Centralization of data management and maintenance
In order to be able to optimize maintenance, a common platform is therefore required, where information from all equipment and all assets, regardless of source, is collected. The type of solution in question is an EAM (Enterprise Asset Management) platform and it offers many advantages:
• Removes barriers between different connected processes, such as e.g. between inventory, control of guarantees, purchasing and budgeting, as well as between work schedules, work permits and managing contractors.
• The platform becomes a central point where many data sources of various kinds are gathered, including data from IoT (Internet of Things). Sensors such as wheel impact load detectors WILD (Wheel Impact Load Detectors) can provide a large amount of information and early detect problems with everything from damage and errors in wheel alignment to abnormal temperature increases. The sensors are a great source of information especially when its data feeds a machine learning algorithm and can provide valuable insights.
• Businesses can move from traditional maintenance (error-fixing, scheduled and preventive) towards efficient, data-driven strategies including condition-based and predictive maintenance.
• Major rail operators using HxGN EAM, a leading enterprise asset management platform, use data and machine learning algorithms to predict equipment failures and provide real-time decision support. It can reduce equipment downtime by 30-50% and increase equipment life by as much as 20-40%.
• Operators and businesses with responsibility for maintenance (Entities in Charge of Maintenance ECM) use the platform as a central repository for compliance with full traceability of maintenance activities.
• New ways of working that lead to increased productivity are made possible. Repetitive administrative tasks can be automated, schedules can be optimized according to available resources, and with specially developed mobile applications, field personnel can easily access detailed information about the equipment.
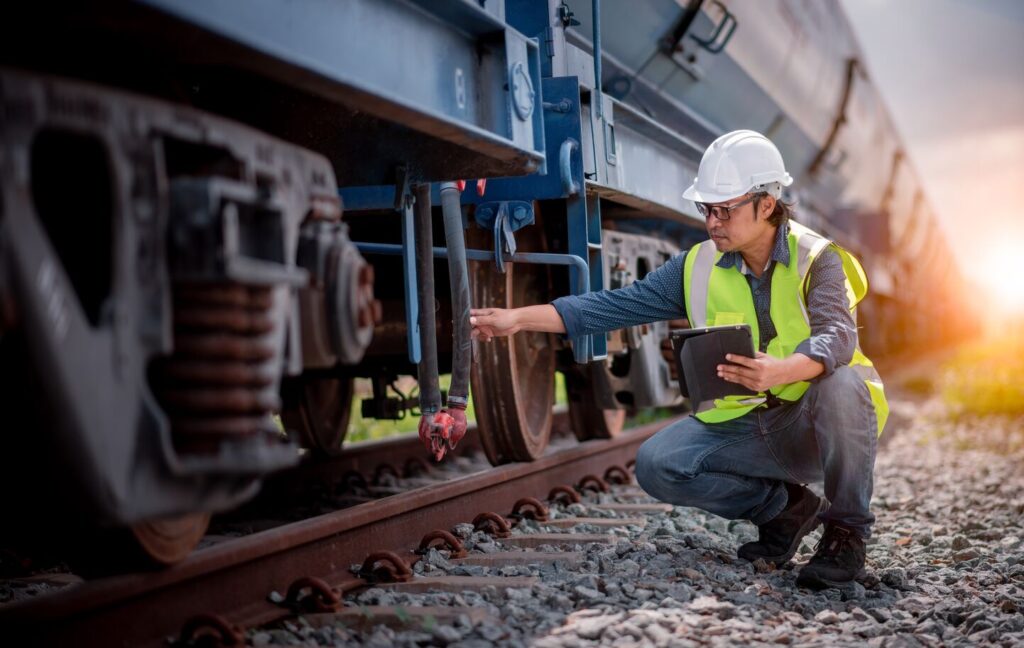
Makes the entire life cycle visible
A centralization of all data related to operation and maintenance, throughout the system’s life cycle, can lead to large efficiency gains.
The Swiss Stadler Rail Group is a global leader in the manufacture of both rack-and-pinion and high-speed trains such as SMI LE, capable of speeds of up to 250 km/h. As the privatization of regional rail transport increased around the world, they saw the opportunity to expand into rail vehicle maintenance. This is an industry with strict compliance requirements, which is also constantly changing, and where there is a lot of money to be made from effective warranty management.
Stadler uses HxGN EAM to document and track all maintenance activities. This means they can define a completely new train fleet and all its maintenance activities in a single system. For Stadler, which both manufactures and maintains trains, this provides enormous advantages in the form of being able to follow the equipment throughout its entire life cycle. Stadler is certified as Entity of Charge of Maintenance, according to EU regulations.
Asset Performance Management – an important step
Data can do even more: as competition among train operators increases, more and more are using advanced software to manage their maintenance strategies. This includes asset investment planning (AIP) and asset performance management (APM), platforms that relate maintenance to finances.
Hexagon’s recently launched platform HxGN APM for asset performance management, helps transport companies optimize maintenance and thus reduce unplanned downtime.
The platform uses an advanced analysis and optimization engine that constantly assesses the risk of a failure occurring and adapts maintenance, inspections and monitoring activities to the asset’s actual condition and criticality. Companies can thus focus their resources where they do the most good.
Asset Investment Planning (AIP) builds on the same way of thinking and optimizes investments and decisions about which is most economically beneficial, to repair or buy new. Both strategies are essential for efficient rail traffic where the cost of maintenance is very high and can easily destroy profitability.
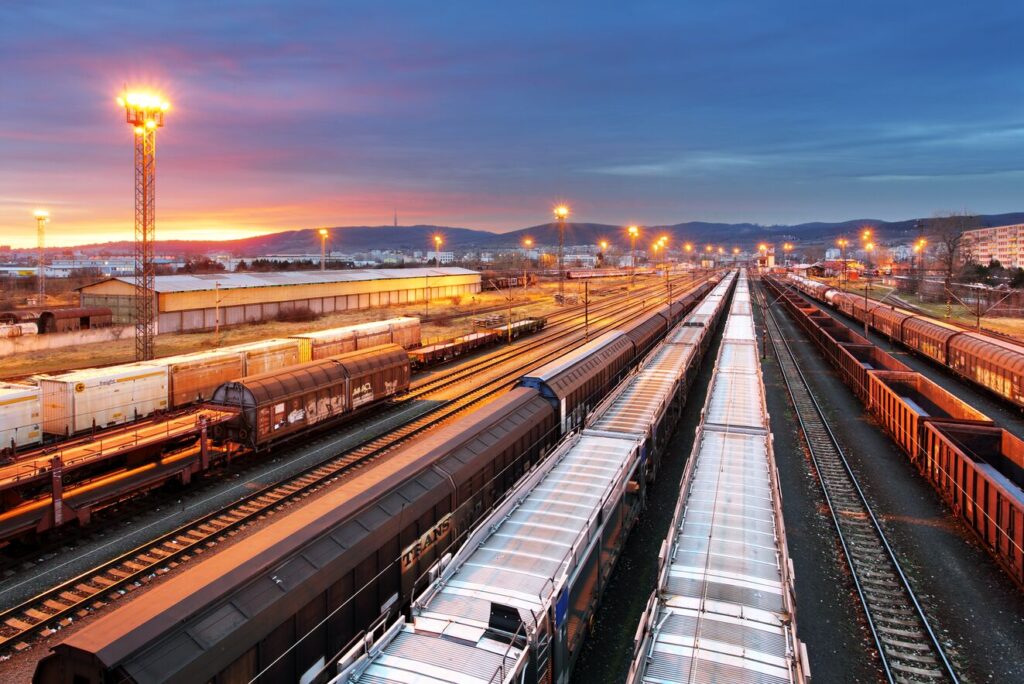
The benefits are extensive. In continental Europe, the average lifetime of rail passenger vehicles is 33 years. With modern digital tools, they can extend the life of their assets and thereby improve overall profitability.
As demands increase to do more for less money, they can optimize maintenance, take the right steps to ensure that errors do not occur and thus avoid unplanned downtime.
Through the insight into how long it is profitable to continue maintaining the assets, they can also free up capital for new investments.