Till saken hör att SKF är en global verkstadsjätte med verksamhet i 130 länder. Bolaget drog in drygt 86 miljarder kronor 2019, hade en vinst på nära 10 miljarder och närmare 45 000 anställda. Att man drar ned antalet medarbetare med 300 är således en marginell minskning, även om det naturligtvis är tufft för de 300 i Sverige som drabbas.
Men det finns som sagt andra aspekter än de rent finansiella på detta. Som i så många andra fall den senaste tiden konstaterade Alrik Danielsson i samband med varslen förra veckan av de 300 medarbetarna att vad Corona framför allt inneburit är att utbrottet påskyndat en utveckling som redan var satt i rörelse; ett kompetensskifte inom koncernen, drivet av kunders och industrins digitalisering och automatisering. På ett eller annat sätt kommer förändringarna alltså att infinna sig, även om Corona nu officiellt får bära det tyngsta ansvaret.
Men mer exakt, vad menade han med att det hela är drivet av, ”kunders och industrins digitalisering och automatisering?”
Vi ska titta närmare på den saken genom ett tal han höll i samband med Siemens event kring ”Closed-Loop Manufacturing”, i Stockholm, för en tid sedan.
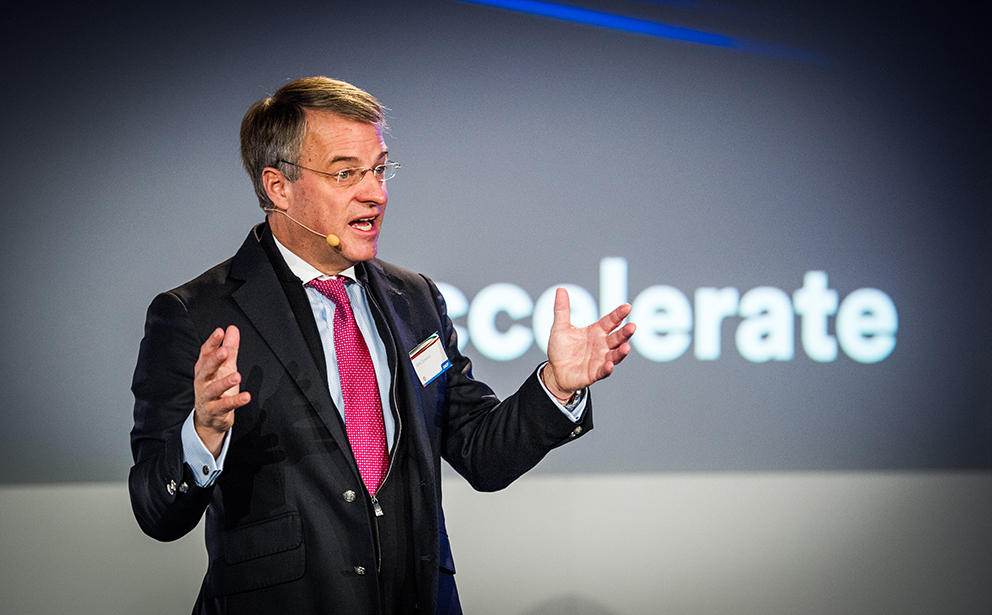
Ensamma om att montera sfäriska kullager helt maskinellt
SKF är i dagsläget den enda branschaktören som monterar sfäriska kullager helt maskinellt, automatiserat och utan mänskliga händer. Det tillhör bakgrunden och var definitivt en huvudpoäng i SKF-basens framträdande under eventet i Stockholm.
– Det är bra för miljön, bra för människorna och överlägset för ergonomin, summerade han och tillade att ”world class manufacturing” i sammanhanget helt enkelt är en nödvändighet för att vara kvar i marknadstoppen.
Danielsson beskrev hur detta ser ut i bolagsfabriken i Göteborg, där man drivit automatiseringen mycket långt.
LGVer, robotar och digitalt
sammankopplad produktion i Göteborgsanläggningen
SKFs Göteborgsfabrik är också ett utmärkt exempel på den typ av förändring som Alrik Danielson adresserade i sitt tal. Här tillverkar bolaget sfäriska rullager (SRB). Miljön är helt automatiserad med LGVs (Laser Guided Vehicles), KUKA-robotar och en i övrigt digitalt sammankopplad produktion på hög nivå.
Kullagren som produceras här är ett resultat av projektet, ”World Class SRB”, som handlar om ett helt nytt sätt att tänka kring och genomföra produktion, underhåll, skapa flexibilitet och service kring sfäriska kullager i dimensionerna 180 till 360 millimeter.
LGVs spelar som sagt en nyckelroll i en logistik-hub där de transporterar och allokerar det material och de komponenter som behövs för tillverkning, från en robotcell till nästa i en kedja som täcker hela tillverkningsprocessen. Mycket maskiner och dramatiskt färre människor än tidigare syns på det ljusa, närmast fläckfria verkstadsgolvet. Men så ser Danielsson också framför sig bilden av vad han kallar, ”the spot less factory”, på svenska närmast, ”den fläckfria fabriken” i bemärkelsen fysiskt ren.
– I slutänden förändrar allt detta verkligen spelet, konstaterade Danielsson. Produktionscellerna i Göteborgsfabriken var de första i vårt försök med kullager i storlekar upp till 35 kilo. Tidigare hade vi en återställningstid av produktionsapparaten på 6 timmar, investeringarna i termer av pengar var väldigt stora, vi hade mycket folk vid maskinerna och vi var tvungna att producera riktigt stora serier för att vara konkurrenskraftiga. Idag, med den nya uppsättningen, har vi minskat bemanningen med 70 procent, vilket helt förändrade ekvationen med avseende på arbetskostnader och vi behöver inte skicka iväg tillverkningen till ett lågkostnadsland för att produktionen ska vara konkurrenskraftig.
Men det stannar inte där. SKF-basen pekade också på faktorer som effektivitet och full flexibilitet:
– Vi behöver inte längre stå vid produktionscellerna hela tiden och vi behöver inte tillverka tusentals lager innan vi kan göra en återställning. Istället kan vi till och med stoppa in beställningar av små serier när som helst utan att förlora lönsamheten. Tittar vi sedan på digitaliseringsnivån så har vi dock inte detta klart för hela processen ännu, men vi strävar efter kapacitet till fullständig digital återställning.
Här är några vinster som World Class-manufacturing-konceptet resulterat i för bolagets anläggning i Göteborg:
• Låg kostnad, stor effektivitet och flexibilitet
• Inget behov av ”reset” av maskiner
• Smarta slipenheter
• Automatisk montering
• Automatisk lagring av komponenter
• Automatiserade guidade fordon
• RFID-taggning
• Kullagren individuellt ID-markerade
• Lågenergimaskiner, flexibel LED-belysning
• SKF “Condition Monitoring and mobile connectivity” för slutanvändare
• Realtidsinformation till operatörerna möjliggjord
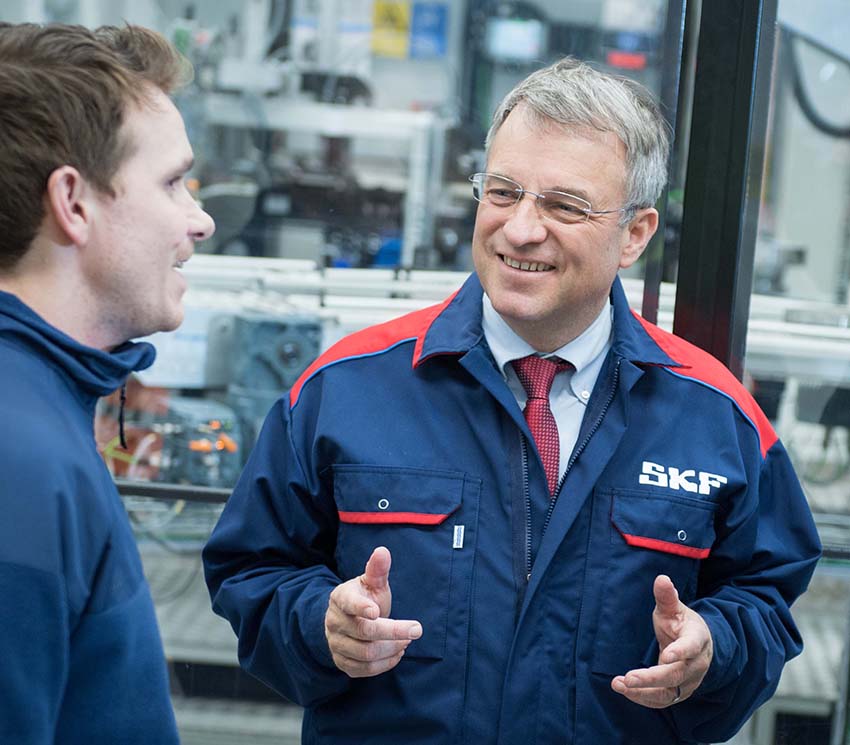
”Stora risker för den som inte hänger med i teknikutvecklingen”
Hur viktig är digitalisering för SKF? ”Mycket viktig,” säger SKFs CEO från scenen i Stockholm:
– Ibland blir jag tillfrågad om vi verkligen behöver ha en digitaliseringsansvarig som en specifik professionell roll? Mitt svar är ja, det här är verkligen viktigt, så viktigt att jag personligen har tagit rollen som digitaliseringschef. Varför? Om det inte är klart för alla i organisationen att jag är entusiastisk, eller att jag inte tydligt signalerar att jag står bakom digitaliseringsprojektet kommer det inte att hända.
Samtidigt är det är av yttersta vikt att det händer, hävdar Danielson:
– Jag har en son som har jobbat för KUKA i Kina och han berättar om vad som händer där och det gör mig ännu mer rädd och klar över att det är brådskande att vi gör något. Och vi måste göra det väldigt snabbt. Om vi inte kör igenom World Class Manufacturing-tanken finns det en stor risk – inte bara för SKF, utan för vilket företag som helst – att man inte kommer att finnas kvar på marknaden inom bara några få år.
– Å andra sidan handlar SKF i ett nötskal om just detta, fortsatte han. Vi var en startup redan i början av den andra industriella revolutionen, men har kunnat anpassa oss hela vägen från de första åren på 1900-talet till idag (SKF grundades 1907). Vi har kort sagt förstått att om vi inte har en beredskap för och kapacitet att förändras snabbt kommer vi inte att ha någon möjlighet att kostnadskonkurrera, vi kommer inte heller att ha någon tillverkningsflexibilitet eller kvalitet för att vara allmänt konkurrenskraftiga.
– För oss handlar dock inte detta om att starta med det ”stora totala projektet”. Däremot om att göra det där det är mest relevant och där det kan göras snabbt.
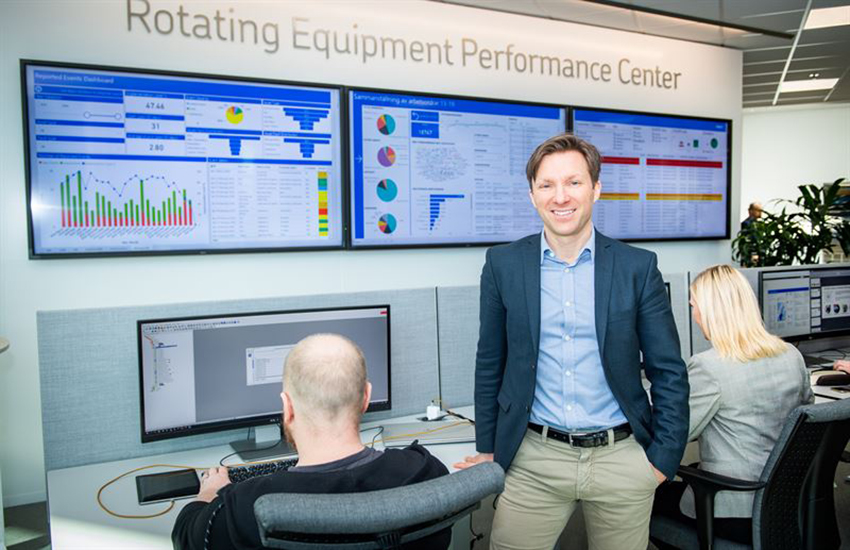
Vikten av att förstå exakt vad som händer med kullagren
SKF befinner sig sålunda i en digital transformationsprocess och har, enligt SKF-basen, även utvecklat flexibiliteten som krävs för att kunna gå vidare.
– För oss är detta vad vi menar med att vi är på väg mot Industry 4.0, sa Danielsson. Om vi kan koppla ihop oss med våra kunder och förstå exakt vad som händer med kullagren i deras maskiner, är vi på rätt väg.
Han konstaterade också i detta sammanhang att, ”om du använder Siemens IoT-programvara, MindSphere, i fabriken kan vi också ansluta SKFs monitoreringssystem för kullagrens tillstånd i den miljö de sitter och via detta vårt övervakningskit återkoppla till vårt datacenter, där vi kan hjälpa till med att exakt förstå vad som händer med kulllagret på plats i den verkliga miljön.”
– När vi kan integrera detta i värdekedjan kan saker och ting verkligen gå snabbt och vara flexibla, tillägger Danielson.
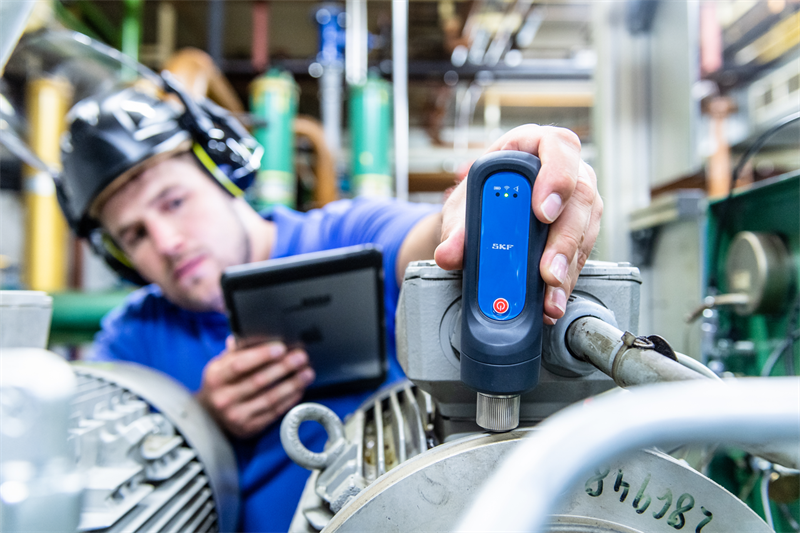
”Med den nya modellen behövs inte stora gigantfabriker”
En poäng för SKF är att man i och med den nya automationsmodellen egentligen inte längre behöver bygga verksamheten på gigantfabriker, utan kan producera i mindre, flexibla och lokala enheter, nära marknaderna och nära kunderna, där storlek är av mindre betydelse. Med detta slag av flexibilitet börjar andra kostnader bli viktigare, till exempel logistikkostnader och kostnader relaterade till ”time-to-market”, etc.
– I framtiden är jag helt övertygad om att vi inte kommer att behöva skicka dessa lager över hela världen längre. Istället kommer vi att ha ”in Americas to Amercias and in Asia to Asia-lösningar” och andra liknande geografiskt relaterade lösningar på plats. Detta är på gång med den typ av digitalisering och automatisering som vi implementerar, hävdar SKFs verkställande direktör.
Är detta bättre för SKF och är det bättre för kunderna?
– Utan tvekan båda delar, hävdade Alrik Danielson. Idag sitter det i allmänhet 5-6 lager någonstans i värdekedjan och s a s ”väntar” på att något ska gå sönder. Med denna typ av installation kommer vi snart kunna ha mycket färre av dessa potentiellt trasiga komponenter och kan istället erbjuda mycket mer flexibilitet, kvalitet, service och tillgänglighet.
Arbetskraftskostnader avgör inte längre konkurrenskraften
Konkurrenskraften är inte heller, i och med den nya modellen, lika tungt relaterad till arbetskraftskostnader. Det ligger i andra saker, som relevant PLM-programvara, digitalt anslutna verktyg när det gäller OT (Operational Technology), smarta processer, IoT, AI etc.
– Idag är vi först i vårt verksamhetsområde med att producera kullagren helt automatiskt, där resten av våra konkurrenter monterar dem manuellt. Vi gör det också verkligen automatiskt, ingen människohand har berört lagren under produktionen. Som grädde på moset får vi också en superkvalitet, som är enastående på marknaden, hävdade SKF-chefen.
Han tillade att SKFs World Class Manufacturing-koncept också vässat ergonomin för de anställda i produktionen. Alla negativa fysiska effekter relaterade till manuellt arbete är borta. Processen att göra kullager är inte farlig längre, berättar Danielsson.
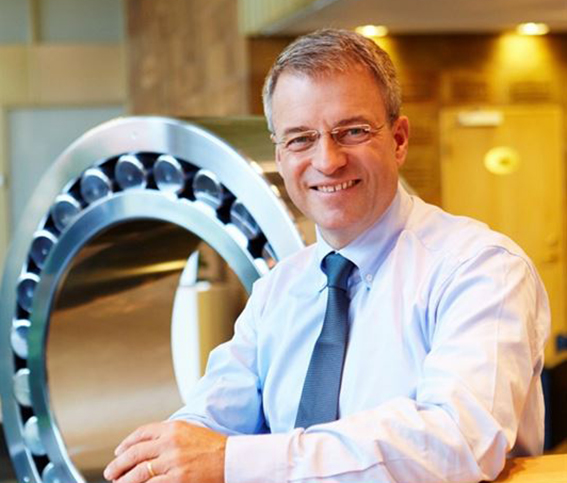
Hittills i Alrik Danielsons SKF-narrativ kring utvecklingen i företaget blir det tydligt att situationen för arbetarna på fabriksgolvet förändras: medan vissa typer av jobb blir föråldrade blir andra jobb beroende av och kommer att kräva nya kompetenser och färdigheter.
– Det är sant, kommenterade Danielson. Vi har ett ansvar att arbeta tillsammans med våra anställda och fackföreningar för att se till att vi verkligen utbildar människor och ger dem nya möjligheter. Men vi ska minnas att den här typen av teknikförnyelse, som jag har talat om, också öppnar upp nya chanser för våra kollegor att växa och få nya, mer givande jobb.
I detta sammanhang påpekade han också att företaget systematiskt arbetar med miljövänligare hållbara lösningar som återvinning och renovering av begagnade lager. Återigen är Siemens MindSpheres funktioner tillgängliga:
– Om du byter lager när systemet ”säger” att det är utslitet och borde bytas kan det skickas tillbaka till SKF för renovering. Denna cirkel kan sedan göras om och om igen, vilket inte bara innebär nya jobb, utan också minskar koldioxidutsläppen upp till 90 procent om det är så många kretsar som är involverade som möjligt. Detta är sålunda varken mer eller mindre än cirkulär ekonomi i praktiken.
Mer om Siemens roll i SKFs resa mot Industri 4.0
Att Siemens spelar en betydande roll som katalysator för SKF-chefens vision om framtiden står utom tvivel. Det är i sammanhanget också relevant att ta upp Siemens breda lansering av begreppet ”closed-loop manufacturing” (CLM); vilket är liktydigt med att man sluter cirkeln inom produktframtagning, med den digitala tvillingen som centralt begrepp och där processerna, från utveckling till fysisk tillverkning, hålls ihop med hjälp av digitala trådar och tajt integrerade, realtidsbaserade PLM/IT- och OT-system (Operativ Teknik).
På sista raden handlar detta om flexibla ”bortom Industri 4.0-lösningar”; från digital produkt-ideation, -definition och -konstruktion till likaledes digitalt uppbyggd tillverkningshantering på verkstadsgolvet, som där övergår i de fysiska produktionsprocesserna.
Med den digitala tvillingen i centrum är allt detta simuleringsbart i alla led, för att man ska kunna säkra att allt fungerar som tänkt innan man går över till de fysiska motsvarigheterna, då eventuella förändringar och upptäckta fel blir dyra att åtgärda.
Mot bl a denna bakgrund har SKF alltså valt att satsa på den tyska PLM- och automationsjättens lösningar och Siemens är också digital partner i SKFs ”världsklass tillverknings-projekt”.
Detta är viktigt och på något vis typiskt för det diversifierade IT-landskap som i allmänhet möter leverantörer och PLM-relaterade marknadsspelare. Inget system från en leverantör verkar stå ensamt.
I SKFs fall betyder det att de lösningar man kör in ifråga om Industri 4.0 i dagsläget möts av en miljö av andra system, som i sig måste vara och är tillräckligt öppna för att låta sig integreras i en helhet, till rimliga kostnadsnivåer. Minns i fallet med SKF att man alltså generellt inom produktutvecklingen jobbar med PTCs CAD-lösning Creo och med bolagets PLM-svit Windchill som ryggrad.
Men när man nu inlett Industri 4.0-resan söker sig den svenska kullagertillverkaren till en annan leverantör. Skälet är, som vi ska gå in på nedan, enligt Alrik Danielson, att man menar att Siemens styrka i sammanhanget är att man klarar av att ”omfamna helheten”; den diversifierade miljön. Samtidigt som projektet ligger med betoning mot automatiserad produktion och slutkundsinteraktion, så är en klassisk PLM-styrka – vilket är extremt viktigt sett i helhetsperspektiv – i Siemens-sfärens programportfölj, med Teamcenter som PLM-backbone, att man satsat på öppenhet och integrationskopplade helheter för att få till den sömlöshet som är en förutsättning för Industri 4.0.
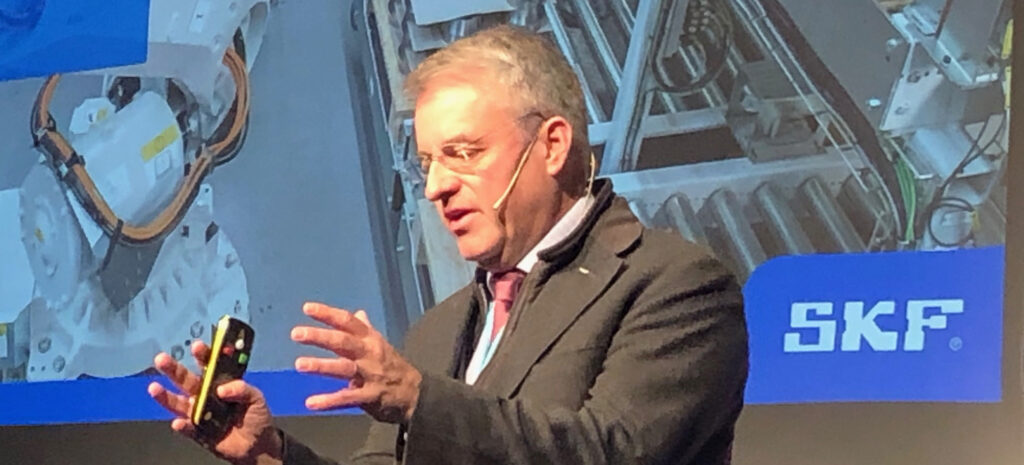
SKF-basen tror inte på inkrementella lösningar
Så, hur ser det då ut med implementeringen av den nya tekniken? En sak är tydlig, SKF-chefen tror inte på inkrementella lösningar här. Satsar man ska det på ett sätt vara fullt ut. Inte så att man ställer en helt fungerande existerande fabriks framtid på spel i ett teknikexperiment. Nej, långt ifrån detta. Istället handlar ”fullt ut-satsningen” om att välja ut en produktionslina i en fabrik och i denna köra det nya systemet fullt ut.
SKFs utvalda modell är att implementera enligt tre huvudfaser:
1) Icebreaker 2) Skala upp 3) Ställa in ”benchmarks”
– Ja, kommenterade Danielsson, så är det. För att vara effektiv måste du välja och satsa på en fabrik och en produktionslinje och göra det fullt ut. Det är inte farligt; om det inte fungerar påverkar du inte mer än just en fabrik och en produktionslinje. Du har fortfarande resten av dina gamla anläggningstillgångar till ditt förfogande.
Det finns också lärdomar att göra av varje misslyckande, tillade han. Och med de upplevelserna i din ryggsäck kan du börja om igen och förhoppningsvis lyckas bättre nästa gång.
Alltså: Börja inte stort, börja inte med alla på en gång, men där du satsar – gå ”all in”!
Varför satsar SKF på Siemens i jakten på Industry 4.0?
– Det finns många människor och företag som arbetar med dig i vissa och specifika delar av värdekedjan. Men det är väldigt få som kan ta på sig och omfamna hela kedjan. Därför är vi partners med Siemens och vi arbetar tillsammans i hela värdekedjan, sa Danielson.
Han hävdade att Siemens också har ambitioner att vara huvudleverantör av digitala lösningar i SKFs resa mot Industri 4.0.
– Vi börjar i Sverige, vi gör det i Tyskland, vi gör det i Kina och i USA. Det vi gjorde i det senare fallet – som började för lite mindre än ett år sedan – var att skapa en komplett lösning i vår racingfabrik i Alaska. Det är en inte alltför stor anläggning och passar bra för oss att driva integration och implementering i.
Hur man än ser på det är SKFs resa synnerligen spännande. Men den är egentligen bara påbörjad. Om inte Coronaeffekter sätter hinder i vägen kommer bolaget att gå en mycket ljus framtid till mötes och ännu en gång visa att man är varken mer eller mindre än något så paradoxalt som en drygt hundraårig startup.
Med Alrik Danielson vid rodret ser denna proaktiva kultur ut att förstärkas.