Intelligenta maskiner är nyckeln i Meveas verksamhet, konstaterar Nikkilä från talarstolen under bolagets senaste årliga användarevent i finska huvudstaden Helsingfors, inför ca 250 deltagare från hela världen.
Men vad är en intelligent maskin? Definitionsmässigt talar han om maskiner utrustade med sensorer, sändare/mottagare, mjukvara och kontrollboxar (styrenheter). För att göra det ännu klarare jämför han med SAE J3016-skalan för självkörande fordon. Den går lite grovhugget i en skala 1-5 från ingen autonomi alls – helt operatörsdriven – till full självdrift.
– Intelligensen i sig själv är inte det viktiga. Det är istället intelligensen som ett hjälpmedel att förbättra människa-/maskininteraktionen och de kvalitativa och kvantitativa resultaten. Skulle man översätta SAE J3016-skalan till intelligenta maskiner skulle det kunna se ut så här, säger Nikkilä:
”1. Ingen automation. 2. Maskinkontrollsystem 3. Operatörsassistens-system 4. Uppgifts- och arbetscykelautomation. 5. Full- eller semiautonom drift.”
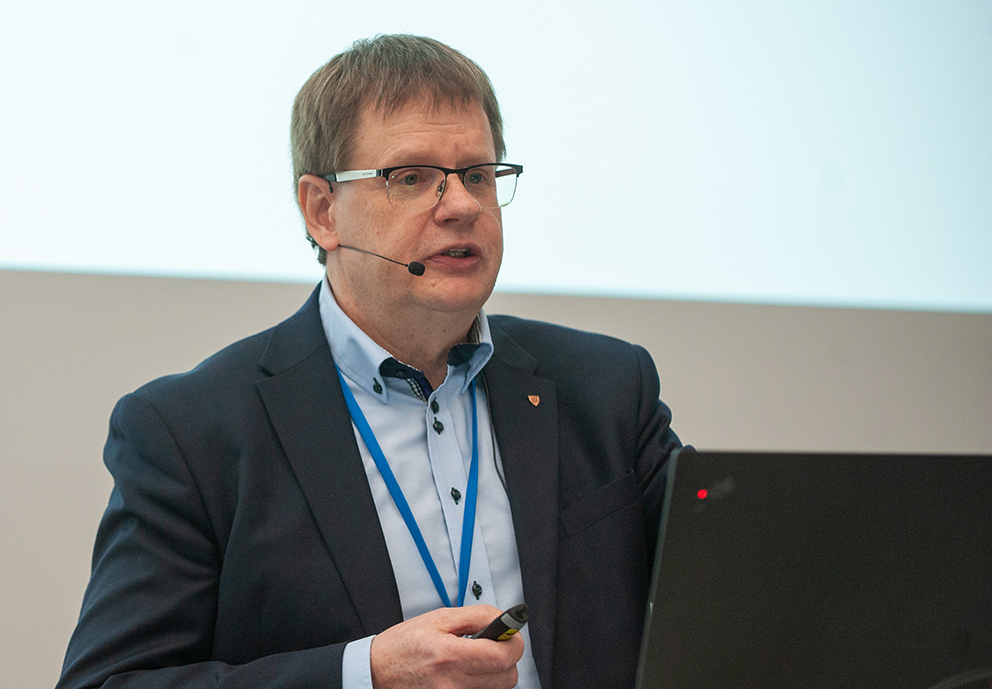
Mevea och den autonoma grävmaskinen
Enligt en sådan skala har Mevea avancerat längre än de flesta utvecklarna. Hur då?
Vi tar en autonom grävmaskin som ett exempel: vad man gjort är att ta fram en lösning som i realtid kan kombinera fysisk hantering med digital simulering via insamling av operationella data. Med detta som grund kan simuleringslösningen skapa de insikter som krävs för att bygga upp allt ifrån fristående träningssimulatorer till lösningar med semi-autonomi.
Raimo Nikkilä exemplifierar med vad bolagets lösning kan göra med just en grävare för att skapa intelligens:
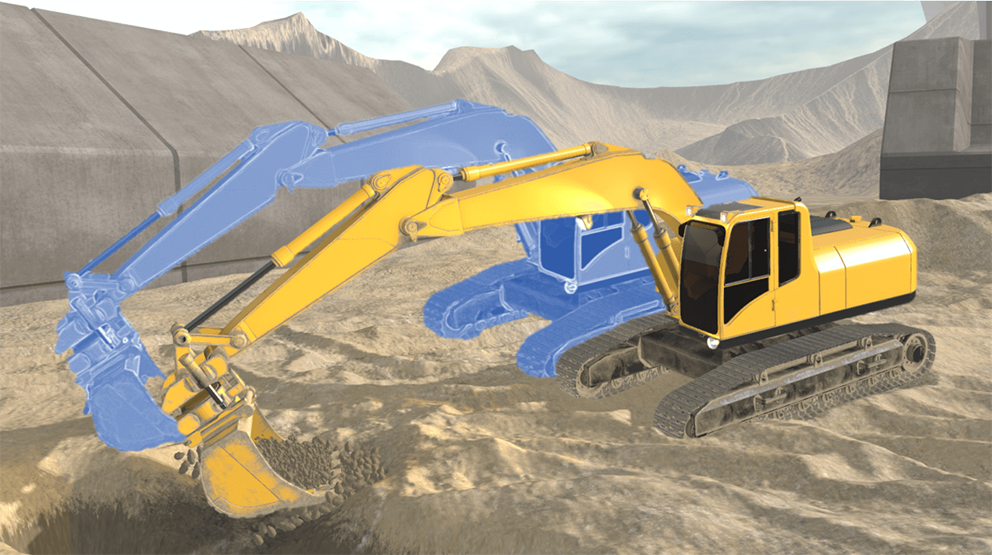
- ”Operatören använder Mevea-systemet för att skapa mönster i vad man vill att grävmaskinen ska göra
- Efter ett par cykler lär maskinen sig hur momenten ser ut och kan själv repetera de ingående delmomenten, vilket i detta fall beskrivs som en slags intelligens
- Katalysator och möjliggörare av denna arbetscykel-automation är den digitala tvillingen.”
– Utöver detta kan operativmiljön enkelt sättas in i den fysiska miljön där grävmaskinen ska jobba, säger Meveas marknadsdirektör. Detta kan göras via en virtuell modell av terrängen där den ska verka. Ett exempel kan vara att man med en drönare utrustad med en fotogrammetri-lösning fångar terrängen i ett stenbrott eller byggnadsområde. Detta gör det möjligt för ett företag att noggrant planera för exempelvis en grävmaskin, innan den placeras i sin verkliga arbetsmiljö. Det ger operatören möjlighet att öva och testa i den virtuella miljön och på så vis ”interagera” med den verkliga världen.
Vad skiljer Medea från de traditionella CAD-lösningarna?
Potentialen är sålunda stor och Raimo Nikkilä menar att det inte är några tillfälligheter att man blivit uppmärksammade av allt större aktörer.
– Det finns idag en hel del som skiljer oss från de ”traditionella” CAD-leverantörerna, påpekar han. De flesta av dessa kan inte erbjuda den arbetsprocess- och interaktiva miljö som vi kan. Att koppla ihop de här bitarna är helt enkelt mycket svårt.
Samtidigt finns det mycket att hämta i produktivitets- och utvecklingshänseende:
– Så är det, vi har kunder, som t ex Mitsubishi, som har plockat hem så mycket som 25 procent på utvecklingstiden, medan andra, som finska utvecklaren av pålningsmaskiner, Junttan, var klara för virtuella maskintester ett halvår innan den fysiska maskinen var klar; med åtföljande tidsvinster ifråga om leverans av den färdigbyggda fysiska maskinen, konstaterar Raimo Nikkilä.
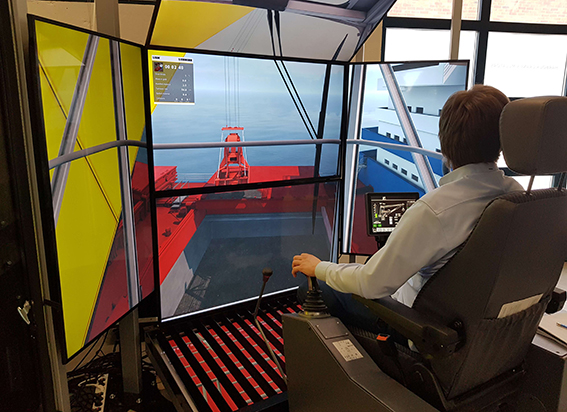
CASE: Liebherrs Smart Grip-system
Att en utvecklare av digitala tvillinglösningar själv påpekar de här bitarna ligger i sakens natur. Men vad tycker kunderna? Under Mevea-eventet presenterades en rad goda exempel på gjorda vinster med digitala tvillingar, ett faktum understryker trovärdigheten.
Österrikiska verkstadsjätten när det gäller skeppskranar, mobila hamnkranar, offshore-kranar, bandkranar och lastcykelkranar, Liebherrs Christian Schneider, produktansvarig för digitala lösningar och konsultationer, berättade t ex att man i dagsläget globalt har 26 simulatorer installerade.
– Vi har tillsammans med Mevea utvecklat en skeppskransimulator. Kranen används bl a används för att lyfta över enorma kolkvantiteter från gigantiska hamnbehållare till ett lastrum i ett transportfartyg. En nyckelfunktion i kranens kontrollsystem har vi kallat för ”Smart Grip”.
Detta är ett kontrollsystem som styr en kranskopa. Tidigare klarade operatören och kranen, med en kapacitet på 12 ton per lyft, av att med 30 lyftcykler per timme föra över 360 ton kol från punkt A (hamnbehållaren) till B (lastrummet) på transportskeppet.
Här har man nu byggt en komplett digital tvilling/3D-modell av kranen och den omgivande miljön. Grafiken är alldeles utmärkt och alla joysticks för styrning av kranen ger realtidsutslag, inklusive svängningar som uppstår om rörelserna är för snabba.
– Genom Smart Grip-systemet har vi nu optimerat kollastningen och lyckats öka antalet ton per timme till 600. Via en skärm ”displayas” en rad värden under varje lyftcykel, med detaljer som visar hur lyften ser ut och vilka värden som kan förbättras relativt prestandagränserna för kranen, säger Christian Schneider och tillägger att, ”simulatorn försäkrar oss om att operatören gör rätt saker”.
Han berättar också att resultaten varit så uppmuntrande att man planerar för digitala tvillingar a la Mevea över hela Liebherrgruppens system.
– Vi har också redan börjat använda lösningarna i produktutvecklingsarbetet. Innan vi går över till att tillverka maskinerna testar vi maskinfunktionaliteterna i simulatorn.
– I framtiden ser vi helt fjärrstyrda lösningar, via digitala tvillingar, som en fullt möjlig option, summerar Christian Schneider.
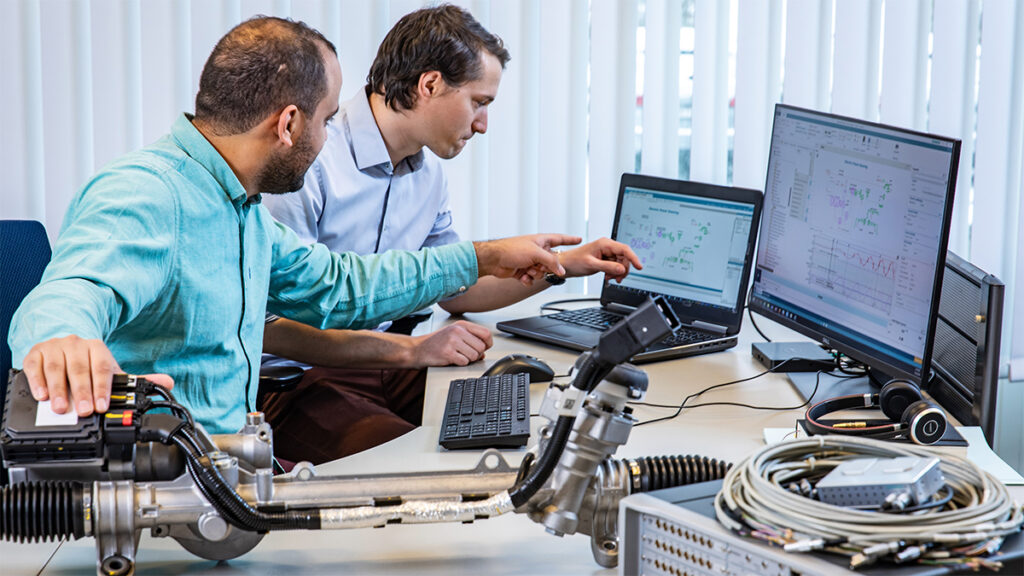
Spelar väl ihop med Siemens syn på digitala tvilling-kocept
En intressant aspekt på Meveas syn på utvecklingen av digitala tvillingar är att det finns en hel del likheter med PLM-ledarens, Siemens Digital Industries, syn på upplägget kring digitala tvillingar. Man har tittat på tvillingkonceptet relaterat till tre områden eller aspekter, där ”tvillingen” kan aktivera olika bitar beroende på vad som ska hanteras. Varför? Ett bra skäl är att man inte behöver låta tvillingen tyngas ner av data relaterat till tillverkningsprocessen när produkten är i drift. Man delar därför upp det hela i tre faser:
- Ideation – ”en tvillingaspekt” för produktens skapelseprocess och produktutveckling
- Realisering – en aspekt för produktens tillverkningsfas med kopplingar till en digitalt styrd tillverkningsprocess
- I drift – ”en tvilling” för produkten hos slutanvändaren, med återmatningsfunktioner till PLM.
Detta spelar tämligen väl ihop med Meveas tankegångar kring konceptet med digitala tvillingar. Inte minst relaterat till de lösningar som utvecklats, där man kopplar tvillingen till tunga maskinerna i drift – det må vara grävare, lastare, kranar, pålnings- eller skogsmaskiner, etc – via deras styrenheter (ECU)/kontrollboxar.
Man har som sagt också ett utvecklat samarbete med Siemens, inte minst Siemens Cranes, som alltså valde att satsa på Meveas lösningar istället för på en ”in-house-lösning”; vilket förstås säger något om den finska lösningen.
På Meveas användarkonferens framträdde dessutom Siemens Gunnar Latz opch talade kring temat produktutveckling och digitalt utvecklingsarbete baserat på simulering; allt i skenet av varianthantering, lokala regleringar och den ökande mjuk- och hårdvarukomplexiteten när det gäller sånt som autonoma och elektrifierade tunga maskiner typ entreprenadmaskiner. Latz berättade att man i detta utvecklar ett interface mot Meveas omfattande meknik- och kontrollsystem.
– Fördelarna med detta är flera, sa han, inte minst när det gäller design av nya maskiner, tidiga arkitekturanalyser och virtuell access kring systeminteraktion.
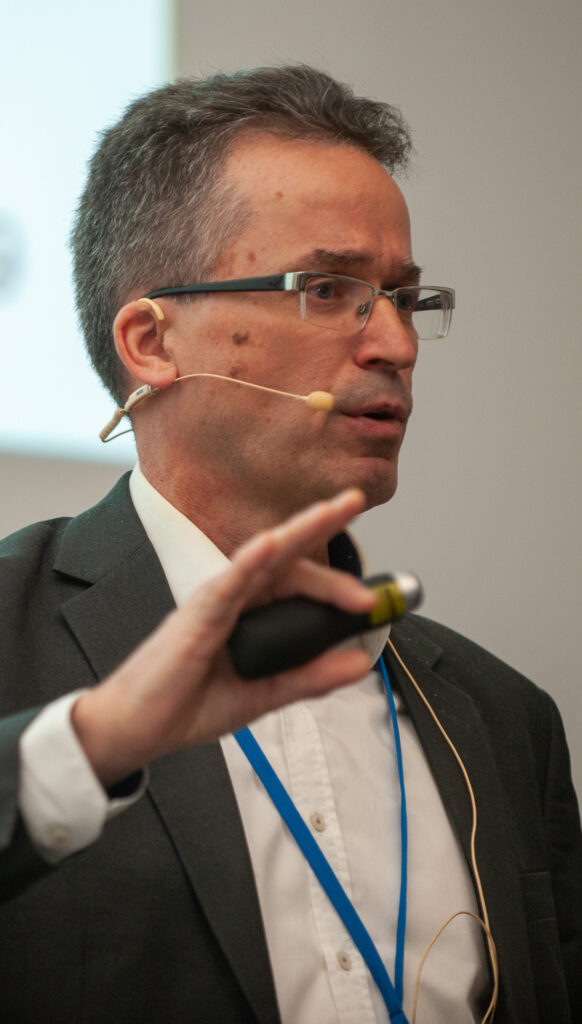
Beröm från respekterad analytiker
Vi ska också notera att Mevea fått mycket beröm för sina lösningar från respekterade analytikern CIMdata. Man beskriver i samband med en utvärdering att det Mevea tagit fram är, ”en end-to-end-metod som tar den verkliga fysiska världen in i den digitala genom att spänna över hela livscykeln, vilket möjliggör simulering av de olika fysiska effekterna från multi-kroppsimulering, över ”Hardware-in-the-Loop” (HiL) och ”Software-in-the-Loop” (SiL) till ”Human-in-the-Loop” (HuiL).”
Som PLM&ERP News noterat i en tidigare artikel finns det inga bra översättningar till svenska av ”in-the-loop-uttrycken”. Men en allmän beskrivning av betydelsen är att exempelvis ”Hardware-In-the-Loop” handlar om simulering som en systematisk metod för att testa funktioner, systemintegration eller kommunikation i elektroniska styrenheter (ECU) oavsett om det gäller fordon, robotik, flygsystem, automatisering eller medicinsk teknik. Metoden bygger på att så mycket som möjligt av det styrda systemets mekanik, sensorer och ställdon simuleras. När ECU:n styr det simulerade systemet kan man t ex medvetet ”injicera” fel för att testa att ECU-diagnostiken fungerar som förväntat. Samma sak gäller då motsvarande för SiL och HiL med skillnaden att det gäller andra saker som simuleras.
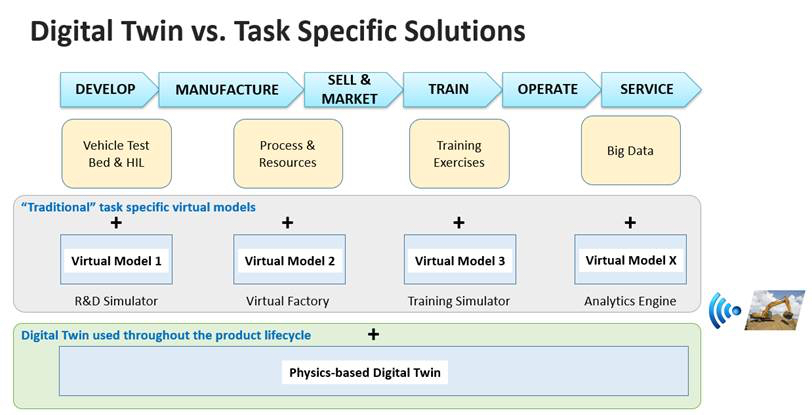
Simulering i realtid
Med sina realtidssimuleringsmöjligheter har Mevea tagit fram en digital tvillinglösning som har de grunder som behövs för att interagera direkt mellan den digitala modellen och den verkliga, fysiska modellen.
Raimo Nikkilä menar att bolaget i detta bidrar till att skapa intelligens i maskinerna och det är här man sedan skapar möjligheter för Meveas Digital Twin-lösning, framför allt i följande tre faser:
- Produktutveckling och innovation: Produktivitet, säkerhet, energieffektivitet och användarupplevelse driver områden som automatisering och elektrifiering/hybridisering
- Träning: Intelligenta maskiner behöver fler och mer kvalitativa utbildningsinsatser och typiskt produktutveckling Digital Twin används i träning
- Forskning och utveckling: Företag behöver ny typ av ingenjörer (inte silos och disciplinutbildade personer, men sådana som förstår värdet av interaktion och tvärdisciplinära systeminsikter); digitala tvillingar är mycket bra för att skapa dessa insikter. T ex kan man tänka sig att byta hydraulik-, mekanik- eller programvara i en maskin och sedan uppleva påverkan för arbetsprocessen med hjälp av en digital tvilling.
Stor potential över hela produktlivcykeln
Men vid sidan av detta kan man diskutera om inte den största potentialen i bolagets lösningar ligger i just detta med att kontinuerligt kunna övervaka och styra maskiner under drift och jämföra dess faktiska prestanda med den digitala tvilling som etablerades under produktutvecklingen. På så sätt går den vidare till nästa steg i sin livscykel, samtidigt som den digitala tråden bibehålls. Denna förmåga kan ge Meveas användare möjlighet att reagera snabbt och exakt på förändringar, vilket CIMdata menar, ökar deras konkurrenskraft.
Digitala tvillingar kan beskrivas som simuleringsmodeller av en fysisk produkt, maskin eller produktionslinje. Dessa modeller är tänkta att vara identiska med dels den fysiska produktens egenskaper och funktion, dels den miljö produkten ska användas i.
I princip finns det inga hinder för att en digital tvilling kan användas i alla moment av produktens hela livscykel, från produktutveckling och produktionsplanering till eftermarknad.
På Meveas användarseminarium konstaterade CIMdatas Frank Popielas, att, ”digitala tvillingar kan användas i alla produktutvecklingsskeden. T o m i konceptskedet. Men den tidpunkt när vi egentligen mest och bäst ser den digitala tvilllingens värde är när en produkt och en process knyts till en fysisk tillgång.”
Det är en konklusion som i högsta grad talar Meveas språk.