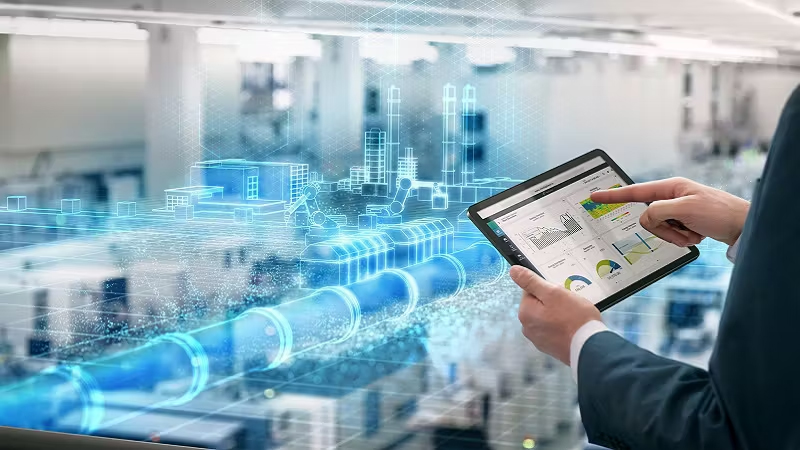
As companies focus on managing each of these pressures, the industrial landscape can appear chaotic. Many companies have responded to this chaotic landscape in a disorganized manner. The first reaction has most often been to seek out digital tools to gain advantages in product development, production design and operation, management of information, supply chain dynamics, and more. But these adoptions have often been piecemeal or uncoordinated. While these tools can offer benefits in isolation, their true transformation advantages cannot be unlocked without a broader strategy. Moreover, digital transformation takes more than expanding one’s digital toolbox.
Looking ahead to 2025, I’d like to refocus on the fundamental reasons why companies should pursue digital transformation and explore the full scope of what digital transformation entails. For the coming year and beyond, it will be critical to remember that tools are not enough in the absence of appropriate processes and talented people with ample support.
Navigating the digital transformation journey
It is first important to recognize that digital transformation is a marathon, requiring investment, commitment, and some patience. Digital transformation, as with any long-term project, starts with a plan and a strategy for executing the various phases of the plan. In general, it can be useful to outline the plan around specific goals, measurable targets, and key pain points in current processes that should be addressed as part of the digital transformation.
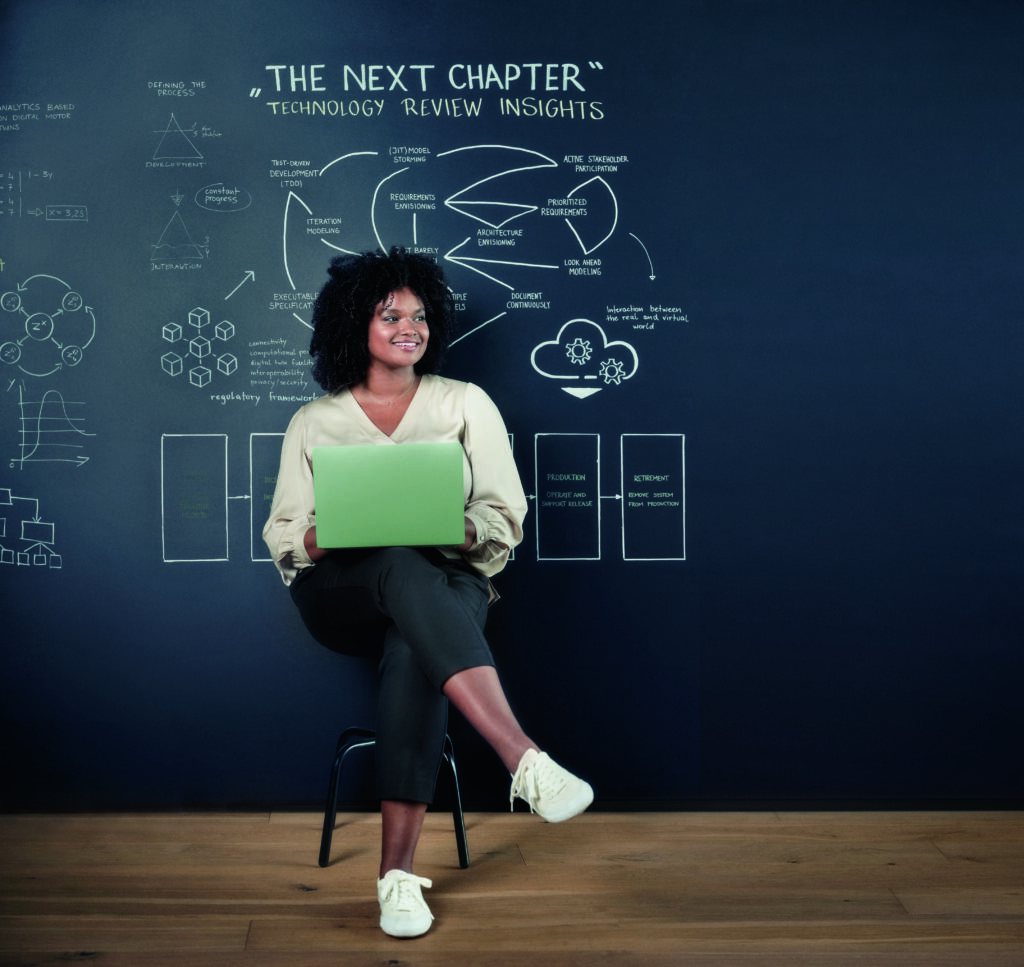
There are several additional considerations that can help guide the finer details of planning a digital transformation:
- How to ensure compliance with a growing number of regulations and avoid penalties?
- Can departments be stretched to develop more internal competencies? Or would it make more sense to partner with suppliers to augment existing capabilities?
- Where can digital technologies provide the greatest value, and how can processes be improved to maximize the investment?
- How can technology empower the people behind the processes? What kind of support may people require?
The final point in the above list demands elaboration. Digital transformation entails organizational change. Organizations, ultimately, are collections of people connected by structures and processes, and empowered by technology. Therefore, the success of a digital transformation program depends on more than just the technology. A successful digital transformation program must account for the structural and cultural shifts that will occur with the adoption of digital technologies and re-architect processes to support the new digitalized ecosystem.
In the past, many companies reacted to uncertainty and disruption by purchasing point tools to solve urgent problems without addressing broader limitations. As a result, many of these companies never invested time or effort into understanding their new tool(s) or determining how processes needed to be updated to flatten the learning curve and extract the most value out of the investment. Moreover, simply investing in the digitalization of processes without intention or strategy risks leaving employees behind as they attempt to learn new skills or adapt to new methods of completing tasks.
Instead, the digital transformation of an organization requires a holistic approach. Once a new tool has been identified that can drive a transformation in a process, the process needs to be optimized or redefined to take advantage of that tool, especially in cases where cross-domain connectivity and collaboration will increase. Perhaps most important, users of new solutions and processes need educational support and a forum to offer feedback and improvements that will help maximize the results of the transformation. These details can be outlined in the digital transformation plan.
Digitalization then expands throughout the company by repeating this activity: strategic implementation of new tools and processes and user education to accelerate adoption. Approaching a digital transformation strategy in this way ensures that users adopt a new technology and process with confidence and can deploy new capabilities to great effect.
Building around the comprehensive digital twin
With the blueprint for digital transformation in place, the next step is to lay the foundation. At Siemens, we believe the technological foundation of a successful digital transformation is the construction of a comprehensive digital twin. A digital twin, at its most basic, is a physics-based digital representation of an asset or process, a virtual copy of a physical or soon-to-be physical thing.
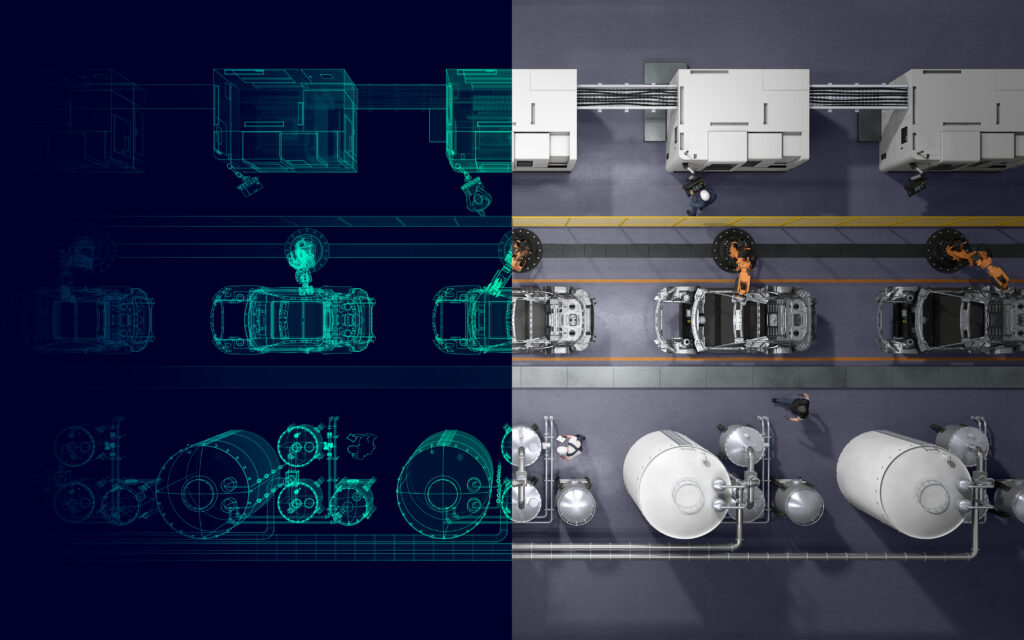
The digital twin helps define and optimize products and production systems, thus significantly reducing the need for physical prototypes during development, saving valuable resources. The digital twin updates to reflect any change to its physical counterpart throughout the product lifecycle, creating a closed loop of feedback between the virtual and real environments. This enables companies to continuously optimize their products, production and supply chain processes at minimal cost.
To be comprehensive, a physics-based digital twin must incorporate all product domains: mechanical, electronics, electrical systems, software, and connect with manufacturing to fully capture today’s smart products and processes. A comprehensive digital twin comprises a set of consistent digital models representing different aspects that can be used throughout the entire product and production lifecycle and the supply chain.
The comprehensive digital twin enables the seamless integration of the product and production lifecycles, including software and automation. It allows manufacturing companies to design, simulate, test, improve and validate products with the digital twin, including mechanics, multiphysics, electronics and software. All of this can be achieved in a virtual environment using robust simulation tools to enhance the quality of the product or process while shortening the overall design cycle.
Enable a shift-left with the comprehensive digital twin
As companies build towards and upon a comprehensive digital twin, they can shift key activities earlier in the development lifecycle of a new product, manufacturing system, service offering, or internal business process. Critically, a shift-left of engineering, design, costing, and other analytical activities produces valuable information and insight earlier in the lifecycle where it is easier and less costly to act on, and where it can drive the greatest improvement at the end of the lifecycle. This creates outsized value in reduced cost, faster development, and an optimized product at program completion.
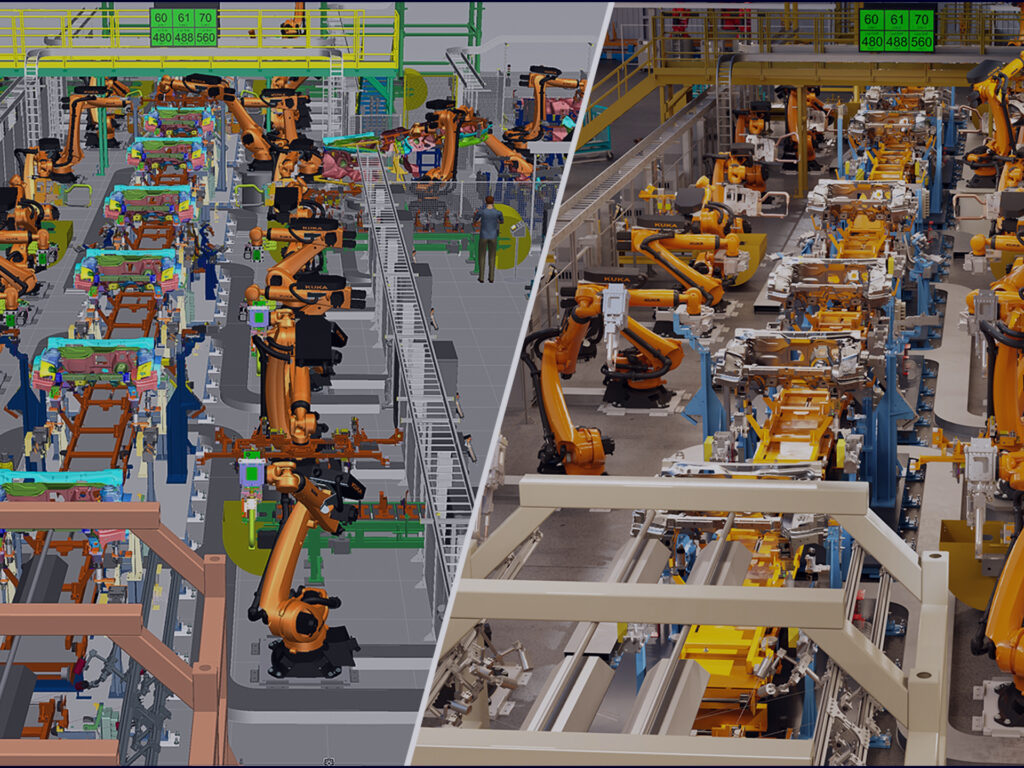
When it comes to a complex modern product, such as a car or aircraft, the shift-left of digitalization enables engineers to integrate design requirements across domains and perform testing and validation earlier using virtual product or system models rather than physical prototypes. Virtual testing, verification, and validation of system designs can root out integration issues across domains, provide early performance estimates, and drive design optimization all with the advantages of speed and relatively low cost that come with working in the virtual world.
In my time working as an engineer and project lead in the aerospace industry, such a shift-left would have been transformative. In aircraft development, it is often the airframe that matures earliest while other systems like the hydraulics and electrical systems reach maturity later in development. Early in the program, the teams responsible for the airframe would try to reserve space in the frame for hydraulic lines and wiring bundles, but these allowances were made based on best guesses and information that would soon become outdated. The result was costly and time-consuming re-work of airframes already in production to accommodate larger wiring bundles or changes to the hydraulic systems.
Digitalization and the comprehensive digital twin offer companies the opportunity to uncover and address such issues before they become expensive and burdensome late in development. A shift-left of analytical processes also supports greater optimization of products, manufacturing processes, or supply chains to meet increasingly rigorous performance, reliability, cost, and sustainability requirements.
Prepare for emerging technologies with digital transformation
A well-founded digital transformation strategy built on the comprehensive digital twin also prepares a company to quickly integrate emerging technologies into processes to gain further advantages. Industrial artificial intelligence (AI), and the industrial metaverse (IMv) are already on the horizon, promising distinct advantages to companies that can take advantage of their powerful capabilities.
Digital transformation unlocks data from throughout the organization, making data streams accessible to key decision-makers from the shop floor up to the executive suite, and across engineering and business domains. In other words, digital transformation empowers companies to collect and synthesize data from throughout the product and production lifecycle. This offers both greater transparency throughout the product and production lifecycle and the perfect ecosystem to integrate industrial AI and IMv applications.
Industrial AI will be critical to increasing the processing speed and throughput of data, which will enable accelerated product and process evaluation and innovation. Today, industrial AI can help automate mundane tasks, leaving engineers more time to focus on solving design challenges. AI can also help users learn new tools by learning command patterns and offering new commands based on contextual cues. Some companies have leveraged this technology to capture the patterns of experienced employees to help train new hires.
The industrial metaverse is the next stage in the evolution of digital transformation, combining the comprehensive digital twin, AI, and software-defined automation to create an intuitive and collaborative virtual environment built on precise real-world data. The IMv will also act as a single-pane-of-glass behind which all lifecycle data is collected, orchestrated, and displayed for review or manipulation.

The IMv, for example, can be applied to the operation and management of production assets in the real world. Modern production machines are highly automated and connected, and the Industrial metaverse can help operators manage and maintain these machines more effectively. Sensors on a machine may trigger a vibration warning, which prompts further investigation from the machine operator. The operator can directly review the digital twin of the machine, contact a process expert to review the machine program, and examine the setup of the actual machine all within the IMv to uncover the root of the issue.
With industrial AI, the IMv may also persistently monitor production activities during a given period, produce reports, and detect and diagnose issues automatically. Such early identification of anomalous behavior, whether by an industrial AI or by the machine operator, allows proactive problem identification, leading to fewer unplanned breakdowns and increased uptime.
Invest for the future with a holistic digital transformation journey
Major pressures across industries are set to continue in 2025. Companies are navigating an increase in the cost, complexity, and pace of innovation in new products and manufacturing systems. Rapid changes in global sustainability regulations and requirements, and fierce competition for talent in key areas only make the task of fostering success more difficult.
These simultaneous pressures combine to create an industrial landscape that feels chaotic, changing quickly and without warning. Companies know that technology can help them make sense of the chaos but often fail to approach digitalization with a sufficiently comprehensive scope. As a result, powerful solutions and technologies are adopted as point solutions, leading to confusion, frustration, and sub-optimal performance as users attempt to adapt to the change.
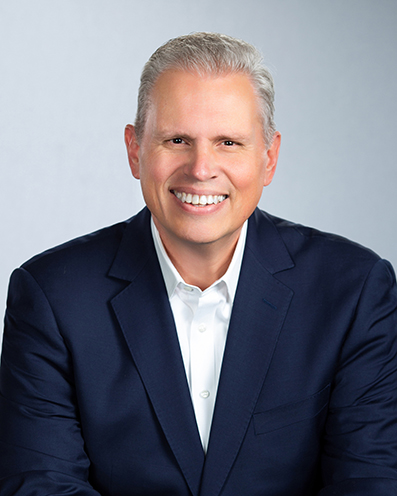
Our instinct is to act in response to chaos. But, when it comes to building for the future of industry, it is critical that we respond first by analyzing the situation, second by making a plan, and third by executing that plan. True digital transformation is a long-term endeavor that will deliver powerful advantages to companies that adopt technologies in key areas, reassess or rebuild related processes, and provide clear information and support to the people affected. Such an approach will mean the difference in the coming years between companies stuck chasing trends and those that surge ahead of the competition.
By Dale Tutt
VP of Global Industry Strategy
Siemens Digital Industries Software