Renault- och Geelys AUROBAY slår två flugor i en smäll med SIMCENTER 3D – MINSKAR SIMULERINGSTIDEN med 88%.
Aurobay är ett intressant, men inte så ofta omskrivet bolag inom automotive-segmentet. Med rötterna i Volvo Cars Powertrain Engineering utvecklar och tillverkar man drivlinor för den globala marknaden. Aurobay knoppades 2021 av efter en deal mellan Volvo Cars och dess moderbolag Geely Holding om att skapa detta samriskbolag för sin drivline-verksamhet. För drygt ett år sedan blev bolaget sedan en del av ett nytt globalt företag, gemensamt ägt av Renault och Geely. Detta företag har i dagsläget runt 19 000 anställda, fördelat på 17 fabriker och 5 forsknings- och utvecklingscenter i Asien, Amerika och Europa. Verksamheten är inriktad på att utveckla och tillverka hybriddrivlinor och drivlinor med låga utsläpp. Bland de bitar som ingår i detta är validering av prestanda, hållbarhet och funktionalitet hos olika drivlinedesigner.
Det här är inga enkla saker utan kräver högt utvecklad kompetens och digitala PLM-verktyg på toppnivå. Bara genom designen av en ny drivlinekomponent kan testningen, kalibreringen och diagnostikutvecklingen som krävs för att få den i produktion vara synnerligen resurs- och tidskrävande. Det är bl a i detta Aurobay kommer in i handlingen med en komplett analys- och verifieringstjänst för att testa och validera drivlinornas prestanda och funktionalitet, med både fysiska och virtuella tester. Man kombinerar i detta teknik i världsklass, högpresterande beräkningar och statistiska analyser för att ta designen till nästa steg. Detta inkluderar att ta hänsyn till tillverkningsteknik och att säkerställa att kraven på bränsleeffektivitet, utsläpp och NVH (buller- och vibrationsmätning) uppfylls.
Det är i det senare sub-PLM-området, simulering och analys, dagens artikel rör sig, närmare bestämt då på NVH-biten. Då Aurobay har specialiserat sig på utveckling av både förbrännings- och hybridmotorer finns betydande ekonomiska och tekniska utmaningar, vilket också är kopplat till NVH-sidan.
För att motverka detta letar Aurobay efter mjukvaruverktyg som kan användas för båda disciplinerna. Detta innebär att inköp inte behöver göras två gånger, och ingenjörer kan växla mellan hybrid- och förbränningsmotor-projekt utan att behöva lära sig hur man använder nya verktyg. Samma verktyg för båda alltså. Efter noggrann utvärdering har man hittat en intressant väg där Siemens Digital Industries Softwares simulerings- och analys-plattform Simcenter 3D, en del av PLM-portföljen Xcelerator, spelar en viktig roll för att hantera simuleringsflödet, inkluderat andra verktyg, som MSC Nastran, Ansys och Dassault’s Simulia.
– Vi fokuserar på att designa och bygga drivlinor, men dessa används i
kompletta fordon så det är viktigt att förstå hur de beter sig när de är installerade. Därför planerar vi att använda oss av Siemens faciliteter och produkter som gör att vi kan kombinera våra simuleringar med fysiska tester, säger Hans Johannesson, teknisk ledare på Aurobay, i en fallstudie publicerad av Siemens, som vi har tittat närmare på.
Det är uppenbart att elmotorer är framtiden för vägtransporter, men det handlar inte om att i ett slag helt stoppa produktionen av förbränningsmotorer (ICE) och omedelbart byta allt till elektriskt. Det blir en gradvis övergång som måste hanteras noggrant av tillverkarna. De måste tillgodose efterfrågan på ICE samtidigt som de fortsätter att öka produktionen av elmotorer för att möta marknadens växande efterfrågan. Parallellt måste de förbli konkurrenskraftiga hela tiden, vilket kan vara en tuff ekvation att lösa.
Aurobay, tidigare alltså en del av Volvo Cars Powertrain Engineering är, som noterades i ingressen, specialiserat på utveckling av både förbränningsmotorer och hybridmotorer. I ett NVH-perspektiv finns i detta utmaningar som har både likheter och olikheter.
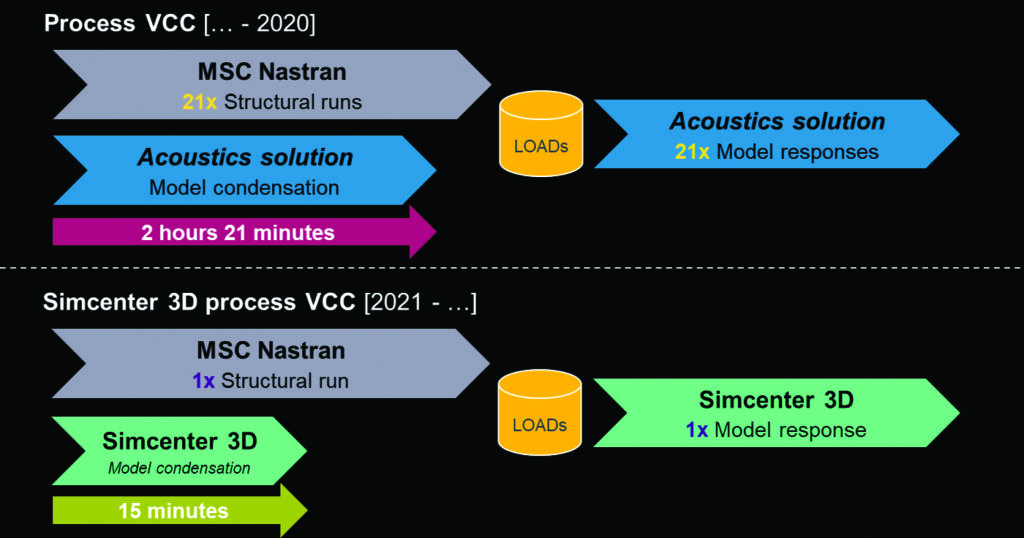
En grundläggande skillnad mellan att förutsäga vibrationer i ICE/förbränningsmotorer och elmotorer är att de förra kräver mer omfattande analys av hastighetsdata (även känd som Waterfall of Frequency Spectra Analysis), medan den senare kräver ett större fokus på analys av ordnad data. Men båda används lika med hybridmotorer. När man utvärderade lösningar fann Aurobay att de flesta specialiserade sig på det ena eller det andra. Detta emedan Simcenter 3D kunde användas för att göra båda lika bra och växla mellan de två utan ytterligare analys.
– Vissa lösningar har ett helt slutet ekosystem, kommenterar tekniska ledaren Hans Johannesson och tillägger att man i så fall, ”skulle behöva byta överallt, vilket skulle ta avsevärd tid och investering. Men vi kan använda Simcenter 3D tillsammans med våra andra verktyg, vilket gör det mycket enklare att använda, snabbare att integrera i hela verktygskedjan och mer överkomligt att implementera.”
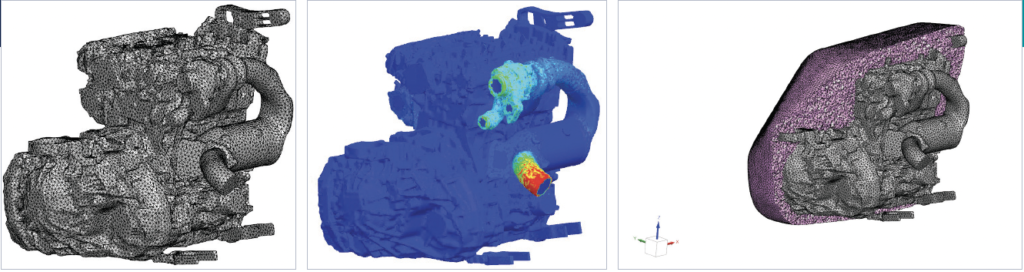
Effektivisering av NVH-analys
För att mäta detta beräknar Aurobays ingenjörer först den strukturella dynamikens vibrationer som orsakas av motorn. Excitationsbelastningar läggs sedan till och akustisk strålning förutsägs. Med deras tidigare akustiska verktyg behövdes 21 körningar med full FE (Finita Element) för varje scenario för att få tillräckligt med data för att göra korrekta förutsägelser. Men genom att använda Simcenter 3D behöver endast en FE-baserad reducerad ordningsmodell (ROM) skapas för varje scenario. Den fångar vibrationernas akustiska känslighet och kan snabbt och enkelt återanvändas för olika driftsförhållanden.
– Att använda Simcenter 3D minskar den totala simuleringstiden från över 2 timmar till bara 15 minuter, en betydande tidsbesparing när den tillämpas över flera scenarier, kommenterar Johannesson.
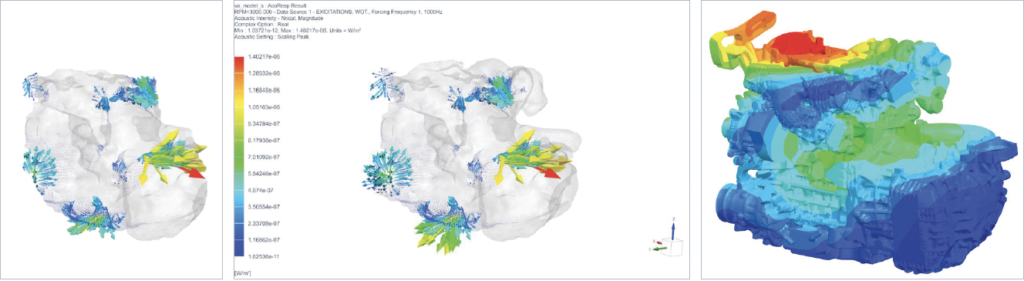
Gör simulering mer tillgänglig
En betydande minskning av simuleringstiden sålunda. Även om mer arbete initialt krävs för att ställa in ROM med en fullständig finita elementanalys (FEA), till skillnad från andra lösningar, behöver detta med Simcenter 3D bara göras en gång.
ROM kan sedan överlämnas till mindre erfarna ingenjörer som kan utföra omfattande analyser genom att justera parametrarna för belastningsförhållandena och köra olika analyser med hjälp av en linjär lösare.
Detta genererar enorma mängder resultatdata som skulle vara omöjliga att använda när man utför manuell analys. Emellertid gör Simcenter 3Ds efterbearbetnings-verktyg det enkelt att söka och hitta relevant information som underlättar utvecklingen. Faktum är att på Aurobay utförs detta steg ofta av en analytiker som förbereder data och delar den mellan alla team inom organisationen. Detta innebär inte bara att alla människor får viktig information snabbare, utan ingenjörer frigörs också för att arbeta med nästa steg i projektet eller på ett helt annat projekt.
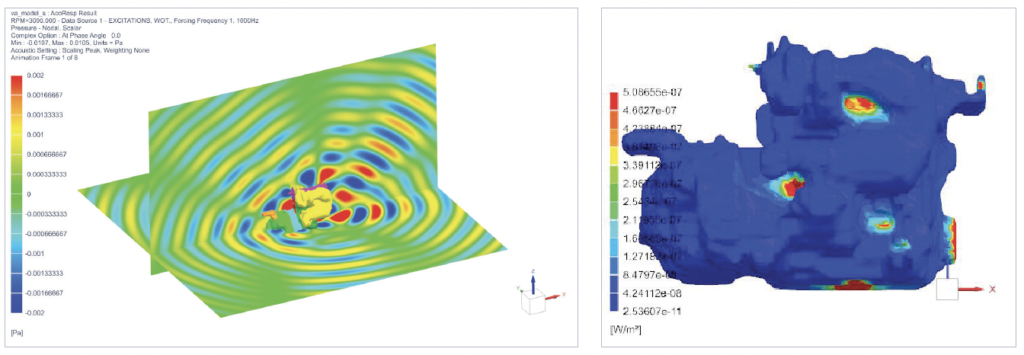
STAR-CCM+ för input till Simcenter 3D Acoustics
Efter att ha framgången med att införliva Simcenter 3D planerar Johannesson att lägga till fler Simcenter-lösningar till Aurobays processer i framtiden:
– Vi fokuserar på att designa och bygga drivlinor, men dessa används i kompletta fordon så det är viktigt att förstå hur de beter sig när de är installerade. Därför planerar vi att använda oss av Siemens Digital Industries Softwares faciliteter och produkter som gör att vi kan kombinera våra simuleringar med fysiska tester.
Genom att kombinera de två kommer Aurobay att göra en mer omfattande utvärdering av prestanda för buller, vibrationer och hårdhet (NVH), såsom bullret inuti fordonshytten för att optimera slutprodukterna för ännu större komfort.
– Vi avser att använda Simcenter STARCCM+ CFD-verktyget för input till Simcenter 3D Acoustics, fortsätter Johannesson. Detta kommer att göra det möjligt för oss att analysera såväl flödesakustik som vibrationsakustik. STAR-CCM+ kan ge oss data om saker som tryck på en kanal och sedan kan vi använda Simcenter 3D för att förutsäga det brus som detta genererar.