Tillverkning enligt ”closed loop-koncept” innebär att man måste planera sina processer på ett sätt som gör att man kan matcha kravet på effektivare produktion. En konsekvens kan alltså vara att man via en IIoT-plattform ständigt matar tillbaka data om hur tillverkningen presterar.
Detta bygger i sin tur på att man ställer in KPIer (Key Performance Indicators) redan från start och etablerar tydliga system för övervakning och insamling av data från den uppkopplade produktionsapparaten. I nästa steg gör man mätningar och justeringar som möter eventuella avvikelser – och återställer sina KPIer. Sedan börjar slingan om igen – den slutna cirkeln, ”the closed loop”.
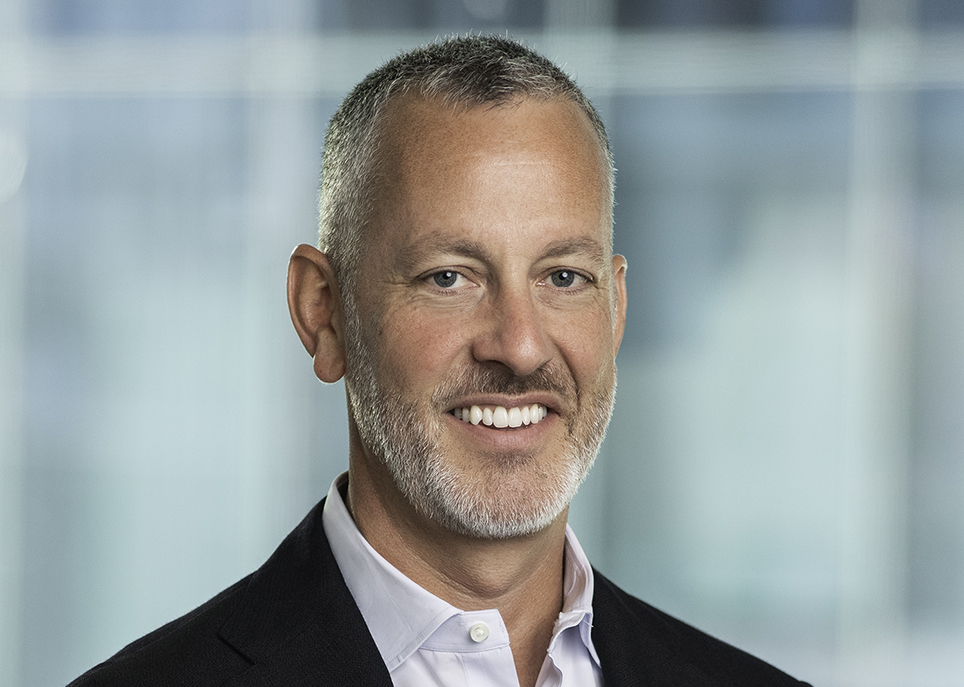
HAN ÄR THINGWORX DPMs FADER
PTCs EVP för digitala tranformationslösningar, Craig Melrose, vet det mesta om de här sakerna. Bakom sig i karriären har han bl a 20 år på McKinsey där han framför allt jobbat med att optimera fabriker runt om i världen. Han är också DPMs fader.
Hur ser han på sin och PTCs nu lanserade approach för att lösa problemet med att effektivisera produktionen? Och hur ska man betrakta ThingWorx DPM i förhållande till PTCs definition av CLM?
För att förstå PTCs approach till Closed-Loop Manufacturing, som är lite annorlunda än den första tanken som slår en, har vi diskuterat kring detta med Melrose.
Han konstaterar som ett svar på hur DPM möter CLM-bitarna att verktyget, ”ger prestandainsikter och möjliggör problemlösning med sluten loop i realtid. Den ger en universell syn på prestanda, kommunicerad i ett begripligt affärsmått: timmar.”
Detta mått är lätt att förstå för medarbetare i frontlinjen och förvisso också för chefer och ger en grund för en lösning baserat på frågan: hur effektiviserar vi produktionen?
Generellt gäller i all problemlösning, tillverkningsprocesser inkluderade, att man måste ha insikter och relevant information för att kunna navigera och agera rätt. För att åtgärda flaskhalsar måste man exempelvis man veta vilka de är och var de uppkommer.
Med DPM, hävdar Melrose, kan företag identifiera rätt prestandaproblem och ge möjlighet för medarbetare i frontlinjen att vidta korrigerande åtgärder. Det hela kan också gå fort med initiala resultat på så lite som 90 dagar.
KAPACITET ATT DRIVA TRANSFORMATION I STOR SKALA
Allt detta är av stor vikt, inte minst i tider när digitaliseringstrenden börjar få fullt genomslag.
Att exempelvis få klarhet i hur mycket en transformations-investering är värd och därmed kunna validera den baserat på produktionsdata i realtid, låter onekligen också som en vettig åtgärd.
– Visst är det så, säger Melrose. Tillverkare anser att digital transformation är väsentlig, men ser ofta bara stegvisa förbättringar i motsats till storskaliga transformationsförbättringar. Vår nya ThingWorx DPM-lösning gör det möjligt för företag att ta itu med de mest värdefulla tillverkningsförbättringarna och lösa gemensamma utmaningar för att driva tillverkningseffektivitet och transformation i stor skala.
Han tillägger att med DPM kan företag:
- Identifiera rätt prestandaproblem för att öka effektiviteten
- Ge frontlinjearbetare möjlighet att vidta korrigerande åtgärder
- Få insyn i flaskhalsar, bakomliggande orsaker och de mest kritiska områdena att fokusera på för förbättring
- Mäta resultat med resultatdata för att säkerställa att åtgärder ger de önskade resultaten
- Uppnå snabb tid till värde och skalning, med initiala resultat på så lite som 90 dagar.
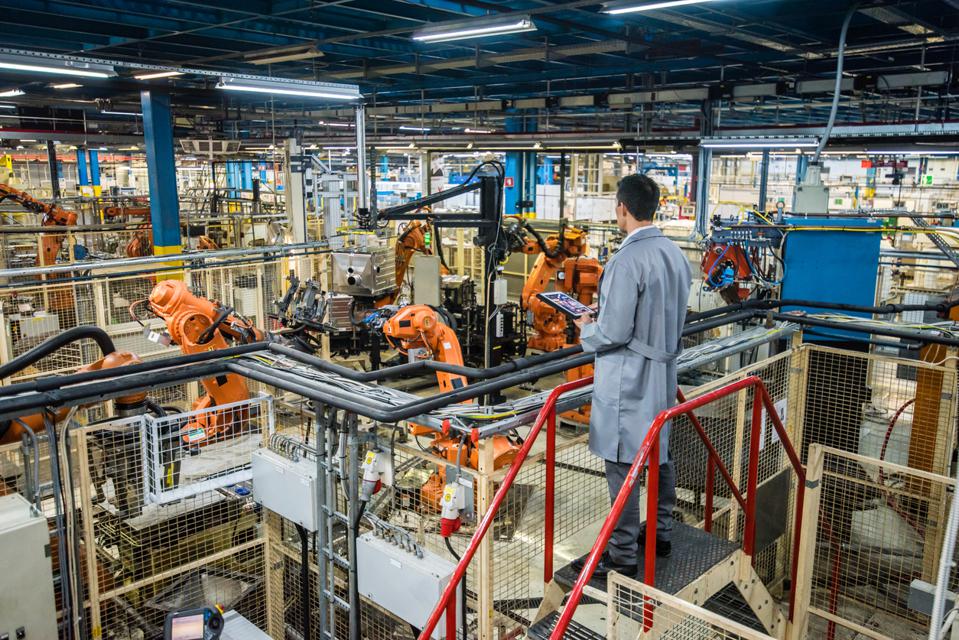
KONKRET PROBLEMLÖSNING PÅ EN DJUPARE NIVÅ
Detta sagt ska vi gå ännu djupare in i vad den lösning PTC nu lägger upp på bordet kan innebära. Craig Melrose ger oss ett exempel:
– Först och främst detta är detta ett system för att förstå och förbättra tillverkning eller genomströmning av produktionen i fabriker. Låt oss i detta sammanhang anta att en tillverkare har 50 fabriker i sitt företag. Den första platsen att använda DPM har 100 processer eller linjer i fabriken. DPM skulle i detta fall förstå effektiviteten och genomströmningen av hela fabriken för alla produkter/SKU’s (Stock Keeping Units) som går genom de olika vägarna och olika kombinationerna i de 100 processerna/linjerna. Låt säga att DPM fastställer, vilket programmet kan göra, att 10 av dessa 100 processer/linjer är begränsade eller har flaskhalsar. I detta läge bör en tillverkare bara fokusera på dessa 10 processer/linjer, eftersom endast förbättringar av flaskhalsar här kommer att leda till ekonomisk förbättring av P&L (Profits & Loss), antingen i form av kostnader eller produktion av ytterligare enheter. Nu när vi är fokuserade på dessa 10 processer/linjer, fördjupar DPM prestanda ur genomströmnings- och effektivitetssynvinkel och tittar på alla prestandaförluster, som planerade och oplanerade driftstopp, omställningar, hastighetsförluster, mindre stopp och annat.
Därmed, fortsätter Melrose, kan man fokusera på problemlösning av de viktigaste områdena och gå en nivå djupare in i pareto, där det senare begreppet står för att en ekonomi har sina resurser och varor allokerade till maximal effektivitet. Här kan man titta på sånt som omställningar, för att sedan gå ytterligare en nivå djupare för att förstå mängden tid, frekvens och att t ex sånt som förändringar från produkt A till produkt C kan vara det största problemet.
Allt detta bedöms nu utifrån att systemet har en enda gemensam måttenhet, som är absolut och intuitiv – alltså timmar. Därför redovisas och prestations-bestäms 100 % av alla timmar för en hel vecka (168 timmar).
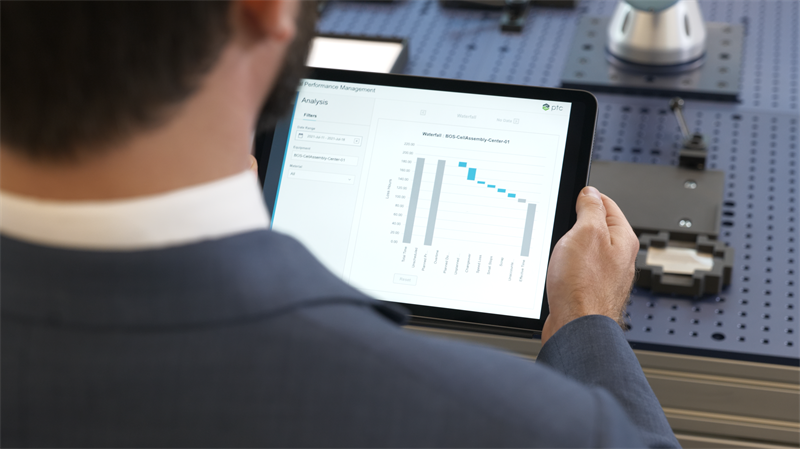
KAN ÖKA OUTPUTEN MED UPP TILL 20 PROCENT
Men detta är nu så att säga bara ena halvan av systemslingan. Den andra halvan handlar om förändringshantering och ansvarsförhållanden. Det betyder att när man nu vet vilka de 10 flaskhalsarna är och vilka förluster de genererar så kan företaget lägga in åtgärdspaket i DPM-systemets så kallade, ”action tracker”, för att se till att ansvarig medarbetare utför åtgärd X på Y-datum, med larm och ansvarsskyldighet.
– Alla åtgärder fångas och hanteras på en plats och flyttas sedan till ett ”scorecard”, vilket innebär en kontroll att de vidtagna åtgärderna förbättrar prestandan som förväntat. Sedan går man tillbaka till startpunkten för flaskhalsar och tar itu med nästa flaskhals.
På sista raden talar vi alltså om en helt sluten prestandaslinga som kommer att driva fram signifikanta förbättringar av genomströmningen i fabriken.
– Förbättringarna i genomströmningseffektiviteten kan ligga på 10 till 20-procentiga nivåer i bara i en fabrik, säger Craig Melrose, och tillägger att om man sedan inför och rullar ut DPM i hela företaget, så kan det handla om miljontals dollar när alla anläggningar utnyttjar DPM.
– Men det här nu inte bara en fråga om pengar, utan också om investeringar som leder till en sann digital transformation.
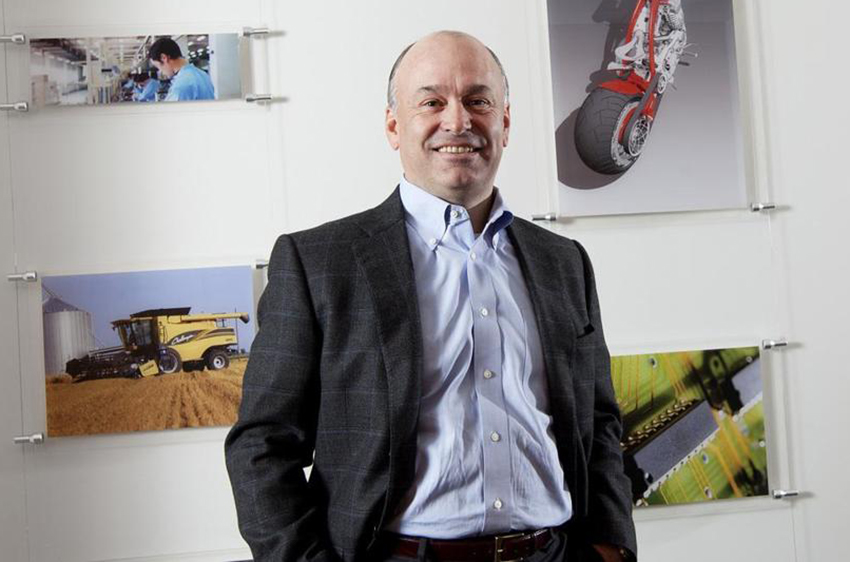
VAD SKILJER PTCs CLM MOT SIEMENS’?
Allt detta är bra och kapabla inslag i strävan mot att möta de utmaningar som ligger i att med ”closed loop manufacturing”. Men frågan är om man trots allt är först med detta. PLM&ERP News har tidigare rapporterat om Simens Digital Industries och deras CLM-lösningar, som allmänt ligger i ett PTC-liknande spår. Men det finns viktiga skillnader. Hur då, frågar PLM&ERP News PTC-chefen, Jim Heppelmann.
– När Siemens syftar på tillverkning i en sluten loop, hänvisar de till automations- och styrsystem, som verkligen är slutna loopar. Men DPM arbetar på en högre nivå, övervakar och optimerar hela produktionsprocessen över all automatiserad utrustning, gammal icke-automatiserad utrustning och alla medarbetare, som ju inte är automatiserade alls.
Heppelmann säger att DPM inte kontrollerar utrustning som en Siemens PLC gör.
– Precis, men den samlar in IoT-data och data om allt som händer, från användare. Vi talar om varje minut av användning och vår lösning redovisar all tid som spenderas i produktionsprocessen. På sätt och vis är det ett tidsredovisning-system. Det gör det möjligt för tillverkningsteamet att identifiera och lösa stora flaskhalsar.
Vad kan en sådan flaskhals handla om?
Det kan vara något i stil med att det tar för lång tid innan en medarbetare får nästa del han eller hon behöver och kan ladda den i maskinen; detta beroende på att t ex fabrikslayouten är ineffektiv (konfigurera om fabriken), eller att ett skiftbyte eller en inspektion tar för lång tid (kan vara åtgärdas via AR, Augmented Reality), eller att ett säkerhetsstopp utlöses för ofta (re-design av processen behövs), eller att en maskin ligger nere (prediktiv analys och underhåll). Denna förmåga att se över hela processen – inte bara den moderna automatiserade utrustningen – är extremt kraftfull och nödvändig och unik för PTCs DPM-lösning, hävdar PTC-chefen.
Craig Melrose håller med Heppelmann och summerar:
– Siemens’ och andras lösningar avser en sluten loop i en maskin och vanligtvis på maskinens sensorpaket och kontrollnivå, vilket begränsar fokus och inte optimerar över hela processer. Än mindre förstår människors påverkan och den pågående produktpåverkan av flöde eller brist på flöde genom fabriken.
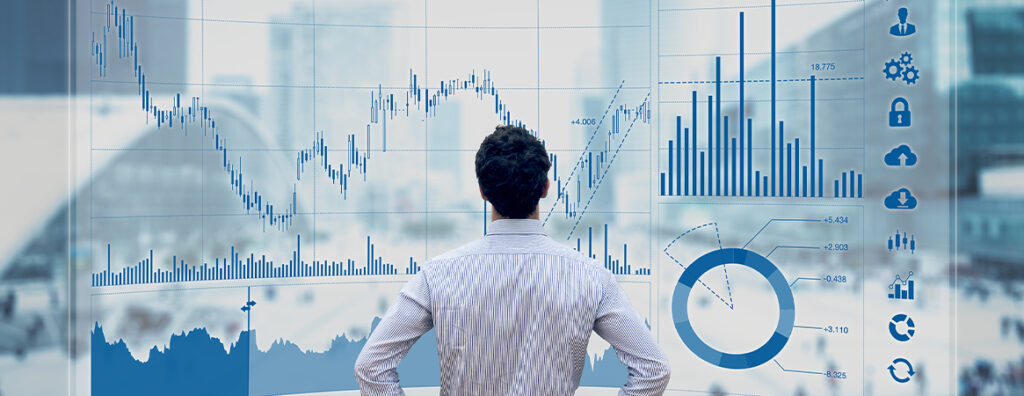
EN MILSTOLPE I PTCs IIoT-VERKSAMHET – MEN UTMANINGAR SAKNAS INTE
Men hur som helst hävdar PTC-chefen, Jim Heppelmann, att släppet av PTCs ThingWorx DPM-lösning representerar en betydande milstolpe i bolagets IIoT-verksamhet.
– Denna programvara markerar början på en ny fas i PTCs IIoT-tillväxtstrategi när vi utvecklar vår positionering av ThingWorx som en svit av kraftfulla företagslösningar som driver betydande företagseffektivitet för att skapa affärsvärde.
Att det är PTCs första sammanhållna lösning på området är klart. Likaså att det pedagogiska greppet att jobba med timmar som måttenhet är en spännande approach som förstås av de flesta inblandade intressenter i produktionskedjan. Men som sagt, det finns alltså andra spelare som hävdar att man redan har denna teknologi.
Hos konsulten Ernst & Young reagerar dock Jerry Gootee, “Global Advanced Manufacturing Sector Leader” med tummen upp på nyheterna från PTC gällande DPM:
– Absolut, säger han. Alla våra tillverkningskunder, oavsett bransch, står inför den ständiga utmaningen att identifiera och snabbt eliminera produktionsflaskhalsar. Marknaden behöver en skalbar teknologilösning som systematiskt och dynamiskt kan identifiera produktionsbegränsningar, prioritera bakomliggande orsaker, rekommendera och hantera korrigerande åtgärder och validera resultat mätt som nya produktionstimmar av kapacitet.
PTC:s nya ThingWorx DPM kan bli ett starkt svar på dessa behov av att eliminera flaskhalsar och öka produktionseffektiviteten i tillverkningen när vi går djupare in i digitalt drivna tillverkningsupplägg.
Men det är en komplex fråga, där utmaningen bl a ligger i att PTCs nya approach behöver en del förklarande, det ska vara lätt att begripa och inte vara förenat med allt för komplicerade implementations- och affärsmodeller. Allt ackompanjerat av snabba och lönsamma ROIer.
När allt kommer omkring är inte heller fabrikernas produktionseffektivitet den enda digitala utmaningen att ta itu med.
Men å andra sidan finns det mycket att hämta för den som får till det bra.