In ABB’s first survey (Global Automotive Manufacturing Outlook Survey), industry experts questioned whether prescribed timeframes for switching to production of pure electric vehicles could be achieved. The question came up again in this year’s survey, and there are now fewer respondents who strongly believe that the transition can be completed, from the previous 11 percent down to just 8 percent this year. Over half (53 percent) still believe that the goals will never be reached, compared to 59 percent in the previous year’s survey.
Specific skill gaps provide insights
One reason for the doubt about whether deadlines will be met for electric vehicle production may be due to concerns about the lack of trained labor. Over half (54 percent) of all respondents believe that specific skills shortages have a major impact on manufacturing: European (52 percent) and Asian (58 percent) respondents point to skills in electric vehicles and batteries as the primary problem areas.
“The skills shortage in certain very specific areas is a concern in the industry,” says Daniel Harrison, Automotive Analyst at Automotive Manufacturing Solutions (AMS), and adds: ”As the production of electric vehicles increases, the need for skill enhancement or relocation of a large number of existing employees as well as the need to attract new talent to the automotive industry increasingly important. Electric vehicle manufacturing, together with more and more software, electrical and advanced electronic components, demands new and different skills, and the survey reflects a conviction that more efforts need to be made.”
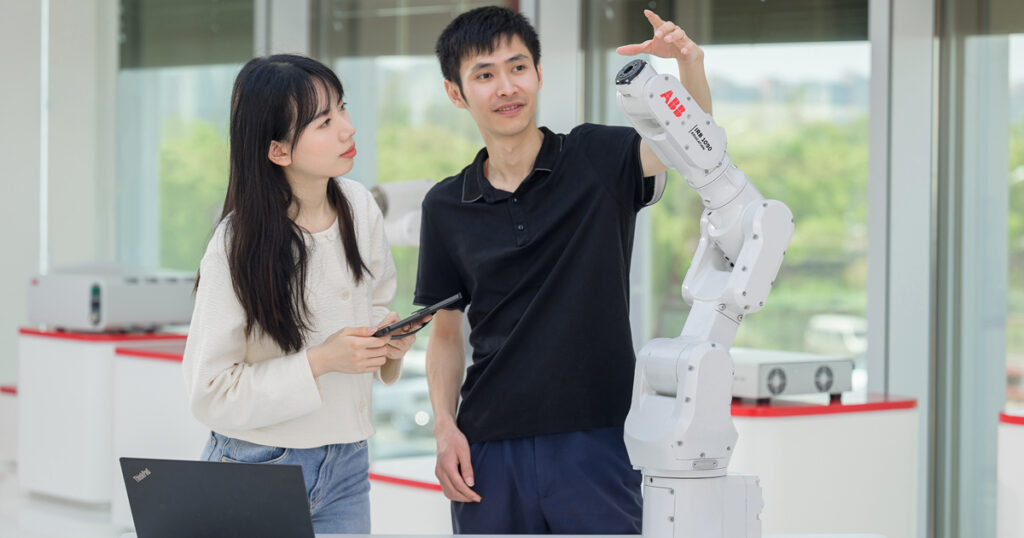
It is also notable in this context that ABB Robotics has responded to the challenge by investing in outreach programs developed together with hundreds of schools and universities around the world to teach automation and software skills to students, skills that can then form the basis for the smart manufacturing solutions of the future. Verified by STEM.org, the company’s IRB 1090 educational robot is designed to empower students as they learn the basics of robot programming.
Disruptions in the supply chain
The survey also highlights how disruptions in supply chain caused by the global instability also continues to be a major problem for the industry and often leads to component shortages and production delays. More than a third (35 percent) of all respondents highlight this issue, and there is a strong increase among respondents in North America (51 percent) who consider this to be the region’s top manufacturing challenge.
ABB’s survey gathered opinions on a number of different topics from a broad mix of nearly 400 industry experts, from vehicle manufacturers and suppliers at all levels of management to engineers and other specialists across the entire automotive manufacturing industry.
In the intro to this article we discussed what BMW managed to produce in terms of saved energy consumption in its engine factory i Steyr, Austria, as an example of what you can do with PLM and simulation tools. Don’t miss to read the case study published by Verdi Ogewell on ENGINEERING.com to learn how the iconic German car manufacturer saved millions of kWh by using simulation tools from Siemens Digital Industries Software – Tecnomatix Plant Simulation. Click on the linked headline below to read the full article:
How BMW Used PLM and Simulation to Save 3 Million kWh Per Year