SKIFTE AV AFFÄRSMODELL: FUNKTION ISTÄLLET FÖR PRODUKT
Victoria Van Camp har mycket att göra i dessa dagar. Inte nog med att Coronviruset och pandemin ställer till det i planeringskalendern och i fabrikerna mitt i en omfattande digitaliseringsprocess, vi lever dessutom i ett industriellt tidevarv där det mesta som tidigare gällt ställs på huvudet. På få ställen är detta lika tydligt som inom kullagerbranschen och för en industrijätte som SKF. Bolaget – med 43,000 anställda, 100 fabriker globalt, och en omsättning som 2019 landade på nära 10 miljarder dollar, motsvarande 86 miljarder kronor – genomgår idag ett skifte av affärsmodell med tillhörande teknologiförändringar, automatiserade produktionsprocesser och annat. Man avancerar i hög grad fram mot ett genomslag dels för Industri 4.0-upplägg, dels för ”Product-as-a-Service-tanken.”
– SKF’s fokus skiftar i detta från att bara sälja ett antal kullager till att snarare sälja roterade varv. Vi på väg bort från idéerna om att köra ut bara vassa kullager till våra kunder, för att istället sälja och upprätthålla den funktion de har, roterade varv utan avbrott, säger SKF’s CTO.
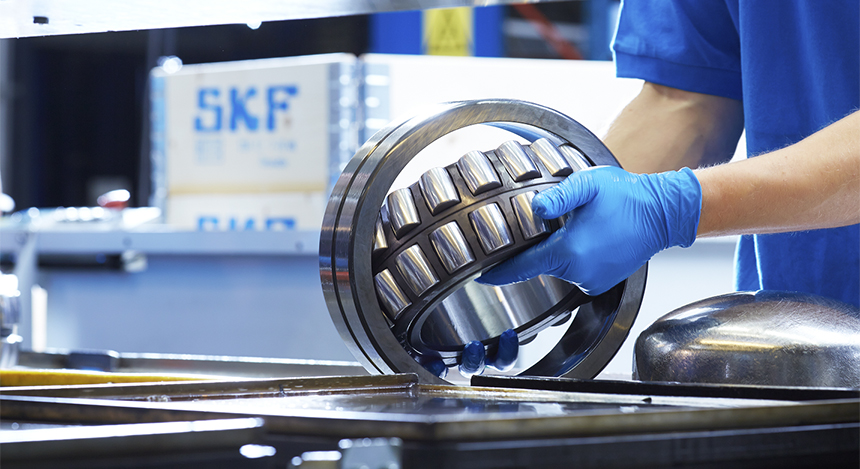
SPÄNNANDE IDÉ MED DRAMATISKA FÖLJDER
Funktion istället för bara produkt, alltså. Det är en spännande idé som får dramatiska följder. Plötsligt talar vi till exempel mer om klimat- och miljöfaktorer, som hållbarhet, cirkuläritet i hanteringen och totalekonomi, än om att bara köra ut nya kullager ”en masse”, där varje trasigt kullager måste ersättas med ett nytt, till dryga kostnader. Detta är inget som intresserar kunderna. De vill inte ha denna typ av problematik. De vill ha kullager som fungerar utan avbrott, roterade varv helt enkelt.
I ett slag förskjuts därför de centrala idéerna kring hur produktframtagningen ska läggas upp mot nya modeller för produktutveckling, tillverkning och eftermarknad när man på SKF planerar för framtiden.
För den som lovar att leverera roterade varv utan avbrott blir incitamentet att vässa kvaliteten ett nytt fokus. Tjänar man pengar på funktion istället för att bara sälja så många nya kullager som möjligt blir därmed en rad nya teknologier hyper-intressanta, konstaterar Van Camp:
– Vi måste förstås kunna mäta antal varv, det är basalt, men samtidigt är siktet inställt på ett läge där kullagren själva talar om för oss när det är dags att byta något som är på väg att slitas ut, eller prestanda som går ner av något annat skäl. Men vi måste få en mer omfattande ’berättelse’ från lagret självt; en analys som långt ifrån bara handlar om effekten av ett slitage, orsakat av exempelvis vibrationer i kullagret p g a yt-förslitning. Då är det redan försent. Vi måste komplettera med andra typer av sensorer och mätdata, som t ex kan ge besked om det föreligger en propp-bildning i ett rör som försörjer kullagret med smörjolja. Bildas sådana proppar kommer inget, eller för lite, smörjmedel fram till kullagren. Därmed är yt-förslitningen snart ett faktum, med omfattande och kostsamma insatser att återställa. Det är alltså redan när smörjoljeproppen bildats man måste kunna ingripa, fixa oljeförsörjningen och därmed minska slitaget innan det ställt till någon skada på rullagret.
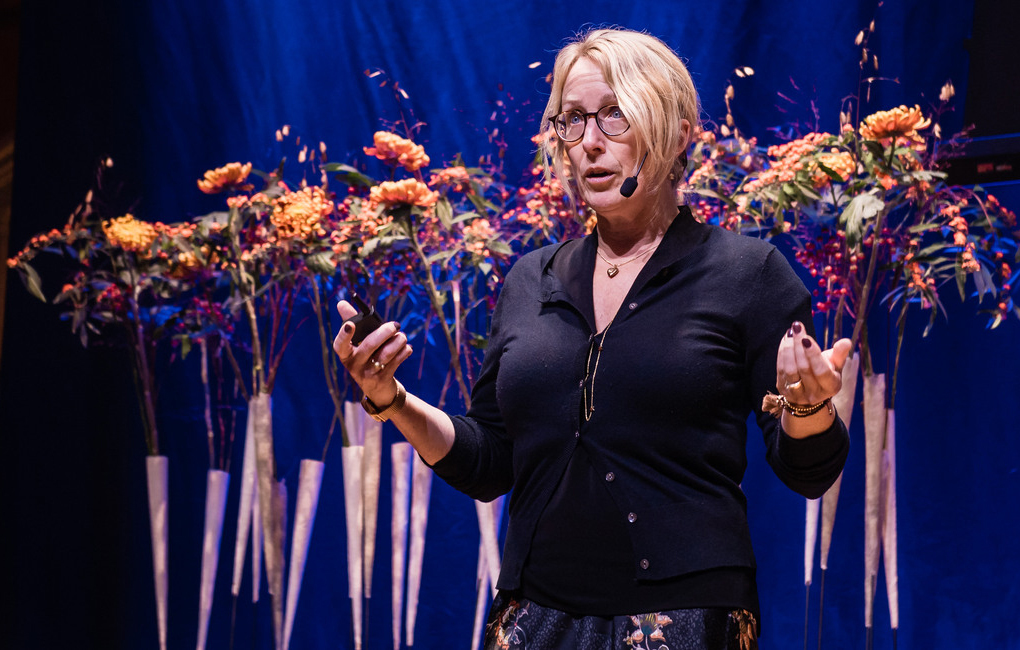
ATT TÄNKA PRODUKTUTVECKLING PÅ ETT NYTT SÄTT
Poängen är sålunda inte bara att mäta en sak, t ex vibrationer eller ytförslitning, utan att också i ett bredare perspektiv titta på rätt saker, menar SKF’s teknikchef. Men hur kommer man dit?
– Kedjan är lång och börjar egentligen redan i utvecklingsänden hos den som designar en produkt som innehåller kullager, säger hon.
Man måste börja tänka produktutveckling på ett nytt sätt; en attackvinkel där designen blir genomförd på ett sätt som underlättar drift- och serviceinsatser. Ska man idag byta ett kullager i, låt säga, i en normalanvänd pappersmaskinen, ser läget i maskinen inte ut som när den var ny. Tiden har gått, korrosion och annat gör att det inte bara är att plocka ut kullagret. Man kanske t o m måste använda kofot eller blåslampa för att få loss det.
– Detta håller förstås inte sett till följder som kostsamma avbrott och måhända ett kullager som gått sönder av den omilda behandlingen vid underhållet; och måste bytas ut mot ett nytt. Det hela blir praktiskt omständligt, logistiskt besvärligt, tidsmässigt utdraget och troligen också dyrt. Här måste man tänka i nya banor redan vid konstruktionen av maskinen, fordonet, eller egentligen i all design som innehåller lösningar som med modern teknik numera mer handlar om uppgradering av mjukvaror, sensorer eller elektronik i ett skal, än om kompletta maskin- eller produktbyten. Produktutvecklare, ingenjörer och andra involverade måste gå mot lösningar som förenklar denna typ av åtgärder, hävdar Van Camp.
Hon nämner som ett exempel att man istället för ett lagerhus designar ett delat lagerhus, eller att man på SKF lägger på nya typer av nano-ytbeläggningar som gör att det inte korroderar. Det handlar om att etablera möjliga designingångar för framtida uppgraderingar som man i designögonblicket kanske inte ens vet vad det är. Så lite som möjligt ska försvinna ur produktlivscykeln, när produkterna blir till ”kärl” eller ”skal” som enkelt kan fyllas och uppgraderas när nya prestanda eller kapabiliteter ska in.
– Här finns enorma utmaningar för oss som ingenjörer, säger SKF’s teknikchef.
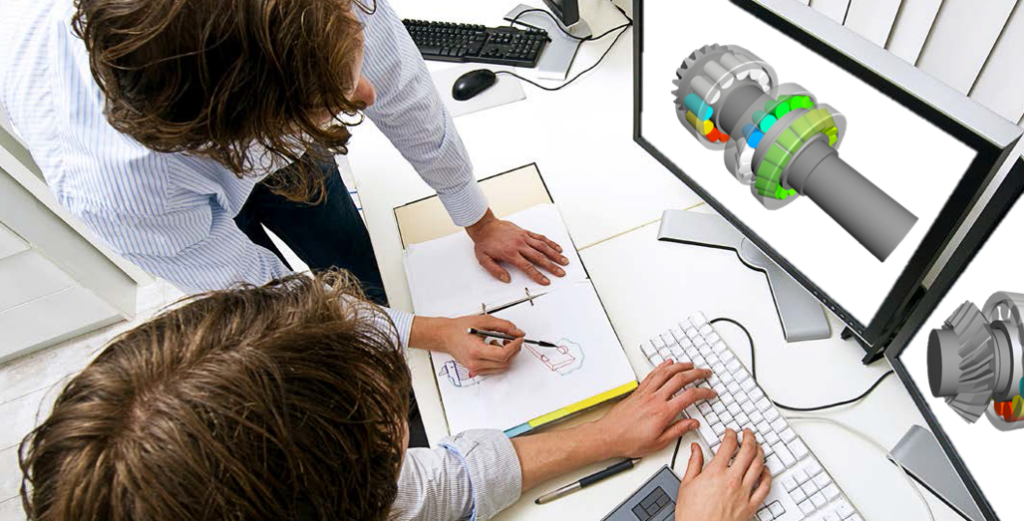
PTC PÅ PRODUKTUTVECKLINGSSIDAN,
SIEMENS PÅ AUTOMATION/TILLVERKNING
Men förändringarna stannar givetvis inte där, de fortplantar sig i hela kedjan, från SKF’s kunder, till bolagets egen produktutveckling, distribution och tillbaka till kunderna och kundernas kunder, där det är relevant. För SKF’s del innefattar detta allt ifrån bolagets nuvarande PLM-stöd inom produktutveckling, till IT-/MES-/OT-stöd, etc, vid tillverkning och programstöd för eftermarknadsinsatser.
Man behöver inte fundera särskilt länge för att inse att det mjukvaru- och automationslandskap som ska ta hand om detta inte bara tenderar att bli diversifierat, utan också tämligen komplext. Även om flera av spelarna på PLM-plattformsområdet har en stark tro på att det egna systemet klarar hela kedjan, ”end-to-end”, är det inte vanligt att en enda leverantörs mjukvaror eller plattform klarar av att på ett optimalt tillfredställande sätt kunna möta alla behov från en verksamhet på OEM-nivå. Det har dock börjat röra på sig även här, vilket vi ska gå in på nedan.
Men först ska noteras att det tillhör saken att de vanligaste PLM-leverantörerna inom maskinteknik- och andra branscher, Siemens, Dassault, PTC, Aras och andra har varierande styrkor. Eftersom SKF har PTC och Siemens som huvudleverantörer av PLM- och produktionsrelaterad mjukvara har vi tittat närmare på dessa bolags särskilda styrkor.
PLM&ERP News har också, för att få den allmänna bilden kring hur det generellt ser ut på marknaden som möter dessa utvecklare, talat med Gartners respekterade analytiker, Marc Halpern. Vi har också tittat lite mer konkret vilka verktyg respektive bolag kan lägga upp på bordet.
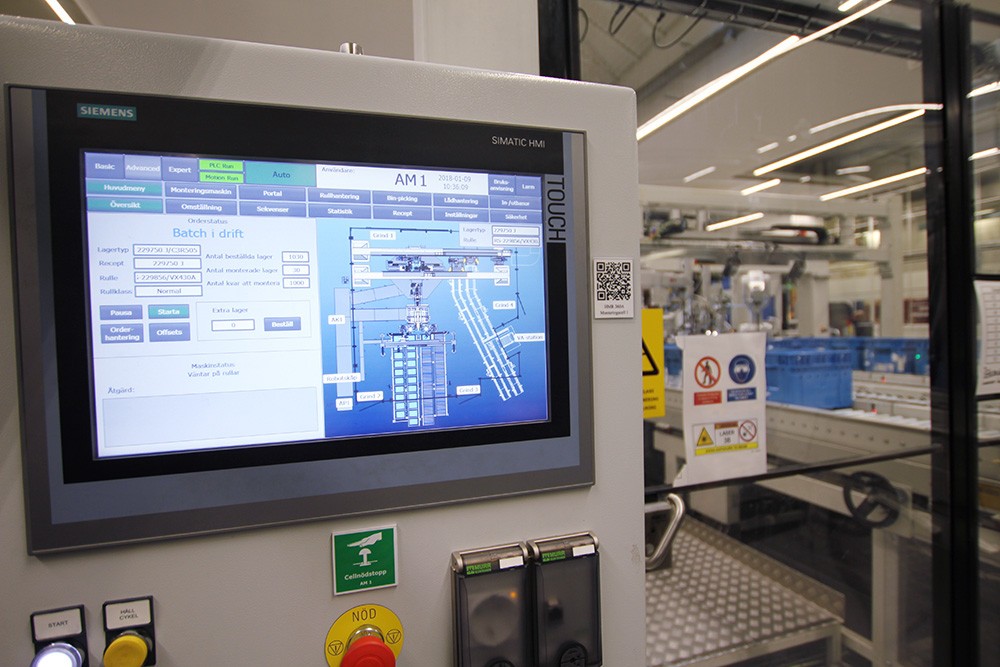
SIEMENS: Vass cPDm och sömlösa kopplingar till produktionen
De kanske mest utmärkande dragen för Siemens på PLM-området är främst en rik flora av applikationer och starka, sömlösa kopplingar mellan produktutveckling och tillverkning. Det handlar i dagsläget om marknadens effektivaste lösningar för arbets- och dataflöden genom stora delar av värdekedjan. I detta har Siemens bra teknik för PDM/PLM, modellbaserad systemteknik (MBSE), digitala tvillingar, simulering och tillverkningsfunktioner. Vidare ger SAP-alliansen, som meddelades i juli förra året, Siemens oöverträffade möjligheter att leverera en riktig digital tråd.
– En generell observation i sammanhanget är att alla bolag som funnits med på banan under lång tid har en viss legacyproblematik att hantera. Även om de ledande spelarnas kapaciteter och resurser är goda, så belastas de också med en del äldre teknik, som viktiga kunder fortsätter att vara beroende av. Ingen är nu ensam om detta, tvärtom måste alla aktörer, Dassault Systemes och PTC inkluderade, hantera en liknande ”arvsproblematik”, men de som har mer av detta utmanas också mer, säger Halpern.
Så långt Gartneranalytikern, men klart är alltså att Siemens alltid har varit starka på cPDm (”collaborative Product Definition management”), alltså det som kan betraktas som ryggraden i ett PLM-system. Andra framstående områden är lösningar för digital tillverkning, automation och OT (Operativ Teknik, från ”verkstadsgolvet”). På senare år har man också förstärkt simuleringssidan kraftfullt och har – bortsett från en allt vassare teknisk kapacitet – med sin Simcenterplattform, inklusive en rad kopplade appar, avancerat till en kommersiell position som marknadstvåa efter Ansys, nya uppgifter gör f ö gällande att man passerat Ansys ifråga om intäkter. Detta gäller även EDA-området, (Electronic Design Automation), där man i Mentor-köpet 2017 fått en succéapplikation, som 2019 var det huvudsakliga skälet till att EDA-området, enligt analytikern CIMdata, genererade 34,1 procent av PLM-sidans intäkter.
SIEMENS DRIVER PÅ INTEGRATIONSSIDAN
MED PARTNERSKAPET MED eQ TECHNOLOGIES
När det gäller dataintegration har Siemens fokuserat på sömlös integration och data- och processorkombination över Xcelerator-portföljen, med appar som:
• Det avancerade CAD-verktyget NX
• Simcenter (CAE)
• Polarion (ALM, Application Lifecycle Management)
• Technomatix (DM, digital tillverkning)
• OP-center (MES / MOM, Manufacturing Operation Management)
• Mentor (EDA, elektronisk designautomation)
• Teamcenter (cPDm), Mendix (IoT-samarbete)
• MindSphere (IoT-operativsystem)
Sedan september 2020 har integrationssträvandena inom Xcelerator-portföljen drivits ännu längre framåt än tidigare med nya och spännande bidrag. Detta är starkt kopplat till SKFs arbete och genom ett utökat strategiskt partnerskap med eQ Technologic kring eQube-lösningen finns en del intressanta potentiella framsteg att hämta med denna lösning.
En kvalificerad gissning är dock att integrationen mellan PTCs Windchill och Siemens Teamcenter initialt kommer att baseras på ProSteps OpenPDM-lösning, eftersom eQube kom upp som en option när affären skulle stängas.
Slutsatsen baserat på vad som hittills är känt är att SKF kommer att fortsätta med och försöka skala upp sitt proprietära MES-system, Artemis; samtidigt som de arbetar för att inse värdet av OP-center och integrationen till Teamcenter som ett alternativ som är en möjlig “dark horse” i framtiden.
Detta överensstämmer också med Van Camps syn på vikten av att kunna samarbeta med konkurrerande lösningar inom ramen för samma företag. Med eQube har Siemens fått tillgång till en serviceplattform för att skapa digitala trådar, som kopplar ihop ett antal olika system: PLM, ERP, ALM, IoT och andra lösningar inom IT och OT (Operativ teknik). EQube utökar också möjligheterna hos lågkodsplattformen Mendix och kan hjälpa till med industriell data och systemintegrationer.
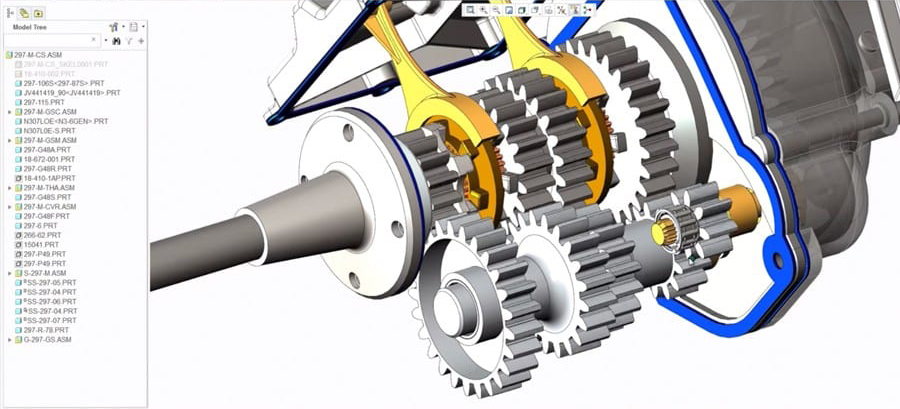
PTC – PLM-SVITEN WINDCHILL RYGGRAD I PRODUKTUTVECKLINGEN
Lite av en paradox i SKF-sammanhanget är att SKF inte valt att satsa på PTC när det gäller IoT. Detta område har nämligen generellt utvecklats till en särskild styrka inom för PTC, och ThingWorxs lösningens ledande roll har också verifierats i flera analytikers utvärderingar. Inte minst då Gartners, där analytikern så sent som nu i oktober positionerade IoT-plattformen, som också kopplats till Windchill PLM, som marknadsledande på IIoT-sidan (Industrial IoT) i Gartner’s Magic Quadrant 2020. Å andra sidan har Siemens vässat sitt IoT-operativsystem, MindSphere, rejält under det senaste året och betraktas nu som en av de ledande plattformarna i exempelvis “The Forrester Wave: Industrial IoT Software Platforms, Q4 2019.”
PTC handlar dock långt ifrån bara om styrka ifråga om utveckling av nya teknologier. Man har tvärtom ett brett och stort teknologikapital, men en bit kvar på resan att integrera denna bredd till en allt smidigare flödande helhet, som är målet.
Väger man samman de viktiga marknadsanalytikernas syn på PTCs styrka så handlar denna om konvergensen av teknologier för produktdesign, datahantering, support för livscykeln och för eftermarknadsservice. I dessa bitar har PTC kapabiliteter som ger hävstångseffekter för dessa teknologier och investeringen i dess färdplan för att stödja produkter från koncept till service, särskilt för att utnyttja produktdata som en strategisk tillgång under hela livscykeln. Detta är enligt Marc Halperns generella observation något som är av största vikt för alla utvecklare som har ambitioner att vara ledare på PLM- och tillverkningsområdena och samtidigt utveckla lösningar kopplade till eftermarknadssidan.
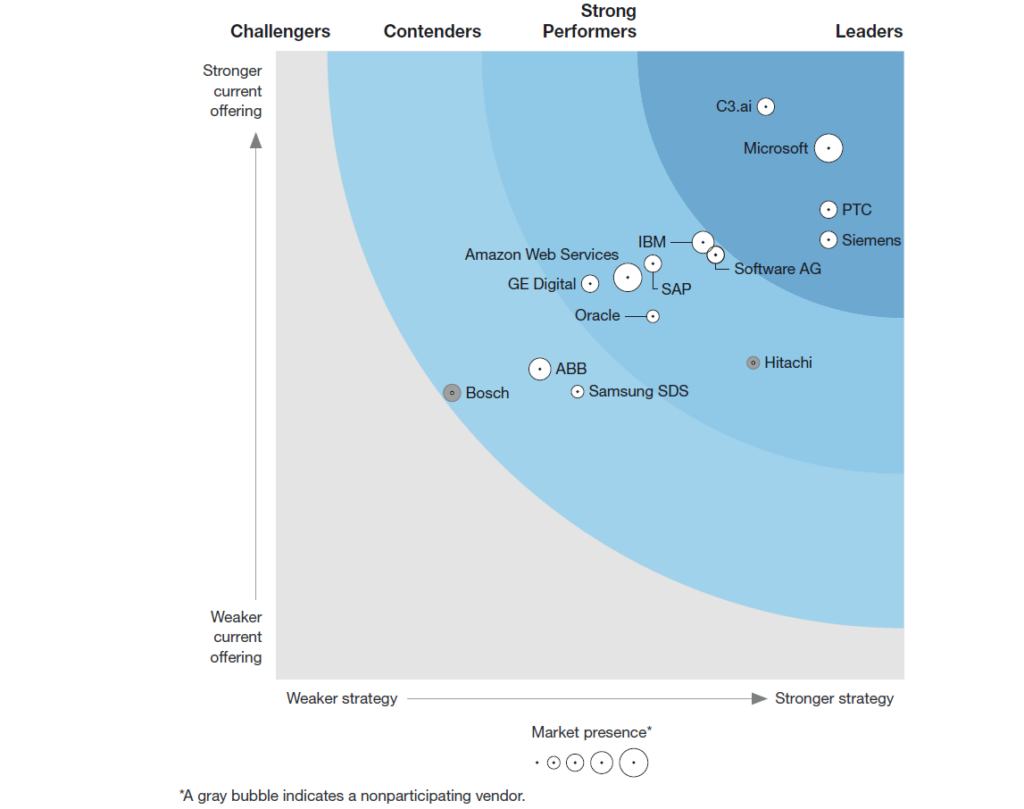
Rockwell Automation-investeringen och partnerskapet med PTC lägger till en tillverkningsdrifts- och underhållsdimension, som har stor potential för återkopplingsloopar som kontinuerligt förbättrar design för tillverkningsbarhet och design för service.
Ett starkt och visionärt ledarskap är också viktigt, vilket är en punkt som i högsta grad kan sägas uppfyllas relaterat till Jim Heppelmanns ledarskap.
Marc Halperna noterar vidare att, ”alla som köper och utvecklar nya lösningar och kapabiliteter på mjukvarusidan också kommer att ha mycket att göra ifråga om att skapa integrationen av alla teknologier.”
Vid sidan av IoT-området har alltså också PTC skapat framstående Augmented Reality-lösningar inom produktutvecklings- och eftermarknadsområdet (AR) med sin Vuforia-plattform – också här kopplad till PLM-plattformen Windchill och CAD-mjukvaran Creo.
Vidare har man i Windchill’s PDM Link en stark lösning på cPDm-sidan, liksom inom CAD med Creo-mjukvaran.
En intressant utvecklingsgren inom bolaget är, precis som Marc Halpern noterar, partnerskapet med Rockwell på automations- och MES-/MOM-/OT-sidan (Operativ Teknik, ”på verkstadsgolvet”), där man börjat flåsa marknadsledande Siemens i nacken, sett till kopplingarna mellan produktutveckling och tillverkning.
2020 har också markerat betydande framsteg i samarbetet mellan Rockwell och PTC; en samverkan där f ö också Microsoft kommit in för kopplingarna till molnplattformen Azure.
Under fjolåret har man också släppt ”Factory Insights as a Service-lösningen”, vilket är den andra stora paketering av IT/PLM och OT, som de två partnerföretagen lägger upp på bordet efter sin partnersatsning, initierad under 2018.
Den första var sammankopplingen mellan Rockwells MES-lösning, FactoryTalk, och PTC’s PLM-lösningar – FactoryTalk Innovation-sviten – som släpptes kort tid efter starten för samarbetet, redan i slutet av 2018. Poängen med detta paket var att skapa sömlösa kopplingar mellan IT/PLM och OT, alltså data från maskinerna på verkstadsgolvet. Övergripande var det som PTC och Rockwell la upp på bordet en lösning som gör det möjligt att optimera industriella verksamheter och öka produktiviteten genom att ge beslutsfattare förbättrade data och insikter. Inkluderat i FactoryTalk Innovation-sviten är FactoryTalk Analytics-, MES- (Manufacturing Execution Systems) och MOM-plattformar (Manufacturing Operation Management), liksom PTCs ThingWorx Industrial IoT-plattform, som inkluderar kopplingar till Kepware (konnektivitet mellan enheterna på verkstadsgolvet) och AR/VR på Vuforia-plattformen.
BOM-HANTERINGEN ETT ”WHITE SPACE”
Detta sagt ska konstateras att BOM-hanteringen hittills baserats på Excel- eller lokala lösningar. Man har kort sagt i traditionell mening inte haft något specifik och generellt upplagt systemstöd för detta, utan det har behandlats som ett ”white space”, med öppna möjligheter för egna lokala lösningar.
I och med det nya avtalet med Siemens finns dock förutsättningar att förändra detta mot en mer central och sammanhållen lösning, som kan vara av vikt för att strömlinjeforma produktionen; något som i högsta grad ter sig eftersträvansvärt i en organisation som har över hundra fabriker globalt och där man, som en konsekvens av Victoria Van Camps tankar, går mot en ytterligare tillväxt ifråga om lokalt förankrade produktionsenheter. Saken är den att det i den paketering som Siemens erbjuder finns stöd för mBOM- (manufacturingBOM) och BOP-hanteringen (”Bill of Process”).
Att det börjar röra på sig i samverkansriktningen visas kanske i ännu högre grad för övrigt av det avtal om samarbete kring försäljningen av PLM-system som omtalas ovan, det mellan Siemens och SAP, där de senare bl a ska börja marknadsföra och sälja Siemens Teamcenter-plattform.
Till saken hör också att SKF använder sig av just SAP på affärssystemsidan S4/Unite, som enligt plan ska rullas ut i koncernen, bolag för bolag, fram till 2022. Startår för detta på SAP HANA baserade system var 2015, till en total beräknad kostnad på mellan 8 till 10 miljarder kronor.
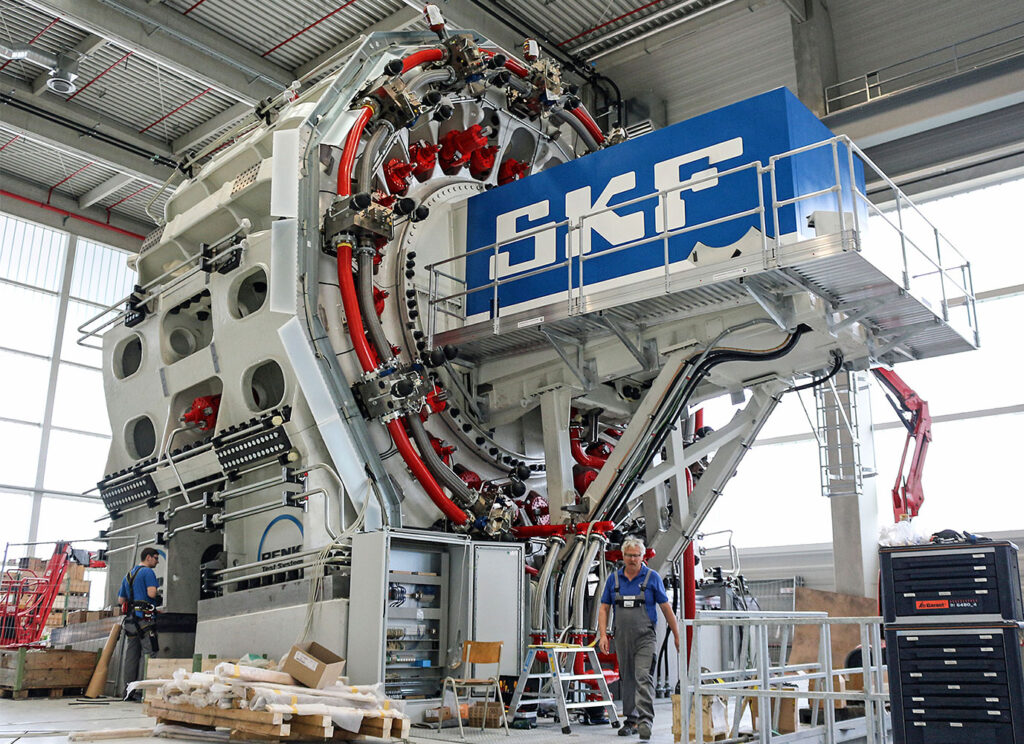
ENDA BRANSCHSPELAREN MED HELT
MASKINELLT MONTERADE SFÄRISKA KULLAGER
Med denna arsenal av digitala verktyg har SKF redan kommit en bra bit på väg. Bolaget är i dagsläget t o m den enda branschaktören som monterar sfäriska kullager helt maskinellt, automatiserat och utan mänskliga händer.
– Det är klart en huvudpoäng i synen på vår framtid, säger Victoria Van Camp. Det är bra för miljön, bra för människorna och överlägset för ergonomin.
Hon talar i sammanhanget om ”World Class Manufacturing-konceptet”, som nödvändigt inslag för att vara kvar i marknadstoppen.
– Visionen är enkel; våra kunder vill ha minskad friktion, maskiner som går snabbare, längre, renare och säkrare. Genom att lösa detta på effektivaste och mest hållbara sätt bidrar vi till en värld av tillförlitlig rotation, byggd på miljömässig hållbarhet, säger SKF’s teknikchef.
CENTRAL IoT-MONITORERING EN ÖVERGÅENDE FAS
I detta finns nu en rad faktorer av avgörande betydelse, IoT är en sådan faktor. Både sett i perspektivet av vad man gör internt på bolaget i tillverkningen, men kanske i ännu större omfattning vad det innebär för kunderna och eftermarknaden.
För drygt ett år sedan öppnade SKF ett Rotating Equipment Performance Center (REP) i Göteborg. Redan har ett antal större nya kontrakt tecknats som bland annat inkluderar fjärrövervakning, analys och förbättringsarbete kring de rullager som SKF levererade. Efter detta år dokumenteras nästan 30 000 mätpunkter – nästan dubbelt så många som tidigare mätpunkter.
Tillsammans med en ny prestationsbaserad affärsmodell har SKF tagit en spännande position på vägen mot produkten som tjänst (”Product-as-a-Service”). Man är med detta drag en pionjär på området.
Det låter förstås som en mycket intressant och som lönsam ingång till framtiden, men Van Camps syn på saken låter i förstone en aning förvånande:
– Det är en jättebra idé, men ändå en övergående fas, säger SKF’s teknikchef och fortsätter, i det större perspektivet är det faktiskt bara början på en resa där jag tror att denna typ av central monitorering på lite sikt visar sig ha ännu bättre efterföljare. Istället är målet inställt på mjukvaruplattformar, som ’själva’ kan alerta för att något behöver göras, men som också, genom vassa AI-lösningar, ’själva’ kan vidta de åtgärder som behövs för att lösa problemet.
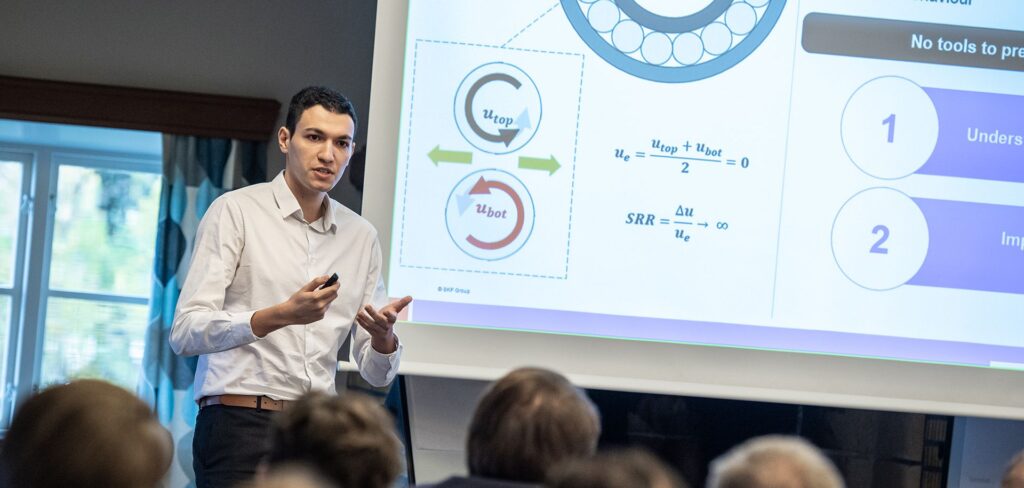
AI SKA TA ÖVER – DÄRFÖR KÖPTES ISRAELISKA PRESENSO
Ett monitoreringscenter som på sikt ska avvecklas alltså; varför och vad blir det istället?Vi kan på sikt inte ha en växande skara människor som ska sitta och analysera det som händer och vidta rätt åtgärder. Det finns inte någon långsiktigt bärbar tillväxt i en sån grundidé. Här måste siktet vara inställt på nästa fas – där AI kan ta över de mesta av monitorerings-, diagnos- och åtgärdshantering. Det var därför vi nyligen köpte det israeliska AI-företaget Presenso, säger Victoria Van Camp.
Sensorer har alltså i detta sammanhang en helt annan framtid än bara som monitoreringsunderlag. Vi talar istället om sensorer, som brett uttryckt kan samla in data från diverse maskiner och då inte bara i perspektivet av vibrations- eller temperaturmätningar. Minns smörjpropps-resonemanget ovan. Detta för med sig att en effektiv IoT-lösning måste gå till betydligt fler sensorer än bara de som sitter i själva kullagret. Det kräver förstås, säger Van Camp, ”att sensorer inte bara måste bli mycket billigare; de måste med sina kapabiliteter kunna placeras i en intelligent miljö och också tåla stora temperaturvariationer och kunna mäta specifika flöden etc, etc.”
Utmaningen är att ta startup-labbens ”proof-of-concept-lösningar” ut i verkligheten och få dem att fungera där. I smuts, i vatten, i kyla, i värme och så vidare. Industrialiseringen är kort sagt problemet. Presenso-köpet ska förhoppningsvis kunna resultera i lösningar i denna riktning. De har den typer av lyssnande, idérika, kommunicerande och sinnesmässigt öppna ledarskap som krävs för att förverkliga de här bitarna kring framför allt IoT. Vi satsar stenhårt här och har anställt 50 personer bara i Israel för att utveckla det här området.
Men tankarna runt utvecklingen visar också på problematiken med en diversifierad IT-verklighet, konstaterar SKF’s CTO.
– Samarbete är ett nyckelord. Mjukvaror är förstås också ett avgörande inslag för att vi ska kunna göra det vi siktar på. Jag nämner återigen Presenso-köpet. De hade lösningar som innehöll betydligt mer och bredare information än något vi tidigare stött på. AI-mjukvaran är det som möjliggör i sammanhanget att sätta rätt sorts data i ”rätt fack”. Applicerat på denna ”mall” kan data användas på ett sätt som ger fantastiskt intressanta insikter. Mjukvaran kommer givetvis att behöva sensorer för att få in de data som behövs, men det finns också annan data som kontrollsystemet har och som är av stor betydelse. Tillsammans kan vi av detta, via mjukvaran, få ut den information vi vill ha.
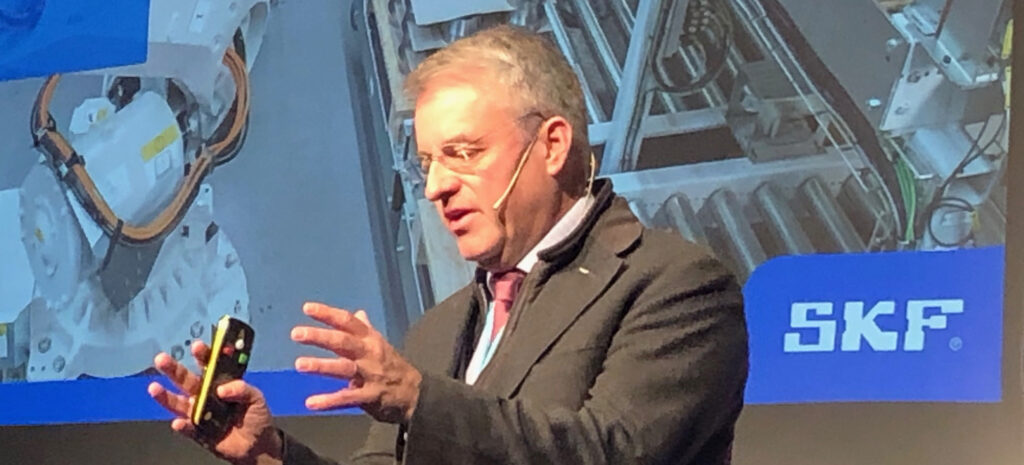
INSPIRERANDE ATT JOBBA MED AVGÅENDE CEO, Alarik Danielsson
SKF är pionjärer och inte är rädda för att ta risker, säger Victoria Van Camp.Vi har en stark vision och den ligger kvar, trots bytet av CEO och koncernchef, när Alarik Danielsson slutar 2021, det har styrelsen försäkrat oss om; vilket är bra. Han har varit mycket inspirerande att jobba med och han har utmanat oss varje dag. Vi i teknikteamet levererar ständigt nyheter, att de blir klara är bra, men Danielsson ställer ofta följdfrågan: ”men hur är det nu med det där andra projektet vi hade på gång?”
Ständigt med blicken mot framstegshorisonten alltså, men det är å andra sidan inte på något sätt lätt att sprida informationen kring hur saker och ting är tänkta att utvecklas på ett sätt som får de plus hundra fabrikerna globalt, att gå i takt.
– Precis, säger Van Camp. Dessutom talar vi om hundra fabriker i en mängd länder, med olika lagstiftningar och skilda traditioner. Om det bara vore så lätt som att man sitter på huvudkontoret och bestämmer hur det ska vara och så blir det så; ja, då vore det lätt. Men så är det nu inte. Jag menar att tittar man noggrant på saken så finns det inte många stora OEM-företag som på kort tid totalt lyckats stöpa om sitt ”footprint” för tillverkning, parallellt med en teknikomställning. Tänk på Volkswagen, Caterpillar eller Volvo Cars. Saker och ting tar tid och snabba omställningar är inget man ser varje dag. Vi är precis som dom mitt inne i detta.
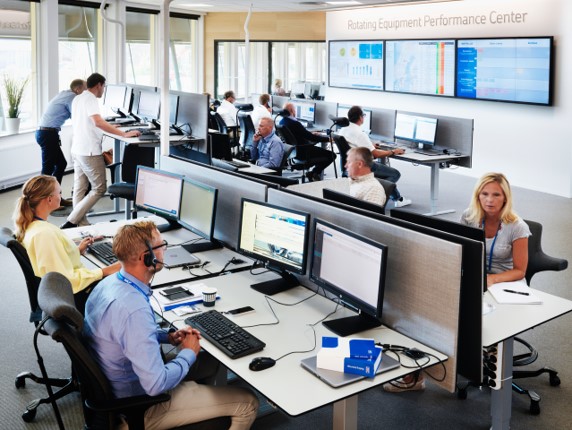
SKALBART UTAN ATT MAN SKA BEHÖVA ANSTÄLLA ARMÉER AV FOLK
Lika lite som det är det för Volkswagen, Caterpillar eller Volvo Cars, är denna omstöpning ingenting SKF inför över en natt. Men man har visionen som behövs, arbetet är igångsatt i form av ”World Class Manufacturing-konceptet”.Detta är ett sätt att automatisera, ja, men mycket mer än så. Siktet är inställt på att ha en fullständigt flexibel och skalbar produktion, utan att behöva anställa arméer av människor. Varför är det så viktigt? Vi tror att med IoT gör att vi ska kunna avveckla detta med mellanlager. Om man tänker efter; vilket otroligt slöseri det är att det måste ligga saker på stock. Det finns säkert beräkningar på vilka enorma värden som ligger på lagerhyllor, men det man egentligen vill åt – förutsatt att vi kan komma till en värld där allt är sensoriserat – så ska alla dessa sensorer som finns, eller ska finnas, i alla maskiner som står och går ute i världen – är att få till sensorer kopplade till fabriker; sensorer som ska kunna säga till att, ”nu behöver vi ett rullager, eller nu behöver vi ett cylindriskt lager”. Vi vill alltså komma ned till egentligen en en-stycks-produktion med noll ”re-setting”. Förr kunde man bara drömma om sånt – idag finns verktygen som gör det möjligt att kundernas maskiner ”talar om” för oss när det är dags.
Det handlar alltså inte om någon typ av entusiasm över vilken fantastisk teknik det finns och att den ska införas bara för att den är ny. Det handlar om en konsekvens av något som behövs och som kan lösas på ett smart sätt.
– Vi har detta i vår Göteborgsanläggning och bygger det nu också i vår tyska anläggning i Schweinfurt. Inte rakt igenom ännu, men det är under stegvist införande. Det är också så att ska vi överhuvudtaget kunna producera i Europa måste vi ha den automatiserade skalbarhet och flexibilitet jag talar om för att det ens ska vara möjligt att komma till lönsamhet. Men ”World Class Manufacturing”-tanken finns förstås med grundkoncepten för de fabriker som är under uppförande i Kina t ex. I det senare fallet startar vi också från ett blankt papper, vilket givetvis underlättar att komma rätt från början. I de fabriker där vi redan har maskiner och etablerade produktionslinjer är genomförandet givetvis svårare.
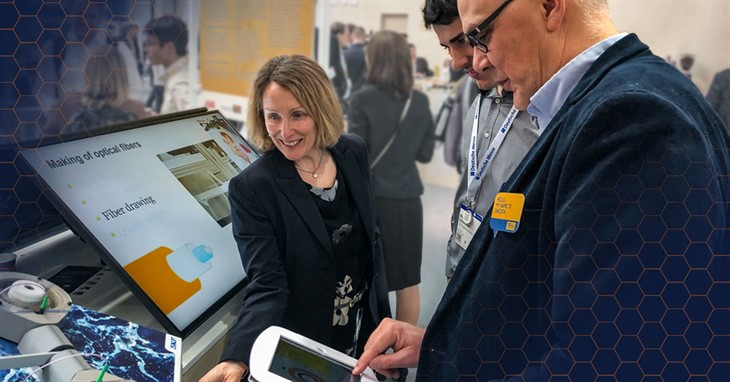
TROR INTE PÅ INKREMENTELLA LÖSNINGAR
Hur implementeriar man den nya tekniken? En sak är tydlig, SKF tror inte på inkrementella lösningar i detta. Satsar man ska det på ett sätt vara fullt ut. Inte så att man ställer en helt fungerande existerande fabriks framtid på spel i ett teknikexperiment. Långt därifrån. Istället handlar ”fullt ut-satsningen” om att välja ut en produktionslina i en fabrik och i denna köra det nya systemet fullt ut.
SKFs modell är att implementera enligt tre huvudfaser:
1) Icebreaker
2) Skala upp
3) Ställa in ”benchmarks”
Tanken är att för att vara effektiv måste man välja och satsa på en fabrik och en produktionslinje och göra det fullt ut. Det är inte farligt; om det inte fungerar påverkar du inte mer än just en fabrik och en produktionslinje. Man har fortfarande resten av sina ”gamla” anläggningstillgångar till sitt förfogande.
Det finns också lärdomar att göra av varje misslyckande, menar Van Camp. – Och med de upplevelserna i din ryggsäck kan du börja om igen och förhoppningsvis lyckas bättre nästa gång.
Alltså: Börja inte stort, börja inte med alla på en gång, men där du satsar – gå ”all in”!
Sammantaget kokar detta ner till att använda människor i produktionen, där människor behövs. Men det innebär inte att vi på något sätt rationaliserar bort alla människor från vår produktion. Vi kommer alltid att behöva människor, men de kommer att göra andra saker än tidigare tunga, slitsamma, manuella och repetitiva arbetsuppgifter, t ex på servicesidan. Maskiner och robotar, styrda av smarta AI-algoritmer och ”machine learning” monterar exempelvis sfäriska rullager istället för att det görs för hand.
”MILJÖVÄNLIGA MODELLER ÄR IDAG
EN BRA AFFÄR, TACK VARE NY TEKNIK”
– Jag kopplar här också på mitt tidigare resonemang om cirkuläritet och grönare tillverkningsmodeller. För att detta ska bli verklighet, t ex att man återtar, renoverar och uppgraderar kullager istället för att kassera dem, är mänskliga bedömningar och viss manuell hantering nödvändig. Att förändra efter ett sånt mönster är bara positivt i en rad miljövänliga perspektiv och där kommer det att skapas väldigt många nya jobb, förklarar Victoria Van Camp.
Hon tillägger också att denna typ av rekonditionering är något man vill göra lokalt.
Behöver man t ex rekonditionera 600 rullager från Karlborgs pappersbruk i Kalix, vill man ju inte skeppa ner dem till Göteborg, fixa dem och sedan transportera upp dem igen. Det ideala vore att göra det lokalt. Därmed kommer också de jobb som skapas att finnas i närheten av kunderna.
Distribuerad tillverkning, alltså. Det är en rad spännande tankar som SKF’s CTO radar upp som konsekvenser av vad moderna sensor- och mjukvarubaserad AI-teknologi kan realisera.
– Visionen är att vi kommer att jobba med maskiner som fungerar för alltid, säger Van Camp. Vi ska kunna bygga maskiner tillsammans med våra kunder. Maskiner som inte behöver gå sönder, eller som aldrig behöver ha ett oplanerat stopp. Men det här kräver som jag konstaterade tidigare, nya tänk på flera ställen. De som designar maskiner t ex kanske får fundera mer på att etablera modeller som designas för uppgradering. Lager och lagerhus är ju t ex inte alls designade för uppgradering, som jag nämnde tidigare. Detta är varken mer eller mindre miljötänkande som ligger inom ramen för ett önskvärt affärsmässigt tänkande.
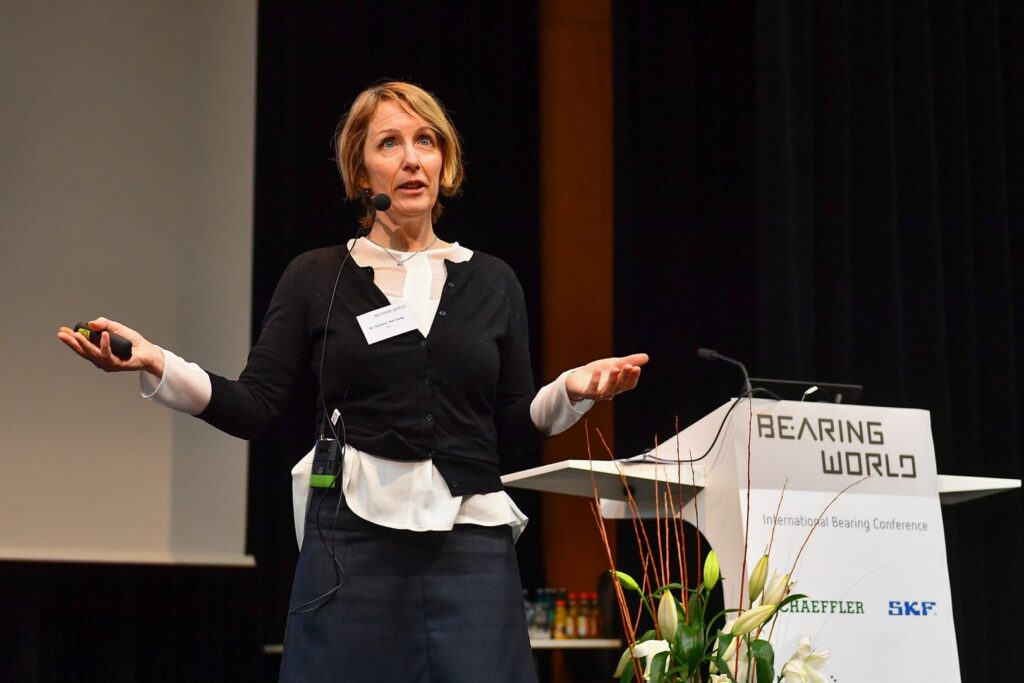
VICTORIA VAN CAMPS ÖVERRASKANDE SVAR
Vad behövs för att möjliggöra de här stora idéerna? Klart är att modern teknologi är ett måste för att kunna hantera den sofistikerade kedja som nu steg för steg byggs upp kring kullagren. PLM-bitarna inom tillverkningen är en självklarhet, men inte bara PLM i största allmänhet, utan lösningar som i varje steg är kopplade, integrerade med nästa steg i produktframtagningskedjan. Från PTC’s CAD-lösningar i Creo, cPDm i Windchill och ”design for manufacturing”, som i sin tur kan kopplas till produktionen via eQube till Siemens automations- och produktionslösningar i Teamcenter/Tecnomatix, OT i Opcenter och annat på tillverkningssidan.
Men att få ut det som PLM-utvecklarna ofta talar om, end-to-end-lösningar, hur är det med den saken? På SKF finns ju idag både PTC (produktutvecklingssidan) och Siemens (tillverknings-, automations- och IoT-områdena), är inte lösningarna från Siemens och PTC användbara i det här sammanhanget?
Victoria Van Camps svar är både intressanta och lite överraskande. Man får en känsla av att hennes syn, som CTO, på den semantiska innebörden av ”end-to-end-begreppet” är en annan än den som PLM-utvecklarna ofta avser med orden. Säger man ”end-to-end” så har det i Van Camps värld verkligen en absolut betydelse. Mjukvarulösningar för allt från A till Ö ska finnas med. Saknas någon länk i kedjan är det inte ett stöd från start till mål, som vi talar om. Medan PLM-utvecklarna troligen lite mer marknadsföringsmässigt och kanske lite slarvigt, med end-to-end avser att de har det mesta som krävs och möjligen bara saknar någon bit här och där, eller i värsta fall en hel domän.
Kanske inte hela kedjan, men i alla fall betydligt mindre än vad SKF avser ska finnas med för att begreppet allt ska täckas in.
VARFÖR KÖPTE SKF AI-UTVECKLAREN PRESENSO?
Man menar kort sagt lite olika saker med begreppet. Ett talande exempel är att SKF och Victoria Van Camp troligen aldrig skulle köpt det israeliska AI-teknologi-företaget Presenso om de kunnat få det israelerna har från PTC eller Siemens. För att hålla maskiner med kullager snurrande behöver man så mycket information, data, som möjligt. Med Presenso, menar SKF’s CTO, fick man AI som kunde knyta ihop, AI som kan få med historiska data, processkontroll-systemets information; data som kontextualiseras och s a s hamnar i rätt fack och som tillsammans med IoT-data kan ge den framförhållning i ”bevakningen” som gör att åtgärdsinsatserna hamnar rätt. Men man fick också ett ledarskap som kan få med folket i produktionen på tåget, vilket Van Camp bedömer vara precis lika viktigt.
Sammantaget faller därmed, i SKF’s ögon, talet om att man har hela kedjan.
– Både ja och nej, mycket finns, men inte så mycket som vi skulle vilja. Både Siemens och PTC är jättebra på mycket, men när man som företag börjar tro att man har ”end-to-end-lösningar” tror jag man är lite fel ute. Ingen har detta. Om man kan inse att man inte har end-to-end, förstår man också värdet och vikten av att samarbeta. ABB’s och SKF’s PLM-team är ett bra exempel på utvecklingen av ett ekosystem och ett samarbete som fungerar. Jag tycker att det i PLM-sammanhanget generellt finns en slags egocentrerad prestige som gör att man tror att man klarar allt, men det gör man inte. Tänk på Apple. Där finns något PLM-världen saknar; någon som tar ansvar för ramverkets kompatibilitet, där de enskilda aktörerna kan s a s ”ta med sig julgranspyntet”. Tillsammans blir detta en fin gran. Även om goda ambitioner finns hos aktörer som PTC och Siemens, så är man inte riktigt där.
”REVIRTÄNKANDET PÅ PLM-SIDAN MÅSTE BORT”
Det Victoria Van Kamp säger är en indikation på att talet som man ofta hör bland utvecklarna, om att det är kundernas svårigheter att skapa vassa affärsmodeller kring den nya tekniken, t ex den IoT-baserade, som är det största hindret mot ett brett genombrott, kanske inte träffar rätt.
– Precis, bra att du säger det, svarar Victoria Van Camp. Vi har en affärsmodell, men den kräver en bredare end-to-end-lösning än vad våra PLM-utvecklare kan erbjuda. De kan inte hjälpa oss med allt från början till slut, helt enkelt. Man behöver vara beredd på att jag kommer med min pusselbit, någon annan kommer med sin, en tredje med sin, tillsammans kan vi få ihop det vi vill ha. Dit måste PLM-utvecklarna och andra komma. Industrin vill att det här ska fungera och samarbete kring och inom ett kompatibelt ramverk är en nyckel till framgång. Revirdiskussionerna måste bort.
Visst, tillägger hon, det funkar med PTC, det funkar med Siemens, men jag skulle önska att de var något mer samarbetsvilliga.
– Men vi har fler system på olika ställen i världen, t ex i Kina, de fungerar där de sitter och att byta dem till våra centrala system har då inget direkt värde. Jag skulle vilja att det fanns en plattform som är så öppen att våra ingenjörer kan fortsätta med det de har och där allt, som i Apple-världen, passar in.
Van Camps uttalanden är intressanta och även stridbara; inte minst i det att egentligen alla aktörer på PLM-banan är intresserade av att få så mycket som möjligt av sina respektive plattformar och lösningar valda.
ÄR APPLE-MODELLEN RÄTT VÄG?
Man kan förstås diskutera om Apple-modellen som helhet är den rätta. Det är den knappast och det är inte så det Van Kamp säger ska tolkas. Apple står för ett av de mest ”låsta” systemen av alla på marknaden. Apple samarbetar med ingen. Allt fungerar tillsammans på Apple för att man måste köpa allt från Apple. Lösningarna är låsta och är proprietära. Bolaget har fullständig kontroll över snart sagt varje hårdvara och mjukvara i sitt ekosystem. Om någon vill lägga en app i Apples appstore kan de göra det om Apple går med på saken, men om de inte gör det kommer din app aldrig kommer att köras på deras appstore. Och om Apple skulle välja att ta in din lösning kommer de att debitera dig 30% av alla intäkter som appen någonsin genererar. Naturligtvis är detta inte en hållbar väg framåt.
Men som sagt, låt oss vara klara över att i Van Camp faktiskt talar om, jag citerar, ”en Apple-liknande” strategi. Det är inte detsamma som att generellt plocka upp hela affärsmodellen. Vad hon letar efter är snarare en liknande men öppen, teknisk plattform.
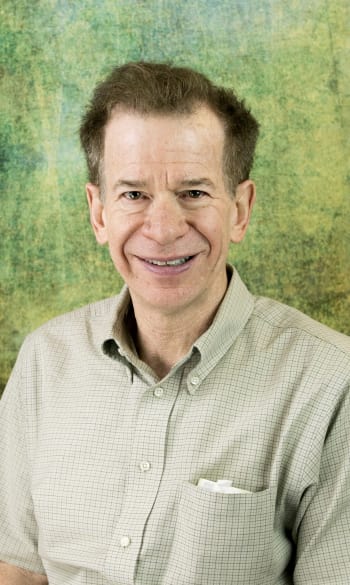
”INGET MAN KAN FÖRVÄNTA SIG,” säger Gartneranalytiker
Vi diskuterade saken också med Marc Halpern, som konstaterar att han inte förväntar sig att PLM-leverantörerna samarbetar över de nivåer som de för närvarande samarbetar. Men här finns ändå bitar i de strategiska mönstren som delvis möter Victoria Van Camps önskemål.
– Ja, på så sätt att jag istället ser PLM-leverantörerna bygga större ekosystem med kompletterande partners, t ex SAP och Siemens, PTC och Rockwell Automation och förmodligen Dassault Systemes och ABB, även om jag i det senare fallet inte har sett mycket material om detta. Men grundställningen är att de alla vill bygga ett större fotavtryck för sig själva och inte nödvändigtvis med sina konkurrenter för att förbättra sina kunder. Jag har i flera år sagt att kunderna måste prioritera öppenhet och tydliga bevis för att leverantörerna tar sådant samarbete med sina konkurrenter på allvar innan de spenderar pengar med någon av leverantörerna. Om inte slutanvändarna gör detta klart för PLM-leverantörerna och agerar därefter kommer Van Camps önskan att förbli som den är – en önskan som har bestått – om än med mycket långsamma framsteg – i minst 30 år redan.
Det ska bli mycket intressant att följa hur det utvecklar sig kring SKF’s CTO’s önskemål här. Klart är att komplexiteten i kravställningarna gör det svårt för en aktör att ta hela paketet.
Mycket talar för det, men att vi detta trots kommer att få se en utveckling mot någon slags gemensamt ramverk, behöver inte vara omöjligt. Att detta är en tuff uppgift behöver ingen tvivla på då det finns en s a s inbyggd motsättning mellan kundernas önskade öppenhet och PLM-utvecklarnas affär.
Men i princip behöver inte detta hindra att allianser mellan oväntade parter kan uppkomma; det är i högsta grad det oväntade samarbetet mellan Siemens och SAP ett bevis på, liksom PTC’s partnerskap med Rockwell. Ett annat exempel är att vi inom automotive ser en rad exempel på kombinationen mellan Siemens PLM-svit, Teamcenter, och Dassault’s CAD-lösning CATIA.
Det finns flera exempel, men till sist landar de ändå i att allianserna än så länge mer får ses som utslag av den ekosystemuppbyggnad som Marc Halpern talar om, snarare än om mer gränsöverskridande ”PLM-to-PLM-samverkan”.