möjligt och sedan installera dem i en bil på destinationer över hela världen.
Teamcenter-data används bl a för att generera en händelsespecifik BOM (Bill of Materials) för varje lopp, förutom en master-BOM för hela säsongens designarbete.
På den senare BOMen listas alla komponenter och delar som är designade för bilen under året, medan de andra händelse- eller banspecifika BOMarna tar information ifrån detta och beskriver alla artiklar och komponenter som krävs för att ställa in bilen för en specifik tävling.
Att upprätthålla färsk information i BOMarna bör av skälen som framgår av upplägget ovan vara realtidsbaserat, för att säkerställa att delar hanteras korrekt under hela tillverkningsprocessen och senare där och när bilen används för racing.

50 000 designändringar under en säsong
Red Bull Racing-stallet har en flexibel pool av ingenjörer som i sitt arbete utgår från BOMarna. De arbetar inom olika grupper som fokuserar på olika saker, som kompositer, hjulupphängning, hydraulik, transmission och systemdesign. Specialteam ser efter prestanda, fordonsdynamik, vätskedynamik (CFD) och stressanalys.
Med Teamcenter som bas kan man sammanföra alla delar av bilen i en enda samarbetsmiljö. Användarna har alla gränssnitt som relaterar till den egna gruppens och andra gruppers aktiviteter tillgängliga i realtid. Ett resultat av detta är bl a att alla problem kan identifieras tidigt och sedan parallellt följas vartefter de åtgärdas. Och dessa kapabiliter behövs med tanke på de tuffa uppgifter som Red Bull Racing Team står inför under säsongen:
De har fem kompletta fullt utrustade fordonsuppsättningar, genomför 20-talet lopp över hela världen, har 7500 unika komponenter i varje bil, gör bortåt 50 000 designändringar under en säsong och skickar 40 000 kilo flyg- och sjöfrakt till varje där loppen går: onekligen är Formel 1-racing mer än det mesta annat de svindlande talens och de logistiska utmaningarnas värld.
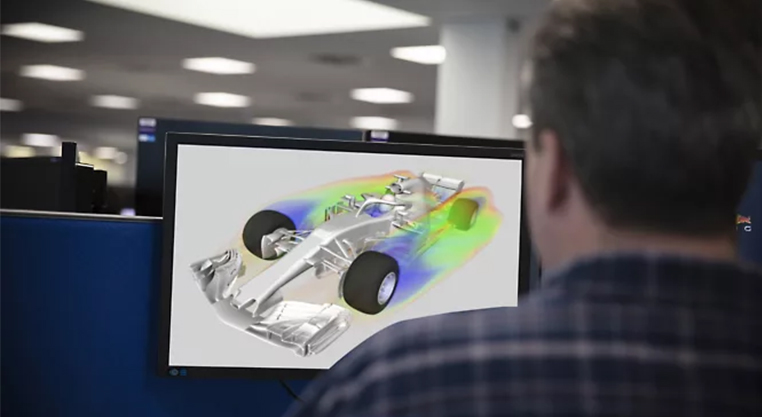
Ansys och HPE kompletterar på simuleringssidan
Men det finns fler företag som utvecklar PLM-relaterade lösningar som används av Red Bull-teamet. Innan varje tävling utvärderas och simuleras tusentals scenarion, från depåstopp till däckstrategi och vilken set-up bilen ska ha.
Under varje race samlar sedan personal på plats in tonvis med data som gör det möjligt för dem att bättre reagera på händelser i det aktuella loppet, men även för fortsatt utveckling av bilen. Dessa data skickas också vidare till stallets högkvarter i Milton Keynes, England.
Vid sidan av Siemens-lösningarna drar Red Bull Racing-teamet när det gäller aerodynamik nytta av HPEs Apollo-lösningar för virtuella prestanda-tester och utvärdering av förfiningar av existerande delar. Något som f ö också gäller nya komponenter innan de vindtunnel-testas i skalmodeller i storleken 60 procent.
Värt att nämna är att den kostsamma vindtunneltestningen är begränsad i reglementet, varför precisa simulationer är av yttersta vikt. Data från vindtunneln hanteras med hjälp av HPE Nimble, medan data från tävlingshelger tas omhand av HPE SimpliVity som en del av stallets mobila datacenter.
Som nämndes inledningsvis använder man också Ansys LS Dyna för simulering av krocktester. Men det är samtidigt så att Red Bull har ett avtal med Oracle kring en nyckelkapabilitet när det gäller datatunga och krävande områden som simulering och analys: processorkraft och HPC-kapabilitet (High Performance Computing).
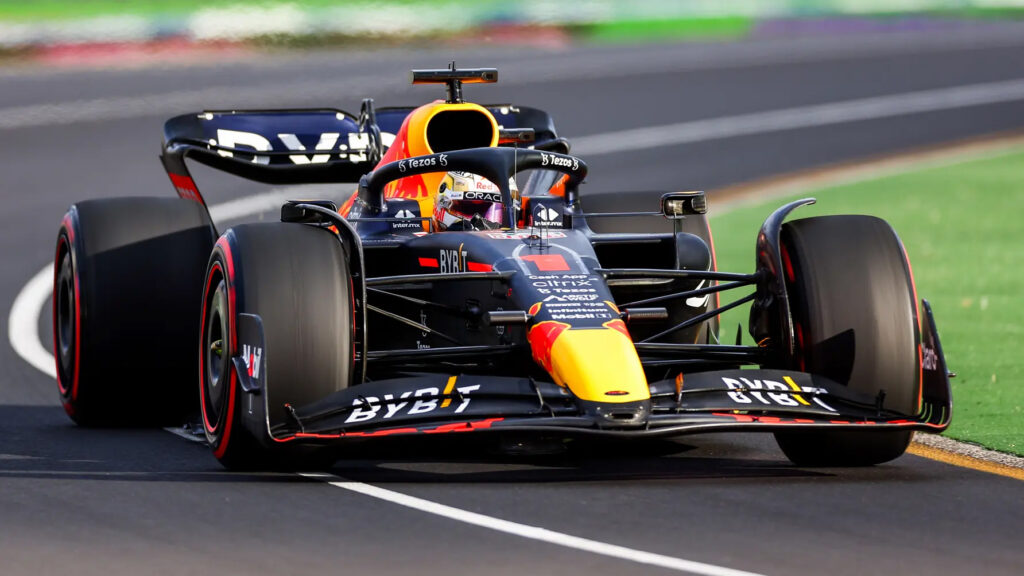
Förändringens vindar blåser i F 1
Sammantaget ska konstateras att förändringens vindar blåser i motorsporten, speciellt Formel 1. Inte bara när det gäller förare och deras prestationer, utan lika mycket hur teknologin bakom de vrålande F1-bilarnas framfart sköts. Den här typen av kombination mellan glamour och toppteknologi har en alldeles speciell attraktionskraft på exempelvis PLM-utvecklarna med tangerande IT- och datahanteringsrelaterad teknologi.
Här kan nu Red Bull-teamet stoltsera med att man när det gäller sitt digitala processupplägg kommit långt – troligen längst av alla just nu – i sina upplägg.