Biltillverkare tillverkar vanligtvis de flesta av kärndelarna och komponenterna i sina motorer internt. Vevhus, vevaxel, cylinderhuvud och vevstakar svarvas, frästas, borras, slipas och slipas på sofistikerade produktions- och överföringslinjer i anläggningar som BMW Motoren GmbH, den största motorfabriken inom BMW Group, i Steyr, Österrike. För detta ändamål använder tillverkningsingenjörer i hela koncernen Tecnomatix-portföljen från Siemens för anläggningssimulering.
Med hjälp av Plant Simulation-lösningen i Tecnomatix-portföljen designas och simuleras kompletta produktionslinjer med verktygsmaskiner och robotceller, men också materialhanterings- och transportsystem.
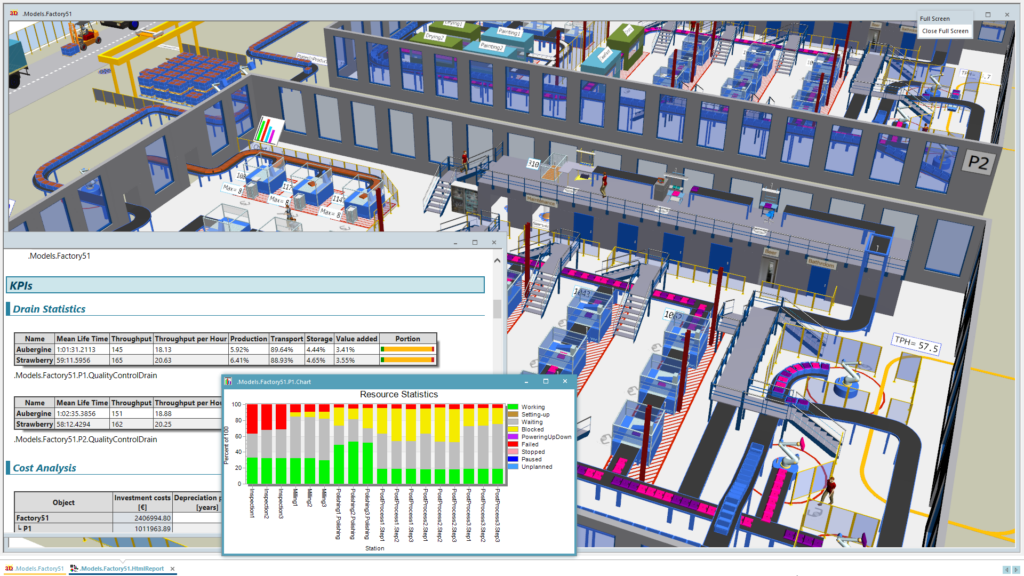
En del av Siemens PLM-portfölj Xcelerator
Vi ska börja med att notera att Plant Simulation-modulen ingår i Siemens PLM-portfölj Xcelerator, där Teamcenter är dataryggrad för produktdata och där Tecnomatix är den del som stöder hanteringen av digital tillverkningsstyrning. I Xcelerator finns allmänt en rad sömlöst kommunicerande appar som knyter ihop helheten i toppmodern produktframtagning. Detta i allt från de initiala kravspecarna kring en produkt, via designverktyg från CAD (NX), produktsimulering (Simcenter), elektronik- och mjukvarudesign (t ex Capital och Polarion) till tillvekningsrelaterade mjukvaror som just Tecnomatix.
Med de senare verktygen har man utmärkta möjligheter att vässa och energioptimera produktionsprocessen genom att t ex om-arrangera layouterna på fabriksgolvet. Finessen är att göra detta digitalt istället för fysiskt. Genom att simulera tillverkningsarrangemangen digitalt, kan man utan dryga kostnader se till att nå de optimala strukturerna i en rad olika perspektiv. Förutom att ha med energiåtgång som en parameter kan man plocka in flera andra som exempelvis kan påskynda produktionscyklerna och spara investeringskostnader genom optimerat verktygs- och maskinutnyttjande.
Men det finns mera ur miljö- och kostnadssynvinkel som kan miljövässa produkter och produktion ännu mer, som Siemens DIS nordenchef, Mats Friberg påpekar:
– Absolut, vi ju också i vår Costing Solution en databas med all CO2-data för material och komponenter, vilket gör att våra användare även denna väg både kan välja energioptimala komponenter och ifråga om CO2-utsläpp framställningsmässigt lågemitterande material till sin design, alternativt konstruera energieffektivt.
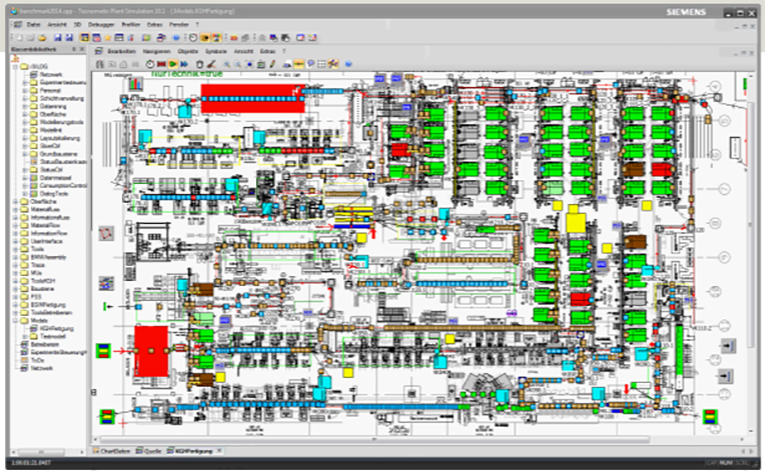
Allmänt för Plant Simulation-lösningen i Tecnomatix-portföljen är att den är mycket vanlig bland tyska fordonstillverkare, bland annat för att den innehåller en sats med drivlinsdelar, som utvecklats av den tyska biltillverkarnas förening Verband der Automobilindustrie e.V. (VDA). I BMWs Steyr-anläggning för motortillverkning används den för planering av såväl personal som maskiner och täcker 100 procent av anläggningen.
Att optimera energieffektiviteten utan extra kostnad
En annan sak som har förändrats dramatiskt de senaste åren är antalet versioner där bilar finns tillgängliga. Det som tidigare var massproduktion har allt mer kommit att handla om en verksamhet baserad på anpassad konfiguration. Det finns också ett mycket större utbud av motorer, med en trend mot lägre volymer och färre cylindrar till följd av bränsleeffektivitets-överväganden, som underlättas av avancerat motordesign-stöd.
Till saken hör vidare att fler versioner av samma principlösning innebär lägre kvantiteter av varje. Samtidigt vill ingen tillverkare att introduktionen av en ny komponent kräver att man skapar en ny produktionslinje. Istället upprätthåller man kapabiliteten i befintliga produktionslinjer så långt som möjligt för att klara förändrade krav. I de mest avancerade produktionstekniska lösningarna kan man t o m klara detta genom att byta ut eller lägga till påkopplingsbara nya enheter, som exempelvis nya eller starkt förändrade bearbetningscentra.
Något av denna senare problematik mötte BMW-ingenjörerna i Steyr-fabriken. Så här beskrivs saken i fallstudien från Siemens: ”För två år sedan i Steyr hade en linje som tillverkade vevhus modifierats för att hantera en växande efterfrågan på mindre motorer. Många nya bearbetningscentra tillkom. Högtryckspumparna i källaren behövde möta denna nya utmaning för att kunna leverera tillräckligt med kylande smörjmedel. Samtidigt användes inte utrustning avsedd för komponenter för 6-cylindriga motorer inom produktionslinjen.”
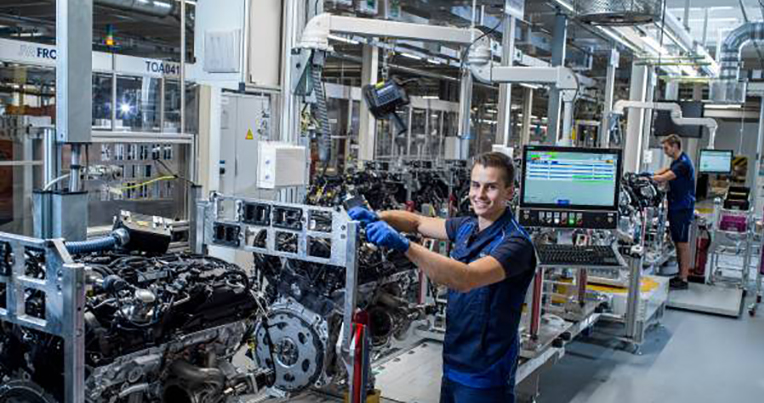
Ny version av Plant Simulation banade väg
Ungefär samtidigt blev en ny version av programvaran Plant Simulation tillgänglig, med nya funktioner för energianalys. I detta utökades det traditionella användningsområdet för simuleringsmodeller av anläggningar för att optimera genomströmningen, lindra flaskhalsar och minimera pågående arbete.
”Programvaran är tillgänglig utan extra avgifter i alla licenskonfigurationer och tillhandahåller dialogrutor för att ställa in wattvärden för olika driftlägen, såsom drift, installation, drift, standby eller ”av” för alla simuleringsenheter, såväl som den tid som krävs för ändras från ett tillstånd till ett annat,” skriver man.
Därmed kan simuleringsmodellen användas för att avslöja lastobalanser, optimera individuell maskinanvändning eller effektivisera reservdelslogistiken. Siemens hävdar här att med denna funktion kan energibesparingar vara lätta att uppnå, ”eftersom även enkla åtgärder, som att aktivt gå över till standby istället för att invänta timeout, ofta visar anmärkningsvärda resultat.”
Vartefter relaterad personal i Steyr-anläggningen lärt sig den nya mjukvarufunktionaliteten stod det snabbt klart för motorprocessteknik- och simuleringsexperterna här att detta borde göra det möjligt för dem att överföra beprövade energisparstrategier, som den automatiska start-stopp-funktionen, till fabriksgolvet.
Modifieringar av PLCerna
När man gjort modellen av den befintliga produktionslinjen i Plant Simulation var allt som krävdes för att få en relevant energisimulering att kartlägga informationen om strömförbrukningen för varje maskin i linjen med produktionsstegen i processtyrnings-systemet, och att lägga till det som en lista till den befintliga simuleringsmodellen.
Eftersom funktionen för energisimulering är en standardfunktion i Tecnomatix-paketet tog det för ingenjörerna på Steyr bara två veckor att få presentabla resultat. Detta utan att man ens behövde investera i programvara. Baserat på energisimuleringen, där bilmotortillverkaren fick hjälp av den tyska simuleringsspecialist-bolaget iSILOG GmbH, testades olika scenarier i den virtuella produktionsmodellen som man hade skapat med Plant Simulation.
I simuleringsmodellen förutspåddes modifieringar av den befintliga programmerbara logiska styrenheten (PLCn) för maskiner inom linjen att ge energibesparingar på 1,66 miljoner kilowattimmar el på verkstadsgolvet. Vilket också blev precis vad man uppnådde i den fysiska verkligheten efter att underhållsteknikerna programmerat om PLCerna.
Eftersom en tomgångsmaskin inte behöver förses med kylsmörjmedel sparades ytterligare 1,4 miljoner kilowattimmar el genom att stänga av en del av högtryckspumparna vid anläggningarna för mediaförsörjning.
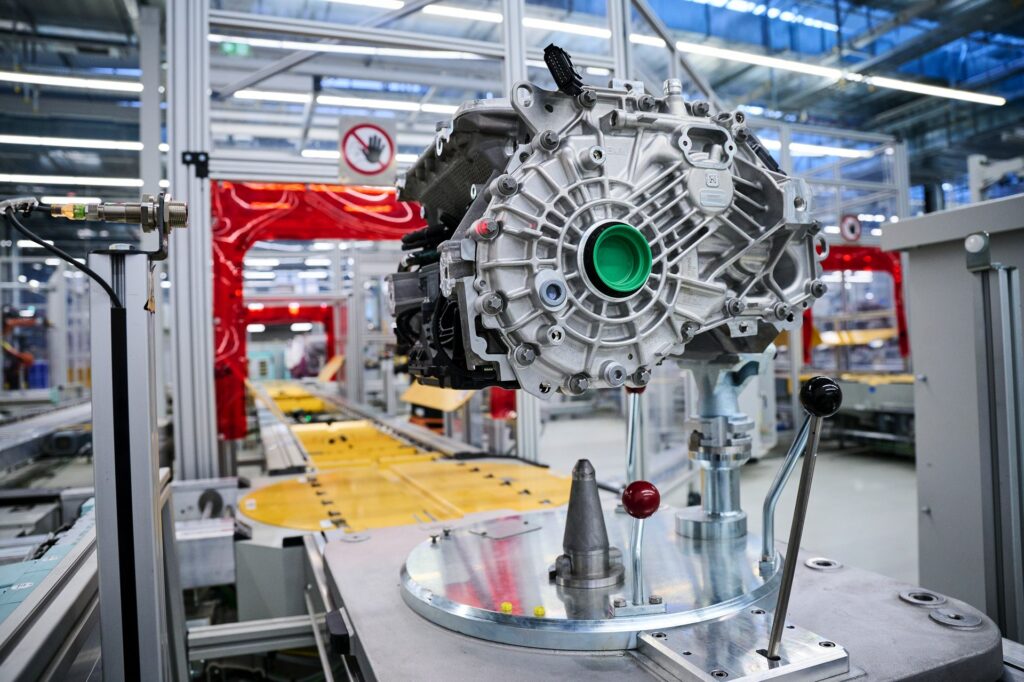
En simuleringsinvestering väl värd att överväga
”Att implementera den automatiska start-stopp-funktionen i vevhuslinjen som en energibesparande åtgärd ledde inte bara till en total energiminskning med 3 miljoner kilowattimmar el per år, utan det visade också en gynnsam bieffekt: om maskiner eller matarpumpar är avstängda medan de inte behövs, detta minskar också brus. Runt om i världen finns det en enorm potential för minskningar av energiförbrukningen för praktiskt taget alla bearbetningslinjer i fordonsindustrin som verkligen skulle göra skillnad om den implementerades,” konkluderar Siemens sin fallstudie kring motorfabriken i Steyr.
Det är inte svårt att inse styrkan med vad produktionsoptimering via simulering kan göra för att som en av flera poster bidra till minskad elkonsumtion, lägre kostnader och förbättrad hållbarhet. Saken ligger i tiden och är en investering väl värd att överväga.