Framtidstron är obegränsad bland Siemensfolket. Man har fått ihop en svit av digitala verktyg som i långa stycken lever upp till drömmen om hela utvecklingskedjan sammanlänkad, och det är mjukvarorna som gör merparten av jobbet.
”150 procent BOM”
Visst, bolaget har under senare år alltid varit välutrustat när det gäller programportföljen. På produktutvecklingssidan är Teamcenter ryggraden i hanteringen av produktdata, medan CAD-flaggskeppet NX är motorn i produktdefinitionsarbetet och på simuleringsplattformen Simcenter skapas den virtuella miljö där allt kan testas. Inte heller Tecnomatixplattformen – tätt länkad till Teamcenter – är någon dagsfärsk nyhet. Denna lösning, används för att planera, koppla ihop och optimera produktionshanteringen; för att i nästa led skicka över den färdiga koden till verkstadsgolvet, till PLCerna och allt det andra där OT, Operativ Teknik, tar över den fysiska produktionen. Allt det där har suttit på plats länge. Men steg för steg har kapabiliteterna förfinats, ”tentaklerna” har sträckts längre in på verkstadsgolvet och integrationen mellan IT/PLM och OT har nått nya höjder. Mats Friberg:
– Vi realiserar idag 150 procent BOM (Bill Of Materials). Informationen flödar nu i en obruten, automatiserad ström från eBOMen (engineering BOM), via mBOMen (manufacturing BOM) till sBOMen (service BOM), inkluderat BOPen (Bill of Process). Det här är vi ensamma om att kunna realisera för industrin, säger han.
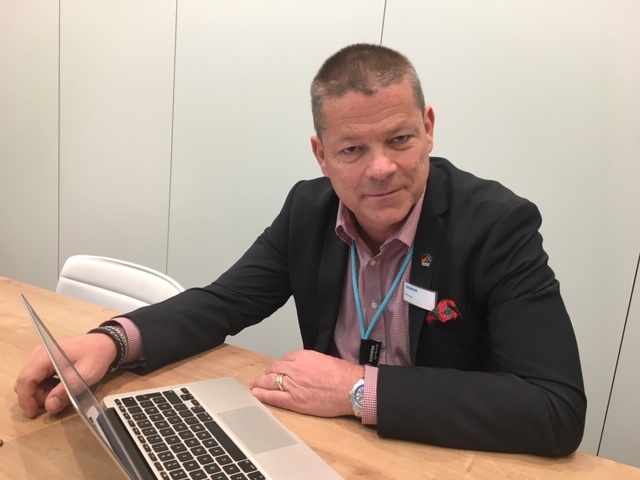
IoT-plattformen MindSphere får hjärtat att slå snabbare
Allt det där där imponerar förstås, inte minst i skenet av BOMarnas betydelse inom exempelvis fordonsindustrin, där de kan beskrivas som branschens ”smör och bröd”. Men det som idag får den tyska verkstads-IT-jättens hjärta att slå ännu lite snabbare är mjukvaran MindSphere.
– Absolut, är det så, säger Ulf Troedsson. Visst var vi, och f ö också de flesta andra i branschen, lite oroliga när GE för 4-5 år sedan kom med sin Predix-plattform. Den kändes som ett hot. Men vi samlade oss och satsade och med MindSphere på plats har vi tagit PLM, IoT och annat till nya höjder.
Vad är MindSphere? Det är en öppen IoT-plattform och ett operativsystem, sammanfattar chefen för Siemens nordiska rörelse. Denna lösning sluter produktlivscykel-loopen: Data från produkten på fältet återmatas till innovationssystemet (i det här fallet PLM/Teamcenter) för att ytterligare vässa den, baserat på hur det fungerar i verkligheten.
Han noterar också att köpet av ”låg-kodutvecklaren” Mendix, för något drygt år sedan, betytt en hel del för kunderna och har adderat möjligheterna att snabbt bygga appar och på så sätt väsentligt förbättrat kapabiliterna relaterat till både PLM och ERP.
– Mendix ”suger” information från ”enterprise-system”, som PLM och ERP, och kan presentera denna information i ett modernt ”appformat”. Det stänger dörren för utmanare som Aras, som ofta kommer in med ett helt system som en lösning på något som kanske egentligen egentligen bara var ett specifikt problem, tillägger Mats Friberg.
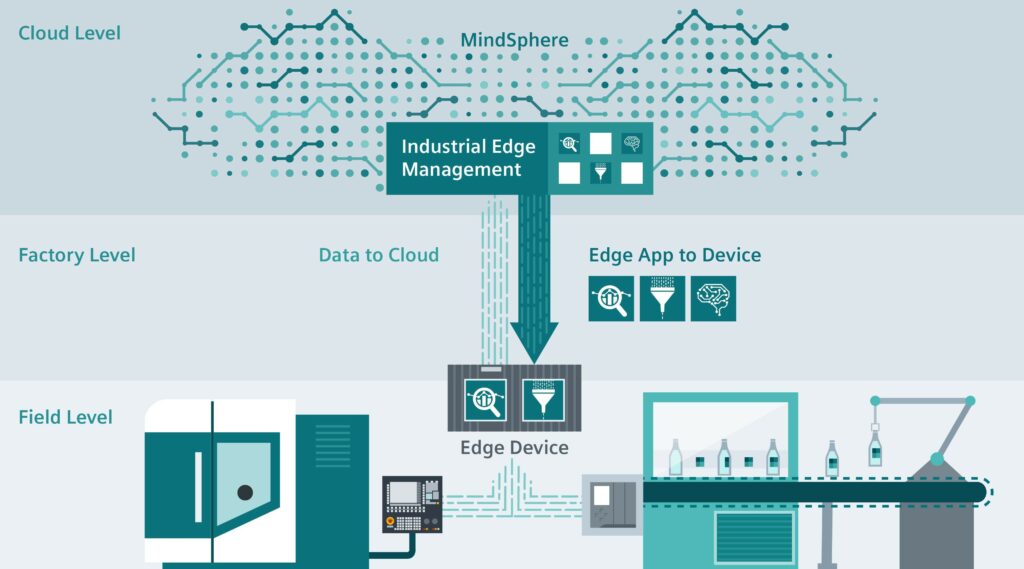
Edge computing för snabbare respons
Annat som är intressant för företagen i Siemenslösningen är ”edge computing-bitarna”, konstaterar bolagets nordiske PLM-bas vidare.
– Ja, det har vi märkt av här nere i Hannover, säger han. I vår lösning, Sinumerik Edge, möter vi sånt som kräver omedelbar, millisekund-kapabel respons på stora datamängder. Ta komplexa AI-styrda maskinoperationer som ett typexempel på tillfällen då ”edge” kan göra nytta. Du vill inte skicka de involverade gigantiska datavolymerna via molnet, samtidigt som sekundsnabb respons krävs; detta kan vi istället med vår lösning processa lokalt.
Edge-begreppet går tillbaka på den enorma ökningen av datatrafiken. Nätverksjätten Cisco har förutspått en nära nog fyrfaldig ökning av molntrafiken mellan åren 2015 och 2020 – från 3,9 zettabyte till 14,1. En zettabyte motsvarar en miljard terabyte.
Med dessa volymer som bakgrund blir det uppenbart att molntrafiken blir besvärande stor när datatrafiken belastas med enorma mängder mätdata från 100-tals miljoner uppkopplade IoT-enheter.
Hur gör man då? ”Edge Computing” är det finurliga svaret på frågan. Istället för att skicka upp dessa oceaner av data i molnet har man byggt upp lösningar där så mycket som möjligt av de stora datavolymer som ska processas kan göras lokalt, på de uppkopplade enheterna, så nära datats ursprung som möjligt – ”at the edge of your network” – alltså, ”i utkanten av ditt nätverk”. Därav begreppet ”edge computing”.
– Edge är också idag en uppskattad kapabilitet som finns i MindSphere och löser dataintensiva användarcase, säger Friberg.
SKF kopplar upp kullager och säljer tjänsten per roterat varv
Men kanske är den riktigt tunga poängen med MindSpere att det är ett slags IoT-ekosystem av partners, som tillför kapabiliteter genom appar på alla fronter. Siemens står inte ensamma i utvecklingsarbetet. Här skjuts nya funktionaliteter, kompetenser och lösningar in på plattformen i en kontinuerlig ström; AI, Machine2Machine, APIer, e t c. ”Himlen sätter gränsen,” är ett omdöme vi hörde i Siemensmontern; ett betyg som inte blir sämre av att MindSphere körs på Microsofts Azure, AWS (Amazon) och det finns t o m planer på att köra det på kinesiska Alibaba.
– Sen tycker jag gott att man kan påpeka fördelen med att Siemens står som en garant för en öppen miljö med maximal konnektivitet, säger Troedsson. Du kan snabbt koppla direkt till de enheter du vill ha upp, fånga data och per automatik konfigurera systemet så att de förs in enligt de strukturer man önskar. Integrationstiden är kort sagt inget problem, det hela går mycket snabbt.
– En annan bit värd uppmärksamhet är skalningskapabiliteten. Man kan koppla upp hela ”flottor” av tekniska enheter. Ta SKF, kullagergiganten, som ett bra exempel. De är ett typexempel på hur man utvecklar nya affärsmodeller enligt ”Product-as-a-Service-konceptet.
SKFs modell går ut på att ta betalt per roterat varv i kombination med parametrar som upptidsgarantier.
– Precis, säger Troedsson. Det är principen att ta betalt för sina tjänster istället för att överlåta ägandeskapet av produkten. Värdet ligger ju i de tjänster utrustningen står för. Atlas Copco är ett annat bra exempel; där tar man på motsvarande sätt betalt per liter luft istället för att sälja kompressorer.
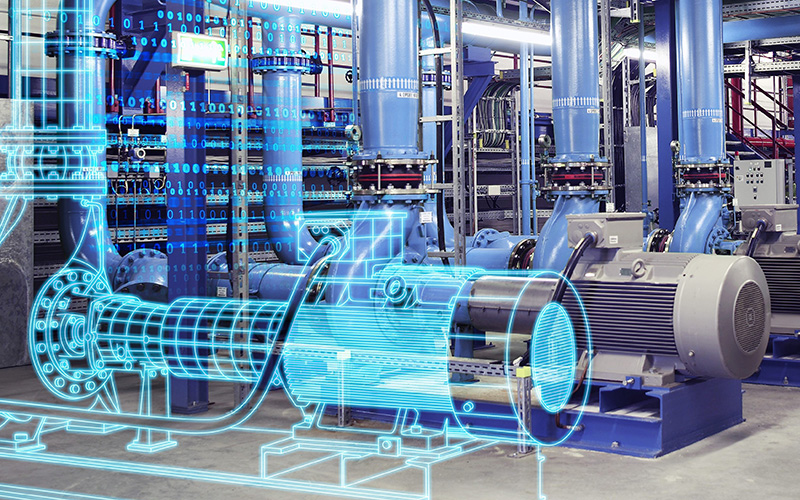
Därför spelar de digitala tvillingarna en nyckelroll
Raden av företag som börjat genomföra den här typen av affärsmodeller kan göras längre, men landar i just principen ”Product-as-a-Service”.
– Den nya tekniken, med sensorer och mjukvaror som MindSphere, i kombination med andra lösningar som NX (CAD), Simcenter (CAE), Mentor (PCB & IC design), etc, blir möjliggörare av de nya affärsmodellerna, där digitala tvillingar spelar en nyckelroll, säger Ulf Trodsson.
Varför är de digitala tvillingarna så viktiga i denna kontext?
– På flera vis, förklarar han. De digitala tvillingarna är den virtuella replikan av en virtuell 3D-modell. Det kan vara i form av produkt eller t ex en tillverkningslina. Den virtuella världen kan nu med hjälp av lösningar på MindSphere-plattformen kopplas upp mot den fysiska världen, där mätdata i realtid kan återföras till den virtuella. Där kan man sedan tillvarata de erfarenheter som gjorts och använda dem för innovationer och förbättringar. I andra fall kan man styra och optimera ett system; eller använda dem för prediktivt underhåll.
Det senare är ju en funktion som ofta framhålls i sammanhanget. Prediktivt underhåll (PU) innebär att man t ex byter en sliten del innan den går sönder, istället för efter ett fast schema; innan det orsakar ett produktionsstopp:
– Just så, konstaterar Ulf Troedsson. Man kan verkligen optimera driftsförhållandena med PU. Ta turbinblad i gasturbiner, som ett exempel på hur denna typ av underhållsinsatser inte bara används för prediktivt underhåll, utan där man också kan välja att köra en turbin med 95 procents effekt för att det inte passsar att byta rotorblad vid det läge det var tänkt. Men det finns förstås en rad parametrar som kan vägas in i helhetsbilden, temperatur, vibrationer, effektuttag, etc.