Generally, the Simcenter environment is well integrated and Siemens’s usual high level of openness is a typical signum, allowing the users to perform in principle most of the CAE pre- and post-processing based on CAD geometry from any source.
There are also a number of tools for geometry manipulation supported by intuitive interfaces.
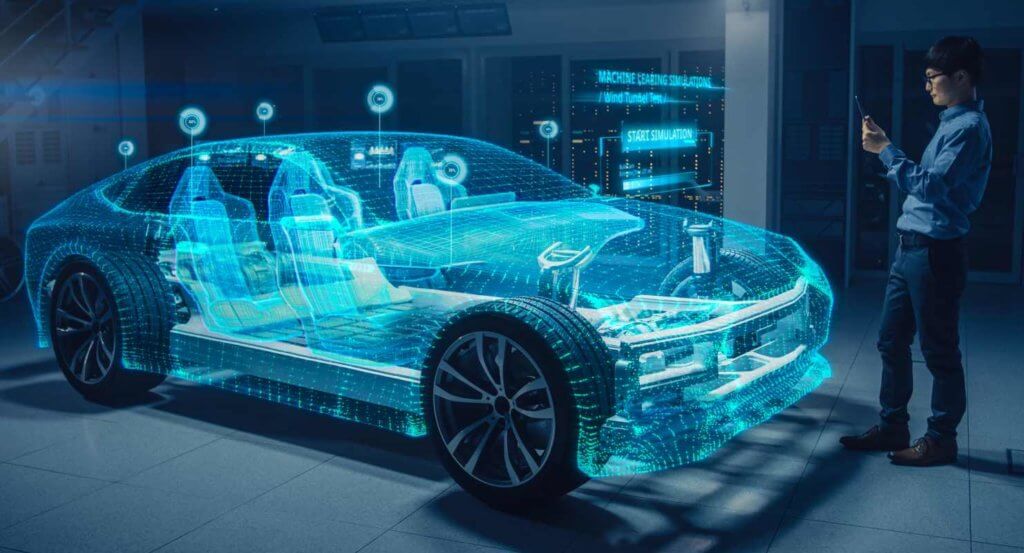
A short background on Siemens Simcenter platform strategy
Siemens S&A approach is characterized by a focus on the next generation of integrated, analytics-driven performance engineering solutions. In this the Simcenter suite within the Xcelerator portfolio is the umbrella, covering the entire Siemens portfolio of simulation, optimization analysis, testing, and related analytics capabilities.
It’s a rich environment that also supports the next generation model-based engineering (MBE) processes as well as traditional product verification and validation activities.
Furthermore, an important role in Siemens simulation landscape is played by the company’s comprehensive digital twin-approach, tailored for design engineers, dedicated analysts, test engineers, domain specialists, and decision makers while enabling collaboration within the broader enterprise.
Significant R&D investments are going towards supporting major industry trends such as 3D printing and additive, autonomous systems, electrification, 5G, MBSE, IIoT and, not least mirrored in the Altair Engineering purchase, an extensive bet on artificial intelligence, AI. Siemens strategy emphasizes a hybrid approach that combines the strengths of simulation and analysis with physical testing and data analytics to accelerate all phases of development for complex systems.
Notably, Simcenter 3D represents an extensive set of CAD-neutral modeling with multi-discipline solutions for structural, motion, thermal, advanced materials and composites, acoustics, flow simulation, both low- and high-frequency electromagnetics, environment simulation, and design optimization. PLM analyst CIMdata writes in its 2023 report that, “capabilities from the former NX CAE suite are integrated with Simcenter Nastran along with the former LMS 3D Simulation solutions (LMS Virtual.Lab and LMS Samcef) as well as other industry vertical solutions into a single, multi-discipline environment for the CAE analyst. These simulation capabilities are available both standalone as well as fully integrated into the NX product development application for ease of use by design engineers. Other solutions tailored to use by design engineers include Simcenter FLOEFD and Simcenter Flotherm from the Mentor acquisition.”
Some examples of companies in the user community are:
SpaceX | Aviation And Aerospace Component Manufacturing | |
General Motors | Motor Vehicle Manufacturing | |
Firefly Aerospace | Airlines And Aviation |
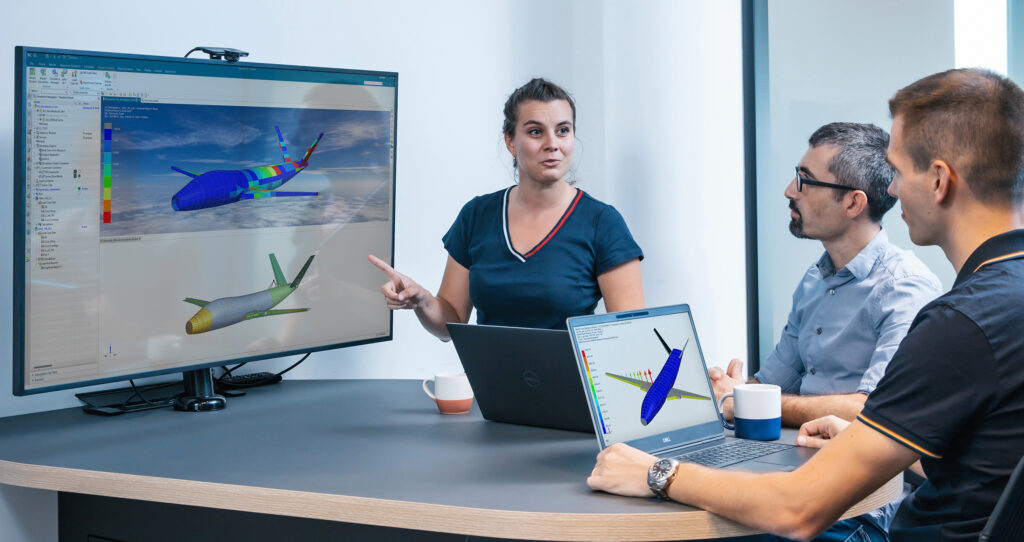
The updated version is addressing complex engineering challenges
This said, let’s take brief look at the general values of this type of broad platform: Overarching is the software’s capacity to predict system behavior, particularly useful for evaluating new designs, diagnosing problems or testing a systems under conditions that are difficult to physically reproduce, such as a satellite in outer space or the enormous miles of test driving required to develop ADAS (Advanced Driver Assistance Systems) functionalities in the automotive sector.
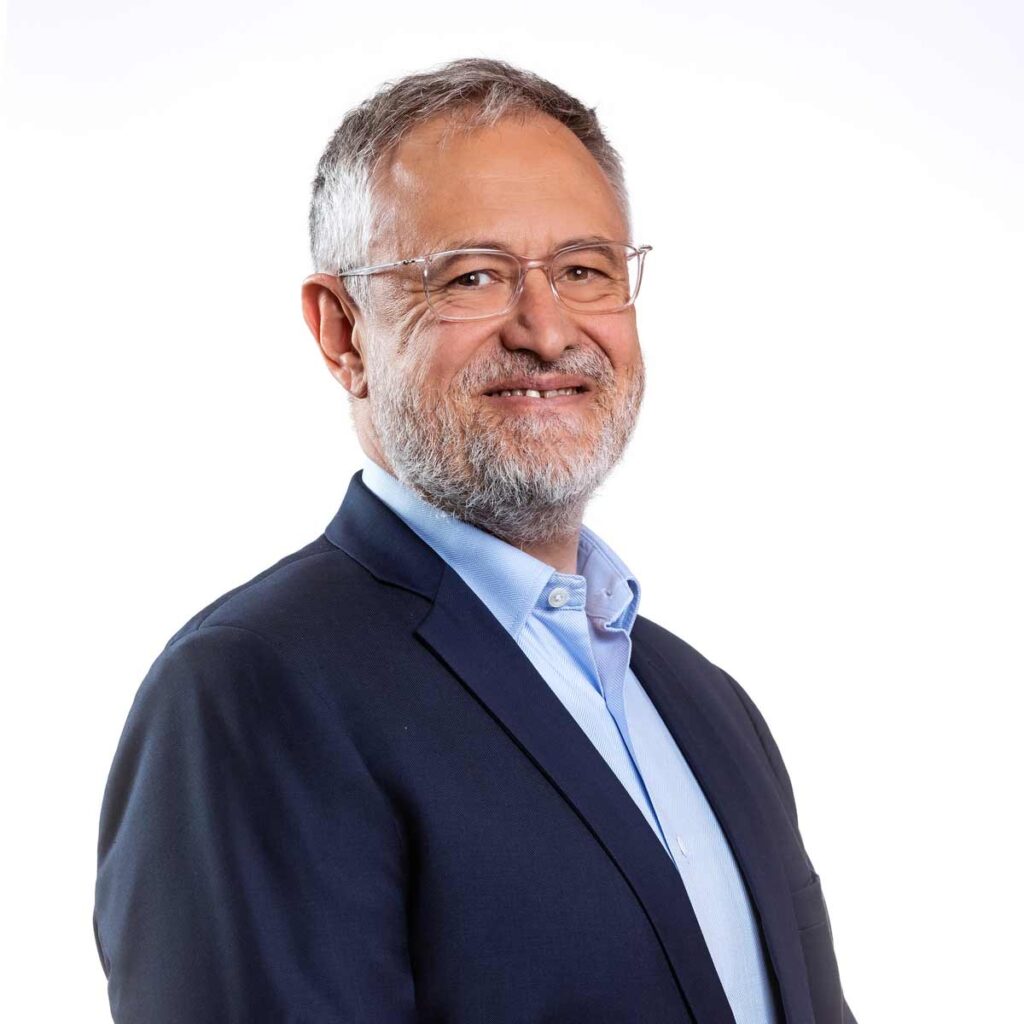
“In short, addressing complex engineering challenges such as developing products that are more powerful, yet greener; lighter, yet stronger, requires exactly what we offer with Simcenter – a fully integrated CAE solution,” says Jean-Claude Ercolanelli (pictured to the left), who also notes that the latest version of Simcenter offers a host of powerful enhancements to help engineers meet these challenges effectively and significantly faster than ever before. Whether it’s speeding up additive manufacturing simulations by a factor of 200%, solving tire contact simulations 45% faster, or automating the creation of free-body diagrams and margin of safety (MoS) calculations in integrated aerostructure analysis to accelerate the development of certification schemes by 20%.
“But our development work continues unabated. I believe in the value that simulation and analysis tools bring to the world, whether it is software, hardware or services.”
From sharpened tools for aerostructure analysis to
super-fast simulation in additive manufacturing
Here are the key improvements and some of the benefits that come with them in the new updated Simcenter version.
Integrated Aerostructure Analysis: Simcenter automates the creation of free-body diagrams and margin of safety (MoS) calculations, accelerating certification schedules by 20 percent. Engineers can now evaluate load paths across aircraft models and perform full-envelope MoS analysis without the need for costly in-house tools.
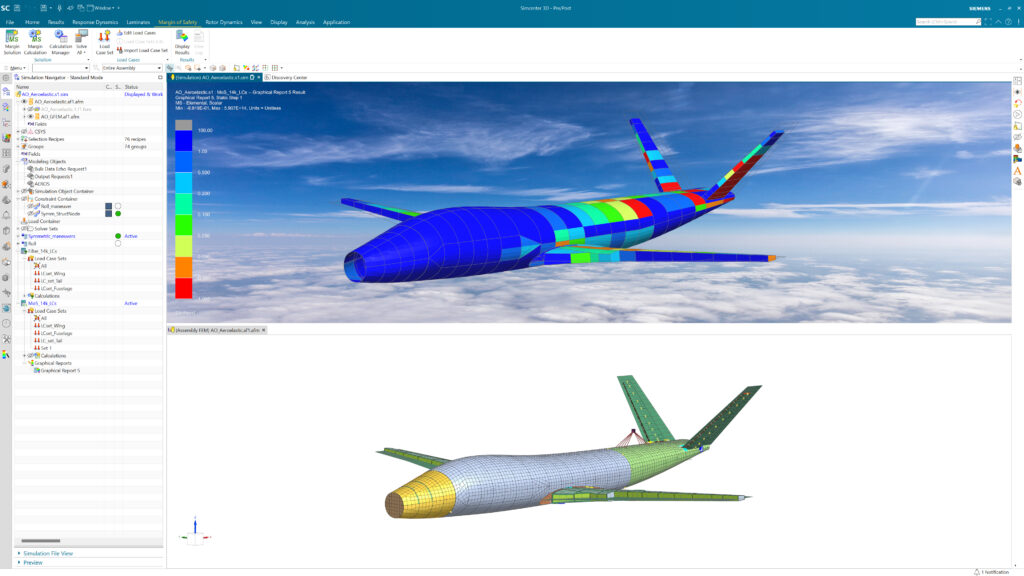
Axial flux motor simulation: Simcenter enables faster design and simulation of compact, high-power-density motors. Engineers can quickly create lightweight designs using Siemens’ Simcenter E-Machine Design software, then transition seamlessly to 3D simulations in Siemens’ Simcenter 3D software for comprehensive electromagnetic, thermal and mechanical performance assessments.
Gear Design Optimization: Simcenter introduces lightweight gear blank parameterization and an optimization framework to improve gearbox noise, vibration and harshness (NVH) performance. These tools help reduce late-stage design changes and streamline the development cycle.
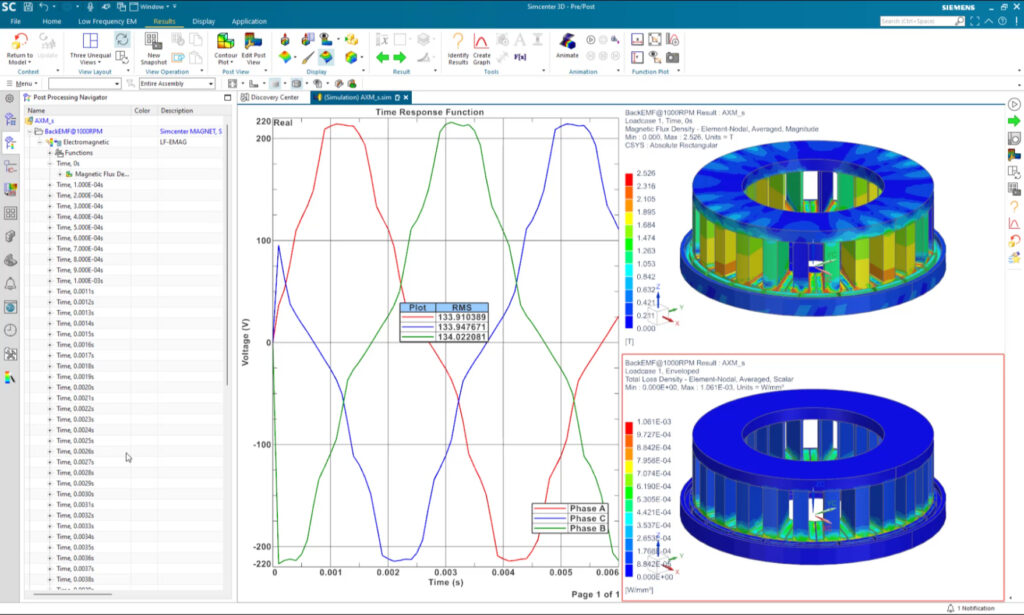
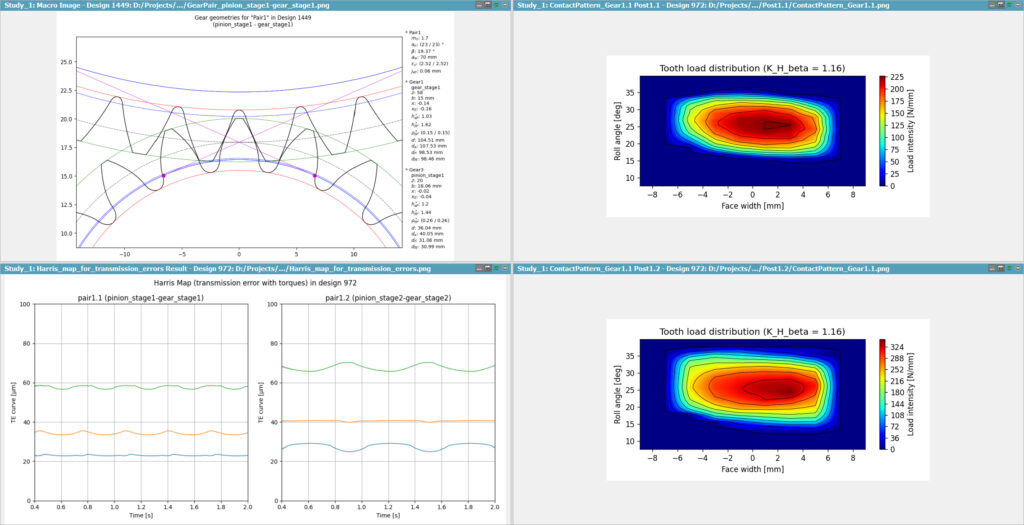
Extended Smart Virtual Sensing: Simcenter expands capabilities to include rigid body motion sensors and damage assessment tools, providing insights into the durability and remaining useful life of machines even in challenging test environments.
Simulation efficiency and collaboration: Speeds up additive manufacturing simulations by a factor 200 percent with voxel mesh improvements and enhances collaboration with centralized model data and streamlined load and boundary condition transfers.
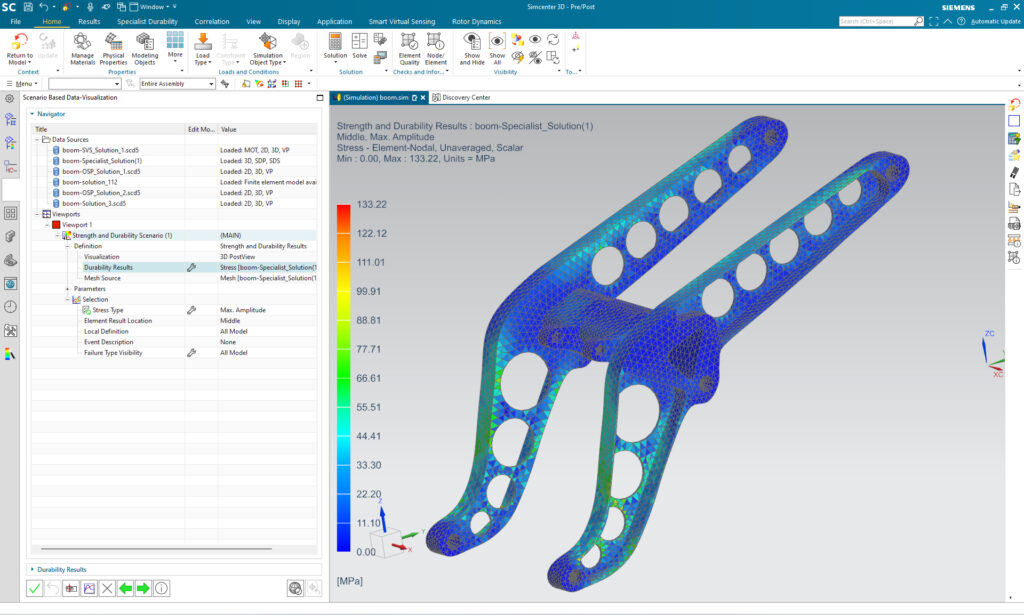
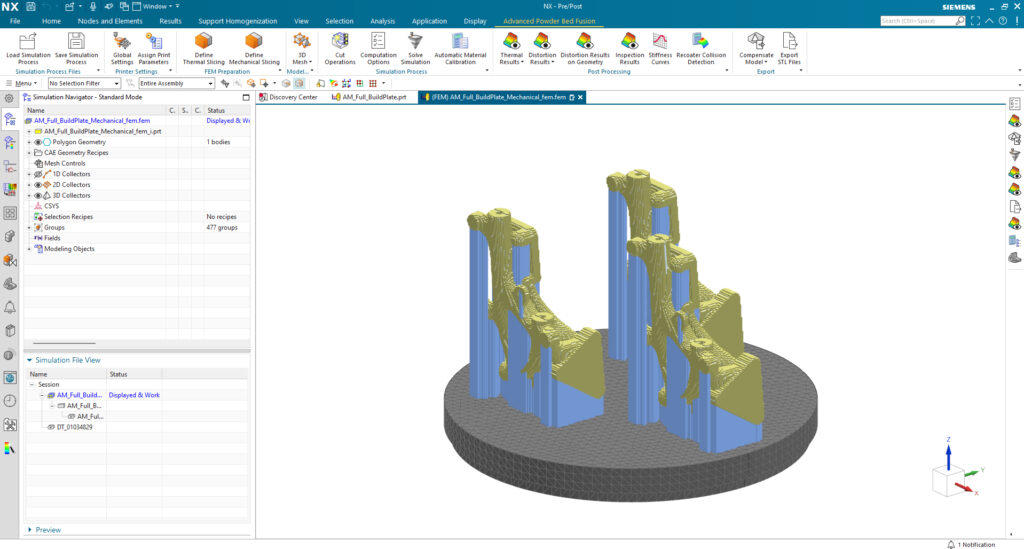