En snabb titt på marknaden avslöjar kostsamma satsningar
Men hur kostsamma satsningarna än är, är de totala investeringarna i PLM- och automation fortfarande en fråga om en relativt begränsad andel. De exakta investeringsstorlekarna är affärshemligheter, men en välgrundad gissning – baserad på listpriser och förväntade kundrabatter – är att PLM- och automationsinvesteringarna i Siemens Digital Industries PLM- och Closed-Loop Manufacturing-koncept i en gigafabrik lika stor som Northvolt Ones (40 GWh) ligger i intervallet 22 till 25 miljoner euro (mellan 260 till 300 miljoner kronor).
Av dessa gäller 1,9 miljoner dollar till 2,3 miljoner dollar för PLM-delarna (mellan 23 till 27 miljoner kronor), beroende på storlek och mer specifika detaljer i layouten. Detta medan automationsbitarna normalt ligger på en faktor 10 i förhållande till PLM-investeringarna. Automationsinvesteringarna landar alltså i allmänhet i intervallet 20 till 25 miljoner dollar (mellan 220 till 275 miljoner kronor).
I slutänden handlar det sålunda om stora pengar att tillverka litiumjonbatterier, som främst används inom bilindustrin. Detta underbygger i sin tur nödvändigheten av att etablera effektiva verktyg för att skala upp batteriproduktionen med digitala, sömlöst anslutna verktyg som täcker hela värdekedjan, menar Siemens Sinha.
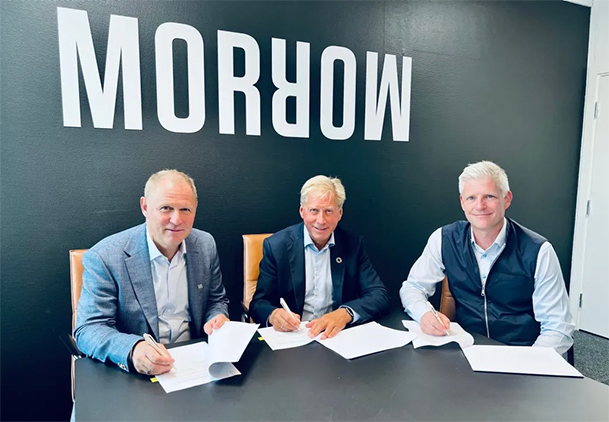
Digitala tvillingar i huvudroll
Så fördelarna med att skapa pålitliga virtuella versioner – digitala tvillingar – av produkter, processer, produktionslinjer och anläggningar, med iterativa distributioner av produktionsprocesser, är därför mycket stora, hävdar Puneet Sinha. Dessutom kan dessa satsningar göras utan de kostnader och risker som normalt är förknippade med att göra motsvarande i den verkliga världen.
– Precis, genom simulering i Siemens-miljöer, och inom ramen för Siemens Xcelerator-portfölj, kan ingenjörer enkelt täcka in flera domäner som spänner över kemi, mekanik, el/elektronik och mjukvara för att noggrant utvärdera inverkan av olika kemier gällande cellprestanda, cellsäkerhet och åldrande. De kan också optimera celldesignen för att maximera energitätheten och snabbladdningen. Genom att utnyttja Siemens digitala tvillingar kan de dessutom virtuellt validera celldesigner och beteenden mot paket- och slutsystemkrav. Detta frigör företag från kostsamma och tidskrävande testmetoder, förklarar Siemens seniora batteridirektör.
Starka kopplingar mellan produktutvecklings- och tillverkningsverktyg
Med det sagt kan noteras att industrins tillväxt drivs av ökande efterfrågan på litiumjonbatterier, främst för elektrifierade transporter och energilagring. Den höga efterfrågan på marknaden och trenden med statligt stöd till satsningarna i många länder skapar hård konkurrens mellan nystartade företag, joint ventures och redan etablerade företag.
Att vinna framträdande marknadspositioner i detta kräver mycket. Både för nya aktörer och etablerade leverantörer, som också står inför samma utmaningar när det gäller hur man kan minska uppskalningstiden, minska mängden skrot och maximera genomströmningen, samtidigt som ökningen uppfyller målen för kostnad, kvalitet och hållbarhet. Kort sagt, traditionella tillverkningsmetoder kan inte uppfylla dessa ambitioner, hävdar Siemens Sinha.
Han menar här att Siemens har en stark fördel i sambanden mellan produktutveckling och automationsverktyg.
– Korrekt, det företag som vill skala upp produktionen kostnadseffektivt och ta en ledande marknadsposition behöver ett digitalt ramverk för produktutveckling och tillverkning, där produktionens digitala tvilling kopplas till verklig fysisk fabriksverksamhet genom automationsteknik och där industriell IoT (IIoT) är aktiverat. Detta möjliggör i sin tur digital design och optimering av produktionslinjen och validering av produktionsprocesser inför implementering på fabriksgolvet; vilket minskar investeringsrisken och förkortar skaleringstiden. Att koppla ihop det digitala ramverket med automationshårdvara och mjukvara, samt industriell IoT, underlättar en övergripande integration av produktionen.
Enligt Sinha ger detta insikter om åtgärder och upplägg för att förbättra produktionskvaliteten och upprätthålla bästa praxis för tillverkning, allt i akt och mening att minska skrothastigheten och maximera produktionsgenomströmningen, samtidigt som processhållbarhet och lönsamhet balanseras på lång sikt.
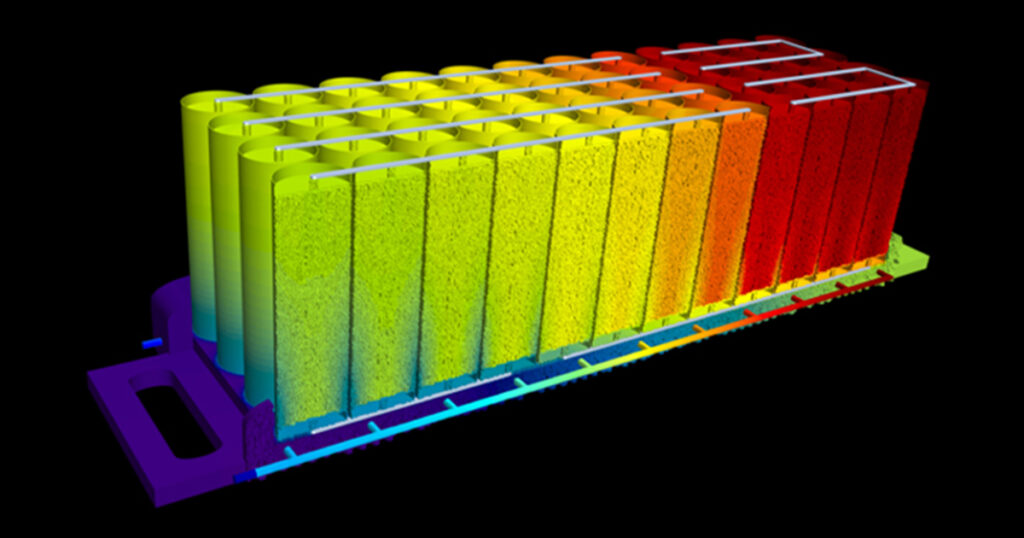
Simulering av primär betydelse
Utan tvekan är design- och simuleringsområdena av primär betydelse i detta. Ett uppkopplat arbetsflöde av Simcenter Amesim och Star-CCM+ är ett bra exempel. Lösningarna stöder ingenjörer i digital validering av Li-ion-cell- och packdesigner tack vare detaljerade cellgeometriska specifikationer, simulering av elektrisk och termiskt beteende. Omfattande komponenter i en battericell finns tillgängliga, såväl som en materialdatabas för att stödja modellutveckling.
Dessutom har Simcenter-portföljen flera nivåer av prestandamodeller: en fysikbaserad makrohomogen modell för att få insikter i cellens elektrokemiska mekanismer, och en likvärdig RCR-kretsmodell (”Replacement and Cross Reference chart”), som är ett empiriskt tillvägagångssätt för att modellera cellens beteende på ett beräkningsmässigt mycket effektivt sätt. Puneet Sinha kommenterar saken så här:
– Användning av simuleringar, cellteknik och optimering påskyndar utvecklingstiden radikalt, säger han och påpekar också att detta bekräftar vikten av att använda digitala tvillingar. ”Med Siemens-simuleringar kan ingenjörer noggrant utvärdera inverkan av olika kemier ifråga om cellprestanda, cellsäkerhet och åldrande och kan optimera celldesign för att maximera energitätheten och snabbladdningen. De kan virtuellt validera celldesigner och beteenden mot paket- och slutsystemkrav genom att utnyttja Siemens digitala tvillingar. Detta frigör företag från kostsamma och tidskrävande testmetoder. Vi ser att man kan snabba upp accelerationen i batteridesign och konstruktion med upp till två till tre gånger när företag tar upp vårt digitala tvilling-ramverk. Med en robust PLM-ryggrad, produktens digitala tvillingar och med detta sammankopplat till fabriksanläggningen, blir det möjligt för företag att överväga de ömsesidiga beroendena och effekterna av förändringar under hela livscykeln.”
Den digitala tvillingen som nyckelkomponent
Enligt Puneet Sinha är den digitala tvillingen en nyckelkomponent, inte minst relaterat till den snabba utvecklingen av materialkemi, celldesign och tillverkningstekniker. I sammanhanget pekar han på ett kundexempel där man genom att etablera Siemens digitala tvilling-ramverk har kunnat förkorta den tid det tar för battericeller att gå från laboratorietillverkning till storskalig produktion, samtidigt som de uppfyllt hållbarhetsmålen och sina egna unika krav.
– Att koppla samman industriell IoT och automationsteknik med tillverknings-exekverings-system och en digital tvilling av produktionsanläggningen är av grundläggande betydelse i datadriven tillverkning, hävdar han.
Klart är också att tillverkning av li-jonceller är en synnerligen komplex process som involverar cirka 600 process-egenskaper, som olika maskinparametrar.
– Med tanke på mängden data och det komplexa ömsesidiga beroendet mellan olika tillverkningssteg i en typisk cellproduktions-process behövs AI (Artificiell Intelligens) för att förstå samspelet mellan de olika stegen och för att kunna lära sig av interaktionen mellan produkt-/processpartnerna”, säger Sinha och tillägger: ”Typiska användningsfall involverar, men är inte begränsade till, kvalitetskontroll av produktionslinjen, datorseende för att mäta viskositet och beläggningsdefekter, men också förmåga att kunna förutsäga cellens beteende under bildnings- och åldringsprocessen. Integration mellan batterispecifik IT (informationsteknologi som MES, moln etc) och OT (driftsteknologier som PLCer, enheter etc), datainsamling från maskiner och gigafabriker i samband med produktionsprocess och analys är avgörande möjliggörare för att förbättra produktionskvaliteten och genomströmning.
Han betonar också att industriell IoT och datadriven verksamhet gör det möjligt för företag att spåra energiförbrukning och optimera fabriksdriften för att minska sitt koldioxidavtryck.
Ett annat värde är att olika former av stillestånd i fabriken kan minskas genom prediktivt underhåll av maskineriet, vilket förbättrar den totala produktionsgenomströmningen.
Avfalls- och skrotningsproblemet
En av de största utmaningarna för storskalig produktion är höga halter av avfall. Även här, tror Sinha, kan det digitala tvillingramverket kopplat till automationsteknik och IOT spela en viktig roll. Hur då?
Bakgrunden är att tillverkning av battericeller involverar olika steg som bläckblandning, elektrodbeläggning, kalandrering till bildning och åldring innan celler går igenom kvalitetskontroll. Även små fel i de olika stegen kan leda till dålig kvalitet på celler. De avvisade elektrodrullarna leder till ökning av tillverkningskostnaden och sänkning av produktions-genomströmningen. Majoriteten av celltillverknings-metoderna bygger på många års erfarenhet från få företag, vilket är extremt svårt att replikera i nya företag som precis har börjat sin produktion. Även i de ”rutinerade” företagen kan det vara tufft att översätta med förändringar i batterimaterial. Därför förlitar sig företag ofta på prov- och testmetoder för att justera sin produktion, vilket är kostsamt och ineffektivt. Siemens Sinha igen:
– Vi har sett nivåer som var 40 % eller högre i början av cellproduktionen, medan det i de flesta fall är strax under 10 % när produktionskapaciteten nått full fart några år efter produktionsstart. Det är viktigt att få ner dessa nivåer, att produktionskostnaden sjunker, konstaterar han och tillägger:
– För att minska avfallsnivåerna och samtidigt uppfylla kvalitetsmålen för tillverkning av Li-jonceller krävs insikter om utförande på fabriksgolvet. Jag tror att integrerad hårdvara och mjukvara för end-to-end-produktionsprocessen är nyckeln i detta för att förbättra cellproduktionen. Det möjliggör digital kontinuitet från validerade processplaner till papperslöst produktionsutförande. Tillverkning av exekveringsmjukvara kopplad till automationshårdvara genom ett SCADA-lager gör det möjligt för tillverkningsteam att enkelt orkestrera storskalig produktion och genomdriva önskade produktionsmetoder. Detta är möjligt genom integrationen n av IT och OT som möjliggör spårning och maskinintegration för att snabbt identifiera och åtgärda problem.
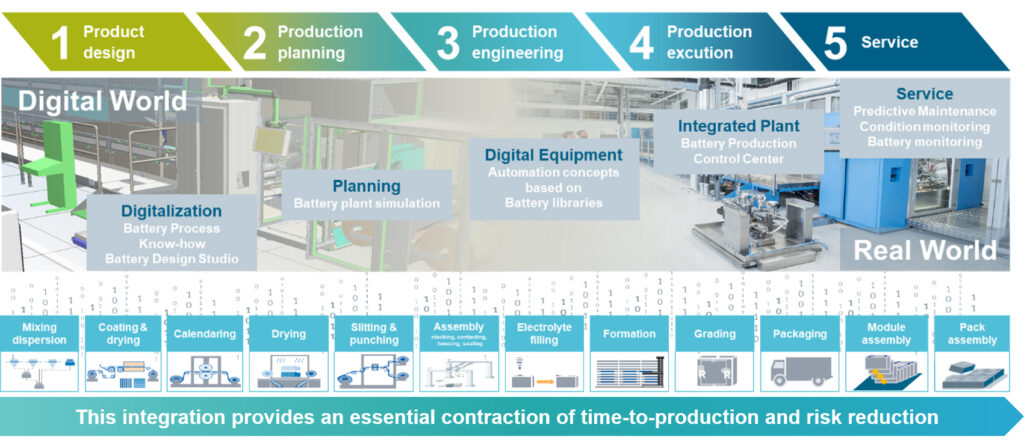
Hemligheten bakom att bli en marknadsvinnare
Hur blir man då en vinnare i den extremt snabbt växande batteribranschen?
Puneet Sinhas korta svar är: ”Omfamna smart design- och tillverkningsmetodik.”
För att lyckas med detta är det framför allt nödvändigt att fullt ut utnyttja uppkopplade digitala verktyg:
– Precis, jag brukar säga att man ska flytta till vänster i den traditionella utvecklingssekvensen. Simulera och validera digitalt innan verksamheten påbörjas. Se också till att skapa en enda källa till sanning för cell, pack, maskiner och fabriksdefinitioner och utveckling med en robust PLM-ryggrad. Det minskar tiden för att sprida tekniska förändringar och möjliggör en motståndskraftig leveranskedja. Med integrerade hårdvaru- och mjukvarulösningar, som ger verkställande insikter för end-to-end-produktion, vilket möjliggör minskning av skrothastigheten och förbättrad kvalitet.
Batteribranschens ambition är att kostnadseffektivt skala produktionskapaciteten 10X under åren fram till 2030.
– Att göra allt detta hållbart och lönsamt på lång sikt kräver att företag minimerar energiförbrukningen, begränsar det holistiska koldioxidavtrycket, bibehåller synlighet över produktionen och förutsäger problem innan de inträffar, avslutar Siemens seniora chef för batteriindustrin.