Klart är att den tyska fordonsjätten i högsta grad befinner sig i utvecklingens framkant när världens fordonsflottor elektrifieras eller ”hybridifieras”. Bolaget krigar ständigt om den globala tätplatsen – i hård kamp med framför allt Toyota, men också Renault-Nissan-Mitsubishi-kombinationen – när det gäller vilket bilmärke som säljer flest fordon per år. Var och en av dessa automotivespelare säljer drygt 10 miljoner bilar per år. Det är alltså stora värden som står på spel när världens bilpark ska transformeras till i huvudsak elbaserad drift.
DRAMATISKT FÖRÄNDRAD utvecklings- och tillverkningsprocess
Men eldrift i kombination med online-uppkopplade fordon betyder inte bara förändrad konsumtion av energislag, från fossilt till eldrivet, utan också en dramatiskt omdanad produktutvecklings- och tillverkningsprocess. Vi går från ett läge där mekanikinnehållet minskar, medan elektronik och mjukvaruinnehållet ökar. Detta kommer också att speglas i nya behov när det gäller kompetens och den digitala verktygsarsenalen – vid sidan av, förstås, förändrad produktframtagningsmetodik – där framför allt PLM/cPDm, simulering, mjukvaru- och tillverkningsintegration (OT, Operativ Teknik) växer i betydelse och användning. Det hela blir lätt synnerligen komplext.
PLM&ERP News ska i dagens artikel titta allmänt på Volkswagens PLM-upplägg och det nya ”Industrial Cloud”, som lanserades under fjolåret. Vi har också tittat närmare på ett simulerings-case, som berör Volkswagens fabrik i tyska Kassel. Denna anläggning är specialiserad på utveckling, planering och produktion av elektriska enheter och dagligen färdigställer man 150 elektriska och 300 hybriddrivna bilar. Men när det gäller den första ID.3-modellen så är det VW’s anläggning i Zwickau som producerat dem.
På PLM-sidan är Siemens Teamcenter huvudlösning, med Dassault’s CATIA som CAD-program. I ”Industrial Cloud-upplägget” är Amazon Web Services en huvudkomponent, Siemens IoT-operativ MindSphere en annan. Men precis som alla stora OEM’s inom automotive använder man sig av en rad andra mjukvaror. Svenska COMSOL Multiphysics är en sådan lösning, som spelar en viktig roll när det gäller simulering i samband med utveckling av elmotorer. Vi ska återkomma till detta senare i artikeln, men först lite om hur kontexten runt dessa digitala verktyg ser ut.
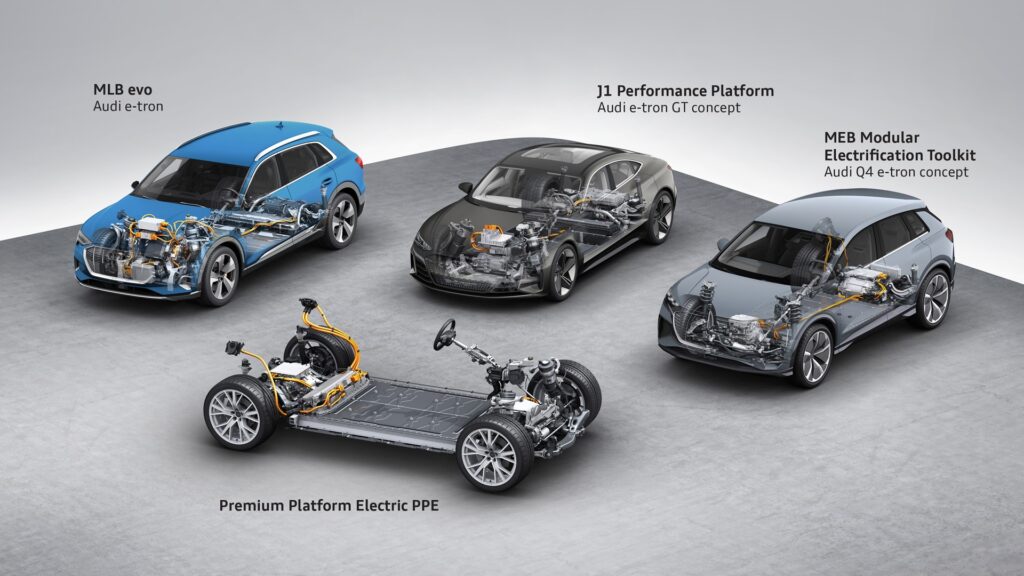
Volkswagens MEB-plattform I FOKUS
En intressant aspekt på modern produktframtagning inom automotive är ”plattformiseringen” som en grund för designarbetet inom ett eller flera modellprogram. I Sverige har vi Geelys produktutvecklingsbolag CEVT, som bl a levererar plattformar till Volvo Cars, som ett närliggande exempel. Men man är inte ensamma om detta. Flera fordonsbolag jobbar i samma spår och Volkswagen är som sagt ett av dessa.
Volkswagen Group har utvecklat fyra modulära plattformar för att stödja elbilar över hela sin portfölj av varumärken. Några av dessa kommer man att öppna upp för konkurrenter eller andra tillverkare att använda, för att sprida kostnaderna för att införa elektrifiering. En av dessa, MEB-plattformen för små och medelstora mainstream-bilar, debuterade i september 2019 i form av Volkswagen ID.3. Plattformen kommer vidare att delas med Ford i en affär som meddelades i juli samma år.
VWs andra EV-plattformar, du ser dem på bilden ovan, är designade för framför allt premiumbilar och kan också delas med konkurrerande biltillverkare, särskilt PPE-plattformen som utvecklas av Audi och Porsche för medelstora och stora bilar. PPE-plattformen debuterar 2021, troligtvis i Porsches nästa generations Macan, vilket bekräftats vara en EV.
Optimerar enskilda komponenter och systemet som helhet
Bolagets MEB-plattform utvecklades med start 2015 med målsättningen att bli en rationell grund kring utvecklingen av elfordonen. Det handlar om ett modulsystem (MEB står för ”Modularer E-Antriebs-Baukasten“ på tyska; ”Modular Electric Propulsion Platform” på engelska) som är uppbyggt för att optimera EV-designen (Electrical Vehicle) och effektivisera tillverkningsprocessen. MEB-funktionaliteten omfattar t ex sånt som vridmoment, kraft och hastighet för huvudhjulsdrift och för valfri framhjulsdrift, som används i versioner av fyrhjulsdrift.
Bland andra krav, som förhållanden för axlar, drivenheter, vikt och hjulbas, spelar utformningen och placeringen av högspänningsdrivbatteriet en viktig roll i det övergripande MEB-konceptet. Medan MEB hjälper till att optimera enskilda komponenter och systemet som helhet, tar balansering av dessa krav noggrann hänsyn till designerns arbete, särskilt när man jobbar kring ny teknik som digitalisering, autonom körning och elektriska enheter.
Totalt planerar Volkswagen-koncernen att investera nästan 44 miljarder euro i elektrifiering, digitalisering, mobilitetstjänster och autonom körning fram till 2023, varav 30 miljarder euro är öronmärkta för e-mobilitet enbart.
Före år 2025 förväntas elektriska fordon stå för cirka en fjärdedel av modellportföljen. MEB-plattformen spelar alltså en nyckelroll i satsningen.
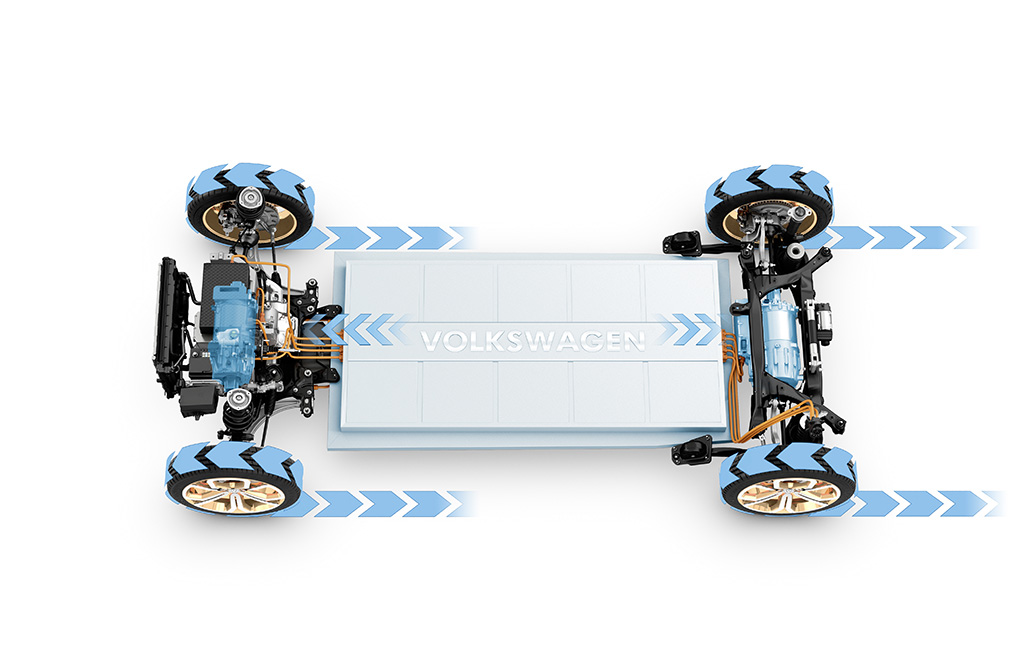
MASSIVA MJUKVARUPROBLEM med nya ID.3:an
Att den tyska biltillverkaren satsar på elfordon är inga dagsfärska nyheter. Affärsplanen, ”Tillsammans – Strategi 2025”, inkluderade 30 nya elmotordrivna bilmodeller fram till 2025. Med MEB-plattformen som grund blir det alltså en rad varianter på elbilsmodeller: I.D. Concept, I.D. Buzz, I.D. Crozz och I.D. Vizzion. ID.3 var, som nämnts ovan, först ut på plattformen i november ifjol.
Men all vår början bliver svår. Plattformens första ”batch” av ID.3-bilar har enligt tyska tidningsrapporter drabbats av massiva mjukvaruproblem. I samband med produktion av den första ”batchen” rapporterade i december tyska Manager Magazine att Volkswagen hade de här problemen på mjukvarusidan. Enligt rapporten kommer ID.3, ”att byggas i månader med en ofullständig programvaruarkitektur, som kan påverka upp till 20 000 elbilar. Dessa enheter, avsedda för försäljning i Europa och inte USA, kommer att kräva en manuell programuppdatering.”
Enligt andra rapporter har tusentals ID3-bilar parkerats i dedikerade hyrda utrymmen tills man, enligt kalkylerna, under våren skulle försöka få rätsida på problematiken.
Ny programvara med en ny arkitektur installeras, enligt dessa planer, manuellt i de första 10 000 ID.3-orna. Totalt ska mer än 20 000 ID.3:or alltså omarbetas när det gäller mjukvaruarkitekturen. Tanken är fortsättningsvis att man ska kunna uppdatera mjukvaran via ”luften”/nätet. Något som t ex Tesla gör i dagsläget.
I slutet av februari berättade källor inifrån Volkswagen att orsaken till mjukvaruproblemen var att programvarans grundarkitektur hade utvecklats ”för snabbt”, vilket resulterade i att många delar av systemet inte samarbetade effektivt, vilket i sin tur ledde till funktionsbortfall.
Totalt har VW tvingats till programfixningar på 20 000 ID.3-fordon till den andra produktionsvågen, som var tänkt att starta i maj. Vid den tiden ska ytterligare programuppdateringar kunna distribueras över luften, men det är i dagsläget oklart hur Coronapandemin påverkat tidsplanerna.
Första bilen på MEB-arkitekturen
ID.3 är den första EV som använder Volkswagens modulära MEB-arkitektur och produktionen av ID3 startade, som nämnts ovan, i november 2019.
Allmänt när det gäller dessa plattformar talar man idag inom bilindustrin om två eller flera ”strukturella” principer kring elektriska plattformar:
- Dels ett lågt s k ”skateboard” för traditionella bilar
- Dels ett högt ”skateboard” för SUVar
Ordet ”skateboard” används här som en liknelse som illustrerar utseendet på en fordonsplattform som de vi diskuterat ovan. De ser kort sagt ut som gigantiska skateboards, vilka i de senare utvecklingsprogrammen ”kläs upp” i olika skruder i form av varierande karosserier, interiörer och instrumentpaneler, e t c.
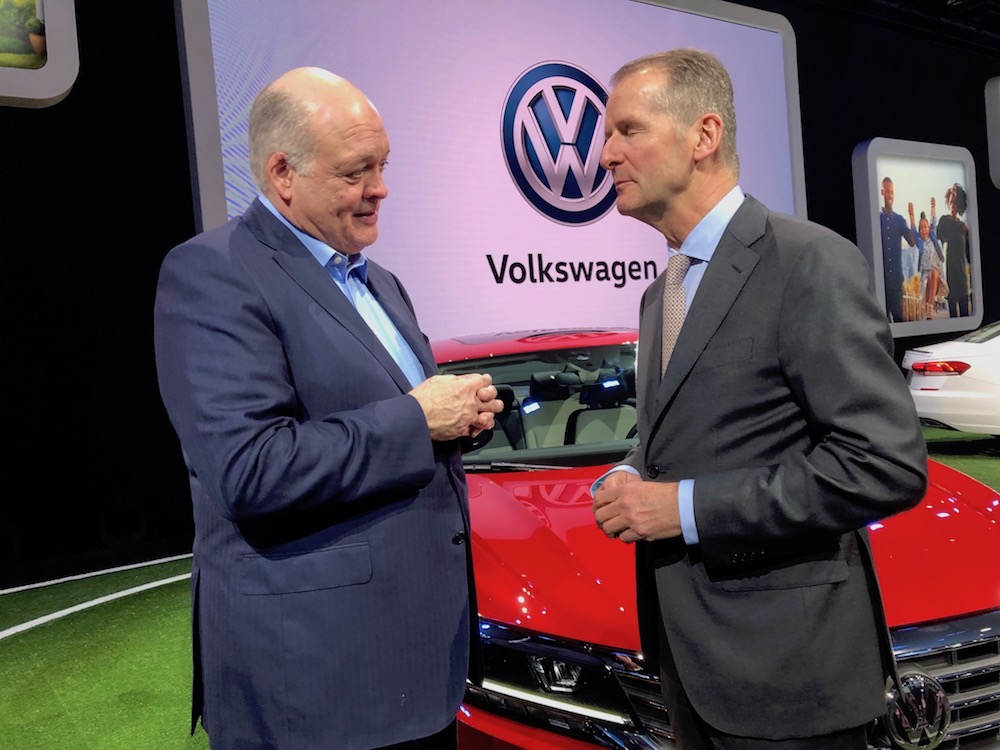
Ett gemensamt drag när dessa ”skateboards” tas fram är att man vill de ska packas så effektivt som möjligt med batterier för att kunna tillhandahålla så mycket energi som möjligt.
Volkswagen har vidare fr o m november 2018 också planerat MEB-plattformen efter just två varianter: en för personbilar och en för nyttofordon och tyngre last, den senare följaktligen med större batteri.
Plattformen är som sagt också tillgänglig för upphandling av andra, t o m konkurrerande tillverkare. I samband med detta kan noteras att Ford har ett strategiskt partnerskap med Volkswagen för MEB-plattformen för att dra nytta av stordriftsfördelarna. Ford planerar att bygga MEB-bilar år 2023.
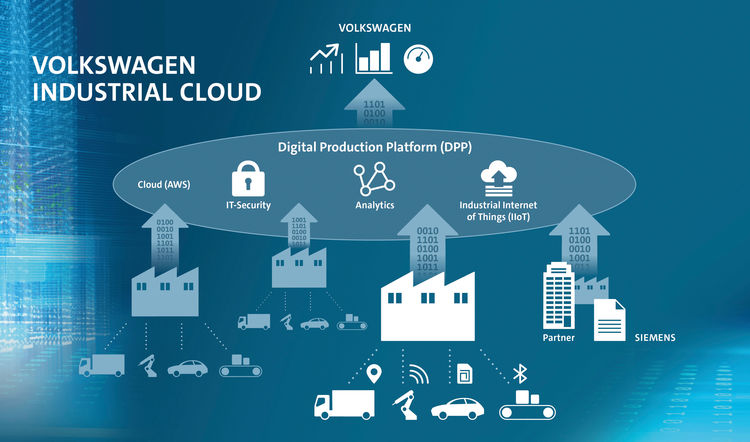
Siemens TEAMCENTER är VWs digitala backbone
När det gäller PLM-lösningar så jobbar Volkswagen med Siemens Teamcenter som produktdatabackbone och på CAD-sidan är det Dassault Systemes CATIA som är huvudsystem.
Allmänt så har VW idag tagit sikte på att knyta ihop sina 122 tillverkningsanläggningar över hela världen med vad man kallar ett ”Industrial Cloud”. I september förra året stod det också klart att den tyska biltillverkaren tänker konsolidera all information till detta molnbaserade system.
En primär VW-partner inom Industrial Cloud är vidare Amazon Web Services (AWS), som ordnar med kopplingarna till Siemens Teamcenter-plattform och ”ovanför” detta skapar det virtuella system som ska hantera VW’s produktionsdata över hela världen. Detta upplägg kommer att göra det möjligt att konsolidera all produktions- och lagerplanering under ett system, detta emedan det idag finns flera IT-system, som används på olika fabriker runt om i världen.
Projektet ska så småningom koppla ihop bilproducentens hela globala leveranskedja, som inkluderar 1 500 leverantörer och partners på över
30 000 platser.
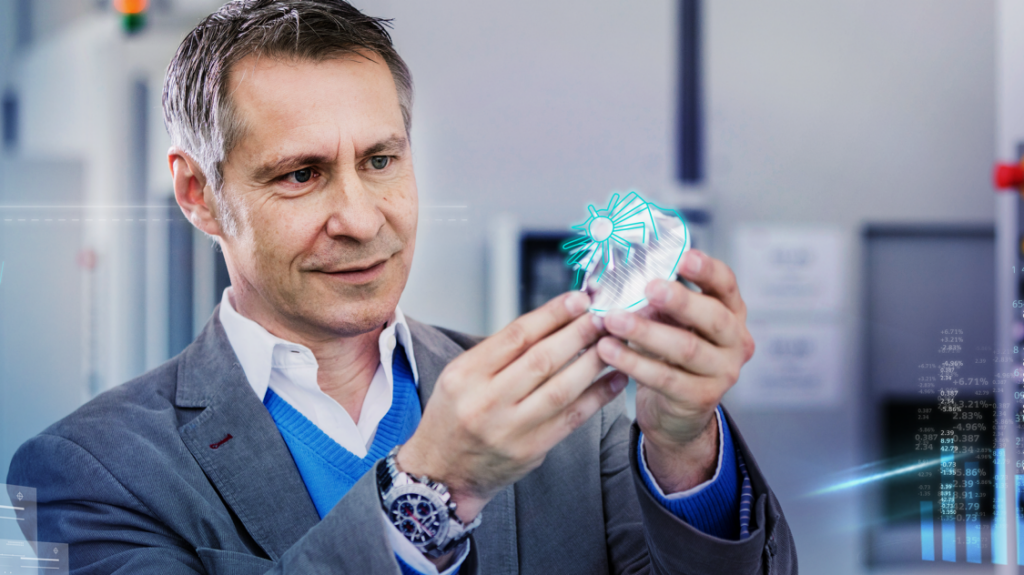
MindSphere kopplar ihop 122 FABRIKER
via AWS och Volkswagens nya INDUSTRIAL CLOUD
En viktig bit i Industrial Cloud är Siemens IoT-operativsystem MindSphere.
VWs användning av MindSphere går ut på att koppla ihop och styra maskiner och utrustning på de 122 fabrikerna. Poängen med MindSphere är just detta: att inom ramen för IoT och teknik för industriell automation koppla de fysiska maskinerna till AWS-molnet. Fördelarna är flera men en vanligt åberopad är att man med hjälp av MindSphere-tekniken kan man jobba med prediktiva analyser för att t ex proaktivt kunna förutsäga när maskiner kommer att behöva underhåll och schemalägga drift och service i enlighet därmed för att optimera produktionen.
Volkswagens industriella moln handlar alltså om att vässa produktionseffektiviteten och flexibiliteten. Kombinationen av och tillgången på data från alla anläggningar ger nya möjligheter för processoptimering, inkluderat effektivare kontroll av materialflöde, tidig upptäckt och eliminering av leveransflaskhalsar, process-störningar och optimerad drift av maskiner och utrustning.
Dessutom är den molnbaserade plattformen, med dess förenklade datautbyte, en förutsättning för att Volkswagen ska tillhandahålla ny teknik och innovationer, t ex kring eldrift, snabbt och på olika platser. Vi talar i detta om sånt som smart robotik och dataanalysfunktioner för att analysera och kontrollera processer på verkstadsgolvet, från anläggning till anläggning. Med den molnbaserade plattformen kan nya applikationer skalas upp direkt till alla platser i hela världen.
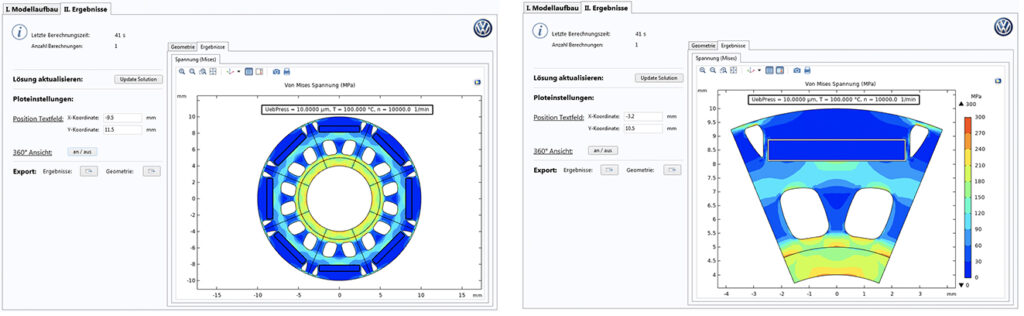
Varför COMSOL-mjukvara?
Så där ser alltså PLM- och produktionsbakgrunden ut på VW. Men det hindrar nu inte att Volkswagen, precis som alla stora OEM’s har behov av och använder mer specifikt kompetenta lösningar för särskilt tuffa problem. COMSOL’s Multiphysics är ett bra exempel.
– Ja, säger bolagets CTO, Ed Fontes. Vår mjukvara har traditionellt använts vid centrala FoU-avdelningar, både vad gäller motorer och batterier för elektromotoriska applikationer.
Vad är det som gör att man väljer en COMSOL-lösning?
– Förmågan att kunna formulera egna ekvationer och att specificera material som funktioner av beroende variabler har varit nyckelfunktionen, förklarar Fontes och fortsätter: ”Att kunna skapa dedikerade användargränssnitt, som är lätta att använda för forskare och ingenjörer, har dock öppnat för avdelningar utanför FoU att utnyttja vår mjukvara. Detta har skett gradvis under de senaste två-tre åren. Dessa forskare och ingenjörer är inte alltid simuleringsspecialister, men med simuleringsapplikationer kan de också dra nytta av multifysikmodeller med hög exakthet för elmotorer och batterier.”
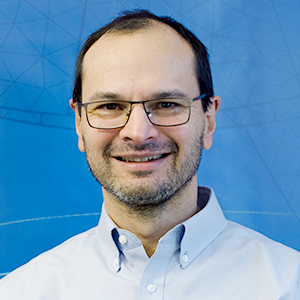
Detta med att man börjat nå utanför de traditionella användargrupperna är en spännande utveckling inom ett område som normalt betraktats som svårt och komplext. Hemligheten, i den mån man kan tala om en sådan, heter Application Builder och COMSOL Server. Dessa lösningar som kom för ett par år sedan har bidragit till att den svenska programutvecklaren har närmare 200 000 användare. Lösningarna används alltså för att göra avancerade multifysiksimuleringar tillgängliga för en bredare publik. Genom Application Builder och Server kan simuleringsspecialister skapa lättanvända och skräddarsydda grafiska gränssnitt (simuleringsapplikationer) som baseras på modeller byggda i den Multiphysics-mjukvaran.
De specialiserade analysverktygen sprids sedan med COMSOL Server. Administratörer har full kontroll över vem som ska ha behörighet till simuleringsapplikationerna. Den snabba och skalbara processen gör att företag kan sprida simuleringsapplikationer på minuter till den globala organisationen.
– Alla, från designingenjörer till tekniska säljare kan med de här verktygen bli effektivare när de kan utföra eller titta på simuleringar med Multiphysics-programmet från en mobiltelefon eller surfplatta, säger Ed Fontes.
Från COMSOL’s CASE BOOK:
Simulering av rotorers hållbarhet på VW Kassel
De här lösningarna faller alltså in under en av de senaste årens tydligaste trender: Enkelhet i användningen, som underlättar kollaborativt utvecklingsarbete.
Man har sedan lång tid tillbaka inom automotive talat om just detta för att täcka behovet av effektiv samverkan i produktframtagningsarbetet. I fallet med Kasselanläggningens utvecklingsarbete är detta redan ett faktum. Man har idag en process kring eldriftslösningar, som från utvecklingsprocessens start präglas av nära samarbete mellan alla som är involverade i design, simulering och testning.
Simuleringsbiten är en väsentlig del av denna process och det är här COMSOL’s Multiphysics-lösning kommer in i handlingen: Som viktiga komponenter i elektriska drivenheter måste rotorer testas för hållbarhet, eftersom de måste tåla ett mycket stort antal varv med varierande hastighet och vridmoment under körningen. Det är dock tidskrävande att utvärdera styrkan hos rotorlamineringarna. Detta har VW Kassel tagit sig runt genom att automatisera denna testprocess för rotorer. Resultatet är minskade utvecklingskostnader och ökad produktkvalitet genom att bygga simuleringsapplikationer med Multiphysics-mjukvaran.
Lite schematiskt ser det ut så här, som det beskrivs av Thomas Forrister på COMSOL’s sajt:
Först granskar simuleringsexperter prestandaspecifikationerna för en elektrisk enhet. Man använder simulering för att undersöka hur man bäst kan komma till den önskade designen. Till exempel genom att modellera frekvensomriktaren för att minska antalet varianter kraftigt. Genom att distribuera en simuleringsapplikation baserad på denna modell blir det möjligt för designers att i nästa skede jämföra olika varianter och välja den bästa.
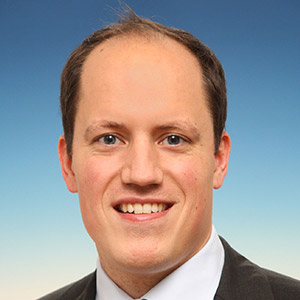
Detta samarbete är viktigt och gynnsamt för alla, eftersom simulering inte kan täcka alla verkliga frågor. Testprocessen spelar därför en viktig roll i utvecklingsprocessen. Dessutom hjälper det experimentella testförfarandet att förbättra simuleringsmodellerna.
– I utvecklingsprocessen för elektriska maskiner måste man uppfylla många krav, förklarar dr Steffen Rothe, simuleringsingenjör för komponentutveckling på VW Kassel. Å ena sidan måste maskinen matcha de elektriska kraven för vridmoment och effekt. Å andra sidan måste rotorn ha en viss hållbarhet, där centrifugalkraften är den största belastningen för rotorn.
”UTMANADE KRAV”
Går vi vidare kan balansering av dubbla krav vara utmanande, eftersom de ibland är osynkade. Även om det är bättre att använda tunna strukturer för de elektromagnetiska kraven, är tjockare strukturer att föredra för mekanisk hållbarhet. Det är viktigt att dessa krav möts tidigt i utvecklingsprocessen. Ett sätt att göra det effektivt är att simulera alla lastfall som täcker kraven.
– Simulering, kommenterar Rothe, spelar en viktig roll för att påskynda designprocessen. Många industriella simuleringsprogram är designade som en ”svart låda”, medan Multiphysics är unik i sin transparens. Det gör det möjligt för användare att se och modifiera de implementerade ekvationerna, eller till och med lägga till sina egna.
Han tillägger att programvaran dessutom är utformad som, ”ett multifysikverktyg från början och gör det möjligt för användare att simulera olika fysiska fält samtidigt. Därför kan användaren kombinera olika fysiska fält för att göra något helt nytt.”
Att analysera komplexa fysiska problem som dessa kan dock vara utmanande, även för en simuleringsexpert. Teamet behövde ett sätt att kommunicera med kollegor och göra det möjligt för icke-experter i mekaniska simuleringar att testa vissa parametrar. Formgivarna kunde tillgodose dessa behov genom att använda Application Builder, för att skapa simuleringsapplikationer som förutsäger spänningarna i en rotor.
Konklusionen är att VW Kassel påskyndar designprocessen för elmotorer genom att bygga och distribuera simuleringsapplikationer som utvärderar styrkan hos rotorlamineringar.
Det är ett gott betyg för den svenska programutvecklarens kapacitet att skapa lösningar i världsklass och som kan bryta de riktigt stora utvecklarnas dominans.
LÄS MER OM COMSOL-CASET genom att klicka på följande länk: https://www.comsol.se/story/simulation-applications-streamline-the-development-of-electric-vehicle-motors-80591
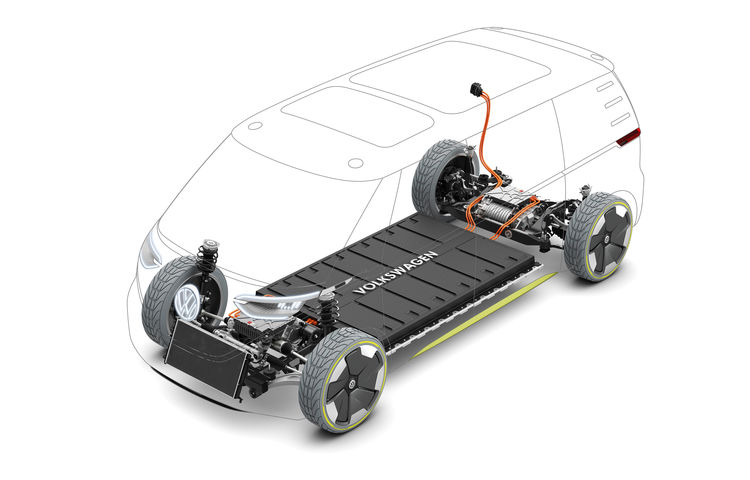
NÅGRA SLUTSATSER – tillfälligt bakslag på vägen mot framgång
All förändring av invanda utvecklingsprocesser har sitt pris och få områden är så komplexa att förändra som fordonsutveckling som involverar tusentals deltagare i utvecklingsarbetet. Särskilt tufft blir det om förändringen, som i fallet med elbilsutveckling, är djupgående, involverar nya verktyg, krav på nya kompetenser och ny utvecklingsmetodik. MEB-plattformen och VW’s nya Industrial Cloud är givetvis inget undantag.
Det är heller i sak inte så märkvärdigt på rent principiell nivå att mjukvaruproblemen med ID.3-modellen – den första på MEB-plattformen – i ett första skede får lösas manuellt för att senare kunna åtgärdas, eller uppdateras via luften, ”nätet”. Om man sedan ens vid något tillfälle i en modern produkts liv kan tala om att den är helt klar kan möjligen vara något av en filosofisk fråga. Att uppdatera mjukvaror via nätet är ju en kapacitet som är en naturlig del i ett dynamiskt utvecklingsflöde kring en produkt. Tesla gör det exempelvis och ingen påstår i detta att Tesla är en ”ofärdig produkt”.
Man skulle snarare kunna betrakta möjligheten att uppgradera en produkt via ”luften” som en rätt fantastisk möjlighet att vässa den. Självklart är funktionsbortfall inget som kan accepteras, men rent principiellt är funktionsuppgradering av mjukvaror via nätet en utmärkt möjlighet.
På sista raden – Volkswagen är absolut på rätt väg i sitt upplägg med PLM kopplat till Industrial Cloud för att få ihop en vassare och optimerad produktframtagningskedja. Barnsjukdomar tillhör utvecklingsdynamiken. Slutbetyget – om man kan tala om ett sådant i en dynamisk process – är beroende av hur och att man löser eventuella relaterade problem.
Med Siemens och AWS som partners är utsikterna för vassa plattformslösningar goda. Min konklusion är att Siemens när det gäller verktyg för en sant integrerad, komplett produktframtagningsprocess där PLM, IT och OT – liksom senare IoT-lösningar som kopplar ihop slutanvändarna med fordonsutvecklarna – kommit längst av alla.