In many ways, the collaboration between the parties in this case marks a new era in personalized medicine. The collaboration has helped redefine personalized medicine, integrating digital thread technology to create personalized solutions that support effective soft tissue ingrowth. For patients facing complex bone cancers, this marks a new dawn – one where innovative technology meets compassionate healthcare. It is as Dr. Solomon Dadia of the Tel Aviv Sourasky Medical Center, says: ”Bioactive printed implants are the future of implants.”
How did it all happen? We will take a closer look at the matter in today’s article.
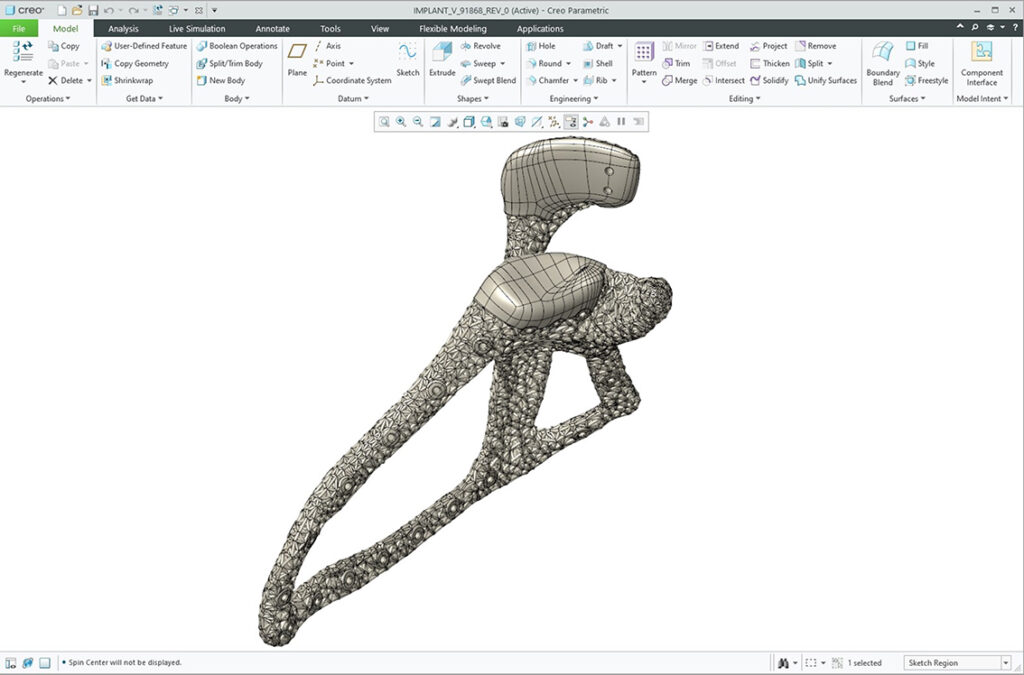
The team chose a new path
The patient was initially treated with chemotherapy to shrink the tumor, but a complete scapula removal, or shoulder blade operation, remained a necessity. Facing an operation that could have left the patient without shoulder function, the team chose a different path: they wanted to design and implant a custom 3D-printed titanium scapula, designed to reflect the patient’s unique anatomy. This approach would not only restore mobility but also help redefine future treatment protocol for complex skeletal operations.
But moving forward required a series of trade-offs and involved parameters. What did the requirements picture look like? Significant implant design challenges included:
• Preservation of the patient’s original anatomical volume, shape and kinematics.
• Optimizing the implant’s mechanical properties while minimizing weight.
• Provision of an optimal set of anchorage points for muscle attachment.
• Implementation of an advanced lattice structure to facilitate ingrowth of connective tissue and muscle, leveraging Creo Design for metal additive manufacturing to minimize support and distortion.
• Introduction of minimal surfaces to ensure smooth joint kinematics.
• Use of advanced mechanical simulations to verify the bearing capacity of the implant for shoulder and arm movements.
• Ensure manufacturability and reduce implant print attempts, leveraging Simufact Additive to simulate and compensate for the thermomechanical processes that distort parts as they are printed.
• Verify successful print quality for certification, leverage VGSTUDIO MAX to process CT scan data and verify the quality of the complex structure and properties of the printed metal.
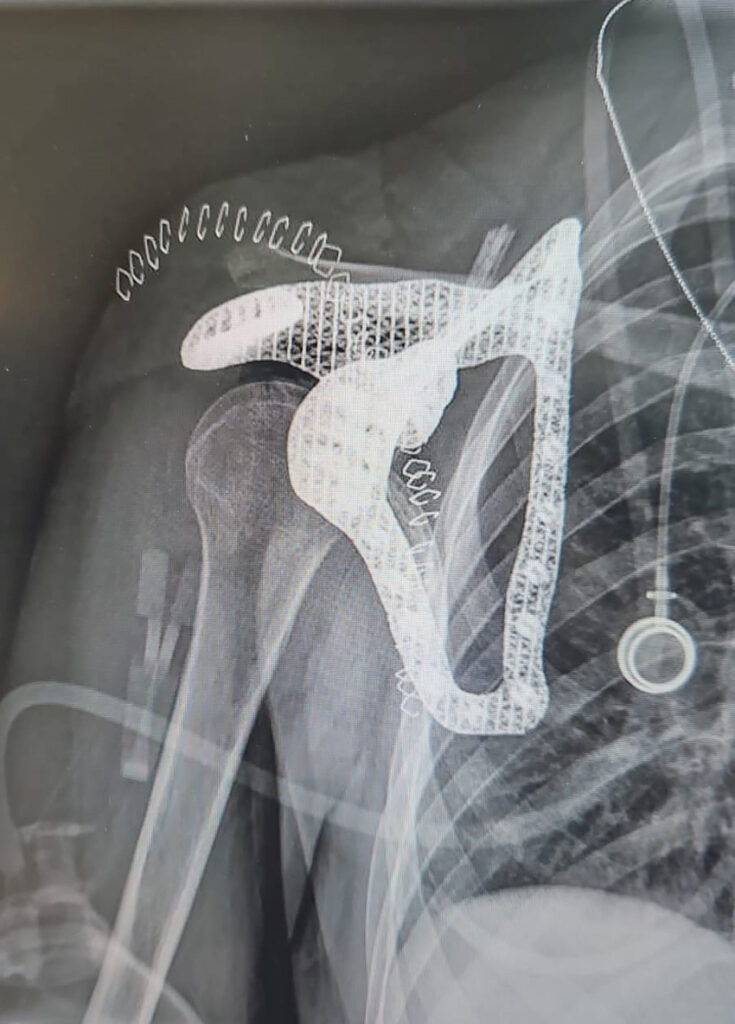
Milestone-level surgery
As can be seen from the above, this project required immense precision to meet the complexity of the problem, and the team needed to find a way to achieve an ideal balance between anatomical, medical, engineering, manufacturing and certification constraints.
Given this, the team advanced to surgery with the personalized implant that seamlessly fit into the patient’s anatomy. The precision-fit part, thus produced through CAD design in Creo and with Hexagon’s certification tools, played a critical role in the patient’s rapid recovery, allowing her to begin regaining mobility within days – a testament to the technical excellence embedded in the implant. Today, the patient progresses through rehabilitation, with restored function and improved quality of life.
“The development of complex implantable 3D printed materials, together with powerful additive manufacturing and simulation software, enables us to introduce smart implants to the surgical world. These implants interact with tissues to optimize their survival in the body, ensuring a perfect fit and promoting tissue growth. These advances mark a new era in personalized medicine,” sums up Dr. Solomon Dadia.
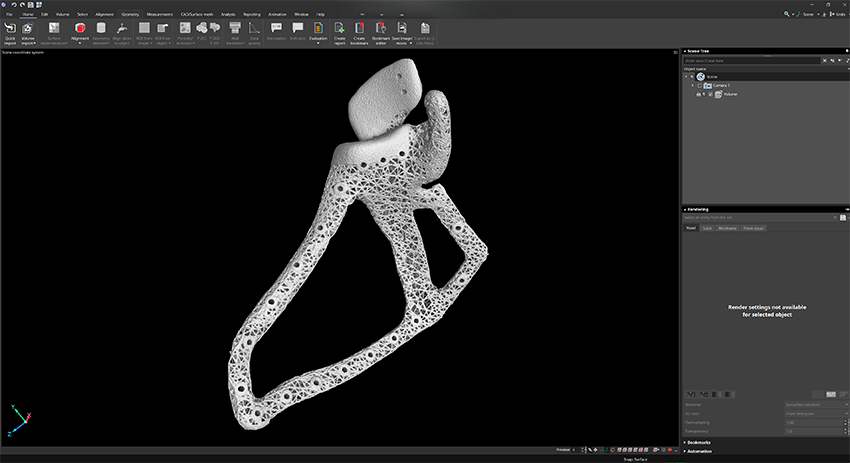
About the partners
• Tel Aviv Medical Center: Leader in patient-centered care, setting the bar for cutting-edge surgical techniques.
• PTC: Leader in PLM and digital transformation, enabling breakthroughs in personalized medical solutions.
• Hexagon: Ensures safe, certified medical advances, drives rapid delivery of high-quality components using a digital twin to predict and improve manufacturing processes.
In conclusion, the power of Creo’s additive manufacturing design tools and high-level simulations have created a successful case. Under the supervision of experts from the Tel Aviv Medical Center, the completely personalized scapular implant was produced and certified using technology from Hexagon – all of which contributed to the patient’s rapid recovery and restored mobility.