Den affärsdeal som låg bakom var ett avtal annonserat i augusti 2020 om att integrera Volvo Bussar Indiens verksamhet i VECV, som i sin tur är också är ett delägt dotterbolag till den större indiska Eicher-koncernen. VECVs uppgift i detta är huvudsakligen att täcka viss tillverkning – t ex karosseri-produktionen, montering, distribution och försäljning av Volvo Bussar i Indien.
– Till bakgrunden hör att vår chef då, Olaf Tellefsen, hade varit i kontakt med Eurostep vid tidigare tillfällen och tyckte att ShareAspace kunde vara en väl fungerande lösning för uppdraget, säger Jörgen Ohlsson och tillägger att man efter detta tog ett uppstartsmöte med Eurostep.
– Vid detta tillfälle hade vi egentligen bara en uppfattning om delar av projektet, men ju mer man trängde in i detaljerna och utmaningarna relaterade till detta, desto mer växte omfattningen av det som skulle göras. Samtidigt hade vi en begränsad tidsintervall på 3 månader för projekt-genomförandet.
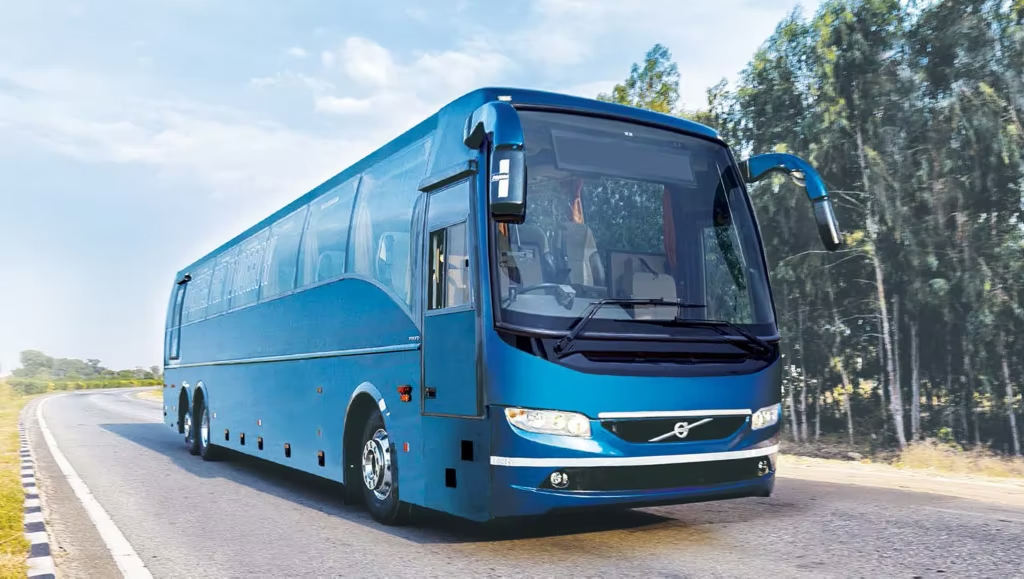
Projektet startade i början av 2020 och involverade då ca 12-14 medarbetare.
– Den kommersiella bakgrunden var alltså att det indiska joint venture-bolaget VECV skulle ta över produktionen av busskarosser som Volvo producerade. Chassierna producerades, och produceras, dock fortfarande av Volvo, men sen bygger man ju på med en kaross, vilken nu alltså skulle göras i Indien.
I princip var det hur som helst kaross-produktionen det nya företaget skulle ta över.
– Det stämmer, men sen ville VECV också vidareutveckla chassit för att det skulle anpassas till deras modell, vilket bl a handlade om att i förlängningen hålla nere kostnader och möta deras indiska partners förutsättningar.
Från CATIA V5 till V6-versionen
Att överföra informationspaket av den här magnituden aktualiserar förstås vilka digitala verktyg man har, hur man anpassar formaten till varandra och hur man avgränsat kan hämta all karossdata från olika källor.
– Först ska sägas att vi på Volvo gjort likande saker förut. Men då överfördes informationen över disketter, som fick flygas ner till de som skulle ha dem. Idag är det förstås annorlunda och det finns avsevärda skillnader i hur man med dagens teknologier och kommunikationsmöjligheter kan lägga upp detta på ett strukturerat sätt. Klart är emellertid att de skulle ha mycket information. CAD-bitarna förstås, plus strukturer och det strukturella upplägget gällande leveransen av artikeldata. Vi hade och har möjlighet att göra detta själva, men inte på den nivå som kontraktet stipulerade att det skulle göras när projektet drogs igång.
Noteras här kan att kaross-CAD-data producerats i Dassault Systemes CATIA. Dessa lade man upp i ett antal Zip-filer med CATIA-data för den aktuella produkten.
– VECV är ett företag som tillhör Eicher-koncernen, som levererar bussar, och som köpte bolaget. Bakgrunden är att det finns ett högt varumärkes-värde på marknaden där att tillverka och leverera Volvobussar. Hur som helst jobbade och jobbar man i detta bolag med just CATIA, vilket under lättade överföringen av data. Men här fanns verisionsskillnader i det att vi på Volvo hade, CATIA V5, medan indierna jobbade i V6-versionen. Detta krävde vissa adaptioner för överföring av V5 till V6 för att filerna skulle kunna tas emot i läsbart skick, men detta löstes av våra datatekniker och Eurosteps medarbetare på ett bra sätt. Men förutsättningarna i kontraktet var att vi skulle leverera i V5-versionen.
Vad fick hämtas ur KOLA?
Detta med CATIA är nu en sak, en annan än mer betydelsefull och känslig är sånt som skulle/ska hämtas i Volvos produktdatasbas och PDM-system KOLA. Detta system är ”lag” på Volvo och inget man gå in och ut ur hur som helst i det att det innehåller bolagets intellektuella kapital (IP).
– I KOLA finns exempelvis data om vad det är som finns på vagnen, att man sen får gå in och hämta CATIA-data är en annan sak.
Vilka data är det som hämtats eller kan hämtas i detta projekt?
– CATIA-data och relevanta strukturdata i KOLA i första vändan, absolut. Men det tar inte slut där, vi har ju en plattform och i denna finns en del som framgent kan komma att innehålla förändringar som berör projektet. T ex designändringar som förekommer av olika utvecklingsskäl, som produktförbättringar i chassit. Här har vi dels en skyldighet att meddela VECV att detta skett och de måste förstås också kunna få tillgång till dessa förändringar. Då får de titta på relaterade bitar i KOLA, ta del av förändringarna för att kunna anpassa sin karossprodukt efter dessa. Men det är dedicerade personer och för dem relevant dedicerade områden de får gå in och titta på.
En chassi-förändring kan påverka karossens utförande och anpassningar kan alltså behövas.
– Ja, det kan ju vara så att de inte vill ha några av oss adderade komponenter, utan istället införskaffar liknande lösningar lokalt. Detta kräver att man kan ändra i både chassi och kaross för att anpassa dem. Det är de här informationstyperna de får.
– Men det finns också relaterade data som vi inte delar med dem, t ex simulerings- och analys-data. Det är unik Volvo-egendom som det ligger mycket tid och kraft investerat i. Däremot kan de ju själva utföra simuleringar de vill ha.
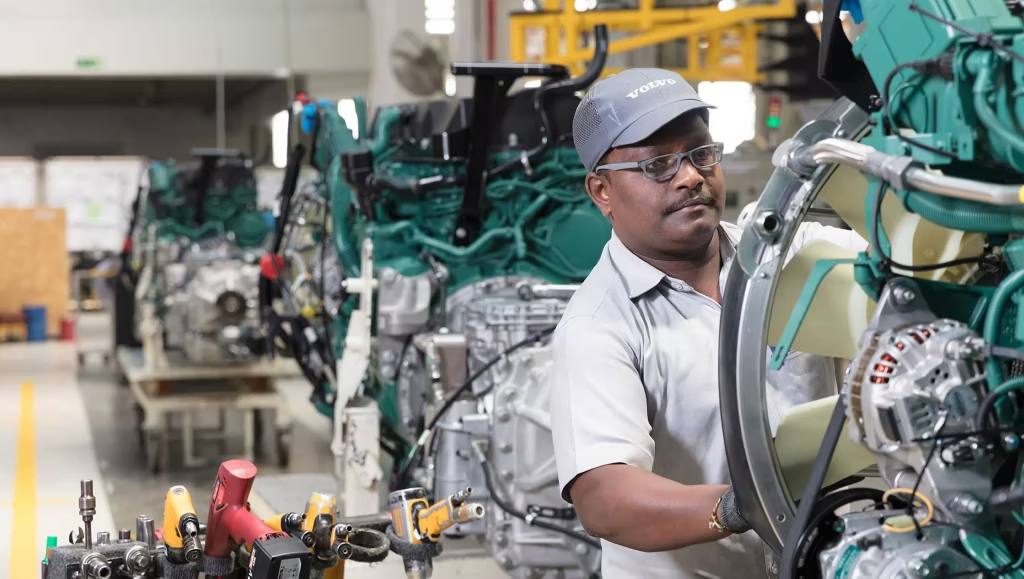
Vilka har varit de tuffaste tekniska utmaningarna?
– Eurostep och ShareAspace-plattformen har varit och är betydelsefullt i projektet. Men det är också mycket data som de kunde få in i ShareAspace, data som VECV egentligen inte behövde. Så här fick vi gå in och göra begränsningar. Det fanns också data som ShareAspace inte hade innan, som vi fick lägga till i lösningen. Det var utmaningarna på ShareAspace-sidan.
– Sen hade vi också en del diskussioner om hur vi skulle lagra informationen om vad som har delats enligt avtalet, vilket kan behövas i en eventuell framtida diskussion: Skulle det göras i molnet, eller skulle vi lägga det elektroniskt på vår dataserver och på ShareAspace?
Detta mynnade hur som helst ut att vi la det i ett moln.
– Från Volvos sida hade vi i tillägg till ovanstående diskussion också funderingar kring hur vi skulle leverera CAD-data och ritningarna. Här tog vi hjälp av vår IT-support, som hjälpte till med att samla ihop data på ett sätt som gjorde att ShareAspace kunde ta emot dem för vidare leverans till VECV.
Jörgen Ohlsson summerar projektet med att konstatera att ShareAspace i sin funktion som datavalv eller hub fungerat mycket bra.
– Man tar in data, ”manglar” till den lite grann för att sedan kunna leverera den vias molnet enligt kundens önskemål.