Viktreduktion är en av de bitar man tittar mest intensivt på när man inom automotiveindustrin utvecklar nya fordonsmodeller. Men fordonen ska inte bara bli lättare, utan gärna också mer hållfasta och kanske, med hjälp av nya teknologier, också enklare att tillverka. En lättare bil är generellt mer resurseffektiv när det gäller bränsle och drivsystem, framför allt för att den kräver mindre accelerationskraft än ett tyngre fordon.
Hemligheten bakom att lyckas med detta är en blandning av nya material, materialkombinationer, konstruktions- och tillverkningtekniker. Det är bland annat därför samarbetet mellan Siemens och Bugatti är högintressant. Tillverkare som Bugatti går ofta före med innovationer som pekar i den ovan angivna riktningen; något som förstås också gäller sånt som händer på motorracingssidan i exempelvis Formel 1.
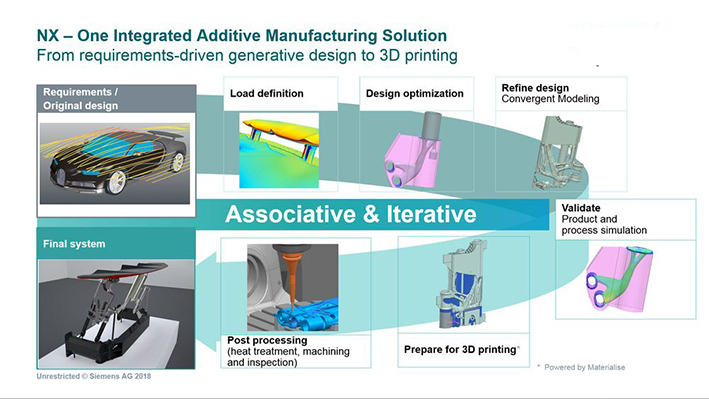
Bioniska ihåliga komponenter. Så vad är det då Bugatti lyckats med i detta projekt? Flera saker, som generellt har bäring på viktreduktion, materialteknik och innovativt konstruktionsarbete:
- Genom att skapa lätta 3D-printade bioniska ihåliga komponenter med hög hållfasthet för det hydrauliska kontrollsystemet av Chironmodellens bakvinge lyckades man minska den totala systemvikten med 50%, samtidigt som den upprätthöll samma styvhet som tidigare.
- Stjärtvingesystemet som konstruerades har specialutvecklade anslutningsstänger gjorda av ultralätta tunnväggiga kolfiberrör, som är 3 gånger starkare än stålstänger av samma dimension, väger en fjärdedel av stålvikten, klarar de höga temperaturerna från fordonets avgaser och är belagda med en keramisk yta för att reducera friktionen.
- De integrerade mjukvaruplattformen för produktutveckling spelade en viktig roll vid systemviktsreduktionen av Bugatti Chiron-vingen.
Detta uppnåddes genom att kombinera 3D-printade titankomponenter, gjorda med hjälp av SLM och kolfiberförstärkta rör.
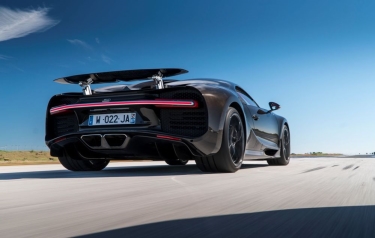
Bugatti Chiron klarar hastigheter kring 400 km/h. Bugatti Chiron klarar – precis som sin föregångare, Veyron – hastigheter en bra bit över 400 km/h. Men medan en Boeing 747 jumbo-jet lättar från marken vid 280 km/h måste Bugattin ligga kvar säkert på marken de här extremt höga hastigheterna, samtidigt som den klarar av höga transversella och longitudiella dynamiska krav. Detta är möjligt genom aktiv styrning av fordonets aerodynamik. Med hjälp av ett sofistikerat hydrauliksystem styrs Chiron höjdläge i förhållande till vägen exakt med hjälp av den ovan nämnda bakre vingen, som justerar och riktar om sin vinkel mot luftströmmarna medan fordonets främre ”diffusorklappar” öppnas och stängs. Detta ger att fordonet konsekvent ”trycks ner” mot marken med jämn kraft. Detta system är unikt i fordonsindustrin och komplexiteten är jämförbar med motsvarande inom luftfartssystem.
Jobbar på en sammanhållen digital plattform. Bugatti har som sagt alltså haft hjälp av digitala verktyg från Siemens genom hela innovationsprocessen; från den virtuella vindtunneln till komponentens ursprungliga design, i en end-to-end-process.
Det finns förstås flera fördelar med att jobba utifrån en sammanhållen digital plattform. Inte minst för att man med en sådan kan undvika tidskrävande och inte sällan felaktiga datatranslationer mellan skilda filformat och problem i samband med ommodelleringar/korrigeringar. Resultaten blir mer exakta och tiden som krävs för att komma till den första komponenten reduceras dramatiskt.
Vi ska också notera att också den virtuella vindtunneln och de virtuella testkörningarna är en del av Siemens fordonstekniklösning, vilket möjliggör ”äktenskapet” mellan den digitala tvillingen för produktutvecklingen och den för tillverkningen. Inom parentes ska här noteras att Siemens PLM skiljer mellan tre ”typer” av digitala tvillingar, relaterat till vad de ska användas för. Genom att använda en tvilling för produktutvecklingen, en för tillverkningen och en för produkten i händerna på slutanvändaren kan man undvika att ”tynga ner” en enda tvilling, som potentiellt skulle kunna hantera alla tre lägen, med onödigt mycket information/data. Därmed blir tvillingarna mer lätthanterliga, är tanken.
Men treenigheten hänger hur som helst associativt ihop och som sagt, simulering är en nyckelfunktion.
– Genom att simulera funktionella prestanda i hela processutvecklingsarbetet med hjälp av en integrerad plattform, från aerodynamik genom en komplex kropp till en additiv tillverkningsprocess för lätta komponenter, får vi en stor fördel när vi strävar efter att driva prestandans gränser framåt för en redan perfekt bil, säger Herr Götzke, chef för ”New Technologies” på Bugatti.
Bugattisamarbetet en del i Siemens ”additiva offensiv”. För Siemens är Bugatti-satsningen också en bit i bolagets senaste offensiv, som går ut på att visa vinsterna med additiv teknik och inspirera företag till att industrialisera den nya teknologin inom ramen för PLM-konceptet. För ändamålet har man inte bara skapat en konceptlösning som handlar om bolagets digitala verktyg och styrka inom automation och industriell rörelsekontroll, utan också bygger på ett leverantörssamarbete inom ett nyskapat nätverk för additiv industrialisering och tillverkning, med spelare som maskintillverkarna Stratasys, EOS och HP, liksom på verkstads- och tillverkningssidan fordonsgiganten Daimler och Siemens Finspångs turbintillverkning, matrialspecialisten Materialise, m fl.
– Ingen aktör klarar nämligen hela detta komplex ensam, säger Andreas Saar, VP för Manufacturing Engineering Software, på Siemens. Vi måste hjälpas åt i ett projekt som handlar om att tänka om hur hela den traditionella produktframtagningsloopen ska gå till. Hur integrerar vi det existerande med det nya? Det handlar om att förändra vårt ingenjörsmässiga tänkande. Men hur gör vi detta? Vårt svar har blivit att skapa dels ett paket med utbildnings- och konsulttjänster och dels att samla bredast tänkbara kompetens inom ramen för ett nätverk, Siemens Manufacturing Network.
Samarbetet med Bugatti kan även det ses i skenet av detta nätverk för att industrialisera additiv tillverkning.
En stark vision. Allt är förstås inte klart, men visionen i upplägget är stark och kommer, när det hela är fullt utbyggt, att bli en konkurrensstärkande faktor för Siemens ambitioner inom digital produktframtagning. I sin förlängning också som en del i tanken att lyckas sluta produktlivcykeln med verktyg som MindSphere.
Siemens additiva initiativ ska också ses i skenet av bolagets senaste initiativ när det gäller digital tillverkning i molnet, med både produktutvecklings-, automations- och tillverkningsverktyg sammankopplade i en kedja. Med detta grepp, Siemens Manufacturing Intelligence, utökar man sitt molnerbjudande med MOM-produktportföljen. MOM, som står för Manufacturing Operations Management, omfattar bolagets mjukvaror för sömlös integration av MES-system och SIMATIC-produkterna.
Missa inte att läsa artikeln om bakgrunden till Siemens PLMs och Digital Factory-divisionens satsning på industrialiseringskoncept kring additivt tillverkning. Klicka på rubriken för att länkas till artikeln: