The success factor lies in combining materials
The most important success factor for the project has been to combine the properties of two different materials in the composites.
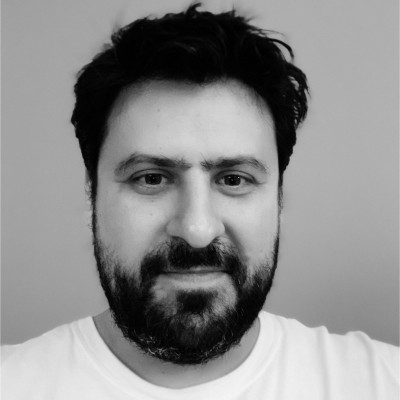
”We have to keep the porous structure of the graphene and also crush it to the designed size. Surface properties are important for the distribution of graphene flakes inside the PU foam. We tried many different methods to modify the surface of the flakes,” says Flavio Presezniak (on the picture to the left).
Regarding the background and tools used in the context of what has been done so far Presezniak said to PLM&ERP News:
”The results are based on a Kundt’s tube material test and on the Biot parameters estimation and show the material performance only. These methods help in predicting how any material will behave acoustically, including how it will absorb, reflect, or transmit sound. Tests or simulations on the complete vehicle have not yet been conducted.”
Going forward, the plan is to further develop and optimize the technology further to apply in a product to be tested in vehicle conditions.