Industrial customers remain interested in the potential of the industrial metaverse for high-fidelity and real-time visualization of systems in immersive environments. The immersive environments of the industrial metaverse can help change how products are designed, certainly, but also how they are manufactured and maintained, hopefully making the jobs of people easier throughout a company.
An environment that enables evaluation, analysis and prediction
Readers have undoubtedly heard of the metaverse as a consumer product – conceived of as a virtual place that users can go to play games, socialize, engage in commerce, even own virtual property. The industrial metaverse is similar in name only. The industrial metaverse is a physics-based virtual environment that enables the evaluation, analysis, and prediction of behavior based on deterministic models of the product, process, production plant, and more. This environment is accessible through several different devices, including but not limited to augmented and virtual reality. It also aggregates and normalizes data from multiple sources to enable a holistic assessment of a system or product all in one environment.
The result is a virtual environment, founded in physical reality, that enables fast and intuitive conceptualization, design, and detailed engineering of complex products and systems. Instead of assessing system performance based solely on charts, tables, or raw data, designs can be visualized and manipulated in full 3D, enabling users to interact with the digital twin. This can help uncover problems that, in the past, were often not discovered until prototypes were built and tested in the real world, leading to schedule delays and increased cost and material usage. Any problems identified in the industrial metaverse can be resolved quickly through rapid design iteration in the virtual world, saving time, resources, and money.
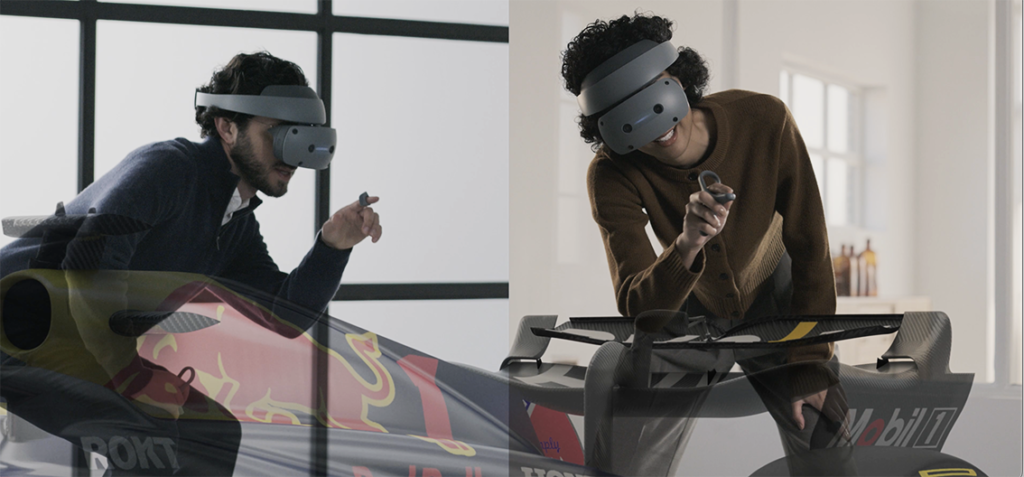
Furthermore, the industrial metaverse is not a standalone environment, divorced from the day-to-day operations of a company. The industrial metaverse can ingest data from multiple sources, both real and digital, and orchestrate this data into a single experience for the user. This brings all the information into one view, enabling greater transparency and a deeper understanding of the dynamics of a system design, production process, supply chain, or myriad other concerns. As a result, the industrial metaverse is more than a space for creation, it also enables companies to actively monitor, analyze, and manage real world assets in a closed-loop process, so they can make more informed engineering and business decisions.
Reach the industrial metaverse through digital transformation
To reach its full potential, the industrial metaverse must become more than a visualized version of the digital twin. On the manufacturing floor, every movement and action must be accounted for in a precise way, demanding real-world physics. Increasing access to cloud computing will support the industrial metaverse with the necessary computational power to back up immersive visuals with physical simulations, vastly increasing its value in the design and development process.By applying real world physics and robust operational data to the industrial metaverse, we have the potential to create more than a gamification experience. The result can be a shared and immersive environment where learning is faster and more intuitive, design concepts are more easily understood, and where new ideas can be investigated quickly and thoroughly to drive innovation for the future.
Such a powerful environment is the culmination of key technology trends taking shape across industries today. Companies that embrace the digital transformation journey will be positioned to overcome the challenges on the horizon and surge ahead of the competition by leveraging the capabilities of the comprehensive digital twin, software and systems engineering, integrated IT and OT systems, artificial intelligence, and ultimately the industrial metaverse.
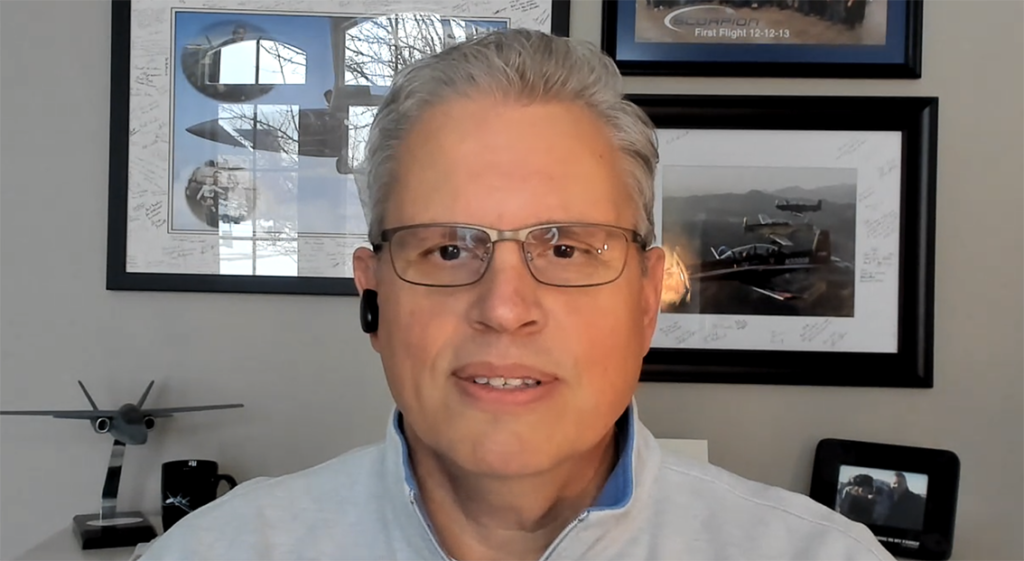
About the author – heavy credentials in the aerospace industry
PLM&ERP News’ and ENGINEERING.COM readers have met Dale Tutt in previous articles:
“The Lockheed Martin Aeronautics Win – Integration and Digital Twins the Secret to Siemens’ A&D Success”
He is currently the VP for Industry Strategy at Siemens Digital Industries Software, and leads the development of digital transformation solutions that meet customers’ industry-specific needs. Tutt joined Siemens in 2019 as vice president for the aerospace and defense industry.
Prior to joining Siemens, Tutt worked at The Spaceship Company, a sister company to Virgin Galactic, as the VP of Engineering and VP of Program Management, leading the development of spaceships for space tourism. He led the team on a successful flight to space in December 2018.
Previously, Tutt worked at Textron Aviation/Cessna Aircraft in program and engineering leadership roles. As the Chief Engineer and Program Director of the Scorpion Jet program, he led a dynamic cross-functional team to design, build and fly the Scorpion Jet prototype from concept to first flight in 23 months.
Tutt also worked as an engineer at Bombardier Learjet and General Dynamics Space System Division.