Mjukvaruteknologin finns, kunnandet finns, maskinerna finns; problemet hittills har dock varit att få ihop hela kedjan. För Siemens additiva PLM-baserade lösning är en pelare i tänket att det krävs ett brett samarbete mellan de olika specialaktörerna inom både additiv och subtraktiv teknik.
– Ingen aktör klarar detta ensam, säger Andreas Saar, VP för Manufacturing Engineering Software inom Siemens. Vi måste hjälpas åt i ett projekt där en bärande del består i att tänka om hur hela den traditionella produktframtagningsloopen ska gå till. Hur integrerar vi det existerande med det nya? Det handlar bl a om att förändra vårt konstruktionsmässiga tänkande. Men hur gör vi detta? Vårt svar har blivit att skapa dels ett paket med utbildnings- och konsulttjänster och dels att samla bredast tänkbara kompetens inom ramen för ett nätverk, Siemens Manufacturing Network. Vi har i detta deltagande av tillverkare, maskin- och materialleverantörer och specialister som Daimler, Stratasys, EOS, HP, Daimler, Materialise m fl, vilka alla bidrar till att realisera konceptet.
Att tänka nytt en jätteutmaning. Här finns hybrida tekniker med mjuk- och hårdvaror, som inom samma bearbetningssekvens kan hantera både subtraktiva och additiva teknologier. Här finns digitala tvillingar, lösningar för generativ design, simuleringsplattformar, inklusive kapabiliteter för topologisk optimering.
Självklart innebär allt detta en stor utmaning, menar Andreas Saar. För att kunna släppa loss kraften och vinsterna i additivt är nytänkade ett måste. Ingen har sagt att det är lätt, men det går: Det är inte första gång ny teknik vänder upp och ner på produktframtagningsprocesserna.
– Visst, inom additivt utvecklas produkterna annorlunda än i de traditionella processerna, säger han. Produkter som tidigare krävde kanske tio eller tjugo delar kan nu göras som en del. Men man får tänka i nya banor vad avser teknik- och konstruktionsupplägg för att kunna utnyttja affärsmöjligheterna i detta. Vårt mål är att erbjuda verktyg som industrialiserar alla involverade processer, från prototyping till tillverkning genom sånt som generativ design, topolgioptimering, lättviktskonstruktion, efterbehandlingsprocesser som innehåller t ex värmebehandling och inspektion.
Allt detta är i Siemens upplägg tänkt att vara ihopkopplat via en digital tråd, driven av digitala tvillingar. I Siemens värld tänker man sig de digitala tvillingarna i tre upplagor för att inte göra en enda tvilling ohanterligt informationstung:
1. En tvilling för själva produkten
2. En för tillverkning av produkten
3. Och slutligen en för produkten hos användaren.
Simulering och topologisk optimering. Sett ur mjukvaru-synvinkel bygger Siemens ”additiva paketering” på Teamcenter som en samlande produktdatabas och ett allmänt process- och produktdata ”backbone”. Här finns också CAD/CAx-systemet NX, som en bas i produktdefinitionsarbetet. Man har i de senaste versionerna implementerat additiva kapabiliteter (AM) i programmet. Men även lösningar för generativ design finns med. Generativt i detta sammanhang betyder att mjukvaran s a s ”själv” skapar en lösning baserat på de mål man satt upp för exempelvis hållfasthet (latticestrukturer), gas- eller vätskeflöden avseende den designade produkten. Det är ju numera så att beräkning och simulering spelar en avgörande roll i det digitala utvecklingsarbetet och för Siemens del är det den sedan ett par år nya Simcenterplattformen det handlar om.
Inom ramen för CAD-lösningen finns vidare i NX topologiska optimeringslösningar. Liksom att man på CAM-området introducerat hybrida kapabiliteter för att styra både uppbyggnad av additiva parter och lösningar för att i samma tillverkningssekvens kunna jobba kombinerat subtraktivt med hybrida fleraxliga maskiner.
Stratasys och Siemens i avancerat samarbetsprojekt. – Utvecklingen är oerhört spännande och produktiv, säger Stratasys Scott Eliason, som PLM&ERP News talade med i samband med Siemens introduktion av det additiva industrialiseringskonceptet.
– Vi har sedan vårt partnerskap med Siemens annonserades 2016 tillsammans tagit additivt till nya nivåer av storskalig kapacitet, fortsätter Eliason. Siemens är mycket starka på generering av verktygsbanor och på automationssidans hård- och mjukvaror när det gäller industriell rörelsekontroll. Vad vi nu gör är att integrera Stratasys avancerade additiva tillverkningsteknologier.
Han pekade i sammanhanget på att man bl a möjliggjort en mycket komplex lösning, Stratasys Robotic Composite 3D Demonstrator, en hybrid multi-axlig lösning, som inkluderar additiva och subtraktiva kapabiliteter och på sista raden också inspektion; allt inom ramen för ett skalbart rörelsebaserat system.
– Här har vi allt som toppmodern produktion inkluderar: Styrka, speed, felxibilitet och konnektivitet, sa en påtagligt entusiastisk Scott Eliason.
Kan man lita på titanblad tillverkade i olika batcher? Stratasys är som sagt också en ”pelare” i Siemens nya Manufacturing Network. Ansvarige för nätverket inom den tyska verkstadsjätten är Robert Meshel och han talade i en presentation om att den bärande tanken är att bygga upp en infrastruktur som krävs för att få fram ett heltäckande ekosystem på området.
– Precis, säger han. Även i detta talar vi om förändring där vi går från leverantörshantering till det bredare begreppet ekosystemhantering. Vi tror på ett diversifierat system som kan lösa problembilder för såväl stora som små företag som vill kunna utnyttja de nya teknologierna. Med nätverket skapar vi ett strömlinjeformad och lätthanterlig process.
I detta menade Meshel att exempelvis reservdelshantering bjuder på spännande perspektiv.
– Digitalisering av detta område är vitalt. Istället för att skicka omkring reservdelar så skickar vi data. Betänk vilka vinster detta kan ge, inte minst i skenet av global access. Man behöver inte vänta på fysiska delar utan kan istället på ett ögonblick ta emot de data som behövs för att 3D-printa, serva eller reparera en produkt. Genom nätverksplattformen får man snabbt tillgång till rätt kompetens, rätta produktdata och rätta tjänster. Allt är baserat på fasta priser baserade på använd volym.
– På sista raden, sammanfattar Meshel, är ett storskaligt industriellt genombrott för additiv teknologi en fråga om tillit. Kan du exempelvis lita på att ett turbinblad i titan håller, som ska ersätta ett annat och som är tillverkat i en annan batch än det första? Finns simuleringsverktygen som behövs för att validera och säkra att ersättningsbladet är av matchande kvalitet? Svaret kan vara en fråga om liv och död…
Hans poäng är att Siemens och bolagets ”additiva” tillverkningsnätverk har det som behövs för att säkra detta.
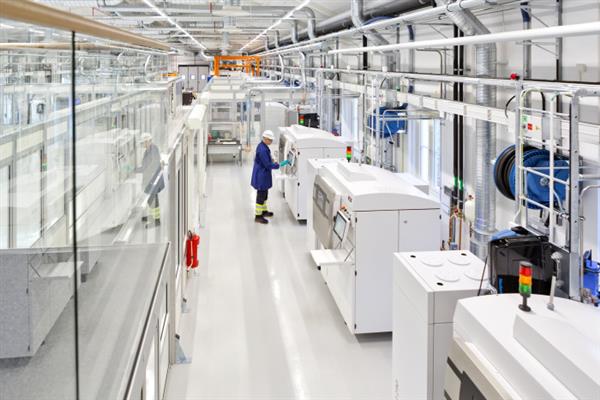
Mer om det goda exemplet i Finspång. I en kommande artikel ska vi titta närmare på turbintillverkning, Finspångcaset, som handlar om just detta med industrialisering av additiv teknik. När bolagets CTO, Vladimir Navrotsky först introducerade tanken, log man lite överseende inom styrelsen som skulle ta beslut om en eventuell satsning. Men Navrotsky gav sig inte så lätt utan jobbade vidare på konceptet och fick med sig styrelsen på en satsning som idag inneburit en rad vinster och fördelar. 2016 invigdes en hel additiv avdelning i Finspång med 20 integrerade EOS-maskiner. Några av vinsterna Navrotsky tog upp var:
* En 30-procentig minskning av växthusgasutsläpp i tillverkningen
* En 65-procentig minskning av resursanvändningen i produktionsprocessen
* En 75-procentig minskning av utvecklingstiden
* Reparationerna går 65 procent snabbare
* Ökning av flexibiliteten när det gäller konstruktion av parter.
* Kortare ledtider.