Detta med ”closed-loop manufacturing” kan låta superspetsigt och komplext, och är det på sitt sätt också. Men å andra sidan är tankegångarna redan omsatta i reala lösningar i Siemensvärlden och i dagsläget pekar många tecken mot att detta sätt att organisera produktframtagning kommer att revolutionera världens tillverkningsindustrier. Poängen är att skapa hanterbarhet och med, så långt det är möjligt, en enkelhet på ytan, men komplex kapacitet på djupet, där det mesta är styrt av automatiserade, sammankopplade och ofta molnbaserade systemlösningar och där AI (Artificiell Intelligens) spelar en huvudroll.
– Allt är ju på något vis relativt, summerade chefen för Siemens PLMs nordiska rörelse, Mats Friberg. ”Closed-loop manufacturing-koncept”, är viktigt, innehåller absolut en teknik som kommer på bred front, men är ingenting man gör över en natt. Idag finns dock både teknologi och metodik som gör att man kan komma igång. Alla vet ju också att utvecklingen numera går väldigt snabbt och den som är proaktiv kan bidra till att skapa riktigt vass konkurrenskraft med CLM-processuella upplägg redan nu. Men då gäller det som sagt att våga ta steget att inleda processen mot CLM.
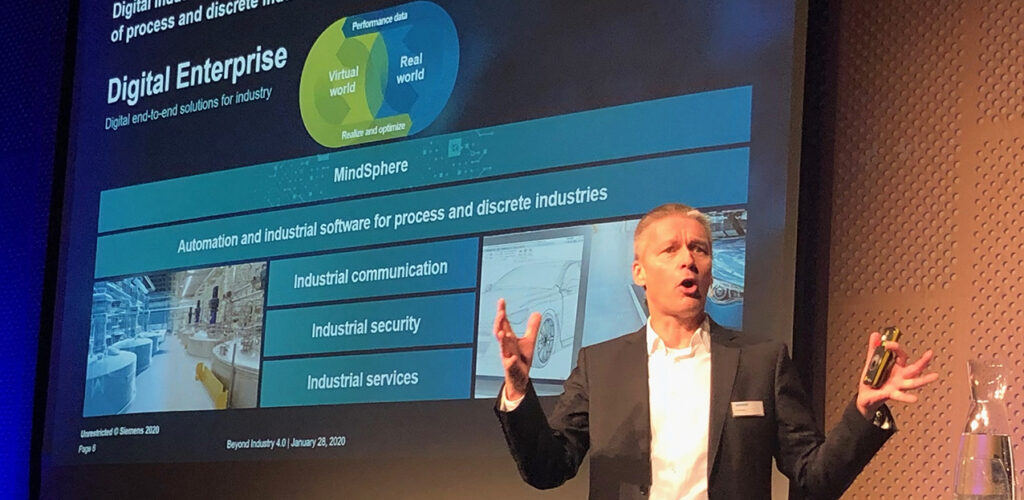
Siemens har satsat mer än 10 mijarder dollar på CLM
Att komma igång är förstås viktigt, men det hindrar inte att CLM-koncept finns redan idag, hävdade Friberg – något som Siemens COO, Jan Mrosik, höll med om.
– Absolut. CLM – som i de flesta perspektiv tangerar Industri 4.0-konceptet – är redan en realitet i flera framskjutna industriprojekt, konstaterade Mrosik, i sitt inledningsanförande och exemplifierade med bolagets egen berömda elektronikfabrik i tyska Amberg. Han fortsatte:
– En finess med det vi har att lägga upp på bordet när det gäller Industri 4.0-relaterade system är att den stora Siemenskoncernen, med total 385 000 medarbetare, har en rad tillverkande enheter i allt från kylskåp och spishällar till avancerade medicintekniska och industriella maskiner. Allt vi producerar i form av digitala utvecklings- och automationslösningar kan vi testa själva i våra egna anläggningar. Det betyder att det som kommer ut från SDI i form av digitala produktframtagningslösningar alltid är industriellt bevisade. Saker och ting fungerar, kort sagt.
Han berättade vidare att bolaget satsat enormt mycket pengar och utvecklingsresurser för att skapa lösningarna som, ”förvandlar data till värde utifrån en holistisk synvinkel.”
– Att få ihop IT och OT (operativ teknik, ”data och drift från och av maskinerna på verkstadsgolvet”) är ett resurskrävande utvecklingsarbete. Vi har exempelvis köpt 35 bolag för över 10 miljarder dollar (ca 95 miljarder kronor). Dessa integrerar vi på ett sätt som kombinerar de virtuella och fysiska världarna, fram och tillbaka i sammanhållna loopar: konstruera, simulera, optimera, gå till tillverkning, simulera igen, optimera igen, och tillverka felfritt. Detta är tanken i vårt CLM-upplägg.
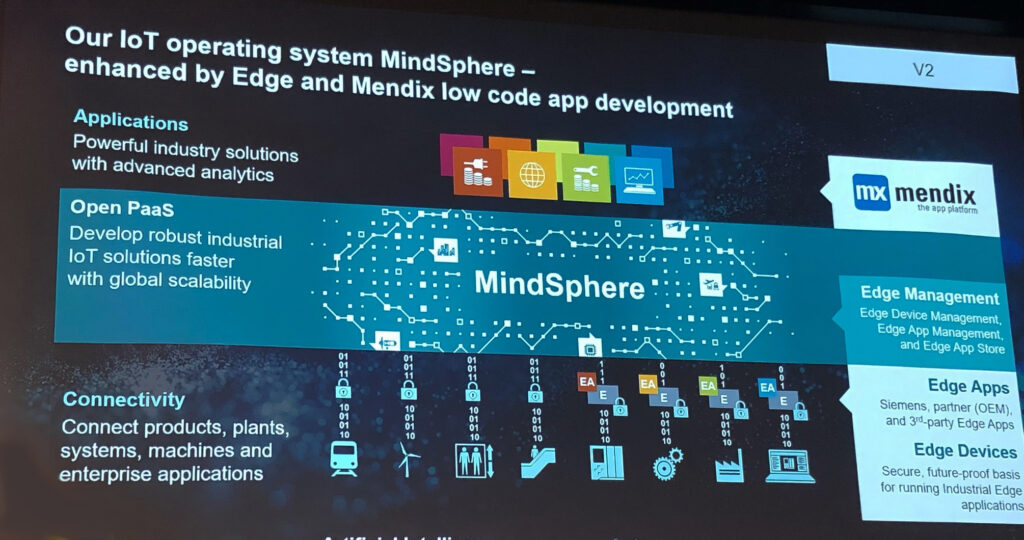
Den digitala tvillingens helt avgörande roll
Det är här den digitala tvillingen kommer in och spelar en huvudroll; på flera sätt är det den minsta gemensamma nämnaren i en process som leder in på fabriksgolvet och sedan ut därifrån. Siemens delar upp tänket kring tvillingar i tre delar:
• Dels den digitala tvillingen av produkten
• Dels en tvilling av produktionsenheten/tillverkningslinan
• Dels en tvilling för produkten i användarens händer, med återkopplingsbarhet till PLM-systemets tvilling. Man ska t ex kunna simulera en pumpanläggning i drift för att optimera flöden, eller om något går sönder eller behöver förbättras, kunna gå tillbaka med fältdriftsdata till PLM-systemet för att där korrigera och förbättra baserat på dessa.
Generellt är också simuleringsbiten en nyckelkapacitet. Med den digitala tvillingen i centrum är allt simuleringsbart i alla led, för att man ska kunna säkra att allt fungerar som tänkt innan man går över till de fysiska motsvarigheterna, då eventuella förändringar och upptäckta fel blir dyra att åtgärda.
– Allt kan kopplas ihop via IoT och IIoT (Industria IoT), vilket i Siemens fall går över vår MindSphere-mjukvara, förklarar Mrosik. Fungerar det inte som du tänkt dig? Förbättra och optimera genom att gå tillbaka och simulera igen. Det är en viktig poäng CLM-tanken.
Men han betonar också vikten av att kopplingarna till ERP-systemen finns med i konceptlösningen. Om dessa inte finns missas länkningen till order-systemet och flera, möjligen divergerande, ”sanningar” kommer att finnas; något som riskerar att dra ner process- och tillverkningskvalitén och öppnar för fel. ”One single source of truth,” som mantrat lyder, är den eftersträvansvärda finessen för att undvika felkällor.
Resultaten som detta kan leverera är imponerande, fortsätter Siemens’ COO och pekar på flera verkliga Siemensrelaterade case, som är igång:
• Dulux, som är Australiens största färgtillverkare.
• Kinesiska fordonstillverkaren Mino, som reducerat tiden för ingenjörsarbetet med 1/3 och som kapat ”comissioningtiden” – att dra igång tillverkningen i en produktionslina – från två till en månad.
• Grundfos som kopplar upp sina pumpar via IoT-mjukvara MindSphere.
Inom parentes ska nämnas att den senare mjukvaran i analytikern Forresters senaste s k IIoT Wave, pekas ut som en av världens fyra ledande lösningar och idag väl i paritet med konkurrerande PTCs ThingWorx.
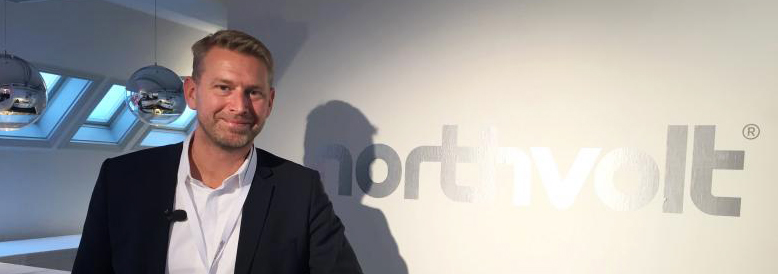
Peter Carlssons Northvolt-projekt har CLM i siktet
Men det kanske mest intressanta caset Jan Mrosik tog upp var svenska batteriutvecklaren Northvolt. Bolaget jobbar i produktframtagningsspåret – när det gäller utveckling och tillverkningsautomation – med mjuk- och hårdvaror från huvudsakligen Siemens, även om också ABB partiellt är tungt inblandade i delar som elektrifierings- och tillverkningsprocess-områdena.
Northvoltgrundaren och förre Teslamannen själv, Peter Carlsson, berättade inspirerat från scenen om detta gigantiska projekt, som är Sveriges kanske enskilt största industriprojekt någonsin. Han nämnde inte beloppet, men i en tidigare pressrelease från 2017 har satsningen angivits till 42 miljarder kronor och de tunga bitarna är bl a:
* Bygget av en gigafabrik i Skellefteå, Northvolt Ett – vilket man är igång med – och Northvolt Battery Systems-anläggningen i polska Gdansk (där man idag skapar konfigurerade systemlösningar kring battericeller).
* Detta emedan man till stora delar är klara med R&D-labbet i Västerås.
* I Tyskland jobbar man också initialt med ytterligare en batterifabrik, som ska förse Volkswagenkoncernen med batterier, Northvolt Zwei. Denna kommer att byggas på ”blueprints” från Skellefteå-enheten i takt med att bygget framskrider där.
När gigafabriken i Skellefteå, som han kallar den, är klar och i full produktion under 2023 kommer den att konsumera ca 2 procent av Sveriges samlade energiproduktion.
Det är uppenbarligen tämligen energikrävande att producera och ladda litiumjon-batterier.
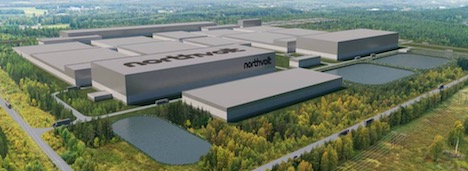
Produktionen räcker till mellan 250 000 – 300 000 bilar
– De första 16 GWh produktion av batterier i Skellefteå kommer att räcka till mellan 250 000 och 300 000 bilar, berättade Peter Carlsson och tillade apropå produktutvecklingen att, ”digitala tvillingar är ett tungt inslag också i fabriksbygget.” Dessa tvillingar kommer sedan vartefter att utgöra ”fabrikskopior” som ska användas när man bygger upp anläggningen i Tyskland (Northvolt Zwei), som framför allt ska förse Volkswagenkoncernen med batterier till elfordonen.
På produktutvecklingssidan är det program som Siemens Teamcenter (PLM-backbone), NX (CAD), Battery Design Studio, Simcenter Structures/STAR-CCM+ (flödessimulering)/Amesim (1D-simulering), som gäller och på produktionssidan finns bl a Tecnomatix/Plantsimulation med i handlingen.
På automationssidan hittar vi Siemens Simatic-portfölj, inkluderande styrsystems-, integrations- och säkerhetslösningar, medan rörelsekontroll av motorer och servon e t c hanteras i Siemens Simotion.
När det gäller ABBs roll så berör det sånt som processautomation och elektrifieringen av anläggningarna.
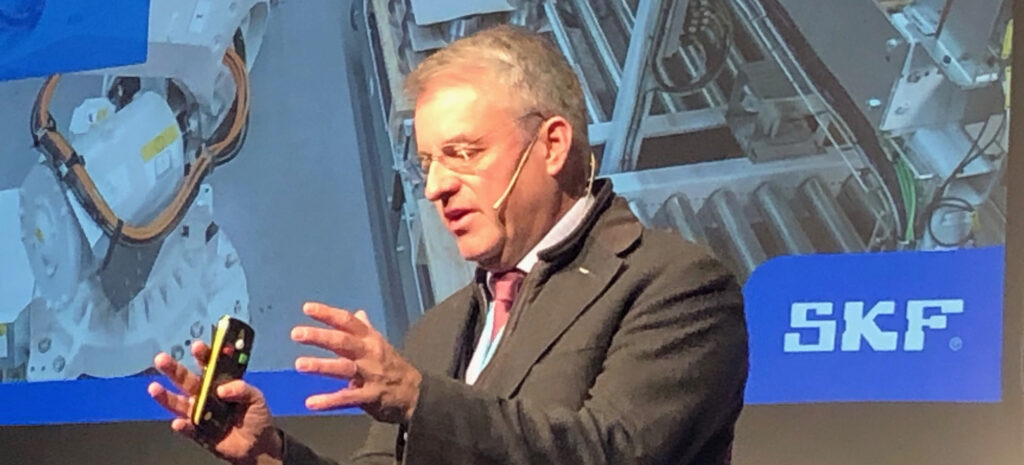
World Class Manufacturing på SKF
PLM&ERP News ska i en kommande artikel – som också ska publiceras på vår amerikanska systersajt, engineering.com/PLM – göra en större genomgång av detta historiska projekt.
Missa inte heller nästa veckas artikel om ytterligare en spännande föreläsare på Siemenseventet: SKF-chefen Alrik Danielsson, som berättade om ”World Class Manufacturing-koncept” hos den svenska kullagergiganten.
– World class manufacturing är helt enkelt en nödvändighet för att vara kvar på marknaden, konstaterade Danielsson bl a och beskrev hur detta ser ut i fabriken i Göteborg, där man drivit automatiseringen mycket långt med hjälp av bl a KUKA-robotar.
– SKF är f ö den enda branschaktören som monterar helt maskinellt, utan mänskliga händer, sa han. Detta är bra för miljön, bra för människorna och överlägset för ergonomin.
Han tillade vidare att man dragit igång ”remanufacturing-program” av kullagren, som inneburit att man reducerat koldioxidutsläppen relaterat till tillverkningen med upp till 90 procent; denna tillverkningstyp har f ö dessutom bidragit till att skapa nya jobb.
Siemens är också i detta sammanhang en digital partner i SKFs ”world class manufacturing-projekt”, vars implementering strukturellt indelas i tre huvudfaser:
- Icebreaker 2. Scale up 3. Setting benchmarks.
Alrik Danielsson är sammanfattningsvis alltså ingen fan av inkrementell implementation av den här sortens nya lösningar. Läs mer om detta case i den kommande artikeln nästa vecka.